Gear Quality Inspection
Three gears of each material were subject to geometric quality measurements on a Zeiss CMM machine, employing a Zeiss VAST XXT scanning sensor (Figure 2). The measured gear parameters were profile, lead, pitch, and runout, which were characterized according to ISO 1328 (Ref. 9) gear quality inspection standard. The evaluated parameters and the associated quality grades are summarized in Table 2. Based on the evaluated quality grades, which were at a comparable level for all seven grades, it can be concluded that the gear’s quality grade did not have a notable effect on the gear pair’s NVH response during testing.
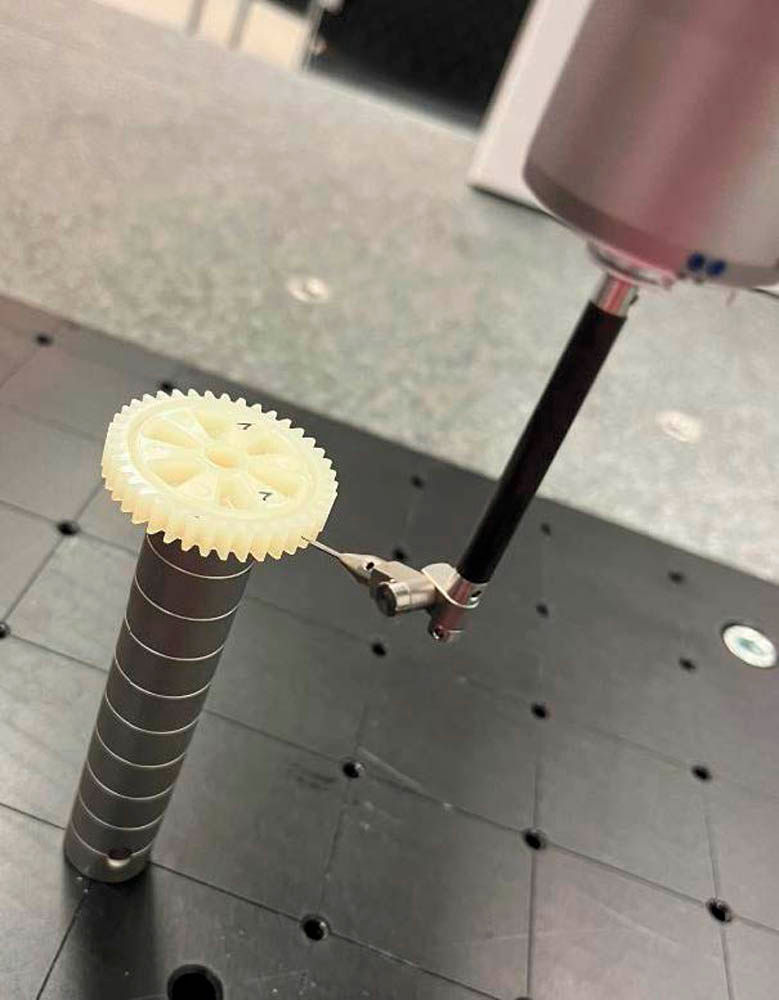
Figure 2—Sample gear during the geometric quality inspection.
Testing Conditions
The gear pairs were tested inside a closed acoustic chamber, mounted on the gear test rig, isolating the tested gear pair from the surroundings. That way only the noise generated by the tested gear pair could be measured, without major influence from other noise sources. Rotational speed, torque and gear temperature were precisely controlled during all tests (Fig. 3). As the NVH performance depends on the operating conditions, the gears were tested at two torque levels, and for each torque level at three rotational speeds, evaluating the effect of both operating parameters. The gear temperature was controlled at 80 °C in all tested cases. The tested loads are summarized in Table 2. The tests were run in dry conditions. For each material combination, three test repetitions were conducted. A new gear pair was employed for each test. The center distance at which the gears operated was precisely set by a precision positioning mechanism with an accuracy of 0.01 mm.
