There are several challenges that can affect the cycle time and quality produced in profile grinding. These include:
- Grinding burns: Burning is usually the most crucial quality element in profile grinding. When not managed correctly, burning can cause scrap and increased cycle times.
- Form holding: The grinding wheel’s ability to hold form is the next most-important quality element, and it has a direct impact on cycle time and gear geometry.
- Operator skill level: It’s crucial that the operator has gear knowledge and machine training in profile grinding. Finding, training and retaining these operators can be challenging.
- Grinding wheel life: It’s important to choose a wheel that can achieve all the quality requirements while also providing the most tool life. Using the correct grinding strategy can help extend wheel life. This makes application training for profile grinding operators especially key to ensure they are using proper grinding strategies.
- Incorrect parameters: The overall grinding strategy must be determined first, then machine parameters can be programmed or adjusted. Using incorrect programming parameters in the profile grinding process can result in increased cycle time, poor gear quality, burning and increased scrap in gear production. Consulting with an application engineer, such as from an abrasives manufacturer like Weiler Abrasives, can improve results.
- Production bottlenecks: The profile grinding process can be a source of bottlenecks. For example, very large gears or a grind-from-solid operation may have a two-to-12-hour cycle time. A strategic change to the grinding wheel itself or perhaps a parameter adjustment can potentially cut that time in half or more.
Abrasive Product Options
When choosing a grinding wheel, many formulations are available. Depending on gear hardness, size and finishing method, different wheels will have different results. Other factors to consider include wheel size (width and diameter) as well as rated speed. Different types of wheels can provide varied cutting properties, durability and product life.
Typically, profile grinding operations select an open porosity, vitrified bonded wheel that uses either aluminum oxide grains or high-performance ceramic grains. This differs from the wheels used in continuous generating gear grinding, which typically uses a normal or non-induced porosity wheel. For profile grinding, it’s preferred to use a wheel with induced porosity, or very large pores, to reduce the risk of damaging or scrapping the part—which can add considerable cost to the operation—it’s important to use the correct wheel for the job. Even if the operation is not running the wheel at its maximum capacity, choosing the right wheel can help avoid disastrous results. One wrong grinding wheel can potentially cost a company thousands of dollars or more if the gear fails after it is installed and in use.
Look for an abrasives manufacturer that can assess your application requirements and produce a wheel for profile grinding that will deliver optimized performance. A quality manufacturer can engineer customized grinding wheels in a variety of grit sizes and abrasive grain types that are adapted for use with a wide range of CNC machines.
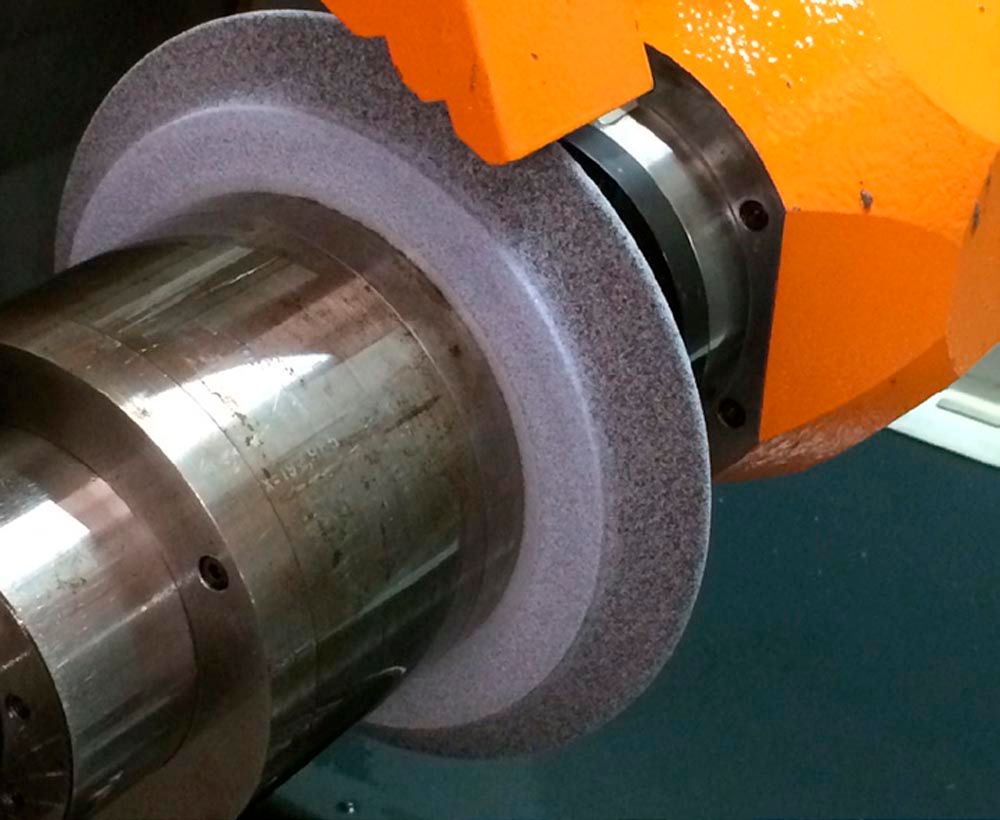
Profile grinding with the wrong wheel can add considerable cost to an operation. This example shows extreme loading on a profile grinding wheel because it was the wrong wheel choice for the job. Working with an applications engineer can help avoid this issue.
