GT: What are some best practices that all gear manufacturers should be aware of?
TW: Utilizing deionized (DI) or reverse osmosis (RO) water for diluting metalworking fluids and wash chemistry is paramount, as it prevents the introduction of minerals and contaminants that can accelerate corrosion. Proper maintenance routines are essential, including accurate analysis of wash chemistry to ensure correct dilution and thorough cleaning. Effective washing, characterized by sufficient pressure to thoroughly clean parts, routine maintenance of nozzles to prevent clogging, and the use of appropriate temperatures, is crucial for removing contaminants.
Ensuring complete drying of parts is also critical; manufacturers should verify that parts are thoroughly dry, adjusting heat and drying time as necessary to prevent moisture retention. The handling of parts requires meticulous attention, with employees wearing clean and dry gloves to avoid transferring contaminants to the metal surfaces. When it comes to packaging, only clean and dry parts should be packed, with the parts’ temperature closely matching that of the room to prevent condensation. VCI packages should be securely sealed using tape, heat seals, zip ties, or by folding over, and resealed after every use to maintain integrity. For added protection, especially in larger or densely packed packages, the insertion of ZERUST VCI materials as interleave can offer additional protection against corrosion. Direct contact between metal parts and materials like wood, paper, or cardboard, which can introduce moisture and acidic conditions conducive to corrosion, should be avoided. By implementing these best practices, gear manufacturers can significantly reduce the risk of corrosion, ensuring that their products maintain their quality over time.
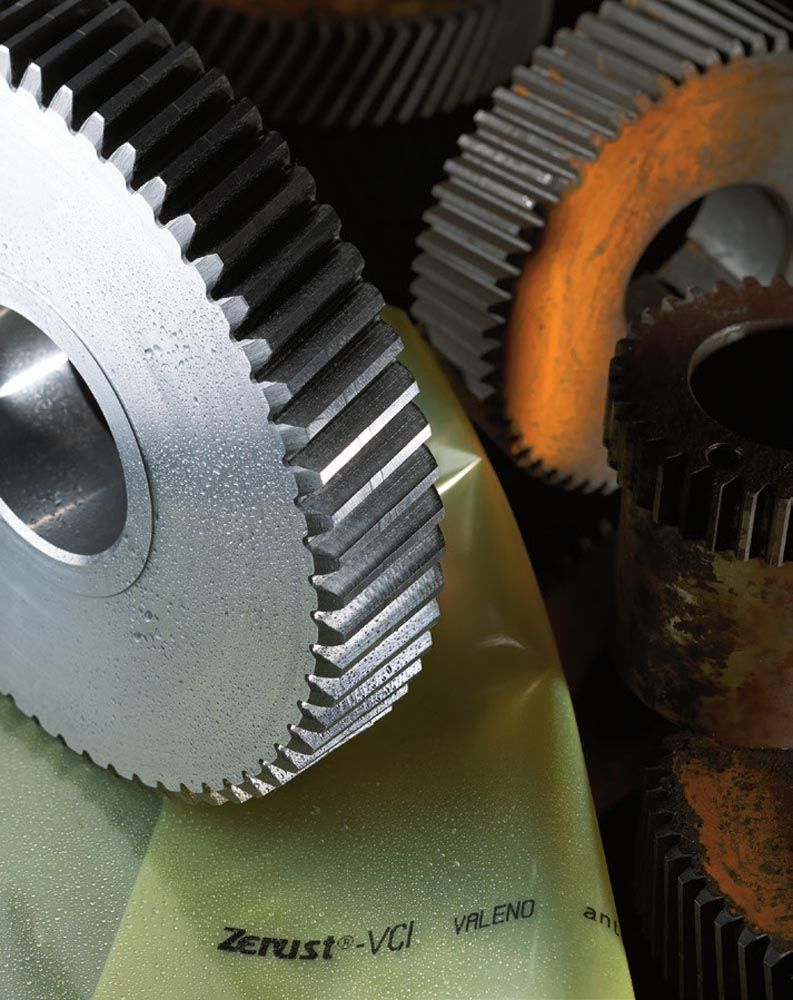
GT: What has changed in rust prevention technology over the years?
