The movement towards electric drivetrains and components means a mechatronics approach is needed from an engineering standpoint. There’s been a large hiring of electrical engineers at Bonfiglioli to address these market changes.
“We have a great core group of mechanical engineers. At the same time, with the knowledge changing and the skills needed to understand how these mechatronic systems work, you need to have seasoned engineers put training seminars together internally for the sales teams, support teams, etc. as these electrification changes take place in our key markets. The end goal is to be known for our diverse range of electromobility technologies for the construction, off-highway, and heavy industrial markets,” Hartsell said.
Hartsell said if IFPE was any indication the future for electrification and e-mobility is very promising. “There’s an anticipation that we’re turning a corner post-pandemic and these products and technologies will be extremely important to our diverse customer base for years to come.”
bonfiglioli.com
Dana Updates Motion and Drive Technologies for Off-Highway Applications
During a press conference at IFPE 2023, Dana executives discussed the expansion of the company’s drive production capacity as well as recently repositioning the final assembly of its line of heavy axles for mining and other extreme-duty applications to its Lafayette facility. The realignment helps Dana better address the supply-chain requirements and onshoring of North American OEMs.
These initiatives enhance Dana’s reputation in gear engineering, manufacturing, and production. At CONEXPO, Dana showcased its ability to deliver precision-made Fairfield gears and gear drives for industrial and mobile applications as well as its push toward electrification.
“Our goal is to improve the performance, efficiency and durability of conventional and electrified construction vehicles and other off-highway machines,” said Jeff Cole, senior director, corporate communications, at Dana during IFPE 2023.
Marcus King, vice president, off-highway global sales, business development, strategy and program management at Dana, said the organization is dedicated to strategic principles supporting its company-wide mission of “Powering Innovation to Move Our World.”
“Our vision is to improve our leadership position in both conventional and next generation driveline innovations. Dana is energy source agnostic. This is so important in both the construction and off-highway industries where the adoption of zero emissions can vary from region to region, from market to market, application to application, and even vehicle to vehicle,” King said.
This balanced, full system approach was on full display at the Dana booth during IFPE 2023 in Las Vegas.
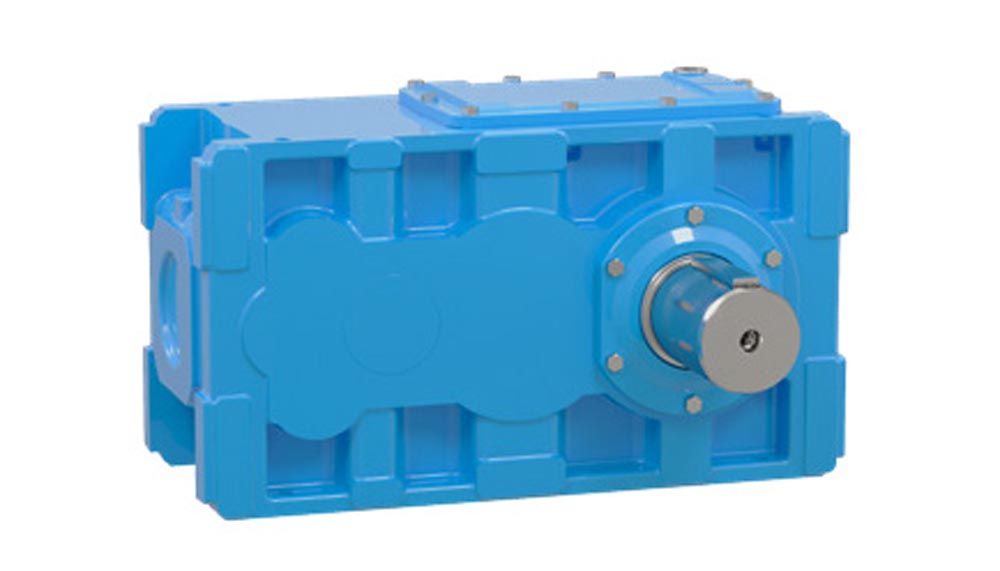
Drive and motion technologies were available for ICE applications and the company continues to expand its offerings in performance and efficiency in these conventional areas. Furthermore, Dana is at the forefront of electric vehicle innovation as well with the e-Transmission and additional e-propulsion systems featured at IFPE.
