Why Pull Doesn’t Always Work
Why doesn’t pull work for the environment described above? Pull is part of the lean manufacturing approach, which works by creating "flow"--essentially by synchronizing all the steps in the company to the average rate of sales of the products. Typical concepts used for this include setting the Takt time for individual operations. (Editor’s note: Takt is the German word for "rhythm" or "beat," as in the beat of a musical piece. In lean manufacturing lingo, it refers to the pace or heartbeat of an organization. An organization with a takt time of two minutes will complete a finished product every two minutes.)
However, in a high variability environment, one could define an average Takt time based on a given month’s orders, but the daily demands on various machines could be so different that the production would be seriously out of balance. Further, note that pull is a replenishment system: when one item (or container) is used, a signal is sent to replenish it. For a company that makes thousands of different items, this implies that there is inventory of each of these items at each stage of the operation where a pull signal is being used. Worse, for a company that custom-engineers products, the pull system fails completely. There is no container of products to be replenished, since the parameters of the product are not known till the order is received and design engineering completed.
The QRM Strategy
For a company serving these environments, top management needs to rethink its strategies for capacity, workforce, and organizational structure, to create the capability for flexible and
fast response. Here we will focus on the material control aspect, which involves the use of POLCA.
In the POLCA system, the flow of orders through the different workcenters is controlled through a combination of release authorizations and production control cards known as POLCA cards. The release authorizations are generated using a standard MRP system. This creates release authorization times for each order at each workcenter.
However, unlike in a standard MRP system where a workcenter should start work at that time, in a POLCA system the workcenter cannot start unless the corresponding POLCA card is also available. The POLCA cards communicate and control the material movement between workcenters. While this may
seem similar to Kanban, there are some important differences. Here are the three key features of POLCA that make it uniquely effective for the manufacturing environments we targeted:
1. POLCA cards are not specific to a product, as in a pull system, but are assigned to pairs of workcenters, and apply to all products going from the first workcenter to the second workcenter in the pair.
2. Whereas a Kanban card is an inventory replenishment signal, a POLCA card is a capacity signal: a POLCA card returning from a downstream workcenter signals that the workcenter has available capacity to process more work. When a workcenter reviews its list of jobs whose start has been authorized, it looks up the next workcenter for each job, and it can only work on a job if it has a POLCA card from that destination workcenter.
3. POLCA cards for each pair of workcenters stay with a job during its journey through both workcenters in the pair before they loop back to the first workcenter in the pair. Since most workcenters will belong to more than one pair of workcenters, there will be multiple loops of
cards that overlap in each workcenter (see Figure 1).
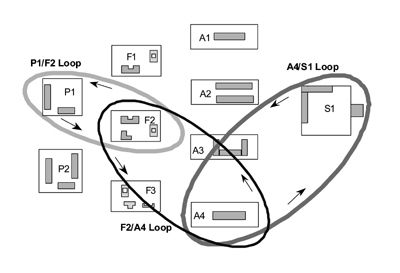
Figure 1--The POLCA system uses production cards circulating between overlapping pairs of workcenters to make most efficent use of production equipment in companies manufacturing custom-engineered and high-variety products.
The design of the POLCA system gives it several advantages for the high-variability or custom-manufacturing environment we described. First, POLCA helps in managing short-term
fluctuations in capacity and also assists in reducing congestion on the shop floor. Essentially, the use of POLCA cards assures that each workcenter only works on jobs that are destined for
downstream workcenters that will also be able to work on these jobs in the near future.