agma.org
Motion + Power Technology Expo Booth Previews
ANCA—Booth 3232
ANCA is delighted to be part of the MPT Expo where the company will showcase its latest products, services, and industry solutions. A mere 30 minutes away from ANCA’s American headquarters in Wixom, MI, the ANCA team is excited to showcase its technology right here in the company’s home state. Here’s what you can expect from ANCA at MPT Expo:
- Cutting-Edge Products and Services. Visit their booth to experience firsthand their latest CNC grinding machines and technologies. ANCA will have a GCX linear machine on the stand demonstrating its state-of-the-art process for gear power skiving.
- Expert Insights. Engage with their experienced professionals who will be available on-site to discuss how ANCA can help address your grinding needs and goals, now and into the future.
“We are thrilled to be a part of Motion + Power Technology Expo this year,” said Russell Riddiford, President at ANCA Inc. “This event provides a fantastic platform for us to showcase our latest innovations and connect with industry leaders. We look forward to meeting and interacting with both existing and potential clients to discuss how ANCA can provide tailored solutions to meet their grinding needs.”
anca.com
Cincinnati Gearing Systems—Booth 3213
Located in Cincinnati, OH, Cincinnati Gearing Systems (CGS) is a recognized leader in precision component gear manufacturing and design engineering. More than just a gear manufacturer, CGS offers customers over 100 years of experience in producing high-quality, reliable, and cost-effective component gearing and gear units for a wide range of power transmission applications. Configurations include epicyclic gear units, multiple pinion gear units, parallel shaft designs, vertical and horizontal offsets, dual and single input, single and double helical, and hybrid designs. CGS has in-house full-service manufacturing, design engineering, testing, and heat-treating capabilities. Whether it is a clean-sheet design or a standard design, CGS is the single source to satisfy your specific gearbox requirements.
Fracking Gear Unit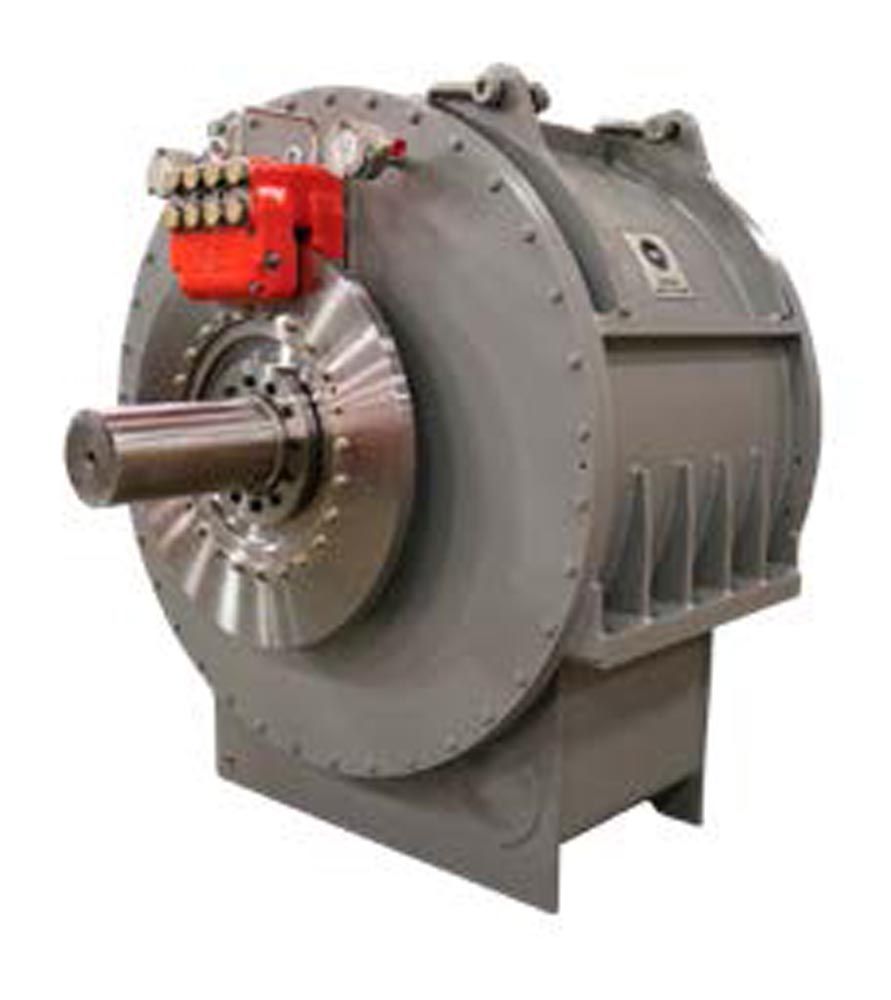
• Gas Turbine to Pump Drive
• Double helical gearing, epicyclic configuration
• 16,000/1,455 rpm @ 5,500 hp
• High efficiency, low noise replacement for traditional diesel engine pumping solutions
Hydrogen Compression and Expansion Services
• Expander to Generator Drives
• Parallel Shaft Single Helical API 617 Integral Gear Unit
• Expander casing flange mounted to gearbox
• Expander wheel integrally mounted to pinion shaft with Hirth connection
• 33,000/3,000 rpm @ 2,000 hp
• Used in the plastics production process
Faster Machining Processes
With the installation of the new Liebherr CNC shaper cutter, CGS has significantly reduced the machining time for double helical gears. This machine doubled previous cutting speeds.
