“In today’s globally competitive market, gear manufacturers need a cost-effective, highly capable, yet versatile hobbing solution for fine-pitch gearing. The Helios Hera 90 fills this role like nothing else on that market,” said David Harroun, vice president of Helios Gear Products.
Construction features of the Hera 90 prove strong fundamentals of engineering and design. The machine uses direct-drive torque motors. A cast iron machine base provides optimum stability and dampening of cutting forces. The machine’s slant bed design uses gravity to efficiently remove chips during the cutting process. Automatic X-axis (radial hob head position) retract at power failure ensures the safety of tooling during electrical loss. Total machine enclosure includes world-standard safety equipment such as electro-mechanical interlock and front splashguard doors.
“Manufacturers have found the Helios Hera 90 CNC hobbing machine to be an extremely cost-effective, high-quality platform for 21st-century gear production,” said Harroun. Evolving the Hera 90’s range of options, Helios has also introduced the 90‑W configuration. This offers gear manufacturers an extended machine bed and axial travel, making the machine an ideal solution for long-shaft, small diameter workpieces. Manufacturers of powertrain shafts for small- to medium-vehicles will be interested in this machine, especially those workpieces with multiple, timed splines and/or gears.
The Hera 90-W is a solution for small-diameter, long-shaft parts with multiple gears and/or splines, especially when those features need to be timed (Courtesy of Helios Gear Products).
The Hera series has been in development for over 15 years, and it continues to address the demanding hobbing needs of North American manufacturers. With Helios' domestic support, the Hera 90‑W adds a valuable offering to the machine line by equipping manufacturers with a high-quality, low-cost, quick-delivery, domestically supported solution for long-shaft horizontal hobbing. The Helios Hera 90‑W is rated at 3 module (8.5 DP) for parts up to 90 mm (3.54 in) diameter. The 90‑W can be configured to optionally load parts up to 600 mm (23.62 in), 700 mm (27.56 in), or greater lengths.
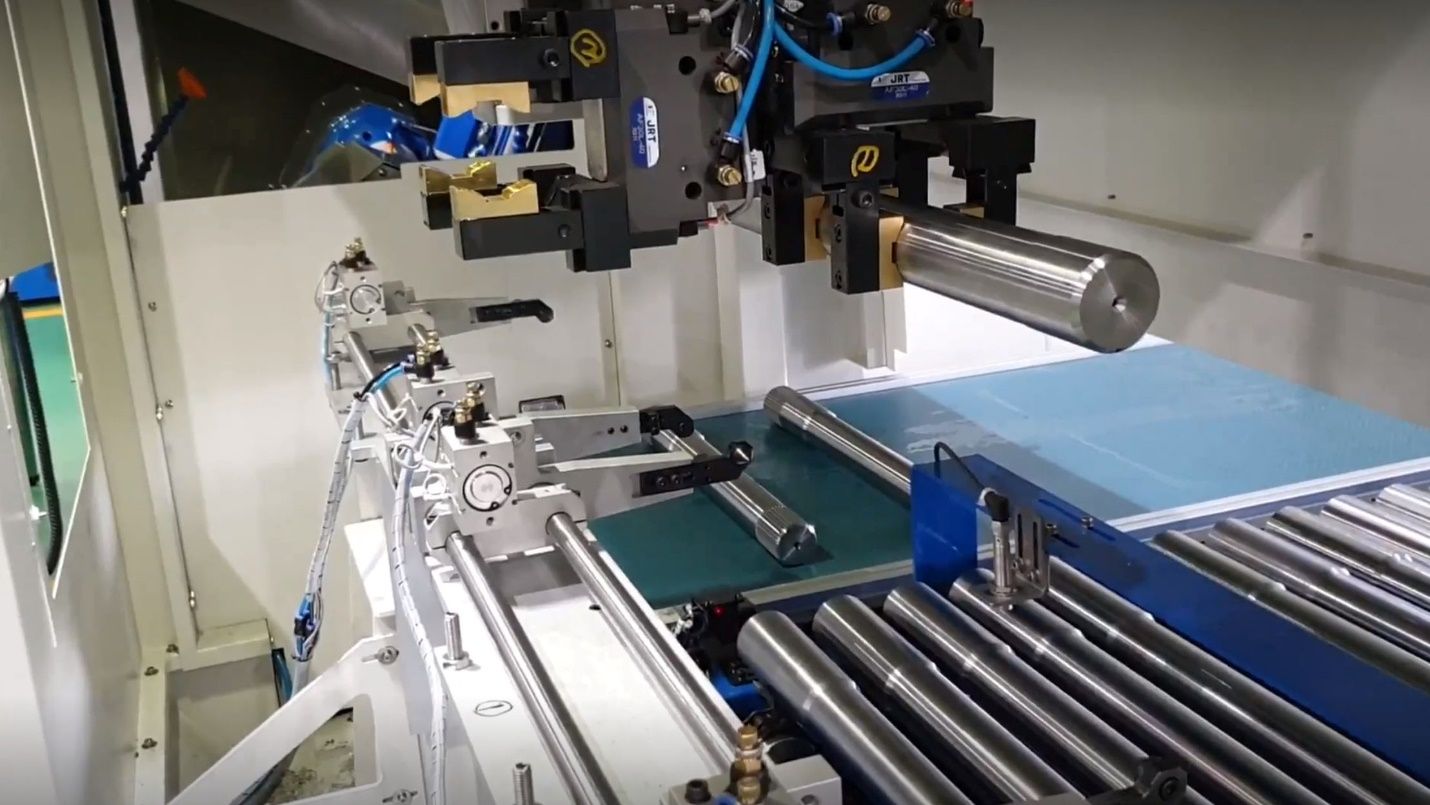