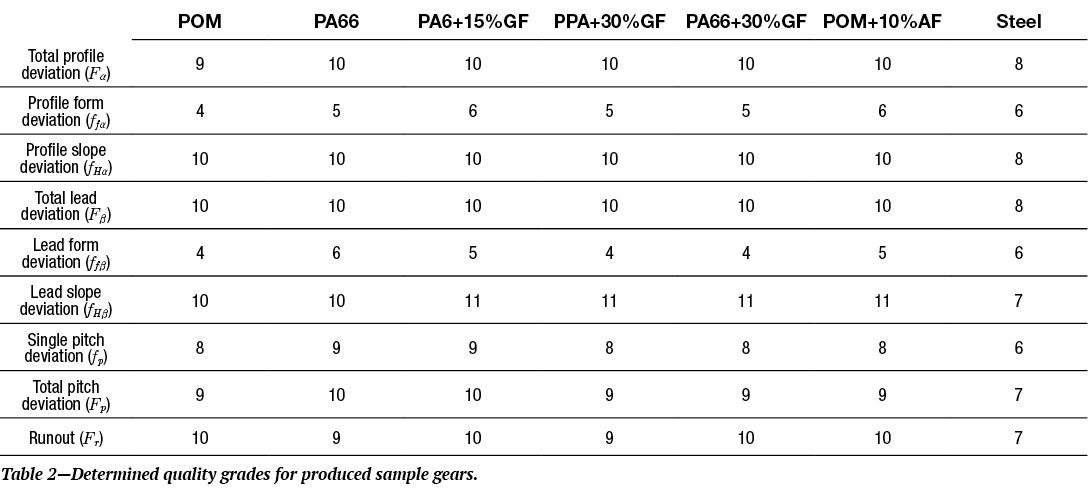
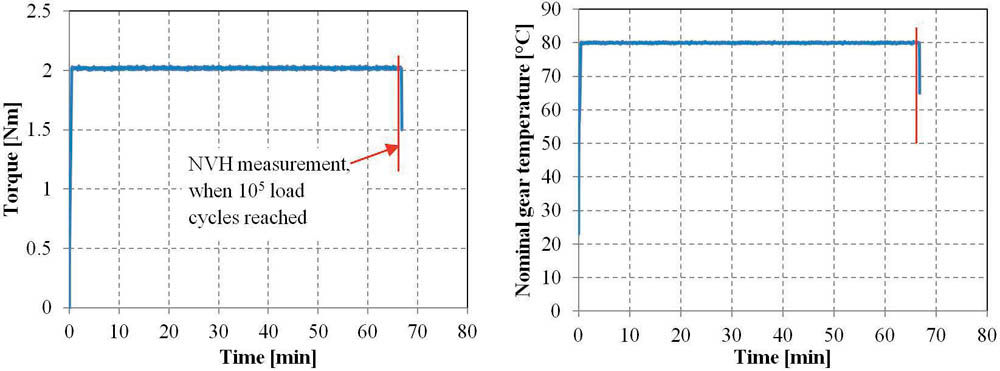
Figure 3—Torque and gear temperature were precisely controlled.
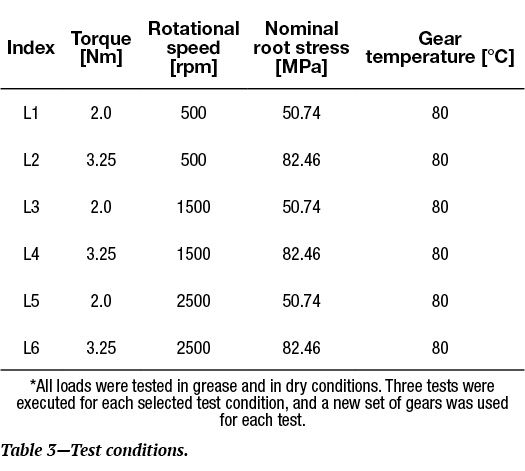
Six material combinations were tested, employing grades commonly used for gear applications. A steel gear pair of the same geometry was tested as a benchmark for comparison. Tested material combinations:
- Steel—Steel (reference) (536.30 MPa)
- POM—PA9T+30%GF
- PA66—PA9T+30%GF
- POM—PA66
- PA6+15%GF—POM+10%AF
- POM—PA66+30%GF
The testing setup is presented in Figure 4. A Dytran 3055D1T (Dytran Inc., USA) accelerometer was mounted on the bearing housing near the driven gear and a PCB Piezoelectronics 378B02 (PCB Piezoelectronics Inc., USA) free-field condenser microphone was placed in front of the tested gear pair. Data acquisition was conducted by using Dewesoft’s SIRIUSm (Dewesoft, d.o.o., Slovenia) module. The tests with plastic gears were run for 105 load cycles, where the operation was considered to reach steady state conditions, and the wear was not yet present affecting the NVH performance. After the 105 load cycles had been reached, the noise and vibration signals were captured. The duration of each measurement window was 10 s, with a sampling frequency rate of 20kHz. Signals, as presented in Figure 5, were acquired in each measurement. Steel gears were run for just a few minutes for the torque and rotational speed to stabilize; after that, the NVH measurement was made.
