A pretty tall order, to be sure. (And yet the same can be said of the politicians in Washington, but more on that later.)
As the North American distributor for Hofler, Great Lakes Gear Technologies’ Ray Mackowsky is taking advantage—along with Clipper, Brad Foote and a few select other domestic companies—of the rapid growth of the U.S. wind industry. But aside from the growing need for more and more of the types of machines he sells—a good thing, obviously for machine tool manufacturers—he has in his cross-country travels taken notice of other issues beyond growth patterns relative to wind energy. One is a dearth of experience and capabilities in the manufacture of the gearing, castings, etc., for turbines.
“When the market started up here about four years ago, I was asked by one of the leading wind turbine manufacturers to identify good sources for components relative to wind turbine development in the United States, he says. “I ran around the country for six months and found out that almost no one out here is capable of doing what the Europeans were already doing with gear manufacturing. You could count the players on one hand, and of those, they had a real reluctance to invest any further” in the necessary machine tools. “Some weren’t really interested because they weren’t sure it (wind energy) was going to stay. Four years later, it’s a different story.”
Capabilities first; sales second. But with that, says Mackowsky, has come a degree of circular-firing squad, chicken-or-the-egg mentality between the major turbine installers and Johnny-come-lately, wannabe suppliers. As usual, it’s all about “show me the money,” or more accurately—capability.
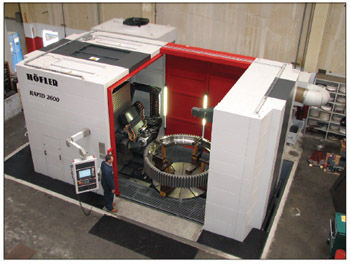
This Höfler Rapid 2600 gear grinder is one example of the specialized machinery necessary for wind turbine gear production. It can tooth grind gears up to 102" in diameter and weighing up to 20 tons. Placement of the 92,000-lb. machine requires a sunken foundation of 350 cubic yds. of reinforced concrete. The base of the foundation is supported by 12 auger cast pilings sunk to a depth of 50 ft. Photo courtesy of Seattle Gear Works.
“What the OEM wind turbine installers (GE Energy, Siemens, etc.) are saying to suppliers is, ‘Hey, you have to put your money where your mouth is first before we give you the business.’
“Today, the guys who the vision and invested early into it, like Brad Foote for one, which has acquired 20 Hoflers in the last several years, they’re now a major player in the wind turbine industry today.”
At NY-based Gleason Corp., another major supplier of specialized machinery for wind turbines, they’re taking a somewhat less sanguine view of the domestic market, as opposed to the international market.
“Most of what we’ve seen has been in Europe and Asia,” says Alan Finegan, Gleason marketing director. “The demand for large hobbing, shaping and grinding machines has outpaced anything that we expected. We are doing some expansion in capacity and shifting some production to accommodate that demand. Most of these large, cylindrical gear machines are made in our Gleason-Pfauter plant in Ludwigsburg, Germany. (Ed.—Please see our sidebar on page 37 to learn how Gleason has changed to meet the needs of the wind turbine industry.)
Finegan, too, has thoughts on why Europe is ahead of the curve regarding the capabilities necessary for turbine componentry, and therefore have more supply in the pipeline.
“The European market is more mature in this industry and places a greater value on technology, which has really fueled our sales in the market. The U.S. market has historically been more price-sensitive, but we are starting to see buyer behavior change, where greater value is being placed on machine accuracy, repeatability and range of capabilities. In fact, we sold a record number of hobbing, shaping, grinding and inspection machines in the North American market in 2007.”
Proper tools—and investment—for the proper job. Whether that translates into a view that the technology quotient is higher in Europe than here is fodder for further debate. But there is no disputing that capital investment in turbines has traditionally been greater in Europe than here. In this arena, equipment rules, regardless of expertise.
“I think there’s a couple of reasons for that,” says Fred Chase, a veteran supply chain consultant to the industry and an AWEA presenter at this year’s Gear Expo Solutions Center. “The technology of making gears today has gone to another level, not that they couldn’t be done (here) in the past, but it was just a few shops. Today the production gears for a turbine gearbox have created a tremendous demand for technology, and I think that the American gear industry in general is not up to that standard. And I think it’s primarily equipment-based rather than technology-based.
“It’s purely just a decision-making process over whether to make the capital investment to do it. The message has to get to them (manufacturers), and that’s what I was trying to convey at Gear Expo—that there’s a market out there in great need. But in order to take part in that market you’re going to have to make the capital investment for updated grinding and cutting equipment.”
