“Governmental influence on the overall market.”
“Raw material cost increases.”
“COVID absences.”
“Automation of production and inspection due to the lack of skilled operators and technicians.”
“Development of next gen workforce.”
“Supply chain and steel constraints. Difficulty to get the right steel grade in a timely manner. U.S. forging houses have very long lead times.”
“Supply chain issues are creating very difficult situations with regard to being able to deliver in a timely manner. Constantly changing replies from vendors make it increasingly difficult to give the customer a commitment that you can stand by.”
“Electro mobility, advanced agriculture applications, wind mill generator gearboxes.”
“Long-term view and targets shared by customers to gear suppliers are essential to create a true partnership. Tomorrow’s winners are companies that are able to provide to their gear suppliers a long-term vision and targets to enable suppliers get ready for the next challenges. We may lose alone, but we win only together!”
“Trend to production with skiving cutters.”
“Renewable energy. Wind turbines pitch and yaw drives. Electric vehicle drives. Highly efficient drives.”
“Sustainability - retrofit older machines; EV gearboxes - requirements and solutions; ICEs - improve fuel consumption.”
“Globally local support of big players more important to international customers.”
“High RPM with low NVH.”
“Agri market in Russia and construction market worldwide look strong and it will stay in 2022.”
“Supply chain to meet increase in product demand.”
“Discounted price demand from customer with increase in commodity prices calls for value analysis and value engineering.”
“Electrification.”
“High speed gears.”
“Supply high quality product with reasonable delivery time.”
“Challenge of creating the next generation of technical skilled workers. Continued supply chain issues and inflation.”
“Wind energy, renewable energies.”
“Paying more attention to planetary gears with control.”
“Epidemic, politics and industrial development in various countries.”
“The adaptation of direct drive technology in all sectors of transmission industry may become a challenging time in the near future and more so in automobile sector.”
“Optimization in product selection and design, process selection. Good finishing teeth surfaces, vacuum heat-treatment.”
“Electric drives.”
“Lack of workers with gear knowledge on the workforce.”
“Higher complexity and finishing grades required by e-mobity applications.”
“Will we have a recession after this inflation.”
“The move to electrification of the automotive industry. What will transfer to direct motor technology?”
“Supply issues.”
“Material lead time and availability.”
“Material pricing.”
“Qualified labor market and their interest to work.”
“Skilled labor difficulties.”
“E-mobility mainly.”
“Cost increases on materials.”
“Government regulations, inflation, transportation costs, material shortages, skyrocketing material costs.”
“Lack of qualified workers.”
“Not enough emphasis on gear train architecture.”
“EV market .”
“Transmissions for electric vehicle.”
“Cost and availability of materials.”
“Worker shortages.”
“Manufacturing sector is highly affected during COVID times. Gear manufacturing is one of them. Potential is good but skilled labor is in shortage. Raw materials are issue. Many related factories are under lockdown or closed.”
“Automotive electrification, superfinishing of gears, gear polishing.”
“Inflation on materials and services. Skilled labor shortage.”
“Digitalization.”
“More power densitiy on gears.”
“High efficient gears/less standards.”
“Skilled labor in gear machining. Next generation interest in metal manufacturing. Trades need to be part of high school learning in order for USA maintain the skill labor edge.”
“Automotive sector is swiftly switching to electric.”
“Space industries are booming.”
“How will EV penetration affect auto gears? How will chip shortages affect trucking gears?”
“Lack of qualified employees both at our own facility and those of suppliers. Lack of management understanding what equipment new employees are willing to learn to operate.”
“Precision (quality), size and quantity of gears demanded by electric vehicles versus the actual combustion vehicles demand.”
“Measuring gear vibration when assembled into gearboxes as an indicator of defect (mainly gear noise).”
“Downturn in military helicopter sales, slow recovery of commercial airlines and production issues at major airframers.”
“Problems with the raw material production.”
“Vehicle electrification.”
