Precision and Innovation in Gear Cutting
Advanced cutting tools to meet changing market demands
Gear cutting has witnessed remarkable advancements over the years, with modern technologies transforming traditional methods into streamlined, highly efficient processes. NIDEC’s tools and methodologies increase productivity and quality in manufacturing. This article delves into the technological innovations, market relevance, and advantages of their gear-cutting solutions.

Precision and Innovation in Gear Cutting
NIDEC has developed a wide range of cutting tools designed for precise gear manufacturing, including hobs, skiving tools, shaper cutters, shaving cutters, round broaches, keyway broaches, rotary cutters, chamfering tools, and fir tree broaches. These tools are utilized globally in gear production processes, particularly in sectors like automotive, aerospace, and robotics. NIDEC’s emphasis is on advanced materials, coatings, and design to improve the performance and lifespan of cutting tools in gear manufacturing.
Cutting Tools Materials and Coatings for Gear Manufacturing
The performance of cutting tools in gear production heavily depends on the materials and coatings used. NIDEC has developed specialized materials and coatings to improve cutting efficiency, enhance durability, and reduce friction. For example, coatings like the Super Dry Coating are designed to improve the thermal resistance of tools used in high-speed cutting operations. These coatings prevent excessive wear by maintaining the tool’s sharpness at elevated temperatures, extending tool life and enhancing productivity.
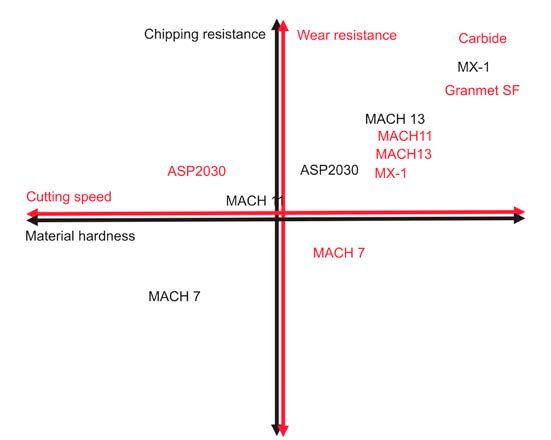
In addition, NIDEC has created coatings specifically for dry cutting, where no coolant is used. Tools with Super Dry coatings can operate effectively at cutting speeds up to 250 m/min, which contributes to reduced cycle times and lower operational costs. This technology is particularly useful in applications where traditional coolants would be difficult or undesirable to use, and it also supports environmental sustainability in manufacturing.
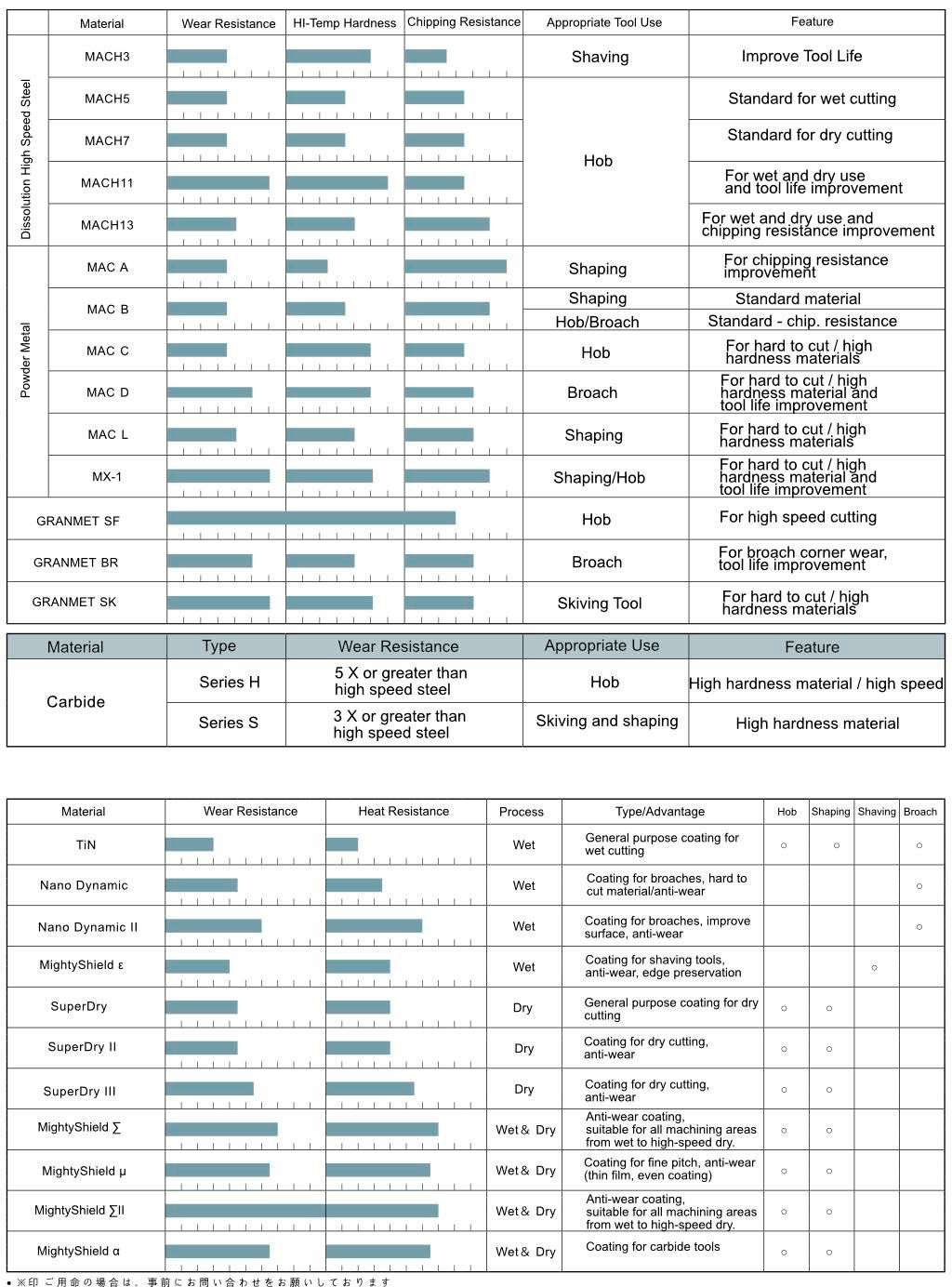
NIDEC’s tools are also designed to be versatile, allowing them to be tailored to specific gear manufacturing requirements. The ability to customize these tools based on factors like the hardness of the material being processed and the type of gear being produced makes NIDEC’s offerings highly adaptable to different production environments.
Applications of Advanced Cutting Tools in Gear Production
Gear production involves a variety of processes, each with its own set of challenges. Hobbing, for instance, is commonly used for generating gear teeth, but it leaves behind tool marks that can affect the gear’s performance. To address this, gear shaving is employed to refine the tooth profile, improving both precision and surface finish. The use of advanced materials in shaving cutters enhances their surface hardness, leading to longer tool life and more efficient operation.