Up to now, the STE is the only standardized process for grinding burn testing (see an overview of the currently applicable standards in Ref. 1). STE can be used for a wide range of parts made of unalloyed or low-alloyed steel. However, strict environmental and health-and-safety regulations must be observed because of the use of acids. It is also problematic that the evaluation of the etch indications on the part surface is currently still carried out exclusively by an inspector. To ensure the reliability and reproducibility of the process, reference bodies were developed in which artificial grinding burn was generated by means of a laser (Fig. 2) (Ref. 2).
These reference blocks are used very successfully by many companies, including a number of global acting corporations, to monitor the NE process.
The electromagnetic test methods include the Eddy Current (ET) and Barkhausen Noise (BNR). They rely on the different electrical and magnetic properties of tempering and re-hardening zones and belong to the nondestructive testing methods. However, they require calibration on parts with defined tempering or re-hardening zones. For this purpose, reference bodies with an artificially generated grinding burn can also be used (Ref. 1).
For grinding burn testing by means of the ET method, surface probes are usually used. Their magnetic field detects only smaller surface areas of the parts and thus enables the scanning of surfaces and thus also the localization of grinding burn. At present, therefore, the differential probes known for crack detection are mainly used for grinding burn testing.
Figures 3 and 4 show examples of the inspection of bearing rings applying ET.
Here, by means of a robot, the test probe is contactless guided over all functional surfaces of the ring.
The testing machine is CNC-controlled so the testing process is automated. The test can be performed without contact, although the distance between the probe and the surface must be kept as constant as possible.
The BNR method is based on the generation of the so-called Barkhausen noise during the alternating field magnetization of a ferromagnetic material. It is generated and registered by means of special BHN probes.
Decisive for the reproducibility of BHN measurements is the contact between the test probe and the part surface. The BHN method is also suitable for testing gears (Figure 5). However, the test speed is significantly lower than the test speeds achievable with eddy current testing.
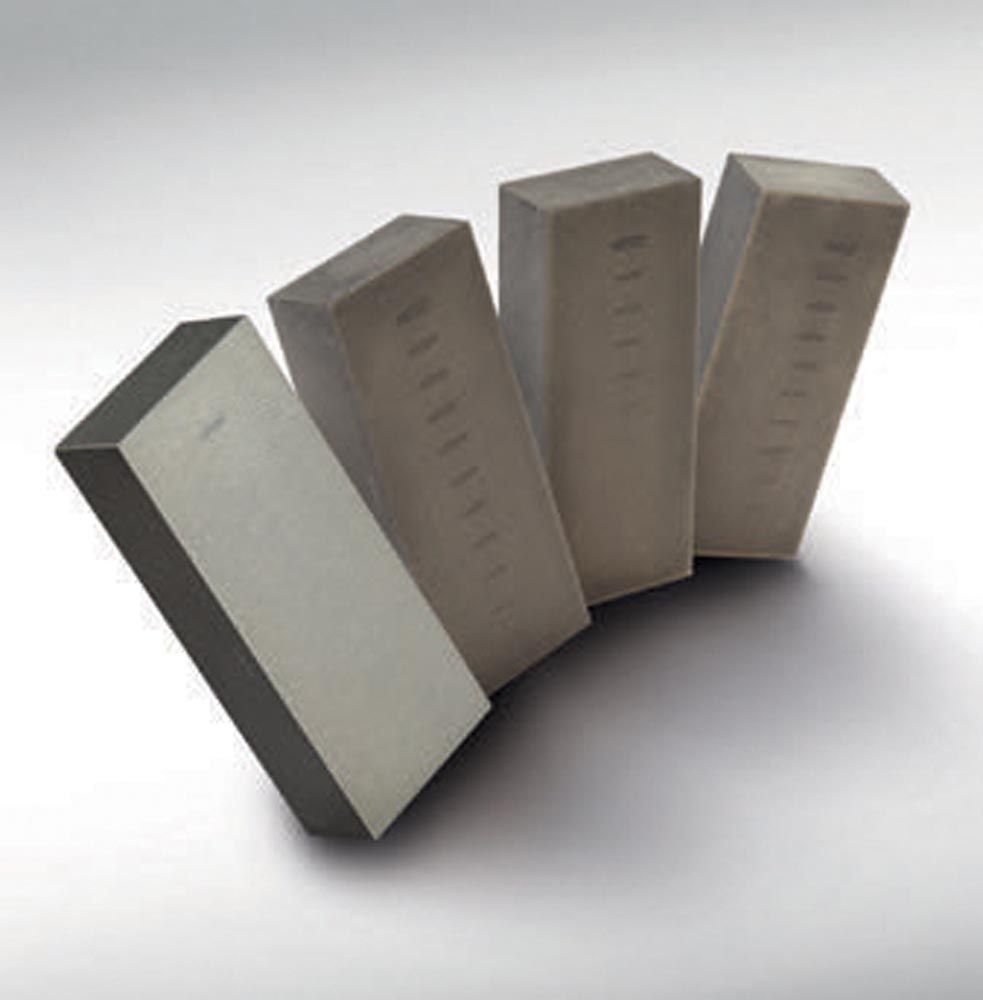 Figure 2—Comparison body NE Test Set. (Source: imq GmbH) |
Figure 3—ET testing of a rolling bearing ring. (Source: ibg GmbH) |
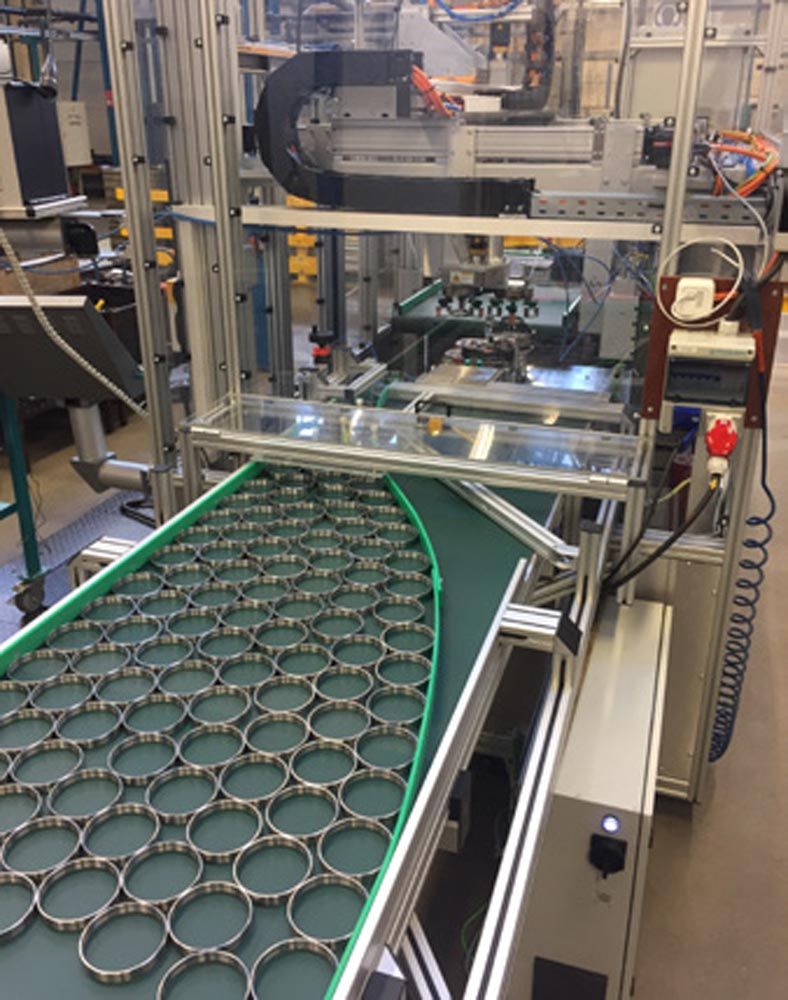 Figure 4—QuaSor E automatic testing machine for grinding burn testing of rolling bearing rings: General view with feed belt. (Source: imq GmbH) | 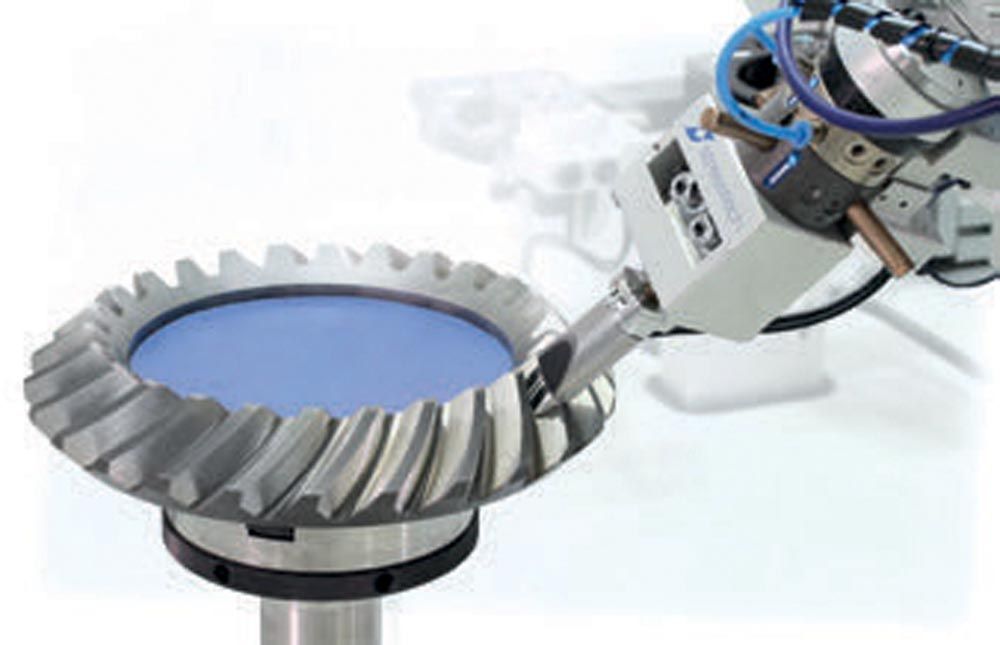 Figure 5—BHN-Testing of gears. (Source: Stresstech GmbH) |
Summary and Outlook
At present, STE is still frequently used as a laboratory test for random sample inspection and in (partially) automated systems for 100 percent inspection of entire production batches. Particularly because of occupational safety and environmental issues, there is a trend toward using electromagnetic methods in its