The correction measurement in the machine substantially increases the quality of the gear; and due to the electronic helical guide, CGS can shape every helix angle without the need for additional tooling.
The new Kapp Niles gear grinder has automatic onboard checking and the capability to grind internal gears up to a 30-degree helix angle both left hand and right hand.
cincinnatigearingsystems.com
Cincinnati Steel Treating—Booth 3213
Located in Cincinnati, Ohio, Cincinnati Gearing Systems (CGS) is a recognized leader in precision component gear manufacturing and design engineering. More than just a gear manufacturer, CGS offers customers over 100 years of experience in producing high-quality, reliable, and cost-effective component gearing and gear units for a wide range of power transmission applications. Configurations include epicyclic gear units, multiple pinion gear units, parallel shaft designs, vertical and horizontal offsets, dual and single input, single and double helical, and hybrid designs. CGS has in-house full-service manufacturing, design engineering, testing, and heat-treating capabilities. Whether it is a clean-sheet design or a standard design, CGS is the single source to satisfy your specific gearbox requirements.
Component Gearing
Cincinnati Gearing Systems is IATF 16949 certified and has over 30 years of experience in producing custom component gears for various automotive and off-highway Tier 1 and Tier 2 customers as well as leading-edge electric drive applications still in development. From pinions, spur gears, and helical gears, to powertrain shafts, Cincinnati Gearing Systems can be your one-stop shop for all your component gearing needs. With over 100 years of gear manufacturing experience with our own heat-treating facility, Cincinnati Gear offers full-service precision gear manufacturing for prototypes, production, and high volume.
Transportation
• Internal Combustion Engine
• Electric Vehicles
• Off-Highway
• Automotive
• Powertrain
Military and Commercial Marine
• Mobile Power Generation
• Land, Surface, Subsea
• Shipboard Power
• Main Propulsion
Industrial
• Power Generation
• Industrial Gases
• Wind Energy
• Oil and Gas
• Mining
Faster Machining Processes
With the installation of the new Liebherr CNC shaper cutter, CGS has significantly reduced the machining time for double-helical gears. This machine doubled previous cutting speeds. The correction measurement in the machine substantially increases the quality of the gear; and due to the electronic helical guide, CGS can shape every helix angle without the need for additional tooling. The new Kapp Niles gear grinder has automatic onboard checking and the capability to grind internal gears up to a 30-degree helix angle both left hand and right hand.
steeltreating.com
Dontyne Gears—Booth 3019
Dontyne will be promoting improvements to design in the new Gear Production Suite 5.8 release and the new GPS CAM module which has enabled smaller companies or those requiring small batch runs to move production onto more flexible 5-axis CNC machine centers.