“Most importantly, we help OEMs minimize development, integration, testing, and manufacturing as they track their paths through this energy transition,” King added.
Leveraging Dana’s field-proven powershift technology, the eSP502 e-Transmission offers a dual-motor, two-speed design that is built on a flexible platform to enable optimized performance at maximum efficiency in a compact package. The modular approach to the transmission design allows for a single motor solution, as well as an optional power take-off, depending on the specific vehicle requirements.
Delivering high efficiency in a compact package that performs like a conventional powershift transmission, the dual-motor version supports continuous power outputs up to 326 hp (240 kW), while the single-motor configuration is engineered for 187 hp (140 kW) of continuous output.
The eSP502 is equipped with next-generation control software and functional safety readiness, enabling easy installation and smooth integration, and it features a patented clutch design that minimizes clutch drag to maximize efficiency.
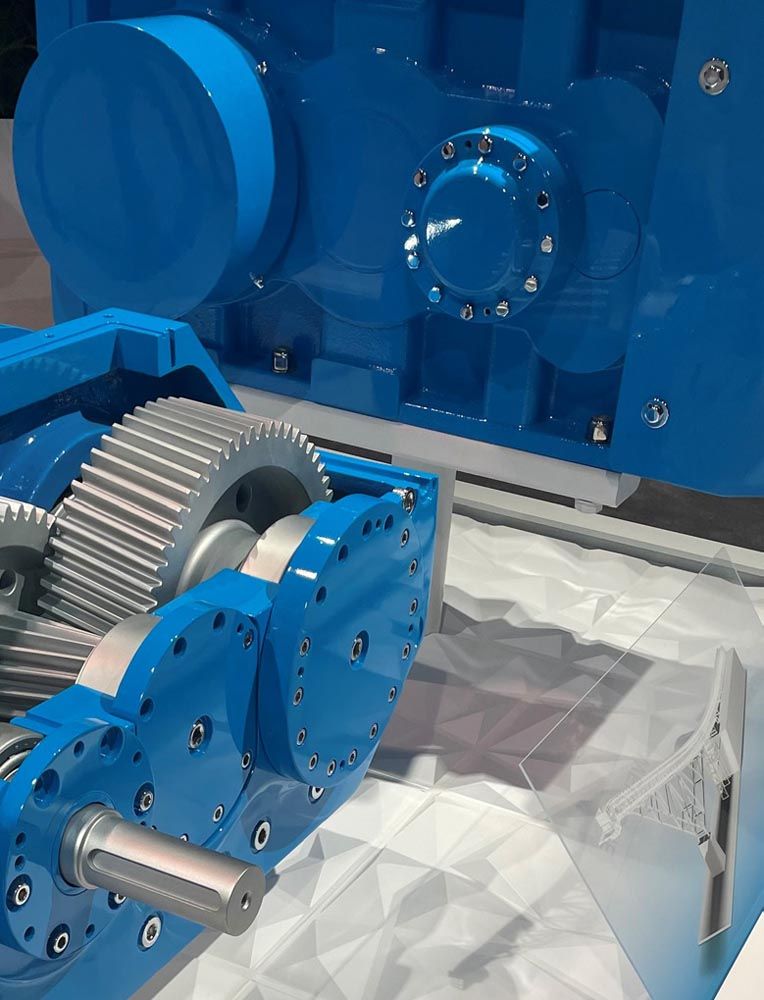
Dana showcased its ability to deliver precision-made Fairfield gears and gear drives for industrial and mobile applications.
It is equipped with Dana TM4 high-voltage motors of up to 800 V to improve efficiency, reduce total package size, and provide redundancy as needed.
The eSP502 e-Transmission's compact and modular design allows it to be adapted for use in 4x2 or 4x4 vehicle applications with a range of ratio options to support a variety of vehicle types.
