Viscotherm Rotodiff Gearbox Tester Lowers Energy Costs for Back-to-Back Gearbox Test Rigs
Viscotherm's Rotodiff solution enables back-to-back test rigs to run with a fraction of the turbine's power while allowing to test gearboxes with different ratios in a mechanical closed-loop system, hence significantly reducing the energy consumption.
Back-to-back test rigs with a mechanical closed loop have two identical gearboxes, with an in- and output shaft coupled to each other in a symmetric arrangement. The system is accelerated and kept idling at the tested gearbox's nominal speed. A torque device that links two gearwheels tightens both gearboxes against each other. As a result of the components' elastic deformation under load, a torsional angle forms that is proportional to the introduced torque. Therefore, only the motor for idle running the gears and the torque device need to be supplied with power, allowing the tests to be run at a fraction of the nominal power of the tested gearboxes. By these means, a renowned helicopter manufacturer saved enough energy with its yearly tests to supply a town of 30,000 people.
In order to test gearboxes with different ratios, Rotodiffs are used to introduce torque, and the test rig's interface to the gearbox is adapted to the respective layouts. The differential rotating speed of the Rotodiff is shifted by monitoring the pump unit's oil flow, so the ratio of the test rig can match that of the gearboxes built for the different types and sizes of helicopters. This is possible since the Rotodiff's rotor and housing rotate with their respective shafts. Since the Rotodiff is a part of the mechanical closed loop, the introduced torque is proportional to the pressure, which is continuously adapted at high frequencies to match the given set points. This solution also allows users to hydraulically eliminate ripple.
Depending on the Rotodiff's size, the housing can turn up to 6,500 rpm, with differential speeds up to ± 200 rpm and torque values of over 100,000 Nm. This way, the torque and direction of rotation of any tested gearbox can be matched. Protection against overload is granted by limiting the pressure (e.g. with a pressure relief valve). This results in flexible test rigs that are able to perform customized test sequences on different types of gearboxes at high torques and multiple frequencies with minimal power consumption. In collaboration with Viscotherm, Airbus Helicopters, for instance, has developed its test rigs up to the last generation of multi-purpose test benches.
To visualize the functions of a Rotodiff, the hydraulic configurations corresponding to the operating conditions in each of the eight operating quadrants are shown schematically in Fig. 3. In the quadrants I, III, VI and VIII the Rotodiff operates as a hydraulic motor: the hydraulic power fed by the pump is transformed into torque and rotational movement. In the quadrants II, IV, V and VII the Rotodiff works as a pump: the mechanical work introduced by the shaft is transformed into hydraulic power and employed, for example, to overcome the hydraulic resistance of a throttle valve as shown in Fig. 3. In the quadrants II, III, V and VIII the rotor turns slower than the housing. In the quadrants I, IV, VI and VII the rotor turns faster than the housing. To ensure this in the quadrants IV and VII, the driving shaft must be connected to the rotor; in all other quadrants it can be connected to either the rotor or the housing. This functional diversity allows users to adapt back-to-back test rigs to the most kinetically diverse of the tested gearboxes and to accurately adjust the parameters of the load with a hydraulic control circuit.
The Rotodiff's multiple kinetic possibilities, its durable construction and remarkable efficiency have made it a key component in test rigs all over the world. Moreover, its compact footprint and simple design lead to reductions in infrastructural costs. Yet another advantage are the energy savings derived from the housing turning idle at high speeds and the high torque being introduced at a very low relative speed - even when compared to similar electromechanical systems.
Wherever large torsional angles or even adjustments of the rotational speed are needed to safely, flexibly and precisely test high-torque rotating components, Viscotherm's compact Rotodiff is the most energy efficient solution.
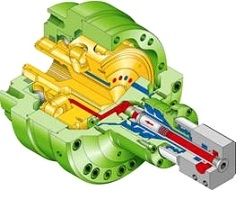
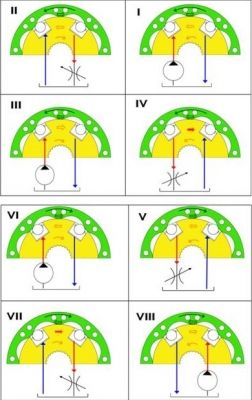