This intuitive hypoid design tool, launched in GPS 5.7, allows flexible design options and ensures complete conjugacy of the teeth through the mesh cycle before the appropriate micro geometry is applied, and has had immediate benefits for our customers. After meeting at PRI 2021, Tubeworks, based in the USA and involved in motorsport, has become an early adopter of our Hypoid software design package. The CAD file can be exported to any CAM package, or, for a more secure approach, the G-Code can be automatically generated from the designed surface using our GPS CAM module. They were able to produce components in-house quickly and at a low cost. Jayson Miles, CEO of Tubeworks commented “This has been a dramatic improvement on our previous approach using gear functions in our CAD system. Not only does it allow more design flexibility, meaning we can optimize our design, but we can roll check the contact in seconds to ensure it is constant over the mesh cycle. The software has helped reduce our development cycle for hypoids from weeks to days.”
In collaboration with Collins Aerospace based in Wolverhampton, UK, Dontyne has developed a dish cutter simulation for the fast production of Coniflex®*
bevel forms on a 5-axis machine using its GPS CAM module for the GPS 5.8 release. This approach uses a fixed tool, so it is not as versatile as the end-mill option but does allow more rapid production and higher volumes. Dontyne has been able to validate the result by producing test pieces on the Okuma at its Dontyne Gears facility in Washington, UK. Dontyne would like to thank the team at Collins Aerospace for their help on the project and look forward to furthering collaboration soon.
*Coniflex® is a registered trademark of The Gleason Works.
dontynegears.com
EMAG—Booth 2813
EMAG invites you to Booth 2813 where machining experts will be available to answer questions and talk about new advances in automated gear and shaft manufacturing.
See EMAG’s K 160 Horizontal Hobber in Action
Horizontal hobbers aren’t just for making shafts. Thanks to integrated automation and part size flexibility, they also work well for manufacturing high volumes of automotive pinions and gears. And, if your operation is looking to replace aging manual hobbing machines, EMAG’s long-bed version of this multiaxis machine can handle long shafts and heavy gears. Like the standard K 160, it comes with direct-driven performance drives, user-friendly and easy-to-program controls as well as built-in automation.
From Blank to Finished Component
Additional displays will cover the uses and advantages of laser welding and electrochemical machining as they relate to gear and shaft manufacturing. The EMAG Group is one of the few suppliers of manufacturing systems that cover the whole process chain—from soft to hard machining—for manufacturing gearbox, engine, chassis, and nonautomotive components. With a line of modular machines, EMAG offers various technologies and integrated automation on a standardized platform to reduce floor space and cost while maintaining world-class quality. Active in the automotive, oil field, power generation, and large equipment industries, EMAG is a trendsetter in the field of vertical turning and multi-functional production machines, allowing the customer to process workpieces in a single set-up.
The North American headquarters of the German-based company is in Metro-Detroit and is an important partner in the advancement of complete manufacturing lines. EMAG is ready to discuss a wide range of automated technologies including:
- Gear cutting and shaping.
- Profile and gear-generating grinding.
- Chamfering and deburring.
- Power skiving, turning, drilling, and milling.
- Laser welding, ECM deburring as well as PECM machining.
Stop by Booth 2813 and learn more about how EMAG can work with you to make your gear and component manufacturing more efficient, productive, and profitable.
emag.com
Forest City Gear—Booth 2809
Founded in 1955, Forest City Gear is a third-generation family-owned gear manufacturing company based in Roscoe, IL. By choosing to invest in the best technology available, Forest City Gear has developed into a world-renowned leader in fine- and medium-pitch gear development, manufacturing, and inspection. Forest City Gear is a member of the American Gear Manufacturers Association (AGMA), is AS9100D/ISO 9001:2015, ISO 13485:2016, ITAR certified, and Nadcap accredited for nondestructive testing.
FCG’s high-precision capabilities extend to spurs, helicals, involute splines, sprockets, worms, and worm gears. These gears are trusted worldwide in everything from telescopes to tractors, artificial elbows to aircraft, military lasers to race cars, printers to medical examining tables, and power tools to dental drills. They can even be found in outer space, most notably on the International Space Station and NASA’s Mars exploration rovers.
