Hainbuch Delivers Precision Workholding to SEW-Eurodrive
From amusement park rollercoasters to cranes, mining equipment, conveyors, automotive assembly lines, and many other applications, SEW-Eurodrive manufactures the gearmotors, electronics, and software that keep things moving. Based in Bruchsal, Germany, the company maintains a network of 16 production plants and 79 Drive Technology Centers in 50 countries around the world. The plant in Lyman, South Carolina, one of the four facilities in the U.S., is staffed by the 300 employees and incorporates more than 100 robots in its automated production processes.
One of the principal products produced at the Lyman plant is the K series helical-bevel gear motor line, designed to deliver maximum efficiency and with low maintenance requirements with optimum ratio and torque.
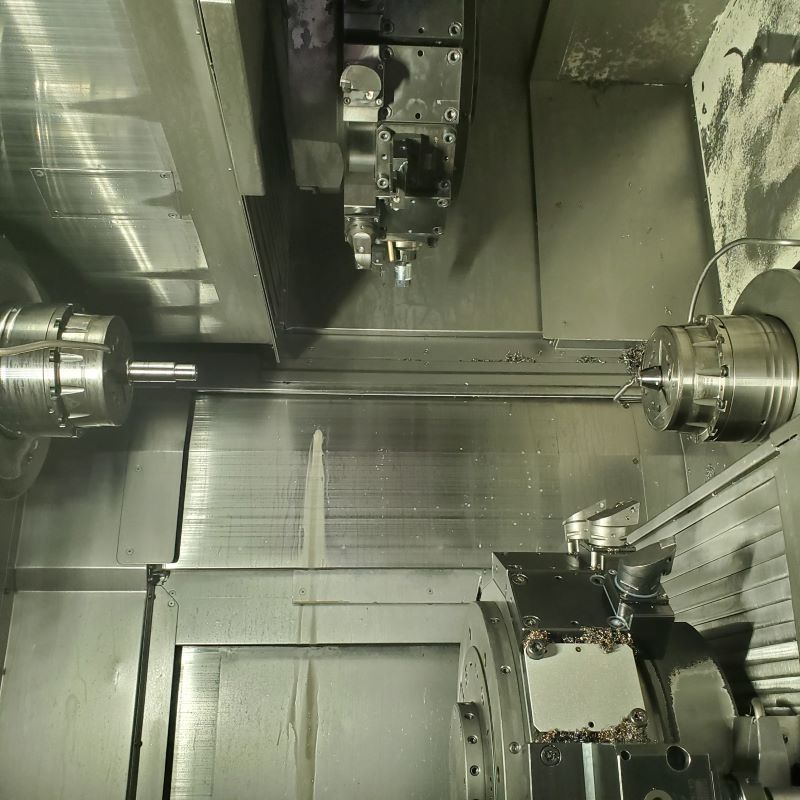
Larry Neely, toolroom supervisor at SEW-Eurodrive, comments, “Because our K box line is extremely popular and is used in many diverse industries, everything we have made for the last couple of years has been for customer orders. We don’t retain any inventory. In fact, demand is so high that, in the near term, we’re looking to double our production and, at present, we’re delivering more than 600,000 gear sets and housings per year,” said Larry Neely, toolroom supervisor at SEW-Eurodrive.
Quality control is critical to the manufacturing process, and tolerances are measured in microns. Robots are used to ensure maximum efficiency and accuracy.
“Among the most challenging applications is the turning of the high-ratio pinion. Machined from 8620 steel, the process involves two separate chucks—one for holding bar stock, where we turn the bearing journals, and the other for finishing the head. Parts are run on two Okuma twin-spindle turning centers. Because we are turning the bearing journals and the head on two different chucks, given our tolerances the machining process is exacting and complex,” said Neely. “When we initially evaluated the Hainbuch system of precision workholding, we reviewed our entire production strategy and realized extensive benefits in both time and money.”
Originally, parts were produced from individual 2-inch diameter blanks that were held between centers. This required the cutting and facing of each part. Because parts were held by the pinion faces, using face drivers, they would have inconsistencies on runout and need to be processed after heat treat, after which a press was used to correct runout.
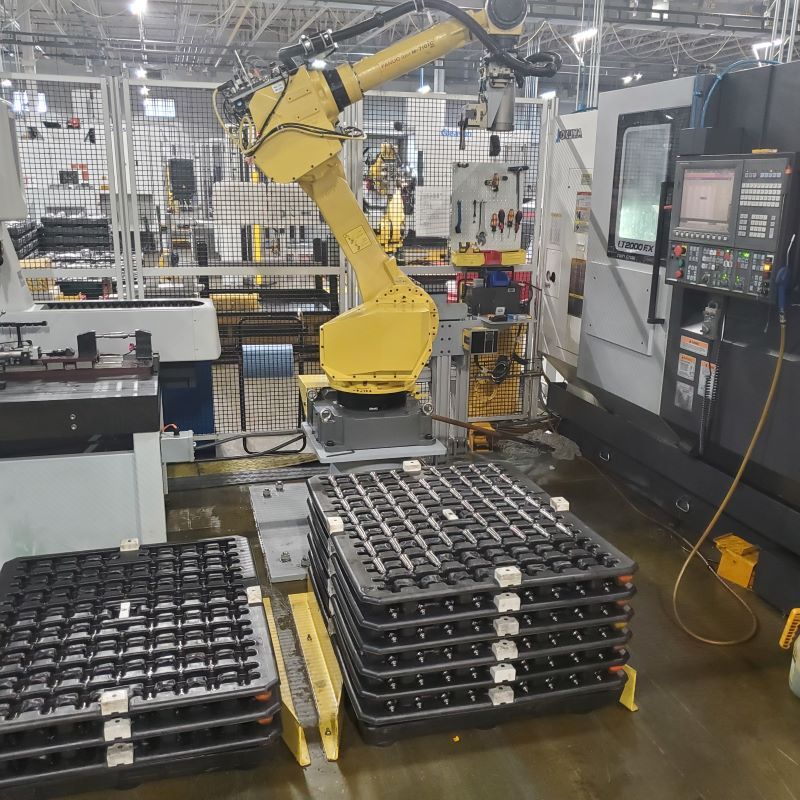