The Evolution of QuesTek's Ferrium C64 for Additive Manufacturing
The unique processing conditions of 3D-printed metal gears have come a long way
Additive manufacturing (AM) of metal gears is in its nascency, but Integrated Computational Materials Engineering (ICME) technologies have served an integral role in understanding, evaluating and designing material microstructures and heat treatments specifically tailored for the unique processing conditions of 3D-printed gears. Applying their Materials by Design methodologies, QuesTek Innovations has expanded their ICME framework under US Army Small Business Innovation Research (SBIR) funding to adapt their high-performance Ferrium C64 gear steel to AM processes to demonstrate printability across multiple systems, achieve AMS minimum tensile properties, and observe a positive response to heat treatment.
As a wrought and forged product, Ferrium C64 steel exhibits a unique combination of high strength, high toughness, high hardness, high fatigue life, and high-temperature resistance, and it has been aerospace-qualified and adopted as a proven material for demanding gear and transmission components. This alloy is beginning to replace common gear steels such as 9310 and Alloy 53, allowing for lightweighting, increased power density and improved thermal stability.
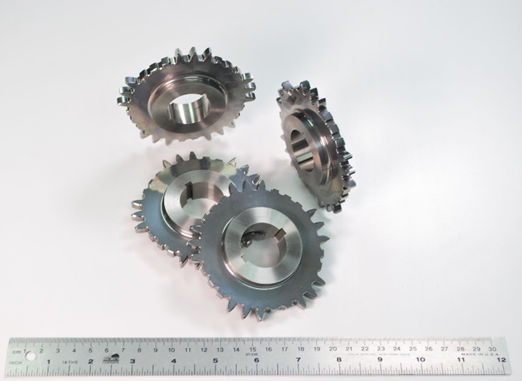
Starting in 2016, QuesTek began to evaluate and demonstrate Ferrium C64 in AM processing. It has been successfully demonstrated in laser powder bed fusion additive manufacturing equipment, and printed components have exhibited improved performance over AM forms of 17-4PH, maraging, and tool steels. It has been atomized several times in >500 lb batches, and test pieces have been repeatedly printed on EOS machines for mechanical testing and microstructural evaluation.
The strength and elongation have been found to be nearly the same as C64 forged bar, and while there is a slight debit in fracture toughness, initial axial (ASTM E466) and single-tooth bending fatigue test results are comparable to the forged stock, making atomized Ferrium C64 steel one of the most advanced alloys in AM for gears.
QuesTek is evaluating and demonstrating AM Ferrium C64 for aerospace gears and fatigue-driven applications as well as racing transmission gears, gears with integral bearing races, and other power transmission components where durability, compactness, lightweighting, high-temperature resistance and/or high surface fatigue resistance are the top priorities.
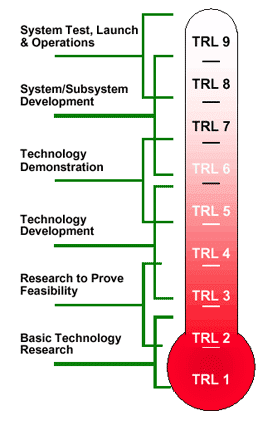
When Gear Technology asked about the technology readiness level (TRL) of Ferrium C64 for AM, Jeff Grabowski, manager of business development at QuesTek, said, “I would put AM C64 at TRL 5 (several industrial-scale atomizing runs; prints at three different vendors and growing; printed and tested actual gear components; measured quite a bit of mechanical property data); and by mid-2023, we should be at a TRL 6.”