Custom-Fit Robot Solutions Ensure Fast Parts Flow in Production
EMAG develops integrated automation solutions
Production solutions with robotic automation are on the rise: With their help, a fast and low-manpower flow of parts can be established within a site—thus reducing unit production costs and increasing production reliability and quality. In this example, EMAG links pick-up machine technology with highly individual robot solutions designed within the requirements of the workpiece and the production process. What are the important details?
According to the “World Robotics 2022” report of the International Federation of Robotics (IFR), there are now around 3.5 million robots in use in industrial production worldwide. The USA is one of the three largest robot markets in the world. Current examples from EMAG show why this is so: The specialists combine their high-performance machines with completely different robot cells—and thus not only ensure highly efficient processes for loading and unloading the machines but also integrate additional stations for quality assurance, labeling, cleaning, and much more. What is the overarching objective at EMAG when robots are used? “The focus is always on the requirements of the workpiece and the associated production process,” explains Jochen Arnold, CEO EMAG L.L.C. “Decisive questions here are, for example, what batch sizes are to be produced in a given period of time and how autonomously the solution should operate. In any case, we are very flexible and adapt in many ways to the existing production environment or space conditions.”
With Conveyors, Palletizers, or Drawers
A look at the details shows just how different EMAG’s robotic solutions are: Parts can be fed, for example, using infeed and outfeed belts, palletizers, drawers, or bin picking. With the help of these systems, the robot “operates” itself when it picks up or finishes placing new components. Each solution has different strengths and basic conditions. For example, belt or hinge conveyors are an ideal option when the flow of parts needs to be smooth from an upstream production solution to the EMAG machine. The robot can then simply pick up the components from the belt and deposit them again later, with the belts arranged in different ways—depending on the space situation or the desired flow of parts. Pneumatic stoppers ensure that the components are separated. It is also possible to detect the workpiece alignment on the belt using a camera. A highly flexible alternative to this is the so-called “bin-picking systems” (“reach into the box”). Here, the workpieces are in a chaotic position, with the robot arm not only picking the components with the aid of a 3D sensor system but also correctly recognizing and aligning them and feeding them to the next processing step. The system can be used flexibly and configured for many applications.
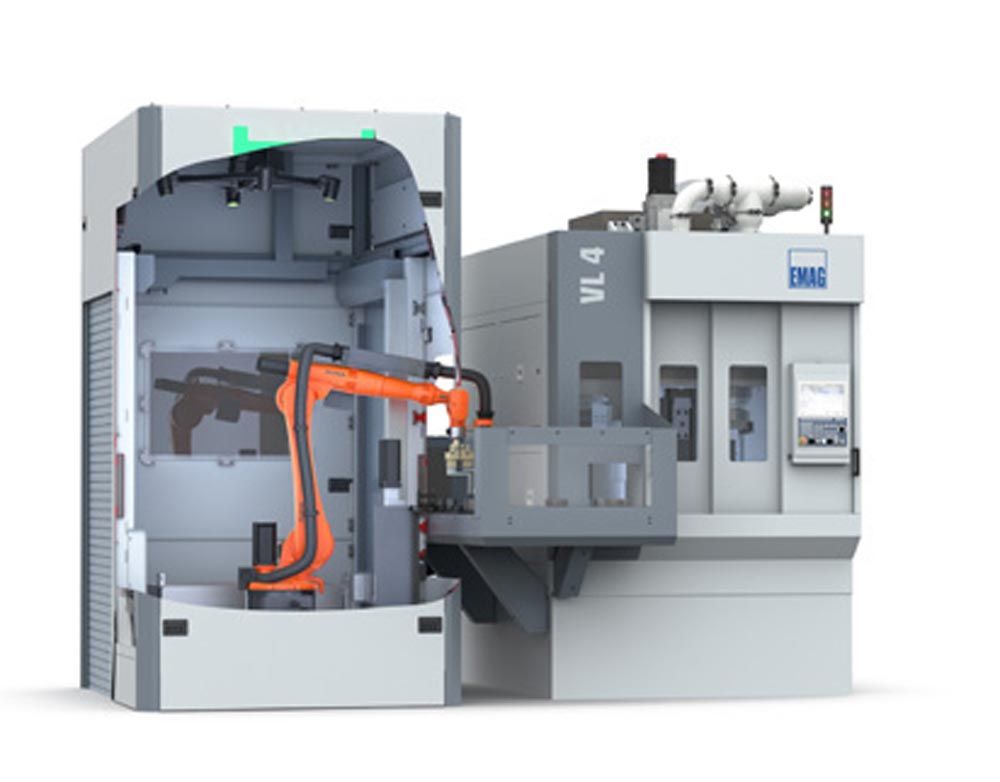
In contrast, the use of palletizers presupposes an “orderly” start. In this case, the system is loaded and unloaded via a blister cart, for example. It contains boxes stacked on top of each other with corresponding mold nests containing the components—i.e., a relatively large quantity per cart, which an operator simply pushes into a defined position from which the robot can access. The cart with finished parts is in a different position. “One of the things that matter in this kind of solution is that you relate the cycle time of the EMAG machine and the desired man-hours at the machine. So, if the machining cycle within the machine is only a few seconds and at the same time you are aiming for minimum operator effort at the machine, this solution may not be suitable because the carriages would then have to be replaced too frequently. But these are precisely the calculations that we carry out for every robot solution and advise the customer accordingly,” explains Arnold.