Furthermore, the machine’s axial travel (hobbing length) covers nearly the maximum loadable part length. This enables easy hobbing of long shaft parts with gears on opposite ends — especially when the gears must maintain a timed relationship. For shorter workpieces, the machine’s versatile tailstock design clamps workpieces as close as 200 mm (7.68 in) measured from the work spindle face. Standard features of the Helios Hera 90 are included with the 90‑W. “Gear manufacturers looking for a truly versatile, future-proof hobbing machine must consider the Helios Hera 90‑W,” said Gimpert.
Nidec Machine Tool Offers Variety of CNC-Controlled Hobbing Machines
Nidec Machine Tool Corporation recently launched the GE15HS and GE25HS models of hobbing machines. Emphasizing high speed, precision, and efficiency, the machines produce gears for electric and hybrid cars amid the global trend toward reducing the carbon footprint.
GE15HS (Courtesy of Nidec).
The GE15HS model is for gears with a maximum diameter of 150 mm, widely used in automobiles and motorcycles. The high-speed, high-torque direct-drive motor for the main cutting spindle provides a maximum spindle speed of 6,000 min—three times faster than previous models. The high-efficiency spindle holding the workpiece uses a special table that provides high rigidity and high-speed rotation to handle the necessary thrust load for high-efficiency machining. The GE15HS provides process efficiency, eliminating the finishing process of shaving before heat treatment, improving productivity, and reducing processing costs.
GE25HS (Courtesy of Nidec).
The GE25HS is for larger gears up to 250 mm in diameter, such as automobile differential gears. With its high-efficiency processing, this model utilizes a high-speed, high-power spindle eliminating the effects of temperatures variation during production. The high rigidity table has the backlash eliminator incorporated as standard equipment. In addition, the motor torque and maximum spindle rotation speed of the main spindle have been increased 1.5 times from previous models, providing a 42% reduction in processing time.
FOR FURTHER INFORMATION:
nidec.com/en/nidec-machinetool
affoltergroup.ch/en
heliosgearproducts.com