Four Tips for Profile Grinding
Optimizing quality and reducing cycle time in profile grinding requires attention to some important best practices. Grinding strategy also plays a pivotal role, so be sure to consider factors such as “how many teeth can we grind before we need to dress?” Keep in mind these four tips for profile grinding:
1. Better form holding:
There are two elements in the grinding cycle to consider: grind time and dress time. The in-cycle dress time can be between three to eight minutes or more. Therefore, the better you can hold the form, the longer you can cut between dress cycles and the faster your cycle time will be. This makes application training for profile grinding operators especially key to ensure they are using proper grinding strategies. Consult with an abrasives manufacturer to formulate a wheel with optimal grain and bond technology to maximize form holding.
2. Cooler cutting:
The most crucial quality element in profile grinding is the risk of burning. Burning, or tempering, is when the tooth surface has been exposed to very high temperatures from the grinding process. This can decrease hardness and cause stress to the gear material, resulting in cracking that will lead to gear failure. Most machines have high-volume coolant systems that allow for adequate flooding properties to wash away metal chips created by the grinding wheel as well as high-pressure nozzles to clean the wheel. Before a grinding wheel can be chosen, these conditions must be met or the wheel will not perform as designed. A wheel that cuts cooler can provide numerous benefits. As you increase performance and wheel aggression, it’s important to choose a cooler cutting wheel to avoid burning the part and possible wheel failure. A wheel grinds cooler by maximizing the exact timing of the grain releasing from the bond and by having the proper grain technology for the job. When a high-performance grinding wheel can cut cooler, it may be possible to cut faster. In addition, having the gear blank roughing process as accurate as possible or of optimal geometry and size before grind will lower the risk for quality failures and help stabilize the grinding operation.
3.Increase wheel life with higher cutting volumes (V’w):
Cutting volume is the measure of how much gear tooth material can be removed before the geometry must be corrected, also known as when form loss occurs. When a machine is set up, the form is dressed into the wheel and the gear is ground—so the form is on the gear. The same form on the wheel is copied onto the gear. How many times this can be done before the form is out of tolerance or unacceptable is known as the achievable cutting volume, which is a volumetric calculation. Remember, the in-cycle dress time can be several minutes; therefore, cycle time reduction can be achieved by optimal grinding and dressing strategy. Different grinding wheels have different cutting volumes. Generally, economical grinding wheels have a lower cutting volume, while high-performance wheels have a very high cutting volume. Higher cutting volumes will equate to longer wheel life and lower cycle time. A lower cycle time is achieved by reducing the amount of dress intervals. When the grinding strategy is correct and optimized, you will get the best result from a high-performance wheel.
