Zimmer noted, “When we launched our line, we offered eight pulleys—we now produce and stock over 4,000 parts. They are available with 4–14 rib configurations in any size that the customer requires. The engineered surface that is machined onto the ribs minimizes slippage to deliver maximum supercharger performance.”
“Fast response is essential in our business. Equally important is the ability to meet special customer demands in the timeliest manner. Some of the parts that customers request are only .005 in. different in diameter. We don’t charge customers for design services, but the design we produce becomes our own. We have extensive patents covering our micro machining technologies that are available for both standard and special orders. When necessary, we incorporate additive manufacturing and micro welding, but these are typically reserved for unique applications,” said Zimmer.
The manufacturing process uses both DMG MORI DS turning centers and a variety of Haas ST-Y standard and twin-spindle lathes. On the DMG units, parts are exclusively processed on Hainbuch collet and mandrel chucks. Starting on the main chuck and finishing on the mandrel, the entire part can be completed in just one cycle. Tolerances extend from ±.0003 to ±.0001 in. on the most critical parts. ZPE’s engineered micro machining of surfaces utilizes a patented ablation process that allows for precise control and repeatability in their microstructures.
ZPE prides itself on rapid manufacturing capabilities that can design and complete parts within hours—a critical process when parts are needed the next day. To meet such tight deadlines, Zimmer emphasized the importance of proper tooling and workholding: “We use Sandvik Coromant Capto modular tools. They deliver exceptionally high cutting performance and rigidity. One of their most overlooked features is that the coolant ports are easy to clean.
In selecting the workholding equipment best suited to ZPE’s demanding schedules and individual application needs, Zimmer worked closely with Hainbuch regional sales manager Tom Chambers. Chambers explained, “With the Haas lathe, we specified the TOPlus mini chuck equipped with a custom draw tube adaptor. TOPlus uses hexagonal outer profile collets that offer 25 percent more clamping force than round versions. Because of the geometry, these chucks have superior chip contamination control, and, in our mini versions, the reduced contour provides the ability to choose the tool you need without interference.
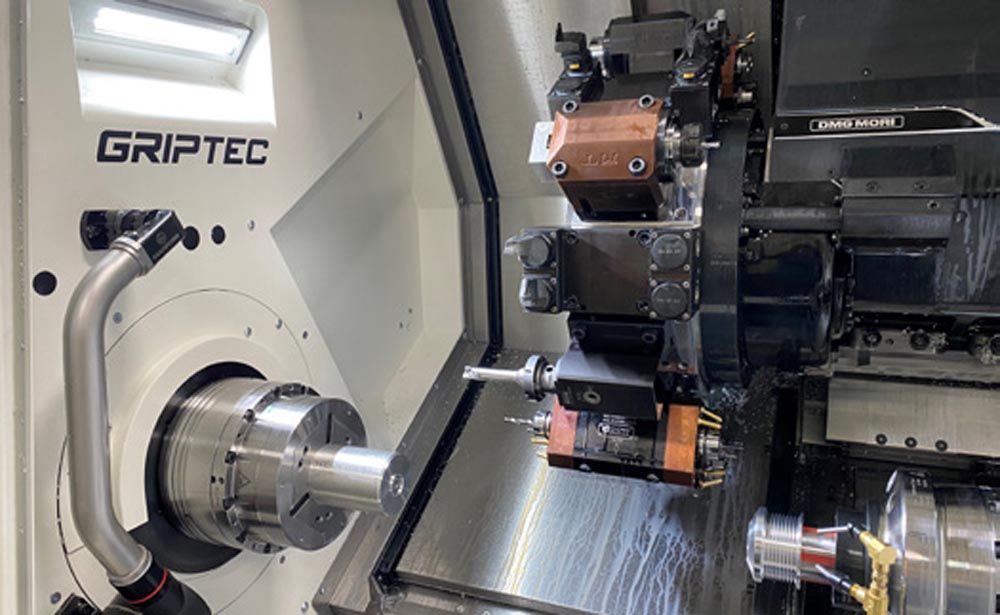
The DMG MORI dual spindle machines use TOPlus units on the main spindle for extra clamping force and rigidity and a SPANNTOP RD (round) on the sub spindle.
“Included with the chuck were several adaptations, including several MANDO Adapt units with segmented bushings for ID clamping, as well as a machinable end stop. The MANDO Adapt can be changed in less than two minutes.
“The DMG MORI dual spindle machines use TOPlus units on the main spindle for extra clamping force and rigidity and a SPANNTOP RD (round) on the sub spindle. The important thing is that ZPE can run production op1-op2 complete parts that are dead nuts accurate and yet the system is fast and flexible on the ID changeover to different IDs,” Chambers added.
“When we got our first DMG machine,” Zimmer said, “I had heard about Hainbuch but thought it might be expensive. When we investigated, I discovered that the price is competitive, and the product is superior in strength and quality. For instance, the Hainbuch mating surfaces and external sealing surfaces are far superior in design and strength. With other collet chuck systems, the exterior sealing of the collet and chuck was lacking. In the open position, small chips that are resting on the surface can be drawn in between the chuck and collet during the chuck cycle, causing what we call ‘denting’ in the inside cone of the chuck. When high pressure is present, these small sealing gaps can further be exploited by small chips damaging the interior of the collet chuck. As a result, we needed a solid solution and found that in the Hainbuch collet chucks. Changeover times between sizes, as well as from OD to ID operations, are extremely fast and, even after years of use, we can achieve finishes in the single-digit micron range.