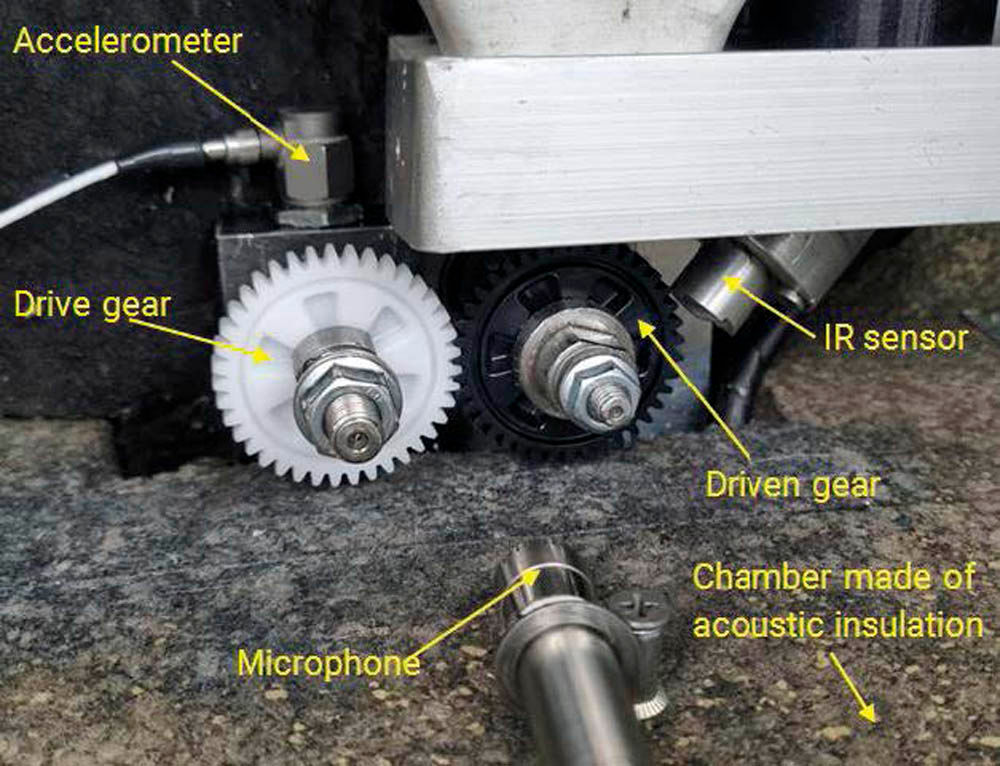
Figure 4—NVH testing set-up.
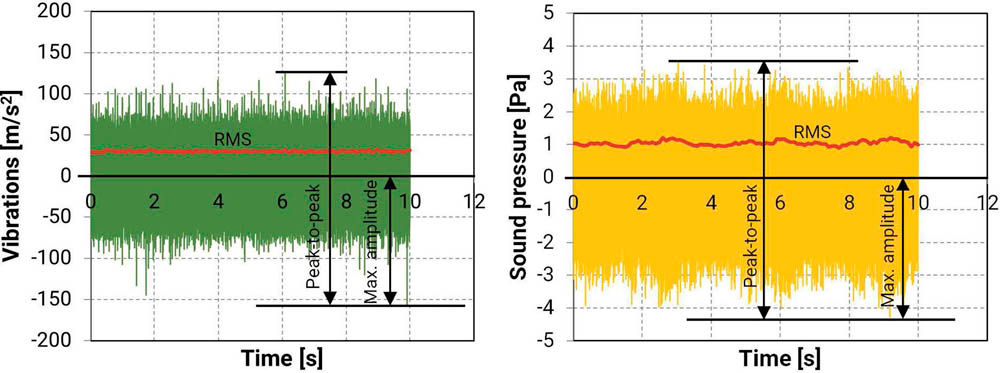
Figure 5—Acquired vibrations and sound pressure signal.