4. Reduce cycle time with high material removal rates (Q’w):
Improving the material removal rate (MRR) will decrease cycle time. Material removal rate is a metric used to understand how fast workpiece material is removed by the grinding wheel. The higher the value, the higher the rate of removal. A higher MRR can be achieved by either increasing the amount of stock or increasing the wheel feed rate—or a combination of both. The formula for Q’w is:
Q’w = (ae * vw)/60
where,
ae = amount of material, units in volume
vw = feed rate, units in distance/time
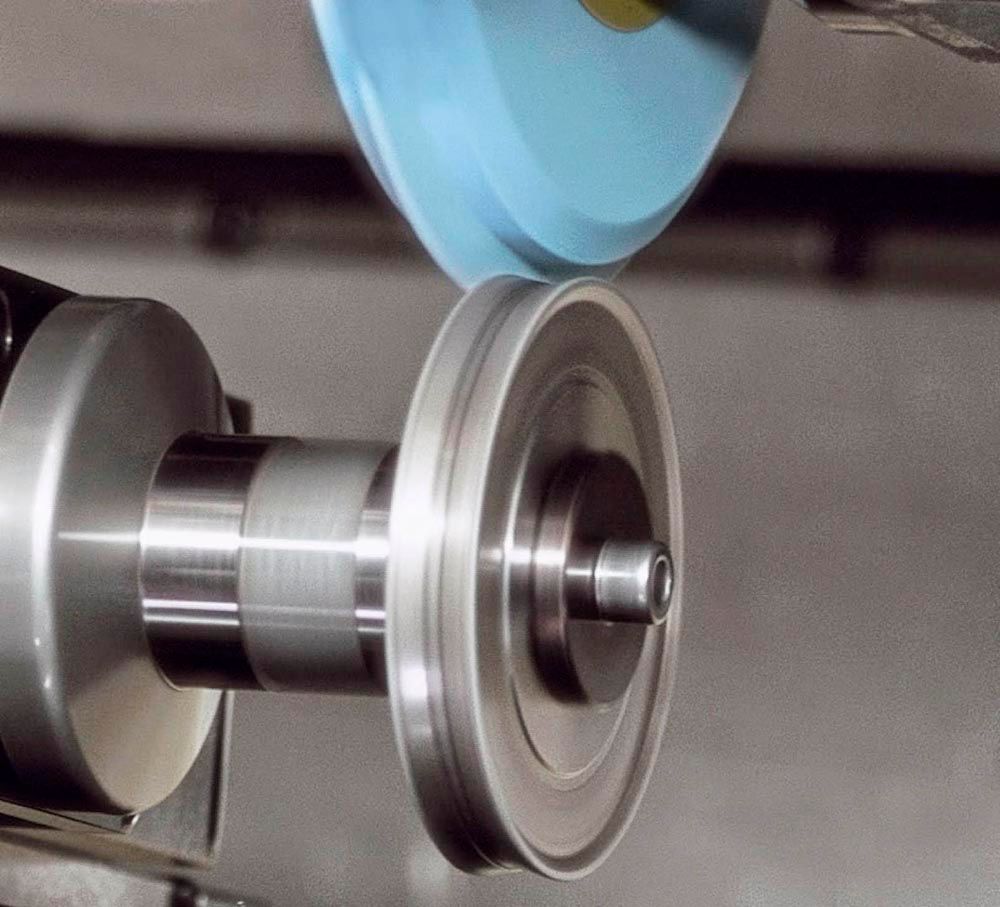
Action of a profile grinding wheel being dressed to demonstrate the method used.
Depending on the grinding wheel technology used, a high feed rate may be preferred instead of a low feed rate and high stock removal amount. This is a common factor used in grinding and is usually one of the first questions asked by operators. The Q’w formula shows you can adjust the material removal rate by understanding how to apply the correct grinding wheel technology to optimize stock amount, feed rate or both. It is important to note that gears with a low number of teeth have a variable Q’w along the profile from root to tip. Because the profile angle varies from root to tip on medium- to large-pitch gears, this type of gear will require a different grind strategy to achieve quality and prevent burn. As with other elements of the grind process, Q’w is impacted by the coolant system, gear geometry and other factors. Consider also that as you increase the removal rate in terms of feed rate, it can put added stress on the machine and cause premature machine failures, adding maintenance and downtime.