TW: For years, rust preventive coatings have been the cornerstone of corrosion protection strategies within the manufacturing sector, including gear production and metal cutting operations. These traditional methods have provided a reliable barrier against corrosion, yet their application and removal often involve the use of hazardous materials, posing safety and environmental concerns. However, the landscape of corrosion prevention is evolving as industry increasingly recognizes the advantages of Vapor Corrosion Inhibitors (VCI) technology.
VCIs represent a significant advancement, offering a safer, more efficient alternative to conventional coatings. Unlike their predecessors, VCIs eliminate the need to introduce hazardous chemicals into the manufacturing environment, addressing health and safety concerns. Moreover, parts treated with VCI are ready to use straight out of the package, streamlining the manufacturing and assembly processes. This immediate usability is particularly beneficial for the customers of gear manufacturers, as it removes the need for any additional preparation steps before the parts proceed to assembly or further processing.
This shift towards VCI technology is driven by the realization of its benefits, not only in terms of enhancing workplace safety and environmental compliance but also in simplifying logistics and reducing overall production times. As manufacturers continue to seek out solutions that optimize efficiency without compromising on quality or safety, the adoption of VCI for corrosion prevention is set to expand, reflecting the industry’s ongoing commitment to innovation and sustainability.
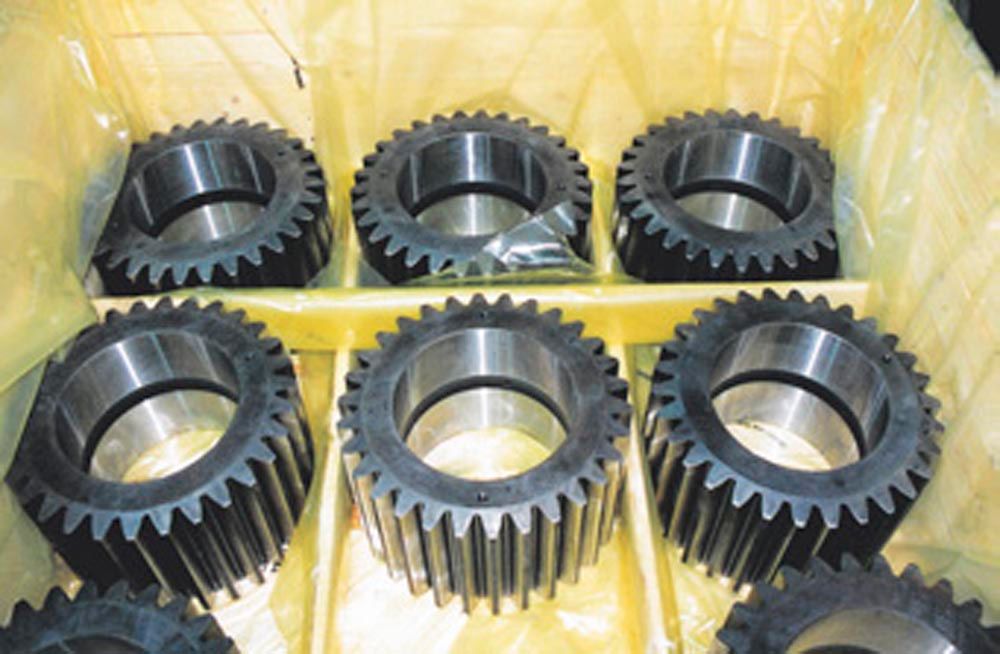
GT: How do ZERUST packaging solutions work?
TW: ZERUST VCI products prevent corrosion in several ways:
- By acting as a protective barrier from external corrosive elements such as abrasion, water, dirt, and acid gas pollutants.
- By emitting Volatile Corrosion Inhibitors that passivate the electron flow between the anodic and cathodic areas on metal surfaces and interrupt the electrochemical corrosion process.
- By adding water repulsion properties to the metal surface, which inhibit water from permeating the metal surface and providing the electrolyte for corrosion reactions.
The vapor corrosion inhibitor portion of ZERUST VCI products is made of proprietary chemical formulations that are invisible, odorless, non-toxic, non-reactive, non-flammable, and non-allergenic. These chemical formulations release a corrosion inhibiting vapor that diffuses throughout an enclosure that either contains VCI formulations or is made from VCI materials and settles on exposed metal surfaces to form a microscopic corrosion inhibiting layer.