Three metrics are usually evaluated for the acquired signals, i.e., the peak value (max. amplitude), the peak-to-peak and the RMS value. The metrics are presented in Figure 5. The peak and peak-to-peak values represent only a single point value and do not consider the total signal energy; any fluctuation or transient vibration of a higher value can influence this metric. The increase of peak value or peak-to-peak may indicate the appearance of impacts in the signal, which can be isolated once a time. The RMS (root mean square) value is the effective value of the signal. It is calculated based on the entire sample using the following equation:

(1)
More practically, the RMS value measures the vibratory energy of the system. Unlike the peak and peak-to-peak values, the RMS value is not a point value, but rather a representation of the total signal energy.
The measured sound pressure was converted to sound pressure level, which is a logarithmic (decibel) measure of the sound pressure relative to the reference value of the 20 µPa threshold of hearing. The threshold of hearing is the quietest sound that most young healthy people can hear. The following equation was employed for the conversion:
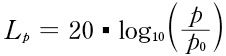
(2)
where p is the root mean square sound pressure and p0 is the reference sound pressure (20 µPa or 0.00002 Pa).
Results and Discussion
The average RMS values of the sound pressure level results are presented in Figure 6, and the average RMS values of measured vibrations are in Figure 7. The results show an average of three tests at each tested operating condition, and the error bars represent one standard deviation between the measured values. A relatively linear increase of measured sound pressure level could be observed for the benchmark steel gear pair while a much more complex behavior was found for the plastic gear pairs. The measured noise levels for the steel gear pairs were approx. 10 dB higher than the loudest tested plastic gear combination. Between the plastic gear pairs and at the lowest tested rotation speed, a difference of 10 dB could be observed between the best-performing and the worst-performing combination. Increasing the rotational speed led to an increase in the measured sound pressure level. A small difference between the measured noise levels could be observed at the highest rotational speed. It should be noted that an average person can distinguish a sound pressure level difference of 3 dB, which can hardly be recognized, especially at noise levels above 100 dB.
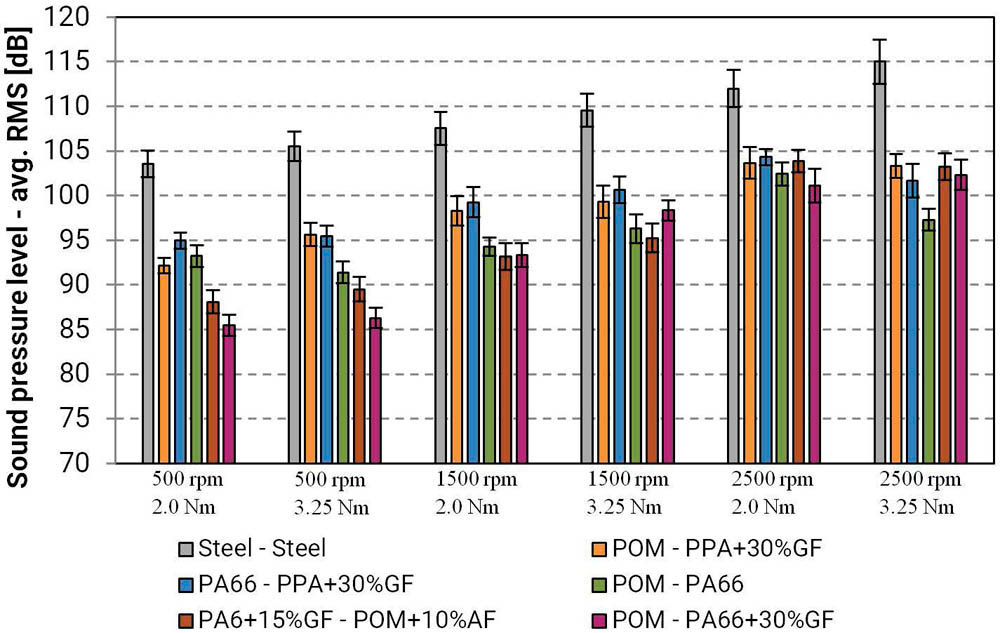
Figure 6—Sound pressure level, measured for the tested gear pairs. The temperature of plastic gears was controlled at 80°C in all tests (temperature measured on the teeth).