But even if the spirit—and pocketbook—are willing, the supply chain is unforgiving. Just ask Sterling Ramberg, vice president of sales and marketing for WA-based Seattle Gear Works. In this case, it’s not all about the money, but more like the old saying, “My kingdom for a horse.” Or a hobber, for example.
“Ramping up production as a gear maker is something—even if you’re willing to commit all the resources—let’s say you don’t have to go to the bank, which we have to do to buy a machine,” he says. “You don’t receive shipment of these essential machines for up to two years. One of our grinders, a 2.6-meter gear grinder, is a unique piece of equipment in the wind turbine industry to do various components. It took two years to get the machine from the time we ordered it. Two years.”
Ramberg’s company is a domestic leader in the aftermarket maintenance, repair and replacement of OEM turbine gearbox gear sets. And that activity in itself is a burgeoning market here, but with few domestic players thus far. Which, as stated, is not surprising—if not disappointing—given the investment required.
“These aren’t vanilla gears,” says Ramberg. “The cleanliness of the steel is important, the heat treating is important in that it must be done right, and then the finishing, which requires very special and expensive grinding equipment in order to put all the bells and whistles into the geometry that these require.
“And so there’s a demand from the major OEMs that produce these gearboxes. And then when they go haywire in a very demanding environment, that’s an issue. Where are they going to send these things for repair? There’s really only a handful of people in the country that have the skills to be able to deal with these higher-end products that wind turbine gearboxes are.”
Who will make tomorrow’s turbines? And that leads to another problem facing players in the wind turbine business—the all-too-familiar state of the country’s manufacturing workforce. Anyone remotely involved in manufacturing knows that the dwindling number of skilled gear designers, engineers and tradesmen has been a drag on continued growth. We’ve all heard the same refrain —What’s the point of having a two million dollar machine on my floor if I can’t find anyone to run it?
“It’s a problem,” affirms Clipper Wind’s Gates. “When I visited some of our suppliers, one of the observations was, ‘You don’t have many younger people here; in 10 years half of your labor force could be gone.’ And they said, ‘You’re right; that’s a real problem.’ I saw that half of their signs were in Polish, and asked, ‘Can’t we import people from Poland?’ And they said, ‘Don’t get us started on immigration policies. We can’t bring in skilled workers from Poland.’”
Says the Gear Works’ Ramberg, “Who’s qualified to run these machines with the atrophying of manufacturing in this country for so many years? We’re trying right now to hire people and it is very, very difficult. We have to train people in-house and then maybe by the time you get someone trained or close to being worth anything—and you’ve been paying them to go to school—they have an issue or a problem and then leave.
“Everyone recognizes that there’s a future in this (market) so people are building their gear making skills. Countries like China and India, they’ll have an engineer getting three bucks an hour. Wouldn’t that be luxurious—to have a mechanical engineer to run your gear machine?”
The industry’s workforce may be on life support, but is not flatlining just yet. At Brad Foote, Drecoll faces the same problem in the Chicago area, but seems to be making some headway. For him, as with others, it’s not finding able workers, but training them that matters most.
“There are no qualified tooth grinders. We now have 30 tooth grinders, but prior to this I’d say there were 30 qualified tooth grinders in all of Chicago. So you can’t go out and say, ‘I’m going to find qualified tooth grinders.’ You have to train someone to get to that level.”
To that end, Drecoll is a firm believer in AGMA’s various online training courses.
“Those courses are very good, and we require all of our people to take them so they know the (gear terminology) we’re talking. So when you describe a lead or involute, they know what the heck you’re talking about. Our managers help them learn online what a gear is, and then we take that to the shop floor and show them how to use the machines.”
Bottom line, what makes the lack of investment and skilled workers for the wind turbine industry even more galling is the fact that projections for continued, accelerated growth domestically are practically off the charts. But like an aircraft carrier doing a 180 degree turn, it will take the industry some time to better position itself. OEMs such as GE Energy are poised to meet the continuing demand, forecasts to the contrary.
Most forecasts just hot air. “When you look at forecasts for the wind industry, if you go back a couple of years and look, you realize that they’re always wrong and too conservative,” says Sean Fitzgerald, a GE Energy 1.5 MW platform leader. “We’ve seen positive demand in the last couple years, and the PTC (production tax credit) was extended last year for two more years, which is a good signal for the domestic wind industry. But as you look out, the PTC is set to expire in 2008, and the fact of the matter is we have very strong orders for 2009, an indication that customers see this as a longterm industry and growth opportunity.”
