In either case, the dressing time should be kept as short as possible even with complex form requirements for the grinding tool. Image 2 shows the portfolio. Multi-ribbed, full form profile rolls are the newest and fastest member of the family and deserve special mentioning – they are the sprinters amongst the dressing tools. Depending on the number of ribs, the dressing time can be reduced up to 2/3 compared to traditional diamond profile rolls. These dressing rolls are workpiece specific, i.e. they are specifically developed for a unique workpiece with pre-defined geometry. These rolls are plated using a reverse galvanic plating process.
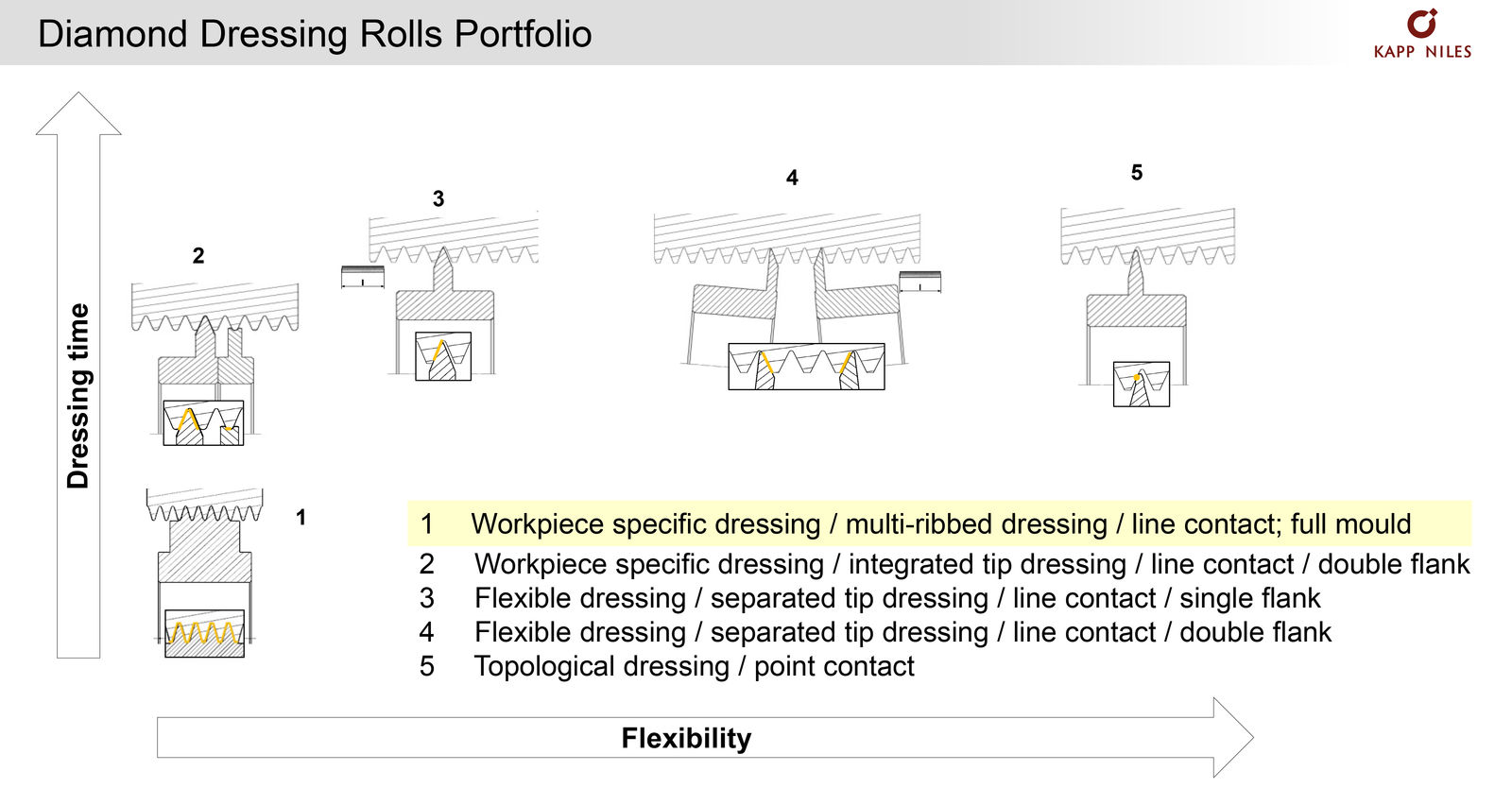
Image 2: Balancing dressing time and flexibility: From large series manufacturing to prototype grinding there is a suitable dressing tool for each application.
Further time savers are dressing rolls with integrated tip dresser, which in addition to dressing the ceramically bonded generating grinding worm to the workpiece profile also dress the tip of the worm at the same time. This saves one extra step, as long one can do without the flexibility that separate dressing of the grinding tool outside diameter offers. The illustration demonstrates the various levels of flexibility depending on the tool selection.
Topological dressing offers the highest flexibility: the dressing tool has single-point contact with the ceramic tool to generate just about any form. A typical application for such tool is prototype production.
Quality characteristics of dressing rolls for generating grinding
Kapp Niles dressing rolls can be produced using either synthetic or natural diamond. Dressing rolls with small radii are reinforced with CVD inserts which are extremely wear resistant. The profile accuracy is 2 micrometers, the module can be smaller than 1.0 mm.