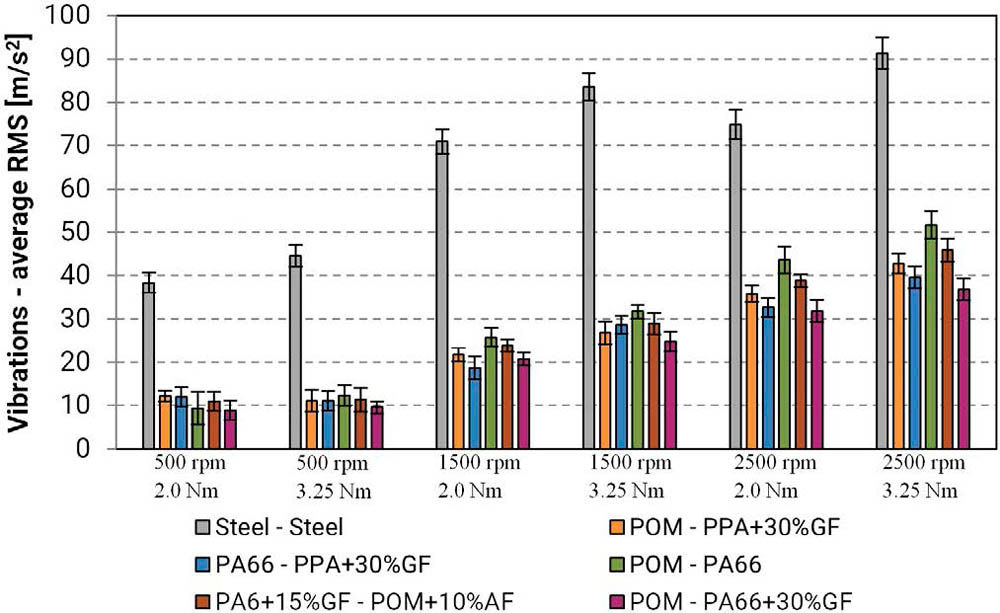
Figure 7—Vibrations, measured for the tested gear pairs. The temperature of plastic gears was controlled at 80°C in all tests (temperature measured on the teeth).
At this point, it must be stressed that the gear pairs were tested in an isolated acoustic chamber and only the noise generated by the gear pair was measured. In a real gearbox, most of the noise is usually generated by the housing, while the main cause for housing excitation is vibrations generated by the gears, which are transmitted to the housing through the bearings and shafts. In some cases, the RMS values of the vibrations for the steel gear pairs were more than compared to the plastic-plastic pairs;; hence, a much louder operation of gearboxes containing only steel gears can be expected.
All material combinations were tested at the same load, i.e., the same torque, rotational speed, and controlled gear temperature. However, the modal characteristics of the tested gear pairs are not the same since the materials exhibit different densities and stiffness. Hence, the gear’s eigenfrequencies are located at different positions in the frequency domain. That means the steel/steel gear pair has a different eigenfrequency than the plastic/plastic gear pairs. Also, the eigenfrequencies of plastic/plastic combinations (composed of different materials) can vary substantially.
If a structure is excited at the eigenfrequency or near it, the amplitude of the response rises significantly (in theory, it is an exponential rise). Therefore, one material pair can show higher vibrations at a certain rotational speed than the other and lower vibrations than the comparing material pair at a different rotational speed (excitation level). Such phenomena will also occur in a real application if the load is varying (which, many times, is the case).
Fast Fourier transforms (FFTs) of the measured vibration and sound pressure signals were generated to verify that the measured NVH resulted from gear meshing and not any other associated effects, e.g., motor noise, bearings or exterior noise. It was crucial that for all the analyzed signals, the most pronounced peak in the frequency domain corresponded to the gear meshing frequency, as shown in Figure 8. By that, it could be confirmed that the measured values were the resulting NVH of the meshing gear pair.
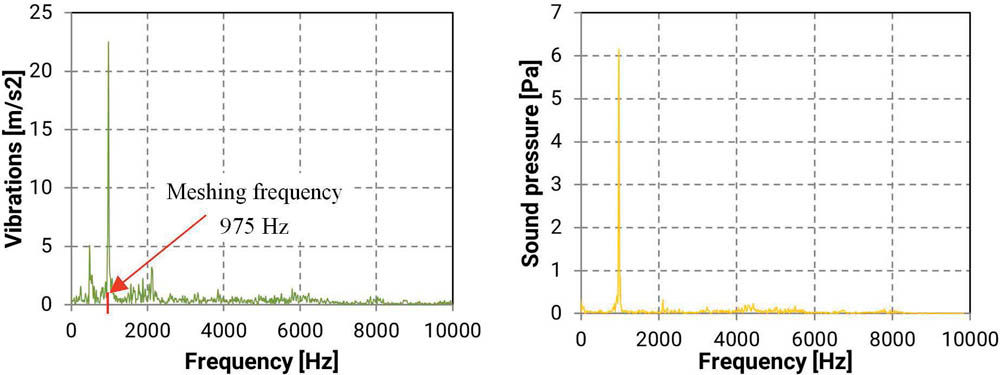
Figure 8—FFT of the measured vibrations and sound pressure signal. The rotational speed of the test was 1500 rpm.
