Haas has been working on improvements to automatic machine tool tending applications. Combining CNC machines with automatic part handling, according to Tandrow, can become complex due to the variation in handling needs and the variety of machine designs.
“Machine tool tending has been made simpler with the introduction of the Robot Ready interface, a standardized interconnect between the CNC machine tool and tending robots using network style communications,” Tandrow says. “Each installation need not be a unique science experiment; rather, the integrator’s package can be replicated and software can be reused as the use of material tending increases.”
Kapp Technologies is working on many enhancements to shorten machine setup times via software features. R&D is concentrated on reduced machine setups, reduced non-grinding times (such as loading) and achieving high utilization of the equipment as well as fundamental advancements in grinding technology.
“Periodic visits by our application engineering specialists enable us to optimize machine performance and productivity as well as improve proficiency,” Miller says.
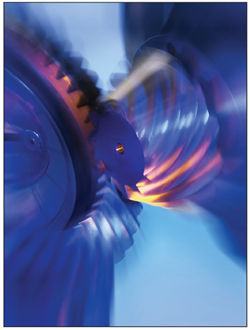
The Gleason 360AT will be used for the MTConnect demonstration at IMTS in Chicago.
Kapp’s KX500 FLEX Gear Center was created to extend the range, speed and flexibility for gear grinding. It now offers profile and generating grinding and integrated tooth quality measurement, and is prepared for the integration of an automatic loading system.
“Value for the long run is what matters, regardless of the economic headlines,” Miller says. “By manu-facturing machines we know will be in operation in 10 to 20 years and by offering our complete process package, which dictates that we will serve the customer for the life of their Kapp or Niles machine, we are ensuring the customer is getting the very best cost-savings possible.”
Higher feeds and speeds, elimination of “dead time” in the cycle and faster acceleration and deceleration rates of machine axes are just a few of the things Gleason strives for in regards to machine tool productivity. The company is developing and patenting software innovations such as adaptive feed rates and automatic workpiece centering on large cylindrical gear profile grinders that save customers time and money.
On the tooling side, Gleason continues to offer cutting tool designs, materials and coatings such as their Opti-Cut line, used in the production of large cylindrical gears, that all take advantage of machine innovations.
“Customers want value, which for them is part quality, productivity, flexibility, tool life, cost per piece, reliability, machine uptime and more,” Finegan says. “Opti-Cut is an innovation in and of itself that brings the cutting tool on par with the advanced capabilities of our gear hobbers and shapers.”
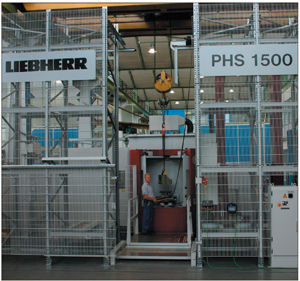
The Liebherr PHS 1500 pallet handling system for machining centers will be at IMTS.
Currently, Gleason is making record levels of investments in R&D for bevel gear, cylindrical gear and gear metrology products and processes, Finegan says.
Focus on functions. Liebherr Gear Technology, Inc. has spent the last year upgrading its machine tools with functions that better serve its customers. Innovations on its LCS 150 machine include the universal application of either CBN or corundum grinding tools. Another advantage is the use of tools in optimal combination so that the benefits of generating grinding and profile grinding can be used individually as well as together.
“The main focus of this machine has been to increase productivity by reducing idle times of loading and meshing, which are now 50 percent lower than previous machines,” says Scott Yoder, regional sales manager at Liebherr. “The machine bed of the LCS 150 was specifically designed for grinding, with a reduction of floor space by approximately 35 percent.”
Floor space reduction, in fact, is a frequent customer request, one that Liebherr has addressed on many of its new machine tool designs.
In addition to the LCS 150, Liebherr has created the high-speed LC130 hobbing machine that features a fully-enclosed work area, an optimized chip-flow for dry cutting and a rigid deburring system. The rotational speed of the tool—up to 7,000 rpm—allows cutting speeds of 1,700 m/min maximum. Loading times have been reduced so that chip-to-chip time is only 4.4 seconds.