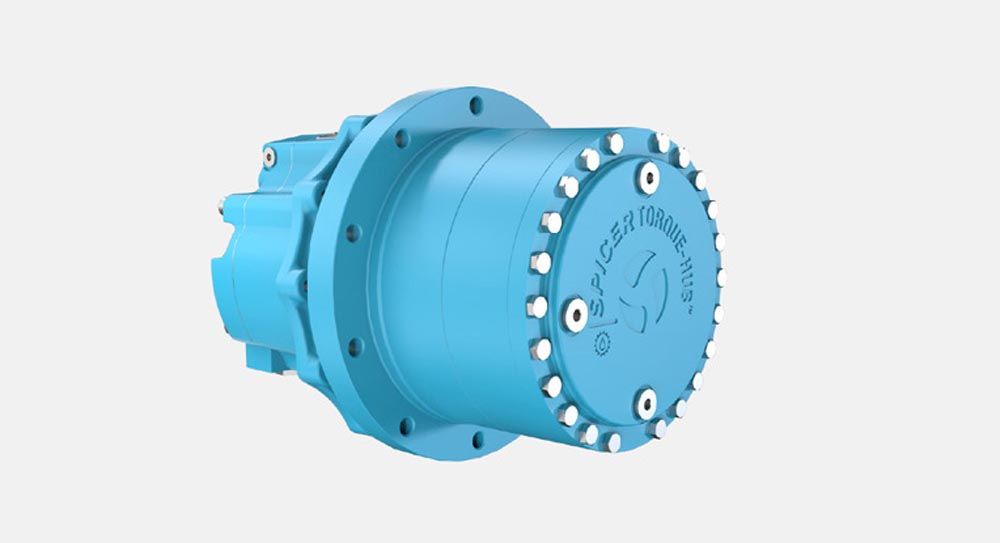
Developed for telehandlers lifting to 12,000 lbs. (5,400 kg), Dana's new driveline comes equipped with a compact Spicer 312 dropbox for high-power hydrostatic motors. This new hydrostatic dropbox functions as a continuously variable transmission without torque interruption, delivering enhanced performance with precise maneuvering at low speeds, reduced fuel consumption, and an integrated spring applied hydraulic release parking brake.
The system includes the field-proven Spicer 222 front and rear heavy-duty axles, which each feature a limited-slip differential and provide the customer with maintenance-free brakes. The complete driveline system is optimized for efficiency as well as noise, vibration, and harshness.
To support the industry's transition to zero-emission vehicles, Dana optimized the axles and driveline system to improve efficiency for a variety of architectures, allowing customers to retain the same driveline solution while choosing between implementing a hydrostatic dropbox or an electrically driven design.
To engage the rapidly increasing interest in CTLs and other tracked equipment in North America, Dana is nearly tripling its annual production of Spicer Torque-Hub track drives within the current footprint of its manufacturing and assembly hub in Lafayette.
Spicer Torque-Hub drives for CTLs offer output torque ratings from 5,000 to 17,000 Nm, delivering increased productivity with maximized motor displacements in a compact package.