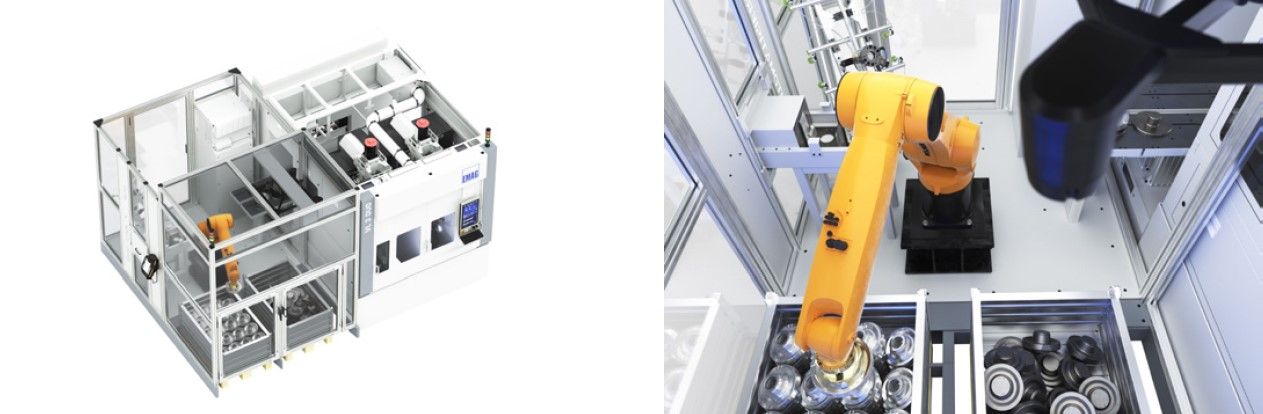
Figure 2—In bin picking systems (“reach into the box”), the workpieces are in a chaotic position. With the help of a 3D sensor system, the robot not only picks the components but also correctly recognizes and aligns them and feeds them to the next processing step.
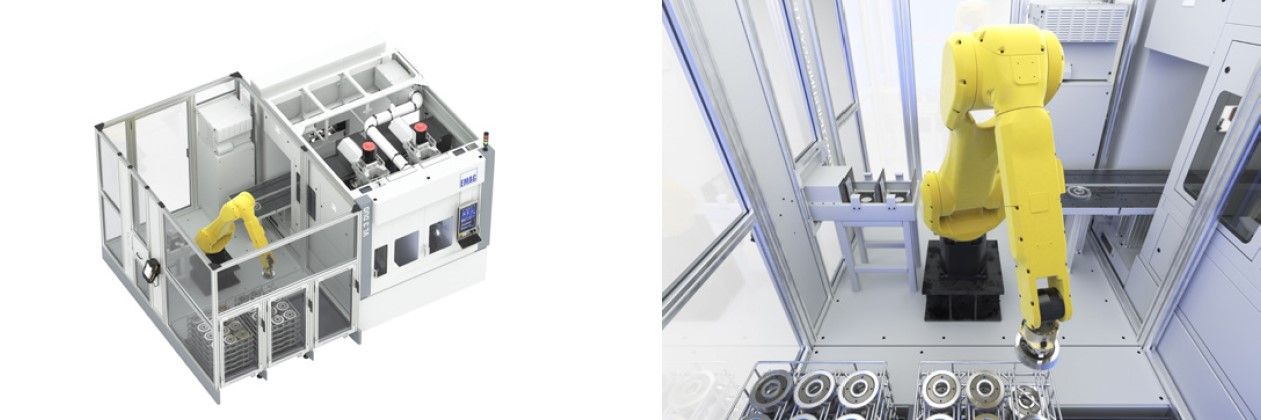