Hardness and Wear Resistance: DLC coatings boast extraordinary hardness, rivaling that of natural diamond, with values typically exceeding 20 GPa (~ 2000 HV). This exceptional hardness renders DLC-coated surfaces highly resistant to abrasive wear, adhesive wear, and surface deformation, ensuring prolonged service life and reliability in high-stress environments.
Tribological Performance: The low friction coefficient of DLC coatings, coupled with their smooth surface finish, mitigates frictional losses and wear in mechanical systems, thereby enhancing operational efficiency and reducing energy consumption. The tribological behavior of DLC coatings can be further optimized through the incorporation of dopants, such as hydrogen or silicon, to modulate surface chemistry and lubricant interaction.
Chemical Inertness: DLC coatings exhibit inherent chemical inertness, rendering them impervious to corrosive agents, oxidizing environments, and aggressive chemicals. This chemical stability preserves the integrity of coated surfaces and prevents contamination and degradation of adjacent components, making DLC coatings indispensable in harsh operating conditions.
Adhesion and Coating Integrity: The adhesion strength of DLC coatings to substrate materials is critical for ensuring long-term performance and durability. Advanced surface pretreatment techniques, such as ion bombardment or plasma cleaning, promote interfacial bonding and adhesion between the DLC coating and substrate, thereby minimizing the risk of delamination or spalling under mechanical loading.
Biocompatibility and Biofunctionality: DLC coatings exhibit biocompatible properties in biomedical applications, facilitating integration with biological tissues and implants. The bioinert nature of DLC coatings mitigates inflammatory responses and tissue rejection, while surface modifications, such as surface functionalization or bioactive coatings, impart biofunctionality for tailored biomedical applications.
Optimizing Gear Performance: Diamond-Like Carbon Coatingsin Action
Now that we’ve elucidated the remarkable properties of DLC coatings, let’s explore their transformative impact on gear applications, with a focus on electric vehicle transmissions and industrial gearbox systems.
Electric Vehicle Transmissions: Efficiency, Reliability, and Sustainability
Electric vehicles (EVs) represent the vanguard of automotive innovation, propelled by electric propulsion systems that demand lightweight, compact, and efficient transmission solutions. DLC coatings emerge as a strategic enabler for enhancing the performance and sustainability of EV transmissions:
Enhanced Efficiency and Range: The integration of DLC-coated gear components within EV transmissions yields substantial improvements in energy efficiency and range. By reducing frictional losses and wear, DLC coatings optimize power transmission, minimize energy dissipation, and extend the operational lifespan of critical drivetrain components.
Thermal Management and Durability: Lower friction results in lower thermal load leading to better thermal management within EV transmissions, thereby mitigating the risk of overheating and thermal degradation. Additionally, DLC coatings enhance the thermal stability and wear resistance of gear surfaces, ensuring robust performance under dynamic operating conditions.
Noise Reduction and Vibration Damping: DLC-coated gear systems exhibit reduced noise emissions and vibration levels compared to traditional metal-on-metal configurations. The inherent damping properties of DLC coatings attenuate mechanical vibrations, harmonics, and resonance, thereby enhancing passenger comfort and drivetrain refinement in EVs.
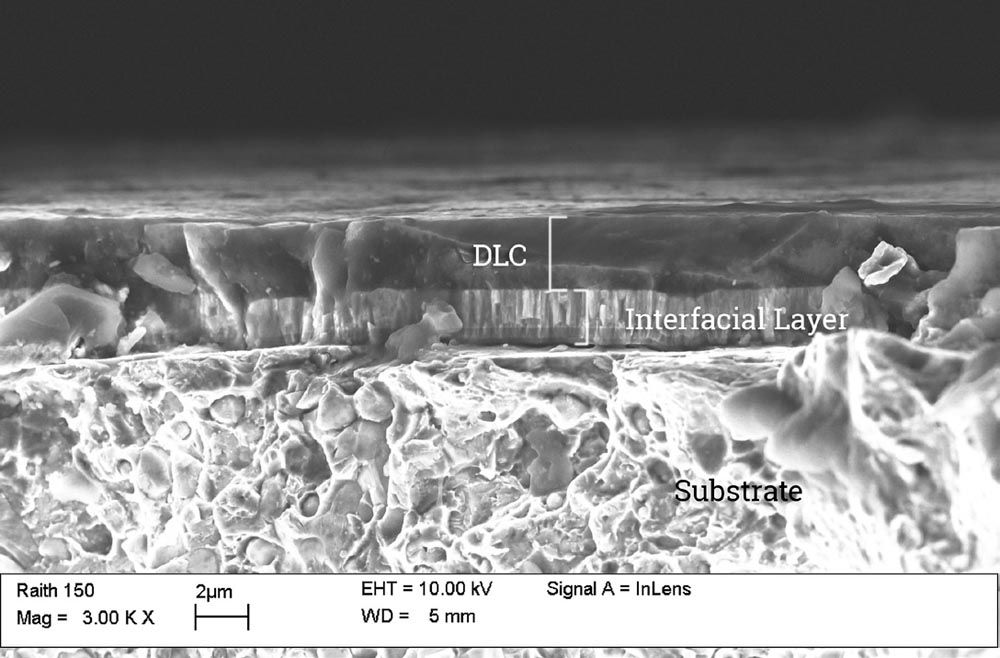
Figure 3: SEM micrograph of Nanocomposite coating.
