Unlocking the Potential of Power Skiving
Improving gear production flexibility and efficiency
Power skiving has evolved from a complex and difficult-to-control cutting method into a viable alternative to traditional shaping or broaching. Liebherr-Verzahntechnik GmbH’s Skiving3technology package combines machines, tools, and processes to make gear skiving more efficient and flexible. This advancement enables manufacturers to machine a broad range of workpieces, from small to large batch sizes, making it suitable for both series production and contract gear manufacturing.
The Evolution of Power Skiving
Gear skiving is a rotary gear-cutting process where the workpiece and tool are positioned at a cross-axis angle. This setup allows for high flexibility in machining while also offering productivity and cost benefits. Skiving is versatile and can be applied to various workpieces, including large and small gears, external and internal gears, and even workpieces with interference contours. However, the complex kinematics of the process historically limited its use.
Haider Arroum, Head of Sales for gear cutting tools at Liebherr-Verzahntechnik GmbH, recalls how gear skiving used to be a repetitive process prone to errors. Once the machine was set up, it was often best to avoid making changes to prevent inaccuracies. But advancements in machine technology, such as direct drives, along with new tool materials and intelligent simulations, have revived interest in skiving in recent years, improving its reliability and productivity.
Streamlining the Power Skiving Process
Liebherr is a leader in gear skiving, offering the Skiving3 technology package, which provides a holistic solution by integrating machines, tools, and processes. This synergy results in faster manufacturing rates, improved quality, higher output, and reduced costs. Marcel Sobczyk, a gear cutting tool applications expert at Liebherr, notes that the switch to skiving has led to improved product quality and delivery times in their own contract manufacturing operations, such as spline and mating gear production.
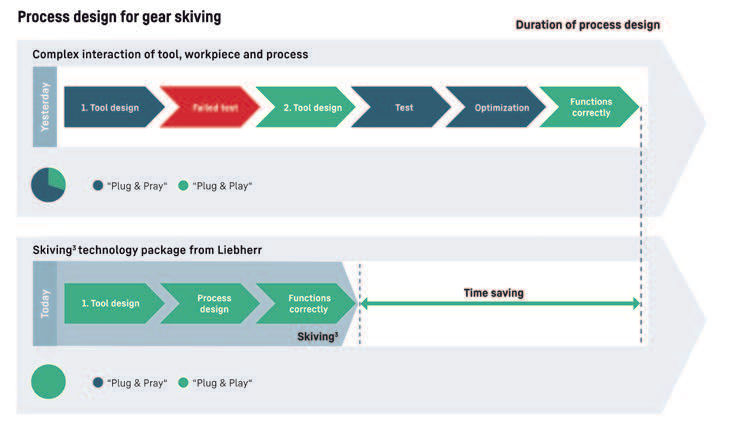
Flexibility in Production
Historically, gear skiving was primarily used in high-volume series production. However, the Skiving3 technology has extended its applicability to small batch sizes, offering manufacturers more flexibility. By using advanced simulations and automatic corrections during the tool design phase, the right parameters are set early on, ensuring the first part is made correctly and the process runs smoothly from the outset.
This flexibility is particularly valuable in industries like e-mobility, where speed, precision, and productivity are crucial. Skiving3 has also proven beneficial in small-batch production, as demonstrated in Liebherr’s contract gear manufacturing. Sobczyk explains that only a few parts need to be run in before achieving high-quality production, which is ideal for job shops or manufacturers with medium to small batch sizes of 20 to 30 parts.