All FCG projects fall under one of two value streams: Make Complete or Cut Teeth Only. Make Complete projects are designed in collaboration with the customer and processed from raw materials to finish. Cut Teeth Only is operational work, in which customers provide specs and gear blanks, and FCG cuts the teeth. With FCG’s state-of-the-art facilities, continuous investment in the best machinery, and an inventory of more than 7,000 hobs and 5,000 shaper cutters, Cut Teeth Only gears ship out in ten days or less.
You can find FCG’s brilliant Make Complete and Cut Teeth Only engineers at Booth 2809, ready to design and plan the gears you need. Cheers to gears!
forestcitygear.com
Helios Gear Products—Booth 3609
Helios Gear Products will feature hobbing solutions including the Hera 350 CNC gear hobbing machine and the MSR rotary magazine with automatic loading at the MPT Expo.
Hera CNC gear hobbing machines support micro- to coarse-pitch gear manufacturing applications with advanced technical features such as complete Fanuc CNC and direct-drive torque motors, X-axis linear scales, easy-to-use (and train) dialog programming, and versatile unified automation systems. With competitive pricing, domestic support from the expert Helios team, and a unique combination of technical capabilities in a small footprint, the Hera machines offer both job shops and end-product gear manufacturers world-class hobbing solutions.
Of the 8 sizes of Hera machines available, Helios will be demonstrating the Hera 350’s ability to produce high-quality spur gears, helical gears, and other hobbed profiles with a maximum pitch rating of 4.23 DP. Jeff Kamps, Helios customer and President at Wisconsin Gear & Machine says, “We’ve cut our cycle times down from 4 hours to a half hour. It’s really been beneficial for Wisconsin Gear. With the shortage of people, it’s really made a big difference; we can still get a large volume of work done in a timely manner.”
Advancing gear manufacturing productivity even further is the new MSR. This rotary magazine with automatic loading offers comprehensive, versatile automation by integrating manufacturing cells with operations such as gear generation, washing, deburring, and laser marking. The MSR features stackable workpiece towers that offer more capacity than rotary conveyors and is offered with a variety of robotic loading options to feed up to four machine tools at a time for fully optimized gear manufacturing operations.
heliosgearproducts.com
Klingelnberg America—Booth 3426
Höfler Cylindrical Gear Roll Testing Machine R 300—The Gear Noise Finder
The metrology on the Höfler Cylindrical Gear Roll Testing Machine R 300 provides a reliable way to determine the root causes of gearbox noise. Due to the short measuring time, it can be easily integrated into any manufacturing process and enables 100 percent quality control of the gears produced. The R 300 is designed for all roll testing processes that are relevant for evaluating the running behavior and noise behavior of gears. These include the single-flank test, the structure-borne noise test, and torsional acceleration test, and the double-flank test. Depending on its equipment, the R 300 enables testing of gears and shafts, a particularly important factor for components from an electric vehicle drivetrain system (e-Drive).
For testing the e-Drive intermediate shaft, Klingelnberg will demonstrate a process for roll testing both gears on the shaft in one test cycle. This saves time for a second loading and unloading and for retooling the machine and reduces test costs.
P 152—The Solution for Medium-Sized Gears
The increasing cost pressure on large components for wind power requires new technologies that will enable proven principles for high-volume and mass production of smaller components to be transferred over to large components. The newly developed Klingelnberg Precision Measuring Center P 152 closes the gap in the portfolio between the mid-sized and the large precision measuring center model series.
The latest addition to the family is capable of measuring components with a maximum outside diameter of 1 520 mm and workpiece weights up to 8,000 kg with the usual measurement precision.
Despite this heavy workpiece weight, no special foundation is required. Klingelnberg has succeeded in scaling the technology concept of the small and mid-sized series to the larger component dimensions. The inherently rigid machine bed with its 3-point support plays a key role here. The bed design and floor support are so cleverly designed that even when loaded with heavy workpiece weights, the angular position of the individual machine axes to each other does not change significantly. The machine bed’s 3-point support enables the integration of an active vibration platform into the machine bed. This means that even the low-requency oscillations from the shop floor can be safely absorbed without the use of a vibration-isolating foundation. Consequently, all changes visible in the measurement results can be attributed to the component and are not induced by the ambient conditions.
