Recent Cutting Tools from Kennametal, Star SU, and Seco Offer Improved Tool Life and Precision
Reliable cutting tools are essential to production-process efficiency
Cutting tools are basic to gear manufacturing. Whether it's a hob, broach, shaper cutter, or skiving tool, the object of cutting tools remains the same: material removal that is fast, accurate, and cost-effective. The field tends to evolve gradually in the machines, materials, and coatings that make cutting tools even more useful. Reliable cutting tools are essential to production-process efficiency, and recent solutions from Kennametal, Star SU, and Seco offer improved tool life and precision.
Cut longer with Kennametal’s KCK20B and KCKP10 indexable milling grades
Kennametal has introduced the KCK20B and KCKP10 indexable milling grades for higher wear resistance and up to 30% longer tool life when machining cast iron and compacted graphite iron components. Both grades offer higher productivity and consistent, repeatable performance during roughing, semi-finishing, and finishing operations.
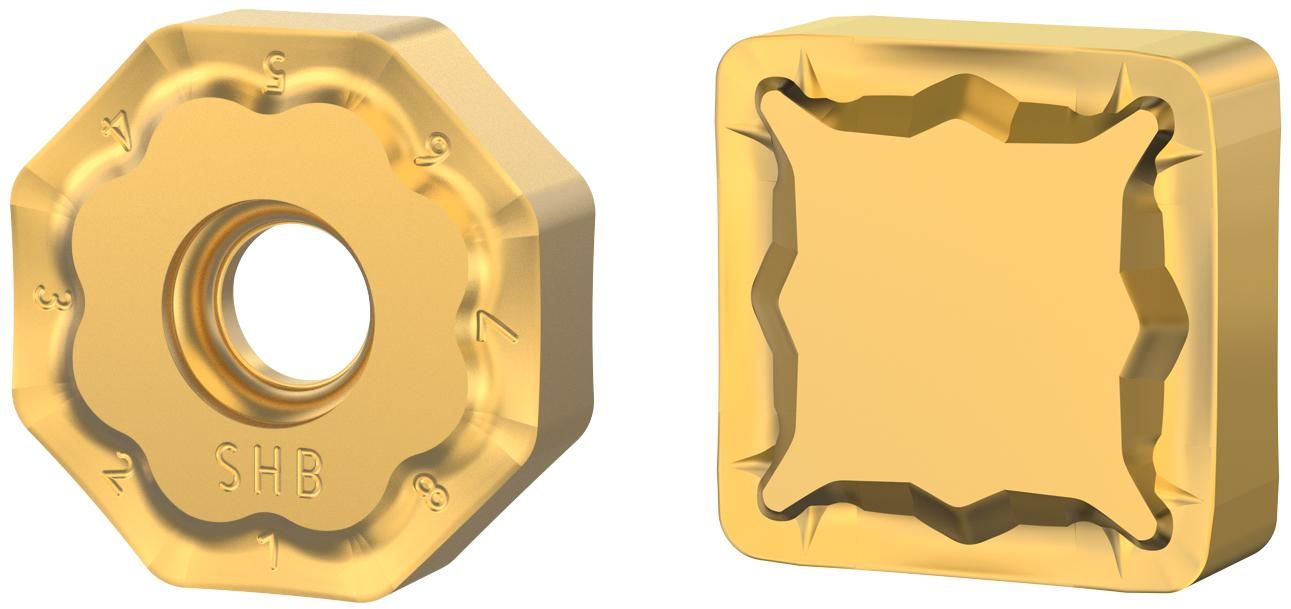
“The new grades feature High-Power Impulse Magnetron Sputtering (High-PIMS) technology that provides a smoother insert surface and optimal layer adhesion for less flank wear—one of the leading causes of insert failure,” says Gil Getz, Product Manager, Kennametal. He notes that the new coating technology also increases cutting edge strength. “The result is high-performance milling in a broad range of cast iron alloys, including grey cast iron, ductile cast iron, and compacted graphite cast iron.”
KCK20B and KCKP10 are suitable for wet or dry cuts. These include rotor hubs used in windmills, pump housings, steering knuckles and gear housings for heavy equipment, and automotive components like crankshafts and cylinder heads. While KCK20B delivers higher productivity in roughing and semi-finishing operations, KCKP10 is applicable for finishing operations, but also works exceptionally well when profiling and copy milling cast iron and steels up to 45HRC.
“For customers where high tooling cost and downtime associated with tool changes are especially important, KCK20B and KCKP10 grades promise to increase tool life tremendously,” says Getz. “And for those who wish to increase throughput, the new grades deliver there as well. Either way, it is a win-win for any shop machining cast iron.”
Achieving perfect concentricity with the Super Round Tool (SRT) Reamer
The Super Round Tool, or SRT, is a patented reamer designed by the Northern Tool division of Star Cutter Company to create the best quality reamed hole across a spectrum of applications. The SRT combines two tools into one—it offers multiple straight flutes for consistent location and multiple helical flutes that ensure roundness and finish. The SRT’s abilities include superior surface finish (Ra, Rz, and Rmax), near-perfect concentricity, roundness deviations of less than 2 µm, and lower cost per hole.
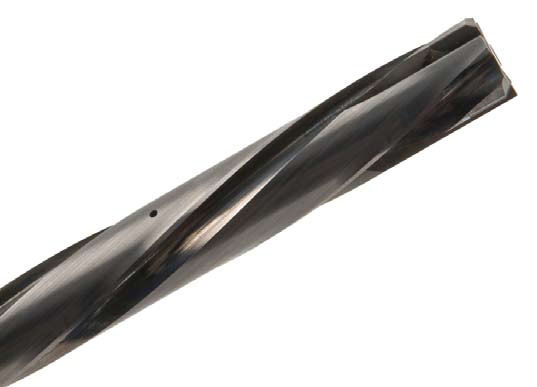