dana.com/off-highway
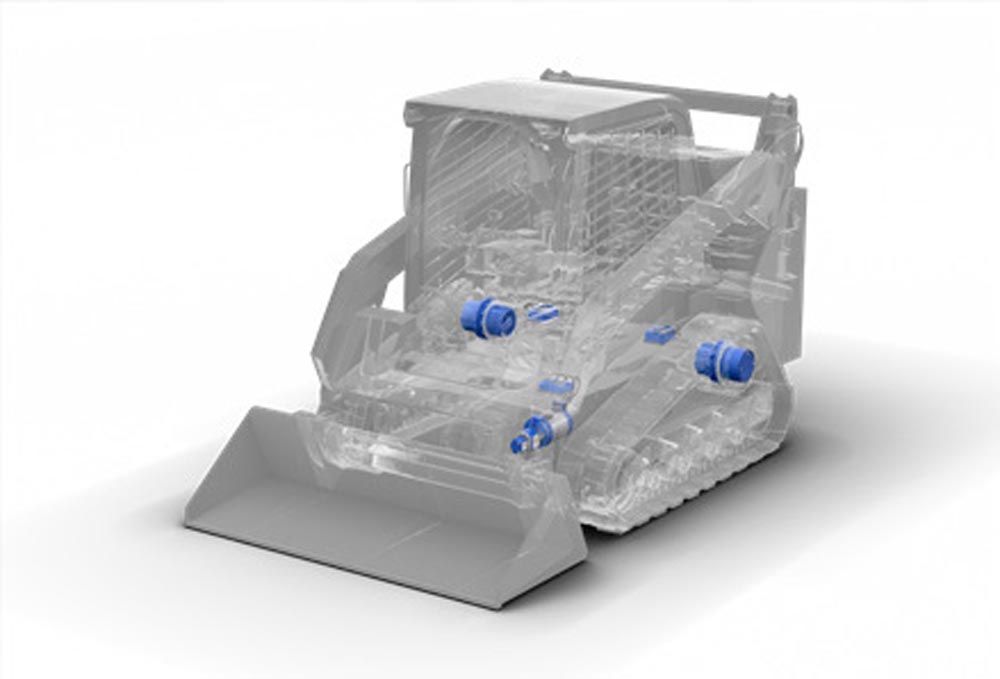
Bosch Rexroth Offers Gearboxes for Electric Motors
The off-highway market is constantly evolving. Mobile working machines are becoming increasingly efficient. At the same time, exhaust gas and noise emissions need to be reduced. Machine manufacturers from all sectors recognize that electric drives are an important building block for a future-viable, sustainable product portfolio.
“We’re a strong, growing and thriving business in America. We’re investing in our mobile hydraulics partnerships. In North America, we’re responsible for our mobile hydraulics, industrial hydraulics and factory automation business which is somewhat unique to Rexroth and allows us to provide solutions to some of our key OEMs in their plants to help them automate and streamline their manufacturing processes,” said Greg Gumbs, president and CEO of Bosch Rexroth Americas.
“IFPE is all about our customers,” Gumbs said. “We want to earn the right to have our customers love doing business with us. Our booth at IFPE was more than just components, it was about manufacturing solutions.”
“A lot of our offerings at Bosch Rexroth are to reduce oil usage in our hydraulic systems, reduce energy consumption, etc.,” said Thomas Donato, chief revenue officer, Bosch Rexroth. “You will find custom apps that enables our customers’ to utilize these technologies.”
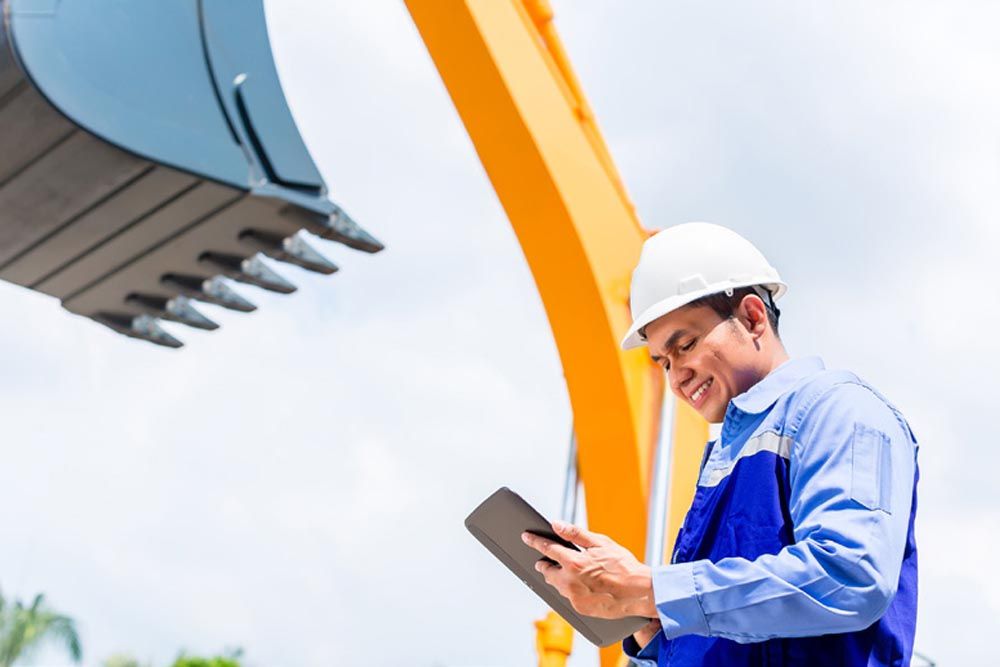
Technology is allowing customers in the off-highway and construction markets to better monitor oil usage, energy consumption and maintain equipment.
