Delphi Corporation’s Rochester Operations, one of the company’s core automotive manufacturing facilities in the U.S., experienced significant improvements under Harris’ guidance. Annualized labor savings reached $2.7 million for the company while productivity improved by 190 percent, according to the HLS website. Harris says that HLS has helped about 50 companies and 180 plants worldwide.
Danaher and Toyota are the two most prominent “poster children” of lean manufacturing, according to Keller. Toyota is the most profitable automotive company in the world, and so far in 2008, the corporation has passed General Motors in first-quarter global sales, he says. Danaher Corporation began implementing lean in 1984 and “The initiative succeeded beyond anyone’s expectations,” the company’s website states. “Since this modest beginning, DBS (Danaher Business System) has evolved from a collection of manufacturing-improvement tools into a philosophy, set of values and series of management processes that collectively define who we are and how we do what we do.
“Fueled by Danaher’s core values, the DBS engine drives the company through a never-ending cycle of change and improvement,” the website states.
Some other “poster children” Keller refers to include Wiremold, which sold for 23 times its earnings before in-
come and tax (EBIT) value; this year, Ventanna Medical sold for 12 times what it was worth in sales and 68 times its income after only six years of implementing lean; and Actuant Corporation’s stock price grew by a factor of 5 between 2000 and 2004.
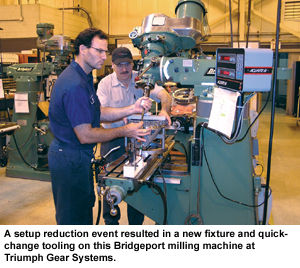
AME’s Rapid Continuous Improvement Workshop hosted by Hearth and Home Technologies included a tour of the plant. The event celebrated the company’s 1.5 million hours without a lost-time incident and on-time delivery of more than 98 percent in June 2007.
Lean Sins
There are various reasons why a manufacturing enterprise may not succeed in lean implementation, but none of the reasons relate to lean principles. Horror stories do exist, which paint a negative picture of it; however, there are common elements of failure that come up in analysis. Serious roadblocks can be averted simply by being aware of some frequent mistakes to watch out for.
One such horror story Keller knows of involved a company that abandoned its lean practices after only eight months. In this situation the command and control manager was left in charge of the implementation, and the manager knew nothing about the crucial people development factor, which Keller believes is the most important piece of implementing lean. All levels of employees must understand and be committed to lean in order to succeed, and it starts from the top down. The company suffered as a result of this failure in several ways, including the loss of some of its senior most knowledgeable workers, who left out of frustration. Keller stresses that lean principles cannot be doled out as one person’s job. Every single member of the organization must actively participate and be informed on lean methods. He says, “Most horror stories are related to trying to delegate the lean transformation.”
There is no one correct way to implement lean, and consultants disagree among each other as to which are the most important points, but they agree that if change does not come from the very top of the enterprise, without a strong leader driving the lean movement, actively engaged and participating with commitment, a lean production system is doomed. In Sonderman’s opinion, “Leadership is often the main reason why a company fails in its lean transformation.”
Lean is often employed as a “program of the month,” meaning that it is featured as a short-term goal or exercise for employees to practice. This strategy typically features lean methods for a short period without maintaining them. Since lean focuses on the idea of continuous improvement, this is an ineffective means of achieving that goal. A similar source of failure is based on the conception that the company will eventually meet its goal of being lean. This couldn’t be further from the truth. Lean is a never ending business system manufacturers must commit to. It is not just a toolbox; practitioners need to know when and how to use the tools of lean in different circumstances.
By nature, lean progress will eventually create idle capacity where employees become freed up due to improved production efficiency. This creates a hurdle along the path to lean. The natural reaction is that this is a good thing, and the company can afford to reduce its workforce in response and save more money. This is a major misconception that is likely to produce disastrous results. Lean principles are about the growth of an enterprise, not cost reduction. A main goal of lean is to reduce waste, but this is very different from reducing costs. Many companies believe laying off employees is appropriate once lean improvements take place, but Sonderman says that many consultants won’t even consider working with a company infected with the layoff virus. He says it “is a good way to kill lean. Stop it dead in its tracks.”
Downsizing the workforce in response to lean success is bad for employee morale as well. People see others being fired as a result of lean, and they are disillusioned and lose the commitment that is imperative for success. Reducing direct labor is a huge turn-off to the people implementing lean, but there are various ways to deal with extra employees effectively. One positive way to handle idle labor is to educate freed-up workers more about lean with continuous improvement programs. A kaizen workshop where teams can identify and practice significant improvements in process or create continuous flow cells is another way to occupy an idle workforce. They can help other employees expand their working knowledge of lean practices and discover how to apply them to gear manufacturing. Where continuous growth is the ultimate goal, new projects are bound to sprout up sooner than later.
The reward system is another factor that drives wrong behavior. Many companies, especially larger ones, institute programs where employees are rewarded for reaching goals or other achievements. People are often rewarded for performance by possibly receiving a promotion. The error in this thinking is that just because someone meets the right goals or executes their job well, does not mean that they have the necessary understanding of lean to practice it at a higher level. One possible result of this rationale is an employee being placed in a position of lean management without the proper know-how.
