Gear Manufacturing for E-Mobility Applications
esco Offers Flexible Power Skiving Software Solutions
The impending mobility revolution and the electric vehicles associated with it are currently the talk of the town. When it comes to their production, a number of changes are on the horizon, particularly with regard to gear manufacturing. The new recipe for success for flexible gear cutting is power skiving. This innovative machining method offers enormous potential for all those working in the field of gear manufacturing. However, to design and to deal with skiving processes require the support of true high-performance software - and this is where esco GmbH from Aachen comes into play.
The topic of electromobility is ever-present. It seems that not a day goes by without some automotive manufacturer informing the public about its future roadmap in this area. And the fleet strategy of virtually every manufacturer is clearly moving in the direction of electric vehicles. However, it is not only the technology, being hailed as the drive of the future, that will in all likelihood change the entire automotive industry. It is also the field of e-car production where alternative manufacturing processes could turn everything that has been done so far upside down – and power skiving can definitely be classified as a disruptive technology.
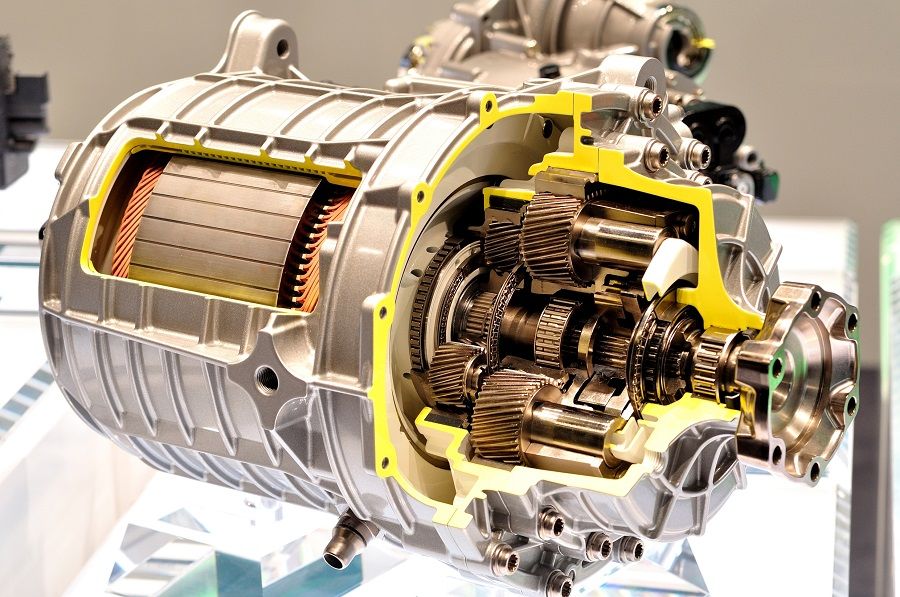
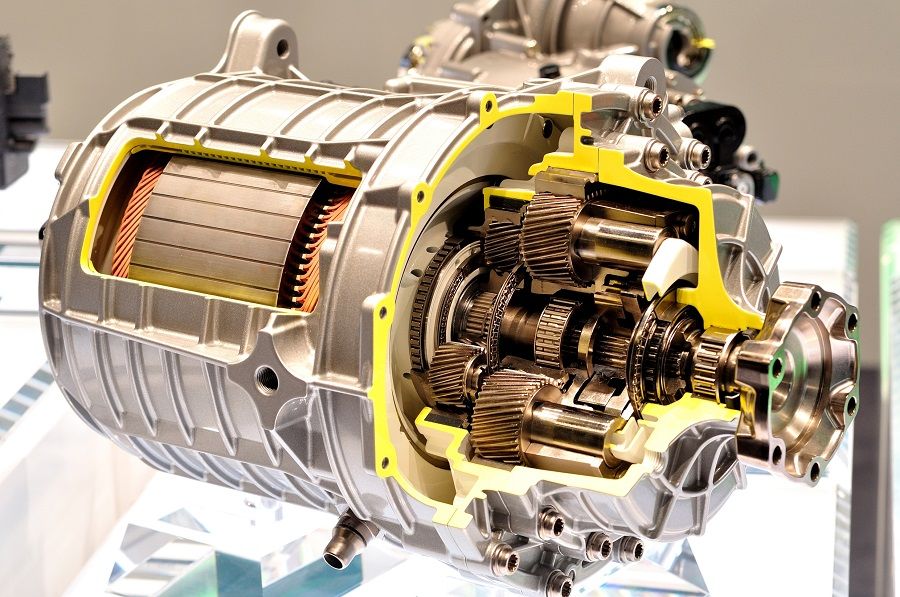
Latest Technology
The machining process, which is suitable for a wide range of components and component features, has the potential to significantly improve productivity, flexibility and cost in the series production of gear components. The special machining method is a continuous cutting process that is much faster than shaping and offers more flexible machining than broaching and gear hobbing. The focus of power skiving, an economical and flexible gear cutting process, is on internal gears and gears with process-limiting interference contours. The types of gearing can be diverse: starting with arbitrarily corrected involute running gears to splines through to toothed belt or sprocket profiles. An important factor here is the accuracy that can be achieved: Power skiving can produce gearing in a module range of approximately mn = 0.3 to mn= 8 mm in DIN quality 5.