Fitzgerald says GE has increased its output by five times since 2002, an “incredible,” if unsustainable rate. But he adds, “This is absolutely a rapidly growing business for GE, and we’ve added a lot of resources. If you look at renewables, wind is the most viable option right now. If you want to increase renewable percentages, wind is where you have to go in the foreseeable future. It can be a staggering growth industry for quite some time.”
Working at Mitsubishi at this time, says O’Keefe, “is personally exciting, to be at the forefront of a market that has an extreme growth potential. It’s good to be with a global leader like Mitsubishi in the wind turbine arena and the U.S. market at a time when the U.S. market has tremendous demand and potential.”
Adds AGMA’s Fischer, “Booming is putting it mildly. It’s really exploded over the last three years.”
Before we leap to assign blame exclusively to the manufacturers of these critical components and machines for the shortfall—which is inaccurate—the case is easily made that it is this country’s late-to-the-dance mindset regarding renewable energy that has been the major impediment to continued growth.
Political will needed. Nurturing and facilitating domestic wind turbine growth is a challenge that begins in Washington, D.C. and extends to the state level, with the latter being the most aggressive. Consider, for example, the PTC’s importance to long-range planning and investment on the part of U.S. OEMs and suppliers. Every time the tax credit comes up for renewal, it becomes a political football between the two major political parties. The fact that it is ultimately extended every time does not mitigate the fact that the nation’s capitol is decidedly behind the curve, and certainly more so than suppliers. For example, Congress finally passed a bipartisan energy bill in December, and there was quite a bit of mutual backslapping and logrolling going on. Sure, there were good, long-awaited things in the bill, such as new CAFE standards for cars and light trucks, and a requirement for the production of 36 billion gallons of renewable fuels by 2022, among other things. But guess what was stripped from the bill in the face of a threatened veto by the White House? You got it—the stipulated renewable electricity standard and incentives for wind and solar/energy.
Regarding the PTC, says industry consultant Chase, “Historically, they’ve allowed it to lapse and usually it takes them anywhere from two to six months to reinstate it. And what that does to the industry is, it stops it; literally stops the manufacturing. The OEM developers are uncertain over when and what’s going to happen, the manufacturers don’t want to invest in building wind turbines on speculation. So everything comes to a standstill and the problem with that is, when the credit is renewed, the tap doesn’t just get turned back on. It takes a year to wind it back up again.” (See our story on jobs creation and renewable energy standards at the state level on page 32 of this issue.)
Perhaps Mitubishi’s O’Keefe, in referencing Charles Reich’s prophetic work of non-fiction from 1970, sums it up best.
“The ‘greening of America’ is coming, and this is a key issue for both (political) parties in the coming 2008 election. And as the demand for reduction of greenhouse gasses, cleaner alternatives and scarce natural resources globally continues, wind becomes a viable solution.”
For more information:
American Gear Manufacturers Association (AGMA)
500 Montgomery Street/Suite 350
Alexandria, VA 22314-1560
Phone: (703) 684-0211
Fax: (703) 684-0242
Internet: www.agma.org
American Wind Energy Association
1101 14th St., NW–12th Floor
Washington, DC 20005
Phone: (202) 383-2500
Fax: (202) 383-2505
Internet: www.awea.org
Clipper Windpower
6305 Carpinteria Avenue, Suite 300
Carpinteria, CA 93013
Phone: (805) 690-3275
Fax: (805) 899-1115
Internet: www.clipperwind.com
The Gear Works Seattle Inc.
500 Portland St.
Seattle, WA 98108
Phone: (206) 762-3333
Fax: (206) 762-3704
Internet: thegearworks.com
GE Energy
www.gepower.com
Gleason Corporation
1000 University Avenue
P.O. Box 22970
Rochester, NY 14692-2970, USA
Phone: (585) 473-1000
Fax: (585) 461-4348
Internet: www.gleason.com
Great Lakes Gear Technologies, Inc.
8755 Ronda Drive
Canton, Michigan 48187
Phone: (734) 416-9300
US & Europe cell: (313) 506-3381
Internet: greatlakesgeartech.com
Mitsubishi Power Systems Americas, Inc. (MPSA)
Patrick O’Keefe, C.P.M., Buyer–Global Sourcing
100 Bayview Circle, Suite 6000
Newport Beach, CA 92660
Phone: (949) 856-8400
Fax: (949) 856-4481
Internet: mpshq.com
Tower Tech Holdings, Inc.
J. Cameron Drecoll
47 E. Chicago Avenue/Suite 332
Naperville, IL 60540
Phone: (630) 637-0188
Fax: (630) 637-8472
Internet: www.towertechholdings.com