place. However, STE will continue to be needed as a reference method for electromagnetic methods in the future. Mobile test systems are particularly suitable for this purpose, with which STE can be carried out directly on a grinding machine, for example, after a new batch has been started up.
The ET method is currently being used very successfully for the grinding burn test of rotationally symmetrical or similar parts. A particular advantage is that high test speeds may be achieved, and noncontact testing is possible. The BHN method is available for parts with gear teeth.
There are currently three trends in electromagnetic methods: First, there is increasing demand for mobile testing equipment that allows testing directly on grinding or honing machines. Secondly, testing systems will be integrated into grinding and honing machines. The aim is to carry out the grinding burn test immediately after grinding in a further work cycle. This will allow a faster response to any deviations from the normal process. Finally, another development is to apply artificial intelligence (AI) to evaluate test results (Ref. 3).

References
- Martin W. Seidel, Antje Zösch, Konstantin Härtel, Grinding Burn and Its Testing, 2021. ISBN 978-3-00-070194-8, imq GmbH: imq-gmbh.com/en/services/literature-recommendation
- Antje Zösch, Konstantin Härtel, Florian Koch and Martin Seidel, “Reference blocks generated by laser treatment for grinding burn inspection,” 12th ECNDT, Gothenburg, Sweden, 2018.
- Wolfgang Korpus, “Deep Learning AI-based evaluation of ECT signals for classification of grinder burn on steel balls,” ASNT Annual Conference Nashville, 2022.