klingelnberg.com
Liebherr Gear and Automation Technologies, Inc.—Booth 2800
Liebherr Gear and Automation Technologies, Inc. offers a complete gear technology and automation solutions program. Liebherr’s machines include gear hobbing, shaping, skiving, chamfering, and gear grinding machines, as well as gear metrology solutions. These machines feature the LHGearTec control system, an intuitive interface that streamlines machine operation and efficiency. In addition, Liebherr manufactures gear cutting tools and clamping fixtures, to provide full turn-key gear machining. Liebherr automation systems offer a wide range of cost-effective, user-friendly, and high-quality solutions and offer the flexibility to expand retrospectively.
At the MPT Expo, Liebherr will introduce the all-new LC 400 M gear hobbing machine, for use in various applications. With box guideways designed for maximum stiffness, this machine is rated for module 8 mm hobbing, and coupled with quick change fixturing the machine is extremely versatile for job shops. Liebherr will also present the WGT 400 gear inspection machine, similarly flexible for a variety of gear applications, and best-in-class accuracy, from e-mobility to industrial gearboxes.
liebherr.com
Machine Tool Builders (MTB)—Booth 3206
Machine Tool Builders Inc. offers gear producers the optimum solutions for the widest range of applications. Examples of these many technologies will be on display at the MTB exhibit at MPT Expo, Booth 3206. Visitors will have the opportunity to experience the many benefits of these new solutions, including:
• The Hamai N70, a CNC horizontal hobbing machine, is the latest in the Hamai series, a highly respected Japanese global brand with thousands of installations worldwide. With the N70, Hamai has made a quantum leap forward for more economical, more dependable production of high-precision aerospace and automotive gears up to 70 mm in diameter, and shaft lengths to 250 mm. The N70 has been completely re-designed to pack more power and precision into a very compact package, with extreme rigidity and the capacity for gears up to Module 2.5. Most importantly, it’s available fully automated to reduce nonproductive load/unload time to just three seconds. Equipped with the latest Fanuc controls, touchscreen, and Hamai’s operator-friendly programming, the N70 is also exceptionally easy for even less experienced operators to run day in and day out.
• The SMG SH410 Vertical Hobbing Machine, for parts as large as 410 mm in diameter, and workpieces to Module 8. It’s a powerful solution to meet the day-to-day demands and flexibility requirements of today’s gear jobbers. The machine combines high hobbing and table speeds and rapid x- and z-axis travel, with high rigidity, high torque, high-precision worktable, and powerful work spindle to cut cycle times while delivering high-precision gear cutting even at high cutting loads. This productivity is coupled with a variety of options with the gear jobber in mind: various automation configurations; onboard chamfering/deburring; provisions for extra-long shafts to 650 mm; and even hard skiving. It’s compact, highly rigid, ideal for both wet or dry hobbing, and available with Fanuc or Siemens CNC with easy, user-friendly dialogue programming.
• MTB’s comprehensive new recontrol/retrofit package for larger-capacity profile grinding gear machines with outdated controls, adding highly desirable performance at a fraction of the cost for new machinery. The package is built on state-of-the-art Fanuc or Siemens CNC platforms and includes MTB’s user-friendly Human Machine Interface (HMI) with Profile and Worm Conversational Software designed to simplify the operator’s programming, setup, and operational tasks, and help reduce costly nonproductive time, as well as the risk of operator error.
In addition, the MTB package includes provisions for advanced, fast, and flexible on-board wheel dressing, as well as optional onboard inspection featuring the latest Marposs or Renishaw 3D scanning probe technology (depending upon the machine, control choice, and application). The package includes all required mechanical and electrical components – standardized, up-to-date, and easily replaceable to help avoid early obsolescence.
“With the rate of today’s controls obsolescence increasing and the longevity of the physical machine tools today, upgrading your controls platform becomes important to remain competitive,” says MTB’s Ken Flowers. “This new recontrol/retrofit program is the best way for companies to extend the productive life of their older machines for years to come, take their performance to levels expected today, and at the same time save tremendously versus the cost of new equipment.”