“Practical experience with our current machine generation has significantly influenced the development of these machines,” Yoder says.
With experience in automation and material-flow, Liebherr has also created the PHS 1500, a pallet-handling system for machining centers that can be loaded in either a manual or fully automatic mode. This combination allows flexibility in production which has been unavailable until now, according to Yoder.
“In consideration for the various requirements for the storage places, the system can be adapted to a variety of applications and manufacturing situations. A modular design allows these units to be combined as the requirements increase,” Yoder says. “Liebherr chose to partner with Soflex (a software supplier), which ensures a user-friendly system with excellent functionality for the entire cell.”
The PHS 1500 as well as the LCS 150 will make the trip to IMTS in Chicago this September.
The technology show of shows. When IMTS opens its doors, it will cater to 91,000 buyers from 119 countries. Exhibitors will have an opportunity to show off their latest tricks while keeping a close eye on the competition.
“Major shows like IMTS are an excellent way to showcase our newest products and technologies,” Finegan says. “Shows like this are only one of a variety of promotional tools. It’s highly dependent upon the specific region and culture as well as the product or service being promoted.”
Miller cites shows like IMTS and EMO Hannover as beneficial in terms of the new opportunities available when Kapp participates.
“We’ve had a good experience searching for applications beyond parallel gears. IMTS generates many opportunities outside the traditional gear market. This has led directly to business in appliances, actuators, steering, non-gear aerospace and energy. The customer is the true innovator in these cases.” Miller says.
Although the company keeps in contact with customers via a newsletter or by mailings, Miller says IMTS remains a unique venue.
“IMTS invigorates our business and leads to innovation. We always meet people who are searching enthusiastically for manufacturing methods for their new products. This drives us to find unique solutions and develop specialty products.”
Haas Automation will be demonstrating improvements in the use and ownership of CNC machine tools in addition to new mill and lathe product offerings. Tanderow says the new Haas CNC control pendant has the USB interface and option controls located directly on the pendant as well as increased user storage compartments on many models.
IMTS 2008 will address machine tool innovations at the Emerging Technology Center with the first public demonstration of MTConnect, an open communications standard for manufacturing equipment inter-operability.
It is being developed by a partner-ship between the AMT and several manufacturing technology companies. The University of California, Berkeley and Georgia Tech University are also directly involved in the project.
“We believe that once manufacturers take a look at the open standard and turn their engineers loose to develop products using the standard, we’ll see productivity gains similar to those achieved with CNC in the 1970s,” says John B. Byrd III, president of the AMT.
For 2008, the IMTS has rededicated itself to technology as its core purpose. The theme of the 2008 show is “Connecting Global Technology.”
“We are producing six theme days at the IMTS Innovation Center, each with a specific industry partner that will provide opportunities to showcase new advancements and technologies as they apply to each of those industries,” Byrd says. “IMTS is also returning to its roots as a science fair—we’re producing the first Manufacturing Business and Technology Forum, which is a series of educational opportunities that cross the spectrum of new and developing technology, as well as manufacturing and management techniques.
“All of these events and new machine tool advancements can be previewed—and will be archived afterwards—at www.imts.com,” Byrd says.
The wait and see approach. The list of customer demands can be daunting. They want value, reliability, quality and high-operating capacity. They want machine tools that cost less, produce more and can keep up with the day-to-day demands on the shop floor. In short, they want an investment they can rely on for many years to come.
“Developing products and tech-nologies with the hope of opening opportunities is probably not a high-percentage play. I think the process works the other way around in our industry,” Finegan says.
Gleason sees the range of applications for gearing expand as it makes machine tools more affordable to its customers. Finegan notes that the end markets Gleason serves today are more diverse than at any time in the history of the company.
“Understanding customers and markets through VOC activities, and using that information to guide technology and product development virtually insures that we can capitalize on opportunities as they are presented to us,” Finegan says. “Like all investments, development activities must be actively managed and are subject to the same lean concepts and principles that drive our manufacturing.
“It’s an investment in future business.”