Load Capacity Evaluation of Production-Related Geometry Adjustments via STEP Import in BECAL
Using the Example of a Freeform Milled Bevel Gear
Bevel gears are widely used in various industrial applications, such as automotive, aerospace, and marine industries, due to their ability to transfer power between non-parallel shafts. The conventional manufacturing of bevel gears involves several time-consuming and costly processes, including gear blank preparation, gear cutting, and gear finishing. The increasing demands on gear components regarding increasing power density, reducing installation space, reducing weight, and increasing efficiency are also reflected in the design of gear components. The reduction of installation space and weight as well as the increase in power density often leads to an optimized wheel body design that interacts with the gearing in terms of load capacity and stiffness. This leads to an increase in the required geometric degrees of freedom (DOFs). Due to the resulting complex wheel body shapes and different production-related effects, production-related geometry adjustments may also be necessary. Tools for evaluating the gearing in combination with the wheel body shape and its influences nowadays form the basis for unlocking the holistic optimization potential of transmission components.
Based on these high requirements for the gearing, the model for calculating the load-bearing capacity must not fall short. With the help of the FVA program package BECAL, it is possible to carry out a tooth contact analysis based on the exact geometry with very high accuracy. Thus, in contrast to standardized, simplified calculation methods (Ref. 1), microgeometry is included in a load distribution calculation and local load capacity verification is possible.
In this article, we introduce the STEP import feature of BECAL and review the underlying theoretical approaches. In addition, fields of application are identified and finally illustrated with an explicit use case. The use case in this article is a freeform pre-milled large bevel gear on which production-related geometry adjustments have been applied. We will explore various approaches to manipulating the geometric DOFs and their impact on the final gear geometry. Also, the results of the underlying calculation without production-related geometry adjustments are compared with the results including the geometry adjustment. The BE- and FE-Method are used for calculation and the differences in the results are discussed. The results of this study provide valuable insights into the use of higher-order calculation methods and free-form milling for the bevel gear design and manufacturing process and contribute to the advancement of the manufacturing industry.
BECAL Methodology and Theory
The programme package BECAL (BEvel gear CALculation) has been developed for several decades at the Chair of Machine Elements on behalf of the FVA (Research Association for Drive Technology). Starting from a manufacturing simulation, it maps the complete tooth contact by means of a simulation of the same. By simulating the manufacturing process, the calculations are based on the exact geometry. The flank topography determined point by point is combined into a compensation surface, which is used for the load-free rolling simulation. The results of this simulation are the contact lines and the corresponding contact distances. These are used in the load distribution calculation. The necessary deflections are split into linear and non-linear influence numbers. The linear compliance is determined numerically with BEM or FEM, the non-linear contact stiffnesses are based on Hertzian theory. The load distribution calculated in this way is calculated locally for each flank point and forms the basis for the local load capacity verifications against pitting, micropitting, scuffing and tooth root fracture. This local calculation is based on a local usage of well-known and validated standards like ISO 10300 (Ref. 1) and FVA 411 (Ref. 11). Figure 1 shows the basic calculation procedure of BECAL.
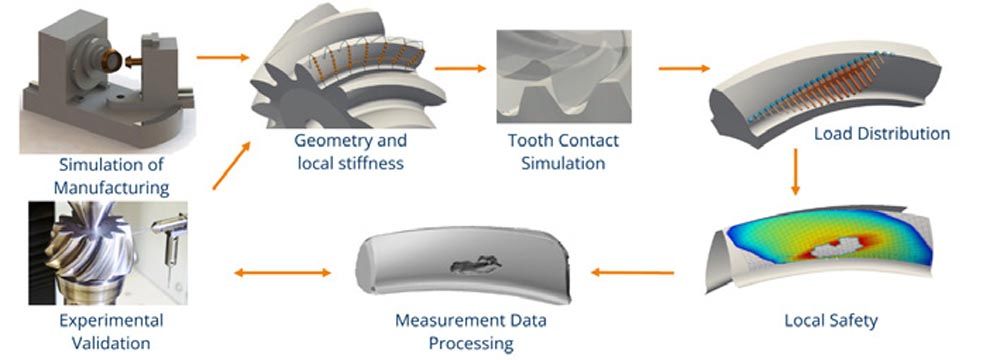