This protective layer will remain on the surface of the metal if there is no significant, continuous exchange of air within the enclosure. Ideally, there should be less than one air exchange per day (for example, when an electrical cabinet or package is opened briefly and occasionally). Once the metal part is removed from the enclosure, the corrosion inhibiting layer is no longer kept in place by equilibrium with the VCI source, and it dissipates from metal surfaces (typically within about an hour), leaving the metal part clean, dry, and corrosion-free.
The vapor diffusing properties of our corrosion inhibiting formulations offer an important advantage over conventional inhibitor coatings since the traces of these gas molecules penetrate hard-to-access crevices, gaps, and slots. They also cover the surfaces of complex-shaped articles that are difficult to coat. They are adsorbed onto the surface of the metal to form a corrosion inhibiting protective layer that is just a few molecules thick. ZERUST VCI products may also include acid gas absorbing chemicals in the packaging material to act as a barrier and add another dimension to the protection of the metal content. These “scavenging” chemicals react and neutralize the polluted air that may diffuse through the ZERUST VCI material. Also used are various combinations of physical barrier properties that optimize the corrosion prevention and physical protection needs of our customers. These may range from plain low-density polyethylene (LDPE) material to combinations of higher strength, higher tear resistance, higher resistance to sunlight or UV, static charge dissipation, and lower diffusion for moisture or acid gas molecules.
ZERUST VCI products offer corrosion protection without having to be in direct contact with or coated onto the parts that are being protected. Metal parts merely need to be enclosed in or with a ZERUST VCI product (where airflow is minimized) for protection to occur. With ZERUST VCI packaging, it is no longer necessary to apply messy oils, greases, and other corrosion protection compounds and incur the cost of their removal.
GT: Is the chemistry of these products inappropriate for any types of parts (due to chemistry, material or end use)?
TW: ZERUST utilizes a variety of VCI formulations to provide the best possible protection for customer’s specific parts and packaging, rather than a suboptimal one-size-fits-all solution. The selection of the correct corrosion protection products is critically dependent on various factors, including the type of metal substrate, the required duration of protection, and the specific conditions under which the parts will be stored or shipped. It’s essential for customers to select the correct products or chemistry to safeguard their gears effectively.
Customers are encouraged to consult with a ZERUST/EXCOR representative to identify the most effective comprehensive corrosion management solution for their metal assets. This ensures that the chosen products are not only compatible with the parts’ materials and intended use but also aligned with the environmental conditions and protection duration required, thereby optimizing the longevity and integrity of the gears and other metal components.
GT: How does a manufacturer determine the root cause of his corrosion problems?
TW: Determining the root cause of corrosion problems can be a complex process that requires a comprehensive approach to identify and address the underlying factors contributing to the issue. Manufacturers facing corrosion challenges can effectively resolve these issues by contacting ZERUST. Utilizing the ZERUST Corrosion Inhibiting System (Z-CIS), a proven methodology designed to deploy complex corrosion management systems, manufacturers can ensure the protection of their metal product shipments throughout the global supply chain.
When a manufacturer reaches out to ZERUST, the process begins with a comprehensive site visit where the ZERUST team collects product samples directly from the manufacturing site, alongside samples of all processing fluids and wash chemistry used on the production line. This step is crucial for understanding the specific conditions that may contribute to corrosion, including the evaluation of climatic stress impacts associated with shipping routes. Furthermore, the team updates process Failure Mode and Effects Analysis (FMEA) documents and reviews process control plans to gain a holistic view of the manufacturing and handling processes.
Following the collection and analysis phase, the products and fluid samples are rigorously tested in one of ZERUST’s regional laboratories around the world to assess corrosion management system compatibility. Based on the results of these tests and the comprehensive analysis conducted, the ZERUST team formulates and recommends a tailored corrosion protection system, which may include one or several solutions, as outlined in the Z-CIS Deployment Recommendations document.
This systematic and meticulous approach enables manufacturers to pinpoint the exact causes of their corrosion problems and implement the most effective solutions, ensuring the integrity and longevity of their metal products.