Generating simulations calculate and determine the dressing tool geometries and allow for the manipulation of typical gear parameters such as profile modifications, root form and bias. Depending on the extent of wear, the dressing rolls can be re-lapped or completely reprofiled.
Dressing of grinding wheels for profile grinding
The dressing of grinding wheels requires a so-called diamond form roll (image 3).
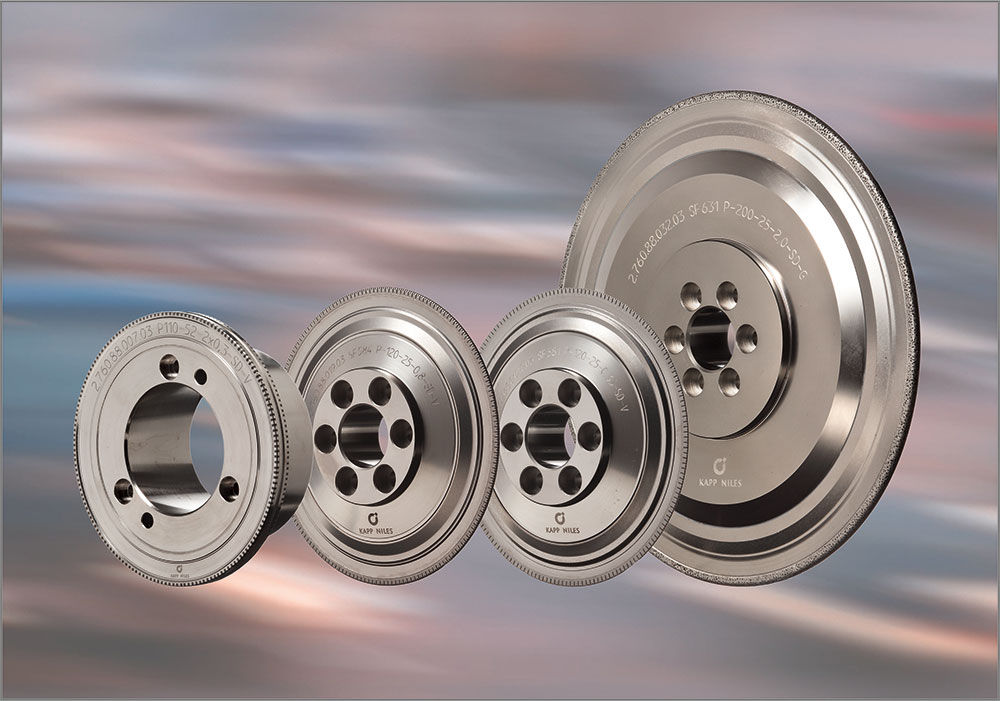
Image 3: Kapp Niles diamond form rolls for dressing of grinding wheels.
The geometry of such tool consists mainly of a high-precision radius and is not as complex as that of a dressing roll for the generating grinding process. The variety of tools is smaller, accordingly. There are two main types: rolls with single and rolls with double radius (image 4).
Image 4: Diamond form rolls are available with single radius (left) and double radius (right). The latter offers small radii for high-precision profile grinding with high stability.
The latter are used for reasons of stability: the tool has less of a chance to lose its form through contact with the grinding wheel to be dressed, especially for tools with small radii. Diamond form rolls are available with a radius ranging from 0.1 – 3 mm and a tool outside diameter from 80 – 230 mm.
Quality characteristics of diamond form rolls
Diamond form rolls allow for a profile accuracy of 2 micrometers (image 5), same as dressing rolls.
Image 5: A grinding wheel in a transmission plant (left); the dressing is done by a diamond form roll (right)
There are two different types of plating of dressing tools. One type is CVD (Chemical Vapor Deposition) inserts which reinforce the profile. Depending on the wear, CVD-reinforced dressers can be re-lapped 5 – 6 times and still guarantee the same profile quality. The alternative to CVD-reinforcements is sintered natural diamond. This type is approx. 20 % less prone to wear compared to synthetic diamond. Diamond sintered form rolls, however, can rarely be re-lapped.
Dressing of honing rings
To round off its product palette, Kapp Niles also offers diamond dressing gears for honing rings. Due to process related reasons, these tools are plated with synthetic diamond. The profile accuracy is in the range of 2 micrometers depending on application. The module can be less than 1 mm.
What does the future have in store?
Non-dressable CBN tools, by all means, are still warranted. Certain grinding applications require that ceramically bonded tools be reprofiled quite frequently. In a worst case scenario, this could be so time-consuming that dressing becomes unattractive. Or the customer prefers the easier handling of non-dressable tools which is indeed an advantage. The trend, however, leans towards dressable tools. Kapp Niles has positioned itself in this highly specialized market to be a supplier of machines, tools and processes. Uebel: „We can offer a customer an individually specified gear grinding process for just about any feasible workpiece. We are a turnkey systems partner and customers do not have to engage different suppliers.”
For more information, please contact service-usa@kapp-niles.com
Author
Martin Witzsch, free-lance journalist for Kapp Niles (www.witzsch.com)
Haßfurter Straße 20, 91056 Erlangen
Tel.: 09131 / 9266725
info@witzsch.com