The Tools Essential to Power Skiving
Cutting tools and strategies hold the key to maximizing machine performance across the application spectrum
The rise of power skiving to a preeminent cylindrical gear cutting process has been one of the gear industry’s most compelling success stories in recent decades. What began many years ago as a promising, but specialized, cutting process alternative for cylindrical gears with challenging interference contours is now exceeding performance and application expectations across the board. A multitude of machine solutions have sprung up seemingly overnight, from dedicated machines to universal 5-axis machining and turning centers, for soft cutting and hard finishing of internal and external gears ranging from fine pitch modules of just 0.2 or smaller, to module 9 mm or greater, as well as for machining shafts, worms and special profiles such as splines or cycloidal gears. The process, depending on application parameters, has proven to be many times faster than shaping, much more flexible than broaching and, in some cases of external gears with small overrun space, can even outperform hobbing. Power skiving can now be applied to greatly improve the productivity of cutting everything from small, complex, high-precision gears for electromobility or robotics, to larger gears, where cycle time savings can add up quickly and quality parameters have never been higher.
Now, if only it were that simple! There’s a reason this process, more than 100 years old, languished on the gear production sidelines for so many years. The best possible result can only be achieved with a particularly rigid machine and drive line that, as a whole, delivers the necessary stiffness. Furthermore, the process works best in a complete system all working in concert: process simulation, production machine, metrology support, workholding, and—of course—the cutting tools.
Tooling Up for Optimum Results, Small or Large
Identifying the optimum cutting tools for power-skiving applications is of critical importance. Simulation software, whether proprietary or “off the shelf,” enables the end user to simulate the entire skiving process in advance—an indispensable first step to determining the most effective process strategy and tool design. The simulation software analyzes the impact of various tool geometries and process parameters on chip formation, gear cutting quality and the collision situation, as well as effects on cycle time. Gleason has, through long experience and considerable application expertise in the field, been a pioneer in the development of conical and cylindrical cutting tools ideally suited to meet the challenging requirements of power skiving. When coupled with a suitable machine, the performance results are very impressive. Here are two recent, real-world application examples of power skiving tools at work, and how customers have benefited.