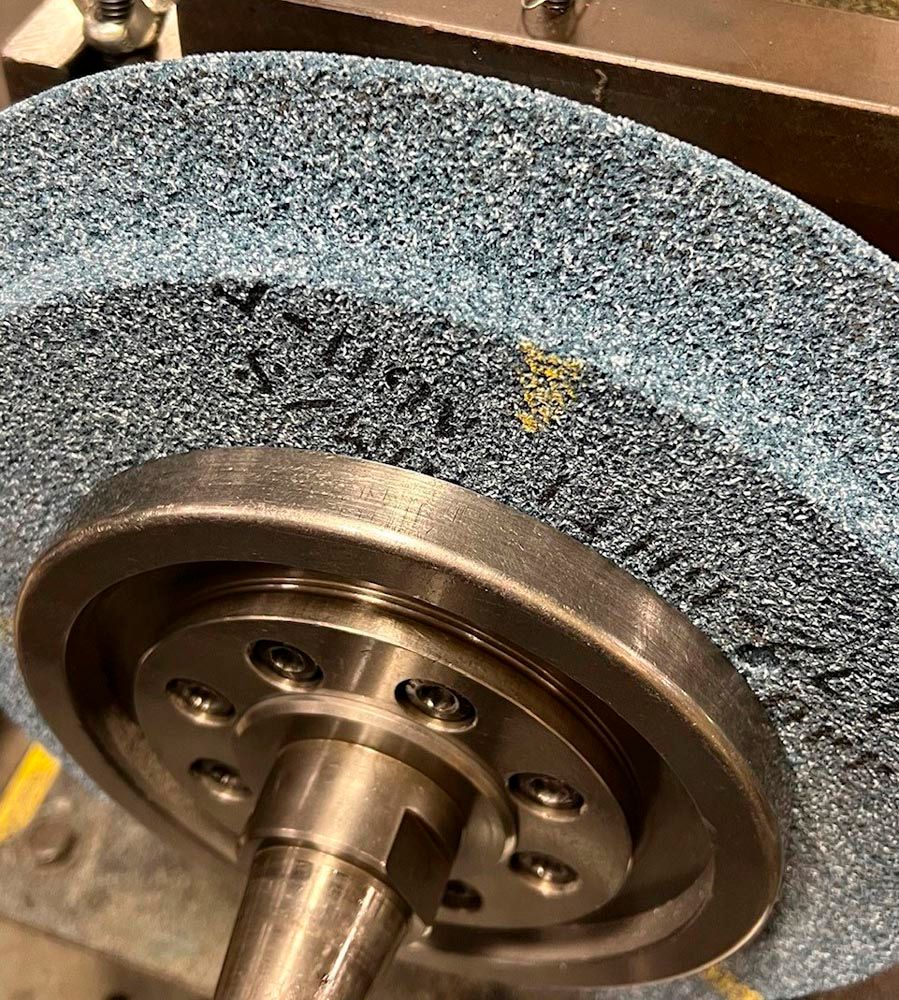
An open porosity, vitrified bonded wheel uses either aluminum oxide grains or high-performance ceramic grains. For profile grinding, it’s preferred to use a wheel with induced porosity, or very large pores, to reduce the risk of damaging or scrapping the part. This image shows an open porosity wheel after grinding with no sign of loading.
Improve Profile Grinding
Quality and efficiency are critical in profile grinding. A gear application engineer can design a grinding strategy for a specific gear before taking the machine offline and set-up begins. Working with an application engineer from a grinding wheel manufacturer will give the operator or tooling engineer valuable data to design the grind program with optimal grinding rates and cutting volumes for the specific wheel technology being proposed. They can also determine if the grinding wheel technology is correct or if it needs to be redesigned or changed. Manufacturers want to be cost-effective and reduce cycle time in profile grinding, but first and foremost they must maintain extremely high quality, making cycle prediction with programming crucial. The right grinding wheel manufacturer understands these challenges and can work with operators and engineers to formulate a wheel that is the best fit—to help save costs and optimize cycle time without sacrificing quality.
weilerabrasives.com