The power skiving concept was first patented in 1910 by German engineer Wilhelm von Pittler. However, the fact that it took almost 100 years until the technology could be used efficiently on an industrial scale was mainly due to the considerable challenges of implementing the technology. This was anything but trivial, especially when it came to fully understanding the kinematics of the process and achieving perfect synchronization between the workpiece spindle and the tool spindle even at extremely high speeds. Ultimately, only high-resolution electric motor spindles and "fast" controls were able to lead to the breakthrough of power skiving. Furthermore, for the creation of optimum machining conditions, programming and application strategies for the production of high-precision gears had to be developed.
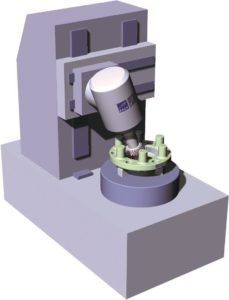
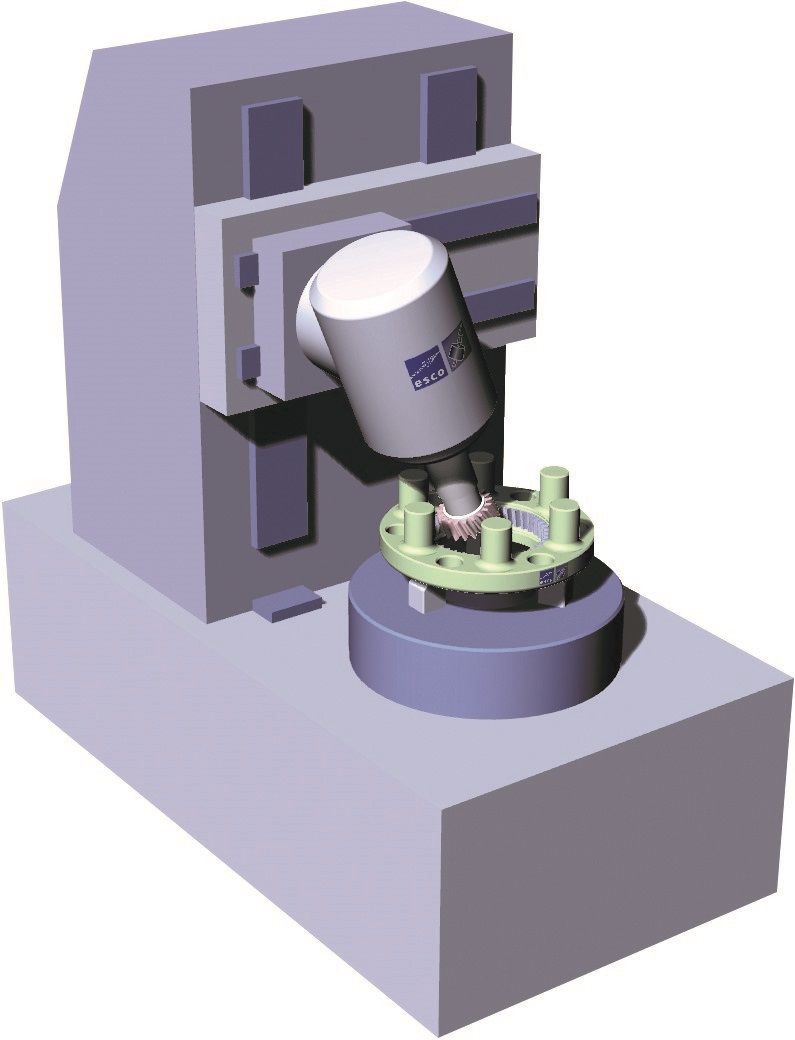
A Sought-After Alternative
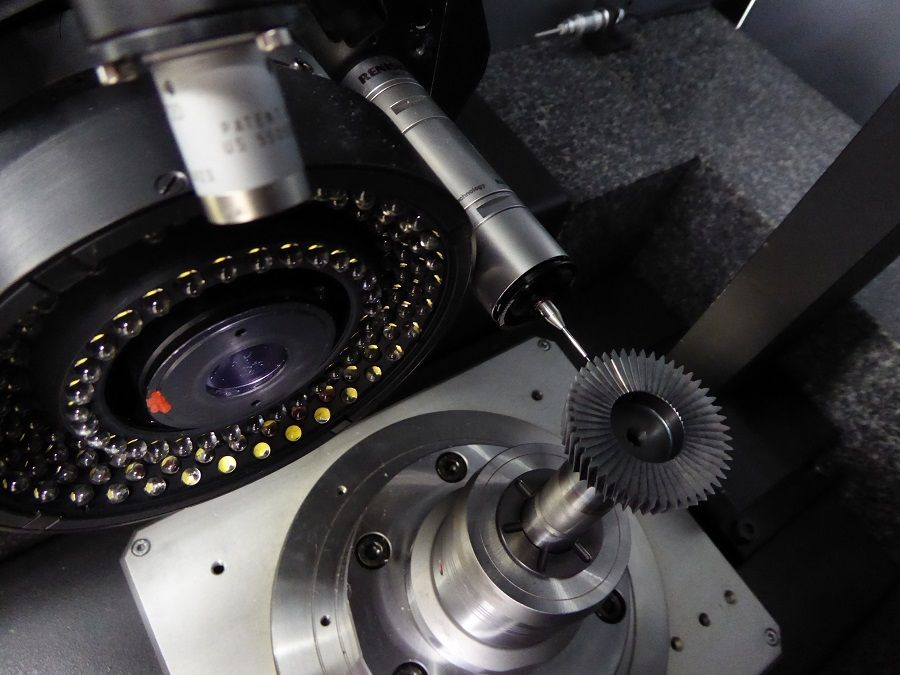