Success Factors
While there are common elements of failure in implementing lean manufacturing, there are also several critical factors to pinpoint success. The overall picture is far from gloomy, and the potential improvements far outweigh the challenges that exist. Leadership is at the top of everyone’s success factors list. It is imperative for the president and/or CEO to drive the lean movement and be visibly supportive. Keller believes that in order for employees to actively practice lean, they need to see the CEO embracing the new ideology and participating in shop floor training. There can be difficulties engaging mid-level managers, but with executive management truly leading the transition, other levels of participation should fall into place. Keller notes that the management pyramid is turned upside down in a lean production system, so management’s role is to ensure the proper training, material and machinery are available to the people that are creating value for customers. Mason has never seen a significant success story that wasn’t led directly from the top. He says, “One of the real upsides in the Boston Gear story has been the high level of management support and commitment, both at the local and corporate level.”
It is also important to work with an individual who has experience implementing lean practices. Lean specialists work extensively to bring hands-on techniques to the enterprise. An outside view with experience is instrumental to guiding continuous improvement, and many organizations are committed to providing lean guidance.
Policy deployment is another element for success. This involves analyzing the methods for improvement to determine whether they will produce the long-term goals for success. This is especially challenging for a large company because there are longer communication lines, and there are essentially many people pulling in different directions. It also involves having a clear conception of goals and objectives while aligning them with strategies and developing a specific blueprint for achieving them. Value-stream mapping is one popular tool where each stride in material and information flows is carefully charted from the point when a product is ordered to its delivery. Value-stream mapping also involves thinking at the system level with a broader view of production. Unfortunately this approach doesn’t come naturally to most humans. The overall culture of the work environment needs to change and reflect this more expansive outlook.
A dramatic change in the work culture is essential to the lean transformation. Individuals are essential, and they need to embrace the drastic culture change. It starts with hiring the most qualified and talented people; proper training is the next step. Larco says that at the lower level, employees must participate, and they will do so once they are convinced that the transformation is real. At the intermediate employee level, a fundamental transformation must take place to move from directing flow to coaching, training and truly enticing and involving people, he says. The people need to transform their thinking from an individualistic perspective to that of a team member. Larco says, “That transformation from I to we, where your personal ego is rewarded by saying we rather than I, that kind of reward is incredible, but it’s a dramatic transformation.”
Lean ideas seem to be spreading rapidly, although the level of effective implementation is arguable. Harris says he has started to see a push towards more interest in lean, but a problem remains in that companies still want too much too fast. He sees the same level of commitment to implementation that he did five years ago, although lean ideas have managed to grab more attention. Larco has witnessed lean practices worldwide, and he sees many people embracing lean in Europe, Asia and Latin America. The biggest challenge in store may be the time and effort required converting a business to lean—but the success is incredible.
More companies all over the world are reaping the huge benefits that lean has to offer, and lean manufacturing might seem to be merely a popular trend at the moment. But with all the buzz and improvements it has generated, lean is not likely to sink into the shadows any time soon. Resources are growing and models like TPS continue to improve. With the explosive benefits successful lean implementers are experiencing, lean manufacturing is thriving as an ideology and is being promoted extensively. With more than 15 years of lean practice under his belt, Larco views it as much more than a trend.
“I think this is an evolution of the industrialized world that is not going back.”
Get Your Gears on the Lean Bandwagon
Lean manufacturing is known by many names: lean production, lean enterprise, Just-in-Time manufacturing, continuous improvement and the Toyota Production System (TPS). In simple terms, lean refers to producing goods by removing waste and using flow, as opposed to the traditional batch and queue method. This is achieved by using various tools, but the tools alone won’t produce the desired results. Having started to revolutionize its production system as early as the post-World War II years, Toyota is the model most lean principles are based on. The company aimed to reduce inventory and produce goods upon customer orders, while in turn embarking on a voyage towards efficiency and quality. The biggest misconception that exists is that lean is a goal one can look towards achieving one day. Despite Toyota’s position as a prototype for lean manufacturing, over a half century later the company is the first to insist that they still have a long way to go. There is no say-all end-all point in a lean enterprise. “Lean is a journey, not a destination,” says Ralph Keller, president of the Association for Manufacturing Excellence (AME).
A plethora of lean manufacturing success stories exist, but some sources insist that lean principles are not well accepted. Jim Sonderman, a consultant and coach at the Lean Learning Center, believes lean is not poorly accepted; it is applied poorly. The Lean Learning Center in Novi, Michigan focuses on educational training and coaching through seminars and other services, including a five-day intensive course about the principles and rules of lean manufacturing. The attendees are polled about their experiences in lean. Sonderman says approximately 50-80 percent of the participants claim they are engaged in some lean practices. Out of this group, 75 percent say they have seen some degree of benefits; however, the numbers plummet from 75 percent to 2 percent with people who claim to have been “wildly successful.” Despite the low success rate, he says “It is very difficult to find companies that haven’t engaged in lean.”
Here’s a list of some resources to aid lean transformation that were mentioned in this article:
The Association for Manufacturing Excellence (AME)
3115 No. Wilke Rd., Suite G
Arlington Heights, IL 60004
Phone: (224) 232-5980
Fax: (224) 232-5981
www.ame.org
Harris Lean Systems
5072 Spanish Oaks Court
Murrells Inlet, SC 29576
Phone: (843) 651-0794
Fax: (843) 651-0852
www.harrisleansystems.com
J. L. Larco & Associates, Inc.
11 Alder Way
Bedford, MA 01730
Phone: (781) 275-3925
Fax: (781) 275-3959
Lean Enterprise Institute, Inc.
One Cambridge Center
Cambridge, MA 02142
Phone: (617) 871-2900
Fax: (617) 871-2999
www.lean.org
Lean Learning Center
40028 Grand River - Suite 300
Novi, Michigan 48375
Phone: (248) 478-1480
Fax: (248) 478-1589
www.leanlearningcenter.com