The quality and lead-time reduction that can be reached by complete machining is a very attractive option. This is also the case for manufacturing components with gear and spline features.
As multitask machine tools were developed to be suitable for gear skiving, the concept of flexibility could be combined with high productivity. This triggered a fundamental change in the gear manufacturing industry. The implementation of mill-turn centers started about 15 years ago and has been going on ever since. Initially, some skepticism was expressed, but quite soon the doubts were eliminated, and the concept of multitask machining has since then had a very positive development. This technology shift has had a strong impact on how gears are produced today—and how gears will be produced in the future.
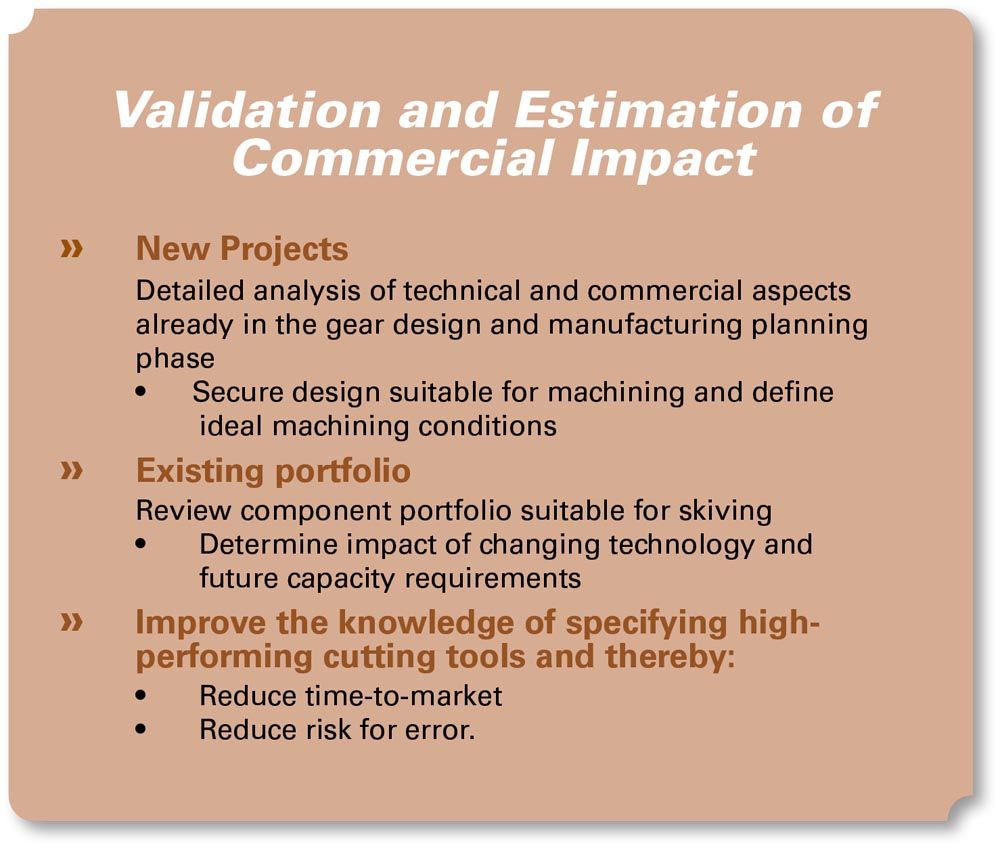
Motivating Factors for ChangingTechnology
The big question for the gear industry is now how to validate gear skiving versus the well-established machining methods which have been used for decades. The tremendous growth in e-mobility has increased the need to validate and decide on future manufacturing technologies, accurately and rapidly. The machining equipment used in the past is probably not generating the desired results needed for high-precision gear components used in e-mobility transmission systems. How can I, with reasonable precision, determine whether I will benefit from implementing gear skiving for my business?
A change to skiving means in most cases that investments in new machine tools are needed, which represent a significant cost. The production or technology manager needs to have a good business case with trustworthy arguments to justify the investment.
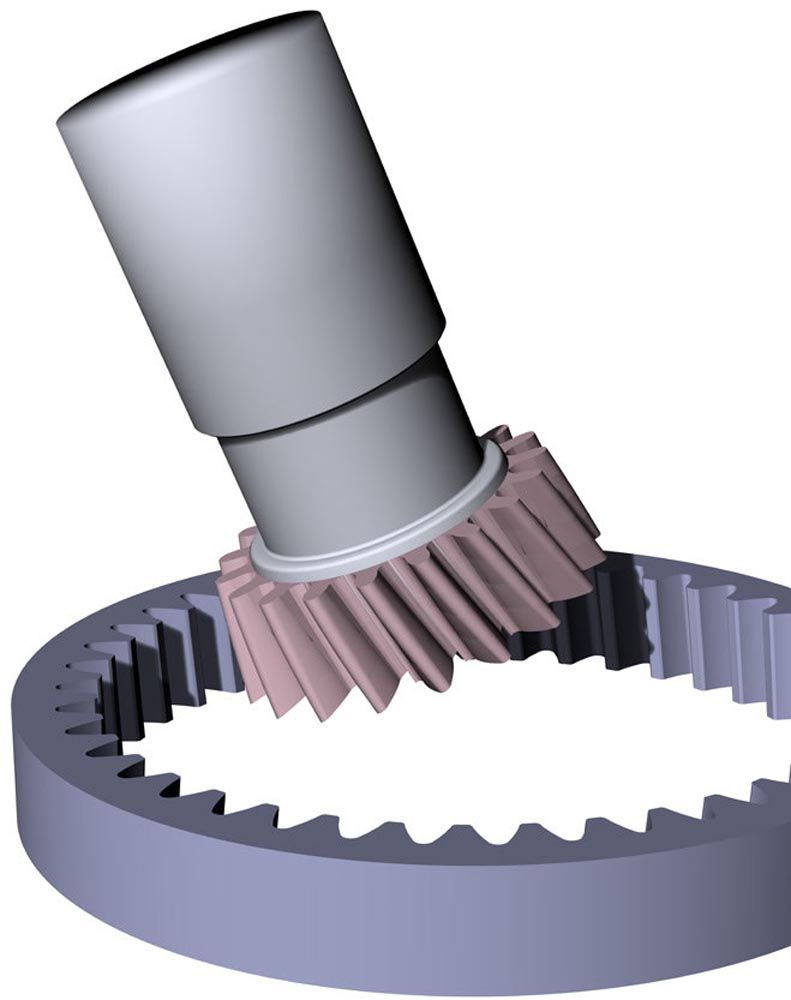
Looking at the Options When Considering Implementing Skiving
- Convert internal broaching of splines, and change to multitask machining.
- Convert shaping for internal and external machining of splines and gears.
- Change from single-purpose hobbing and shaping machines to multitask machines.
- Partly replace hobbing with skiving.
The conversion to skiving should preferably be taken stepwise to generate and spread know-how in the organization over time. Most companies that have implemented skiving see no point of return and most of them are striving to expand the technology once the first processes have been established.
Implementation of skiving is giving users a competitive edge, which can result in gains in lowered component costs that are outstanding. Correctly implemented, also excellent quality and surface conditions can be reached. Skiving does not mean any compromise versus the traditional technologies; many applications show rather the opposite.