GT: What are a manufacturer’s typical objections to the various solutions? How do they justify the added cost?
TW: Manufacturers often express reservations about implementing corrosion prevention solutions, with the most frequent objection stemming from the need for approval from their clients, who are the ultimate recipients of the parts they produce. This approval process usually requires ZERUST’s involvement in conducting necessary tests and demonstrations to get a ZERUST product specified or approved for use. Many manufacturers initially perceive this process as overly burdensome and time-consuming, hesitating to embark on what appears to be an extensive approval journey.
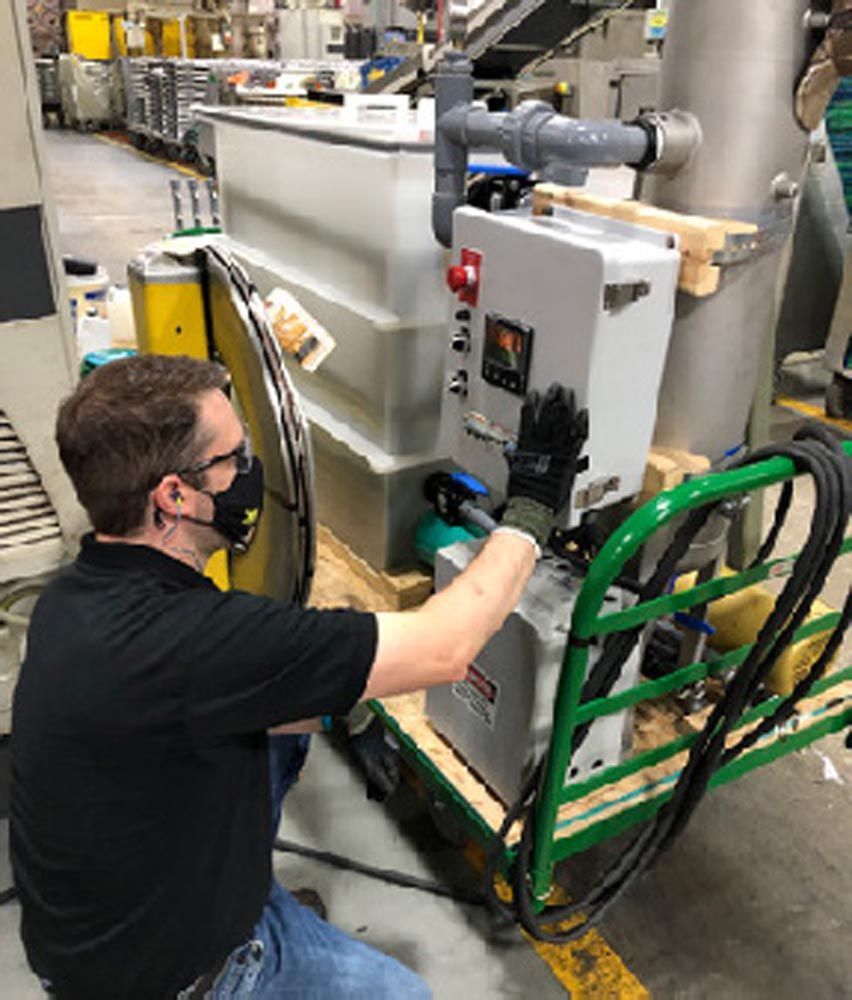
However, the reluctance typically shifts when the tangible consequences of corrosion become undeniable, often evidenced by the rejection of parts due to rust. This scenario underscores the immediate and long-term implications of inadequate corrosion protection, compelling manufacturers to reconsider their stance. The initial perception of Vapor Corrosion Inhibitors (VCI) and other corrosion prevention measures as merely an additional expense begins to wane when faced with the direct costs associated with corrosion, including rework, disposal of compromised parts, and the negative impact on client relationships.
By adopting corrosion prevention solutions, manufacturers effectively invest in the longevity and integrity of their products, realizing cost savings that far outweigh the initial investment in corrosion protection measures. This strategic approach to managing corrosion ultimately proves to be a cost-effective decision, supporting both the manufacturer’s operational efficiency and their standing in the competitive market.
ntic.com