Regarding fluid control, Donato said that the boundaries of using software, electronics and electrification are becoming boundless.
“When you look at electrification, it’s a new space for many manufacturers in the off-highway and construction markets, and they’re looking for a partner with a really strong understanding of how these technologies can be applied on their machines.”
In order to support and drive the electrification of off-highway machines, Bosch Rexroth has developed two axle drives designed especially for electric motors.
Bosch Rexroth has developed spur gearboxes which vehicle manufacturers can use to unlock the full potential of new electric motors. The one and two-speed gearboxes are installed in the central section of the vehicle and pool the energy to drive up to two axles with just one motor. The clever integration of essential components is evidence of the wealth of practical know-how that was drawn on throughout the development process.
The 1-speed spur gearbox (eGFZ 9100) and the 2-speed shift gearbox (eGFZ 9200) are installed in the central section of the vehicle and therefore open a range of new options compared to previous approaches with individual wheel drives. Both gearboxes enable high power densities to be achieved while simultaneously ensuring noise optimization for high-speed electric motors such as the Rexroth EMS1H and the Bosch SMG, but also for motors of other manufacturers with similar power.
Permanent-magnet synchronous motors are famed for being compact and highly efficient. However, their high rotational speeds present real challenges in terms of noise emissions, temperature, impermeability, and splines. The eGFZ 9100 and the eGFZ 9200 have been specially developed for these applications. They also enable the power to be directed to one or both vehicle’s axles. For all-wheel drive, there is also the option to connect or disconnect an axle. A lockable center differential is also provided for permanent all-wheel drive.
When integrating the gearboxes into the installation space available and into the machine concept, Bosch Rexroth drew on the knowledge and experience gained from fulfilling requirements for previous drives. Gearboxes not only have to be compact and reliable but also easy to integrate. While the 1-speed gearbox (eGFZ 9100) can be installed horizontally or vertically depending on the relevant requirements, both Rexroth series feature a plug and drive system. Components such as the heat exchanger and oil pump available in the gearboxes enable both gearboxes to be seamlessly integrated into the existing cooling circuit of the electric drive.
Even the sensors for monitoring functions are already integrated into the gearboxes and can be adapted to suit a wide variety of applications using a range of different options. Machine manufacturers pursue different strategies in terms of voltage supply and battery storage requirements. To ensure that the installation space within the frame of the vehicle can always be optimally utilized, the eGFZ gearboxes with DIN ISO-compliant flange types enable a diverse range of drive solutions to be achieved. These can be executed in two-wheel drive as a U-shape or S-shape gearbox version and in four-wheel drive as a Z-shape version.
Company-wide knowledge of telehandlers, wheeled loaders, and municipal machinery as well as tractors and reach stackers was pooled at the start of the development process to determine which of these drives could be driven electrically and centrally in the future—and with which load collectives. The new eGFZ gearboxes were developed and optimized based on this set of requirements.
Bosch Rexroth now intends to work alongside its customers to determine the best solution for each specific application. The eGFZ 9100 and eGFZ 9200, which are currently being used in different pilot projects, will go into series production in 2022 as part of eLION. Rexroth’s platform for the electrification of mobile working machines covers the full range of electric motor-generators, inverters, and accessories as well as tailored gearboxes, hydraulics, and software.
boschrexroth-us.com