The MTB recontrols/retrofit program is available for all major gear grinding machine makes and models, in size ranges 400 mm and above, and can be performed at the customer’s facility or at MTB, depending on the customer’s location, requirements, and machine size.
machinetoolbuilders.com
Nidec Machine Tool America—Booth 2300
In the spotlight is Nidec’s new CF26A Cut Chamfer System. This new chamfer machine was honored with the prestigious 53rd IDEA “Judges Committee Special Award” at the 53rd Machine Design Awards. Nidec’s Tool Design Simulation software creates the perfect chamfer shape before machining even begins. The specially designed ChamferX tools create the exact specified chamfer through the entire tooth, including the root.
The CF26A’s Unique Circuit Configuration saves time by aligning workpiece grooves and tool blades and the Dry-Cut Method is environmentally friendly with no need for coolants, reducing the ecological impact. Sharing the machine spotlight is the GE15HS. This machine features a specially cooled high-speed hobbing spindle that can operate at up to 6,000min-1, with stability and accuracy. The GE15HS can cut wet or dry and takes full advantage of Nidec’s Granmet SF hob substrate and Mighty Shield Σ coating for maximum productivity.
Complementing the fast cycle times of the GE15HS is the Load & Go system from Automation Within Reach. This automation system easily integrates with NIDEC gear machines and is easily changed over for a wide variety of parts. This combination provides the optimum solution for profitable production.
Federal Broach, part of the NIDEC family of companies, will exhibit a new broaching machine as well as Nidec cutting tools. Federal Broach will display their in-house tool sharpening and recoating services as well. In addition, visitors will see sample parts from NIDEC’s Lamda DED additive manufacturing systems.
Underpinning NIDEC Machine Tool America’s dedication to their customers’ success is an extensive program to have machine tools in stock for quick delivery. Hobbers, shapers, and gear grinders are all available for quick delivery and visitors can take advantage of MPT Expo special pricing. Visitors to the Nidec booth, number 2300, will also be able to discuss the financing and leasing options available.
nidec.com
Norton | Saint Gobain—Booth 3813
Saint-Gobain Abrasives, one of the world’s largest abrasives manufacturers, will be highlighting a range of high-performance, innovative production grinding wheels and technology at the MPT Expo. Norton Quantum Prime grinding wheels, which feature proprietary nanocrystalline ceramic grain offering high productivity gains across a wide range of applications, will be featured. The Quantum Prime grain delivers exceptionally high grinding efficiency and part quality, as well as significantly longer wheel life than traditional ceramic grains.
Also, attendees can see high-performance Norton IDeal-Prime internal diameter grinding wheels for precision applications featuring Quantum Prime nanocrystalline ceramic grain. The combination of the microfracture properties of the ceramic grain and the retention capability of the advanced bond, ensures long wheel life, excellent grinding efficiency, and consistent part quality with superior surface finishes which results in cost savings of 30 percent and more.
Additional key Norton grinding technologies at MPT Expo include:
• Xtrimium range of gear grinding solutions designed for high-performance gear grinding in extreme, tight tolerance environments will be featured. The portfolio of gear grinding products is specifically designed by category to provide higher profile accuracy, supreme form holding, and burn-free grinding in worm, profile, and bevel applications. Highlighting the range is an innovative dual-worm wheel design that enables two operations in one grinding wheel, substantially saving time and cost.
• For the high-performance external grinding of cam and crankshafts and internal grinding applications in automotive and bearing industries, Vitron7 cBN Grinding Wheels have a high-precision vitrified bond.
• Norton Finium abrasive microfinishing film rolls for precision applications are designed with a patented topside resin system alongside two backing types and an innovative grit size color coding. This combination is specifically engineered to deliver high material removal and exceptional surface finish uniformity.
• Norton Stellar inserted-nut grinding wheels for double- and single-disc grinding offer improved wheel life, increased parts per wheel, and lower cost per part.
nortonabrasives.com
Reishauer—Booth 2622
Reishauer continues to have a decisive influence on modern gear manufacturing. Since Reishauer developed the world’s first generating gear grinding machine, it has been driven to consistent innovation.
Reishauer provides solutions to improve your grinding and dressing processes and machine maintenance with the help of the company’s expertise and newly available data science. Process monitoring, optimizing with data analysis, identifying necessary maintenance work in advance, planning efficiently, and reducing downtime to a minimum.
