Determining Bull Gear Wear
Determining Bull Gear Wear
QUESTION
Expert Response Provided by Charles Schultz, PE:
We are currently experiencing wear on the bull gear on our
converter at the steel plant.
We want to be able to draw the original gear profile to compare
this with the worn tooth before we decide on the next steps.
I have attempted this, but there is a correction factor given and I
am unsure how to apply this. Could someone give advice on this?
Please find attached the PDF’s for the bull gear and the pinion gear.
They are old drawings! The wear is on the wheel.
Thanks for your very interesting question and the opportunity to revisit the beginning of my life in gears. As a freshman in high school drafting class, one of my assignments was drawing a spoked gear complete with the tooth flanks. Back in 1967, around the time your gear set was designed, this was an arduous task that certainly tested my skills with a compass and French curve set. Technology has improved since then; you have a number of methods available to you.
Method 1: tracing the existing tooth flank. You didn’t mention if both gear flanks were equally worn. In most cases they are not, so take advantage of symmetry and make a tracing of the leastworn flank, smooth out the profile with a thin flexible scale, and use it to check the depth of damage on the tooth flank. I have used this method in the field and think it will be sufficient for your purposes.
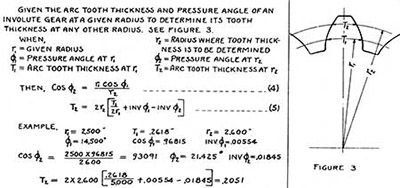
Calculation of gear radii based on tooth thickness, from Manual of Gear Design, by Eliot K.
Buckingham and Earle Buckingham.
- Click image to enlarge
Method 2: use a manual drafting method from the Internet. The biggest change in engineering since 1967 has been the development of the Internet. Now in a matter of seconds you can seek the advice of dozens of people on how to do almost anything. Some of the advice is about as good as I would have gotten from a high school classmate; at least one carefully demonstrated method I downloaded was so bad it wouldn’t have passed that 1967 test. Others are very program-specific and may work better.