Variables to Consider for Broaching on CNC Lathes, Mills, and Machine Centers
Manufacturing continually evolves as technologies become sufficiently versatile and affordable. When it comes to gear manufacturing, CNC machining allows the performance of multiple operations on a single machine, significantly reducing cycle time. Because broaching is a secondary operation still performed using conventional techniques, many gear manufacturers subcontract broaching to specialty houses when the manufacturing process requires splines or keyways. Because gear manufacturers continue to face long lead times and protracted supply-chain issues, replacing costly, time-consuming subcontract work with in-house capabilities is beneficial to manufacturers and customers alike.
John Gardner, owner of CNC Broach Tools in California, says, “I call it the emancipation of broaching. The manufacturer wants to be able to make their own stuff and do this process on their own. And I find with the advent of CNC lathes and mills where the operations are done on one machine, broaching is kind of one of the last processes done offline.”
duMONT CNC Broaching System
Courtesy of Pilot Precision Products Broaching is an unusual machining process, because it has the feed built into the tool, which effectively makes it a collection of single-point cutting tools arrayed in a sequence. Analogous to the multiple passes of a shaper, a relatively new class of CNC tooling and programming allows broaching operations to be done without the need for a second operation, thus greatly increasingly quality control and reducing time, space and cost.
“At the OEM level, if they are fully invested in secondary operations, the pull side of broaching is still the fastest metal removal rate. You’re never going to beat it in a CNC,” said Marco Morgado, Director of National Business Development for Pilot Precision Products, makers of the duMONT CNC Indexable Broaching System.
“It’s where you get into the Tier 1 and Tier 2 contractors who don’t necessarily do a lot of broaching that the CNC broaching is very intriguing to them and is our fastest growing segment. In the last two years, we’ve had 42 – 48 percent growth year over year. That is the future of broaching. For many customers, not all. We don’t see linear broaching going away.”
It can’t be emphasized enough that the software program itself is more than half the battle when it comes to tool life and productivity. Despite the technology having been around for more than a decade, Morgado explains that CNC broaching is still relatively novel in the U.S. because “there’s no canned CAD software that has CNC broaching programming built in. That’s the biggest obstacle of entry. We wrote a macro for variable controls to help customers apply CNC broaching. There is not a lot of standard programming out there, but it’s coming.”
Static vs. Live Broaching Tools
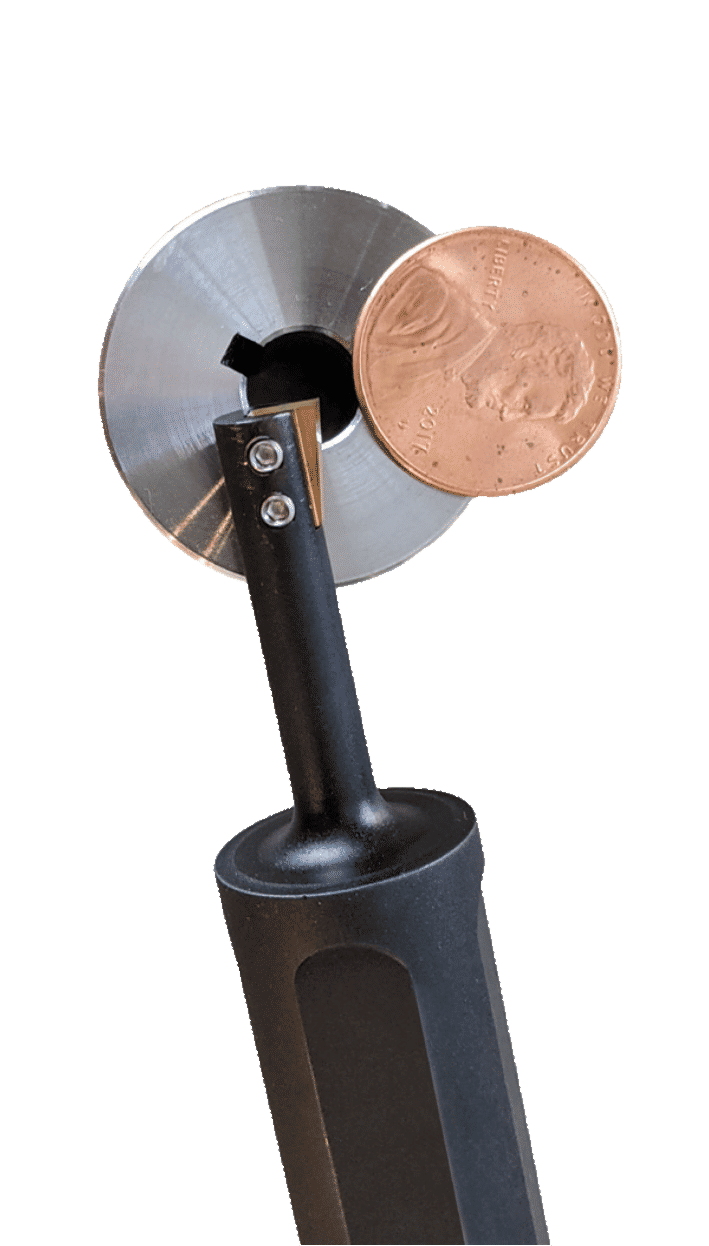