Reishauer’s MPT Expo customer experience will provide an immersive technical journey. Empower your organization with myReishauer, a customer application platform connecting your organization to the digital world of Reishauer. Come see how Argus will keep an eye on your grinding process and the ways it will benefit your organization.
The RZ x60 4.0 series combines the proven machine basis of the RZ x60 series, including its highly efficient double-spindle technology with the latest control technology and modern interfaces, and is ready for future Industry 4.0 requirements. Immerse yourself in our virtual machine and experience Polish Grinding. Reishauer ensures customers can achieve the full performance potential of its generating grinding machines with the company’s own Swiss-made tooling.
Reishauer invites you to be their guest. Refuel yourself, charge your device, and connect your organization with technology and unmatched customer service in an experience that will add value to your production.
reishauer.com
Star SU—Booth 3209
As the exclusive North American representative of Louis Bélet SA (Switzerland) Swiss cutting tools, Star SU will display its line of high-precision drills, end mills, thread, and gear-cutting tools including hobs and skiving tools in Booth 3209 at the MPT Expo. This includes solutions for micromachining applications within the medical, automotive, aerospace, watchmaking, and general machining sectors.
The Louis Bélet product line expands the dimensional range of the Star SU portfolio of round and gear tooling to include micro tools as small as 0.05 mm and specials down to 0.02 mm for Swiss-style machining, as well as extended offerings in fine pitch gear-cutting tools.
Star SU will also be showcasing its wide variety of gearcutting tools including solutions for chamfer and deburring, hobbing, and milling, as well as scudding cutters manufactured to produce gear and spline teeth for reduced cycle times and tool costs.
Additionally, the company will be showcasing its full offering of machine tools for producing gears and other fluid power components. This includes interactive demonstrations or displays on FFG Modul vertical gear hobbing; chamfer, deburr, and rolling of straight or helical gears or shafts; Profilator scudding machines; and Star Cutter NXT 5-axis grinder for cutting and sharpening gear tools.
Star SU, which is the marketing, sales, and service partner for Star Cutter Company, offers a comprehensive line of products and services that enables customization of each cutting and tool grinding operation from cutting speeds and feeds to automation and tool coatings.
star-su.com
ASK THE EXPERT LIVE
Since 2015, Gear Technology has hosted live “Ask the Expert Live” presentations and the next edition will be held at the AGMA Media Expert Stage (Booth 3136) at AGMA’s Motion + Power Technology Expo (October 17–19 in Detroit).
The Future of Gear Manufacturing
Tuesday, October 17, 10:30 a.m., featuring:
• Joel D. Neidig, Director of R&D, ITAMCO
• John Perrotti, Chairman and CEO, Gleason Corporation
• Prof. Dr.-Ing. Karsten Stahl, head of the Institute for Machine Elements and Director of the Gear Research Center (FZG) at the Technical University of Munich
• Carlos Wink, Chief Engineer, Eaton Mobility Group
Manufacturing of Gears for Electric Vehicles
Tuesday, October 17, 2:30 p.m., sponsored by Reishauer, featuring:
• Pascal Diggelmann, Head of Application Technology, Reishauer
• Dr. Hermann J. Stadtfeld, Vice President Bevel Gear Technology, Gleason
• Dr. Oliver Winkel, Head of Application Technology, Liebherr
Automation for Job Shops
Wednesday, October 18, 10:30 a.m, sponsored by Schafer Industries, featuring:
• Rob Cherba, Automation Sales Manager, Liebherr Automation
• Geoff Dawson, Director of Michigan Regional Sales, FANUC America
• Ryan Finfrock, Engineering Manager, Schafer Industries
• Gerd Walter, COO, Creative Automation
Solving the Skilled Workforce Challenge
Wednesday, October 18, 2:30 p.m., sponsored by Forest City Gear, featuring:
• Kika Young, President, Forest City Gear
• Mary Ellen Doran, Executive Director, AGMA Foundation
• Kris Ward, Sr. Director, Strategy & Business Development, SME
• Megan Schrauben, Executive Director, MiSTEM