“Market changes due to the pandemic.”
“Supply delays.”
“Gears for e-mobility.”
“Imports from China and Taiwan. The rates of the gearboxes imported are unbelievable, and we cannot compete.”
“Electric mobility.”
“Transition from ICE to EV.”
“Existing players needs to be involved in diversification of their product portfolio, i.e. to explore EV related opportunities.”
“Improvements in gear design...”
“Electric vehicles and fuel cell vehicles’ penetration and growth are a disruptive element in gear industry.”
“High operating costs making it more difficult to compete. Raw material and utilities such as gas and electric. Problems finding employees.”
“Electrification.”
“The geared drives all along the industry were affected through this pandemic, many enterprises stopped extension projects on their production plants and made just the necessary maintenance works. Nevertheless, now with vaccines developed and people coming back entirely to work in the first quarter of the year, investments will arise and the gear industry might have a lift up. It’s optimistic.”
“Electrification.”
“(Electric Vehicle) EV.”
“Special plastic gears and sintered worm gears.”
“Electrification.”
“Being able to get both labor and materials will affect us this year. The COVID virus and variations have hindered getting labor, and current supply chain issues around the world make getting components and raw material more difficult this year.”
“Getting employees and rising costs.”
“Price increases in shipping and shipping delays.”
“Material increases.”
“Continuing microchip shortages.”
“Material shortages, price increases.”
“Quality of workmanship.”
“Quality of material.”
“Huge labor shortage.”
“Lack of contact with customer on face to face basis, to highlight capacities and capabilities.”
“The future of automotive drivetrains. Rate of change and mix of IC, Hybrid and BEV. Drives will change, but supply of energy and transmission is not being addressed.”
“Availability of local steel and forging capacity as more companies are localizing gears in order to meet the USMCA targets.”
“Hard gear finishing with skive hobbing, scudding.”
“Disconnect from buyer and manufacturing. High tooling costs, low production numbers.”
“Supply/procurement shortages. How long will the industry take to return to predictable and consistent supply?”
“Shortage of raw materials on international market.”
“Materials, gear shaping, increase strength of gear.”
“ Supply chain issues are hampering capacity. Business is moving elsewhere due to this.”
“1) Hiring quality employees and retention. 2) Investment on next generation equipment. 3). Supply chain issues and government inflation will affect the ability to stay competitive globally.”
“Tighter tolerances with same expected turnaround times and inspection reports.”
“Orders.”
“Employees.”
“Raw material lead times and pricing make it hard to supply customers as well as increasing labor shortages AND hourly wages compared to even fast food facilities.”
“Health of auto industry and material availability. Supply chain.”
“E-Mobility with great impact on the manufacturing industry.”
“New methods like power-skiving are being implemented on multi-tasking machines, enabling complete machining and fulfilling very high precision demands.”
“Electric vehicles.”
“Digitization of the daily life, making gears omnipresent for transmitting power from a click to an actuator.”
“Finding people.”
“Increased costs/inflation.”
“Offshore competition, increasing costs due to inflation, coupled with the current labor shortage will be an issue facing the gear industry and the U.S. in general.”
“Supply chain - tied to on-time deliveries.”
“Prices for raw materials affect final products’ prices.”
“Hiring new qualified employees and retaining the existing ones — affecting productivity.”
“Attracting younger generation into manufacturing to replace those who retire, and avoid a huge intellectual/knowledge and production gap.”
“Factory automation — affecting manufacturing process, especially when it is hard to find workers.”
“Offering packages instead of individual products.”
“The impact of the electric vehicle on the powertrain gear box and transfer case.”
“Ability to find qualified machinists and the supply chain issues continue to hit our bottom line severely.”
“Training of engineers with respect to design and manufacture in smaller companies.”
“Gears sold to the energy sector, fertilization producers and plastics industries are in a state of uncertainty as politicians influence the maintenance and development of these industries subject to scrutiny orchestrated by climate change.”