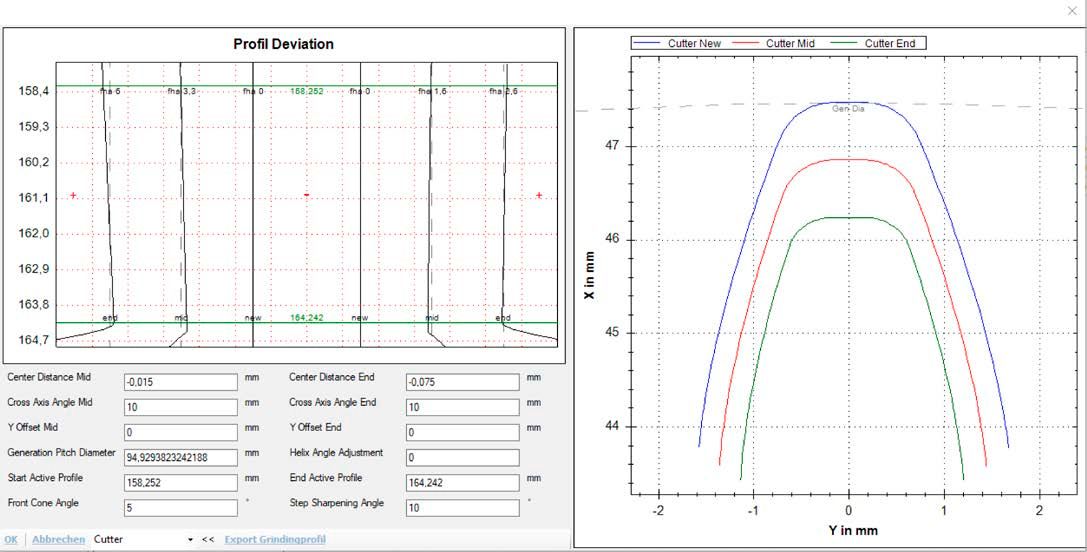
Example 1: Internal Gear, Fine Pitch
(0.25 mm Module)
The workpiece in this case is a “strain wave” cylindrical internal gear, with 320 teeth, cut on a Gleason 100PS Power Skiving Machine. Strain wave gears are commonly used in industrial robots where backlash-free, very high precision performance is of the utmost importance. This particular workpiece consists of an internal gear, which meshes with a flexible cylinder with an external gear. The internal gear is an excellent candidate for power skiving. While the external meshing gear can be hobbed, a shaping operation would typically be used to produce the internal gear teeth. However, in the case of this small-module internal gear with a high number of teeth, power skiving proved to be the perfect alternative to achieve significant improvements in productivity and quality. For this application, Gleason provided a conical, solid-carbide tool with AlCroNite Pro coating. The tool featured quality AA, 163 teeth, designed for a 10-degree cross-axis angle. The power skiving application resulted in a total cutting time of just 0.6 min, performed in four cuts. Gear quality was exceptional as well: an IT5 acc ISO 1328 was achieved, with most criteria even better. Note that, with the solid-carbide tool, resharpening and recoating can be used, extending tool life to the point where the profile no longer meets the requirements.
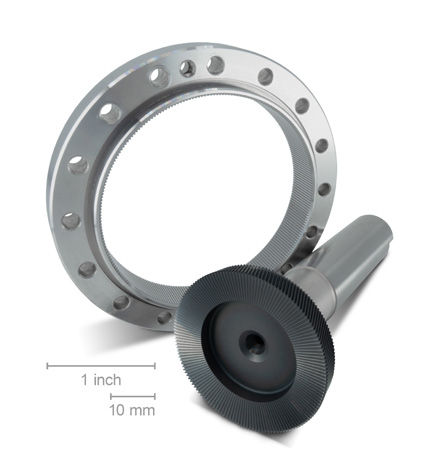
Example 2: Large Internal Gear
(9.5 mm Module)
Power skiving of internal gears with modules 2–4 mm is reasonably common today. For larger modules, however, profile milling or shaping is still considered the norm. However, this recent example—an internal gear, 60 teeth, 600 mm in diameter, module 9.5 mm—demonstrates how the power skiving process is inherently faster than traditional processes for soft cutting of workpieces this large, or larger. In this case, the power skiving time was just 45 minutes, as compared with profile milling (approx. 65 minutes) and shaping (approx. 290 minutes).
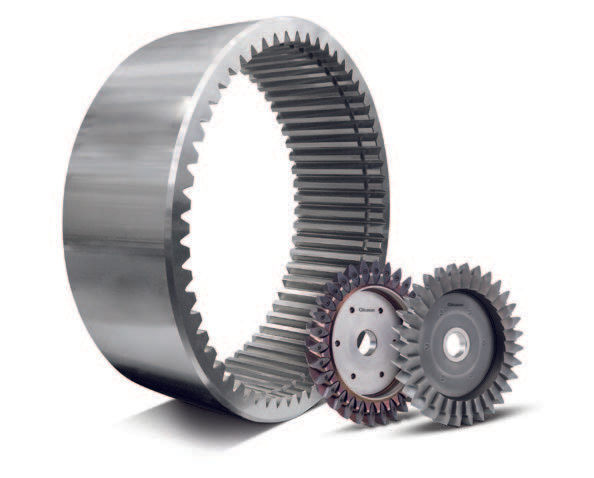
For this application, Gleason chose to optimize the process in two steps: 15 roughing cuts with a carbide-inserted tool in quality B and then finishing with a solid PM-HSS quality AA cutter. Both cutters featured AlCroNite Pro coating. Additionally, the Gleason 600/800PS Power Skiving Machine was equipped for automatic tool change between roughing and finishing cuts.