Conclusions
The present results provide a quantitative comparison of the plastic gear’s NVH level against that of a steel gear pair of the same geometry, operating at the same conditions. While the noise levels measured for the steel gear pairs were 10 dB or higher than those of the tested plastic gear pairs, the main benefit can be seen in the much lower vibrations generated by the plastic gear pairs. Vibrations generated by a gear pair are the main noise generator in most practical applications. The differences between the different plastic combinations were not on the same level as when compared to steel gear pairs. However, a difference in NVH performance could nevertheless be observed. The best-performing material combination (especially in terms of vibrations) was the POM—PA66+30%GF, while the highest vibrations against the plastic gear pairs were measured for the POM—PA66 gear pairs. The meshing stiffness of the POM—PA66 gear pair was the lowest among the tested pairs. While this ensured good damping, it also resulted in the highest transmission error among the tested pairs, which is the main source of vibrations in gear pairs. Gear pairs consisting of one unreinforced and one reinforced gear exhibited a higher meshing stiffness and, consequently, a lower transmission error, resulting in lower vibrations generated by the gear pair.
Future Outlook
Several open topics on the plastic gears NVH still need to be addressed and systematically studied. The professional public accepts that the plastic gear NVH increases with the increasing wear of the gears. To the best of the author’s knowledge, there have not been any relevant studies published yet, where the wear’s effect on the NVH would be systematically studied and evaluated. A similar open topic is the effect of grease. It is generally accepted that by introducing grease to the gearbox, the noise and vibrations get reduced. However, having such an effect more systematically quantified would be valuable.
References
- D. Zorko, J. Duhovnik, J. Tavčar, “Tooth Bending Strength of Gears with a Progressive Curved Path of Contact,” J. Comput. Des. Eng., Vol. 8 (2021), pp. 1037–1058. https://doi.org/10.1093/jcde/qwab031
- R. Wu, P. Wei, Z. Lu, H. Liu, D. Zorko, H. Xie, “A Comparative Study of Fatigue Behavior Between S-Shaped and Involute POM Gears,” J. Comput. Des. Eng., Vol. 9 (2022), pp. 2483–2494. https://doi.org/10.1093/jcde/qwac121
- D. Zorko, J. Tavčar, M. Bizjak, R. Šturm, Z. Bergant, “High Cycle Fatigue Behaviour of Autoclave-Cured Woven Carbon Fibre-Reinforced Polymer Composite Gears,” Polym. Test., Vol. 102 (2021), 107339. https://doi.org/10.1016/j.polymertesting.2021.107339
- T.J. Hoskins, K.D. Dearn, S.N. Kukureka, D. Walton, “Acoustic Noise from Polymer Gears—A Tribological Investigation,” Mater. Des., Vol. 32 (2011), pp. 3509–3515. https://doi.org/10.1016/j.matdes.2011.02.041
- B. Trobentar, M. Hriberšek, S. Kulovec, S. Glodež, A. Belšak, “Noise Evaluation of S-Polymer Gears,” Polymers, Vol. 14 (2022), p. 438. https://doi.org/10.3390/polym14030438
- B. Polanec, S. Glodež, A. Belšak, “Noise Evaluation of Coated Polymer Gears,” Polymers, Vol. 15 (2023), p. 783. https://doi.org/10.3390/polym15030783
- Benjamin van Wissen, Leonid Pastukhov, Fumio Mitsuzuka, Kazuyuki Iwanaga, Adnan Hasanovic, “NVH Performance of Thermoplastic Gears; Modelling and Measuring,” Proc. Int. Conf. High Perform. Plast. Gears, Garching by Munich, 2023.
- Julien Cathelin, Plastic Gears: Investigation on Noise and NVH Behavior, in: Proc. Int. Conf. High Perform. Plast. Gears, Garching by Munich, 2023.
- ISO 1328-1:2013: Cylindrical gears—ISO system of flank tolerance classification—Part 1: Definitions and allowable values of deviations relevant to flanks of gear teeth, (2013).