Industrial Gearbox Systems: Productivity, Reliability, and Maintenance Optimization
In industrial settings, gearbox systems serve as the mechanical backbone of machinery and equipment, facilitating power transmission, speed reduction, and torque amplification across diverse applications. DLC coatings emerge as a strategic asset for optimizing the performance, reliability, and maintenance requirements of industrial gearbox systems:
Enhanced Load-Bearing Capacity: DLC-coated gears exhibit superior load-bearing capacity and fatigue resistance, enabling them to withstand the rigors of heavy-duty industrial applications. The exceptional hardness and wear resistance of DLC coatings mitigates surface damage, pitting, and micro-fractures, thereby prolonging the service life of gearbox components.
Efficiency Optimization and Energy Savings: Industrial gearbox systems often operate at high torque levels and rotational speeds, necessitating efficient power transmission and minimal energy losses. DLC coatings reduce frictional losses, improve gear meshing efficiency, and optimize lubricant retention, resulting in energy savings, reduced operating temperatures, and enhanced gearbox efficiency.
Maintenance Interval Extension: DLC coatings mitigate the need for frequent maintenance interventions and lubricant replenishment in industrial gearbox systems. The self-lubricating properties of DLC-coated surfaces, combined with their resistance to abrasive wear and surface oxidation, contribute to extended maintenance intervals, reduced downtime, and enhanced equipment availability.
Advanced Applications and Emerging Trends in DLC Coatings
Beyond conventional gear applications, DLC coatings are finding novel applications and driving innovation across diverse industries:
Aerospace and Defense: DLC coatings enhance the performance and durability of aircraft components, such as gears, bearings, and actuators, in demanding aerospace environments characterized by high speeds, loads, and temperatures.
Renewable Energy: DLC coatings optimize the efficiency and reliability of wind turbine gearboxes, hydroelectric turbines, and solar tracking systems, thereby contributing to the expansion of renewable energy sources and sustainable power generation.
Medical Devices and Implants: DLC coatings exhibit biocompatible properties and wear resistance, making them ideal for orthopedic implants, surgical instruments, and medical devices requiring prolonged contact with biological tissues.
Microelectromechanical Systems (MEMS): DLC coatings provide lubrication and wear protection for MEMS devices, such as accelerometers, gyroscopes, and microvalves, enabling miniaturization and improved performance in microscale applications.
Challenges and Future Directions in DLC Coating Technology
Despite the myriad benefits offered by DLC coatings, several challenges and opportunities exist on the horizon:
Optimization of Deposition Processes: Enhancing the deposition efficiency, uniformity, and scalability of DLC coatings through advanced deposition techniques, such as plasma immersion ion implantation (PIII) and hybrid deposition methods, to meet the demands of mass production and high-throughput applications.
Tailoring Surface Properties: Engineering DLC coatings with tailored surface properties, such as tunable friction, wear, and adhesion. This is accomplished through the incorporation of dopants, nanocomposite additives, or surface functionalization techniques, to address specific application requirements and performance objectives.
Multifunctional Coating Systems: Developing multifunctional coating systems by integrating DLC coatings with complementary materials, such as diamond nanoparticles, metal oxides, or polymers, to synergistically enhance mechanical, thermal, and electrical properties for multifaceted applications.
Sustainability and Environmental Impact: Exploring sustainable sources of precursor materials and renewable energy sources for DLC coating deposition processes and advancing recycling and reclamation technologies for reclaiming and reusing DLC-coated components to minimize environmental footprint.
Conclusion: Harnessing the Power of Diamond-Like Carbon Coatings
In conclusion, diamond-like carbon coatings epitomize the convergence of cutting-edge material science, nanotechnology, and engineering innovation. Their exceptional hardness, tribological performance, chemical inertness, and biocompatibility render them indispensable in various industrial applications, particularly in gear systems where durability, efficiency, and reliability are paramount.
Embracing the transformative potential of DLC coatings unlocks new frontiers in performance optimization, sustainability, and technological advancement. By integrating DLC-coated components into gear assemblies, you not only elevate the operational efficiency and longevity of machinery but also contribute to the broader objectives of energy conservation, emissions reduction, and sustainable development.
In the ever-evolving landscape of materials engineering and surface technology, diamond-like carbon coatings stand as a beacon of progress and possibility, empowering industries to surmount challenges, transcend limitations, and redefine the boundaries of what’s achievable. These goals drive the continuous innovation here at United Protective Technologies (UPT). For more than two decades UPT has researched, developed, and applied advanced surface solutions for demanding applications. Our nanocomposite coating innovations are used to enable advancements in industries from aerospace to automotive, medical to metalworking, weapons systems to oil and gas.
upt-usa.com

References