“The pandemic.”
“Defense industry cyber security requirements. The aerospace industry is still in hibernation. Price of raw materials keeps increasing.”
“3D gear printing, gear design customization for a particular application.”
“Electric vehicles, additive manufacturing, laser inspection.”
“The landscape of gearing is changing. The amount of gears may be fewer, but all will be hard finished and the quality critical to the success. Noise issues take front and center with EV, and printed gears will become a factor as powdered metal did 20 years ago.”
“Employees.”
“Effect of electric vehicles on industry.”
“Whether the supply chain is stable.”
“1. Moving towards more precision gears; 2. Increased gear grinding requirement; 3. Increased traceability requirement; 4. Increase in gear export from India; 5. Visibility of shop floor CMMs.”
“Pandemic’s impact on labor force.”
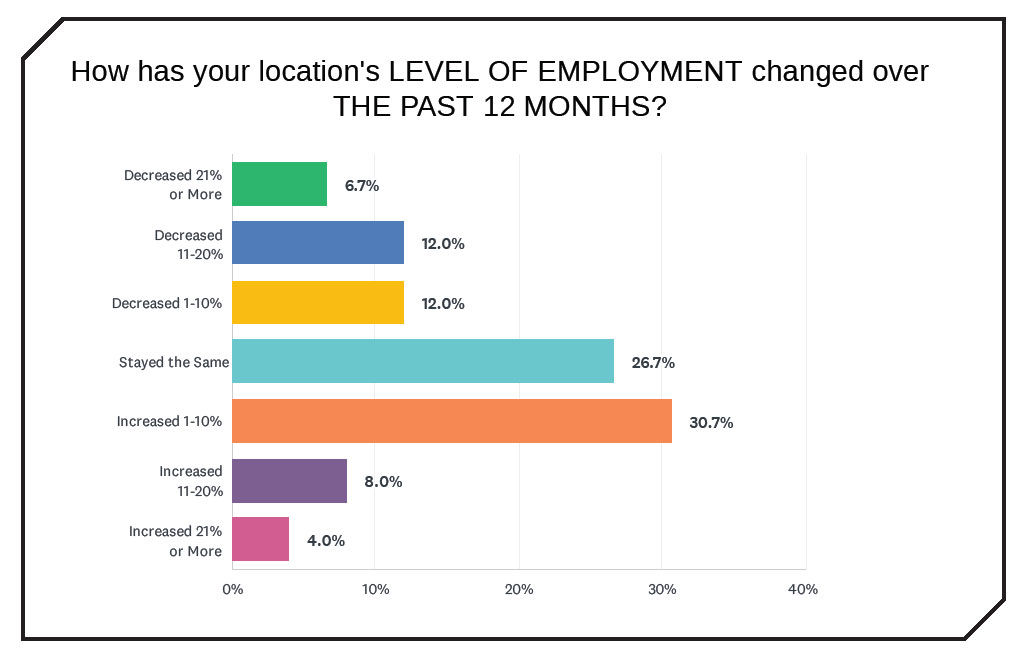
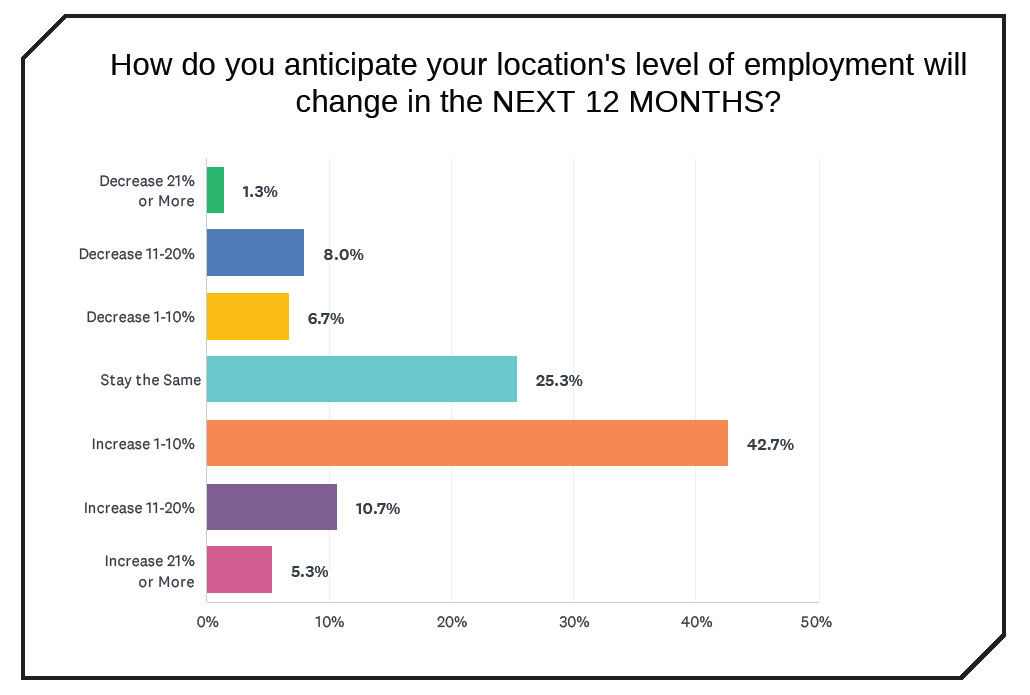
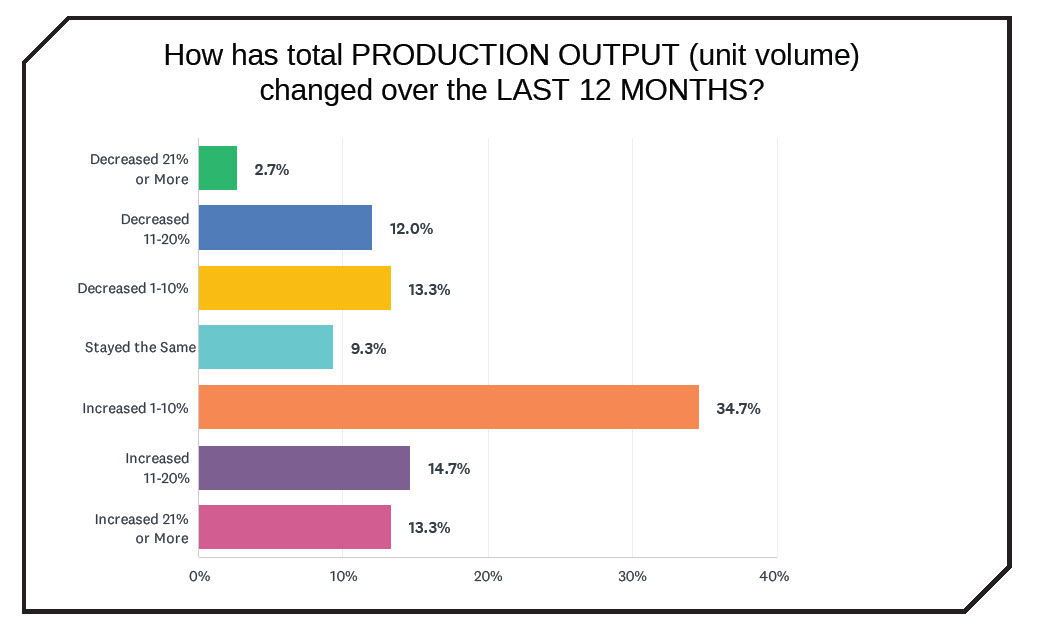
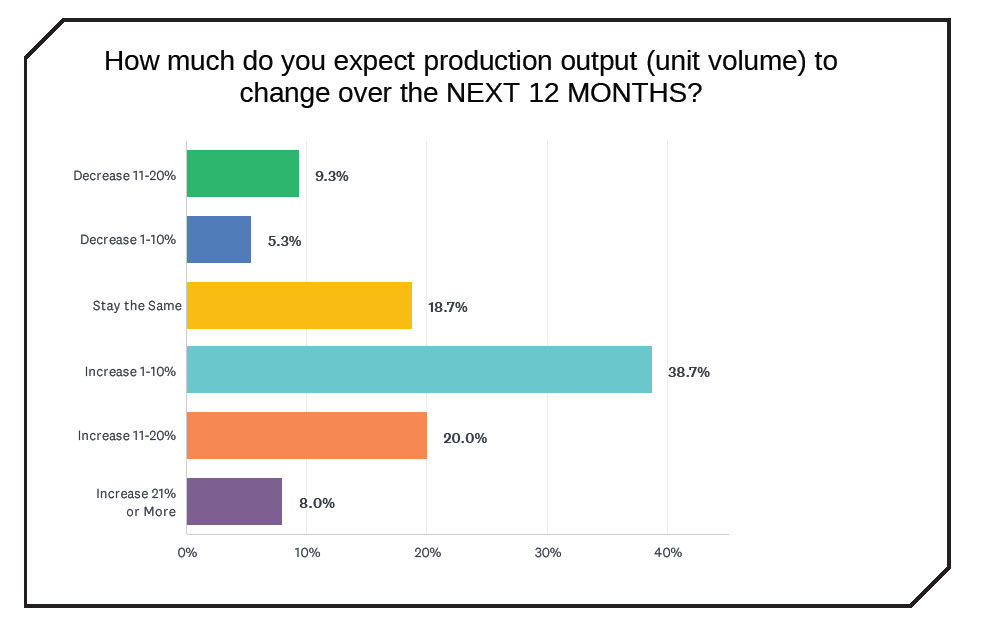
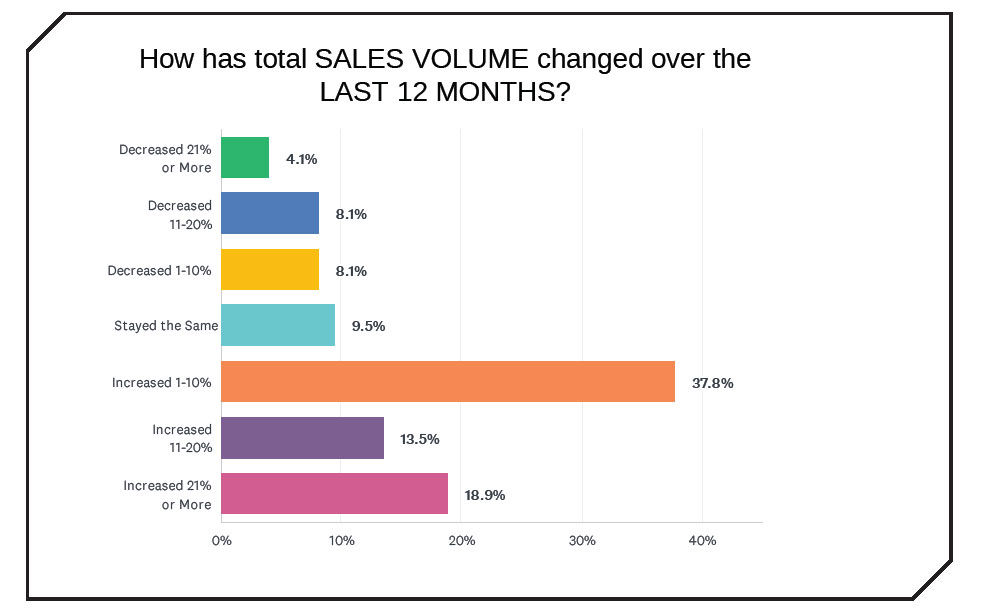
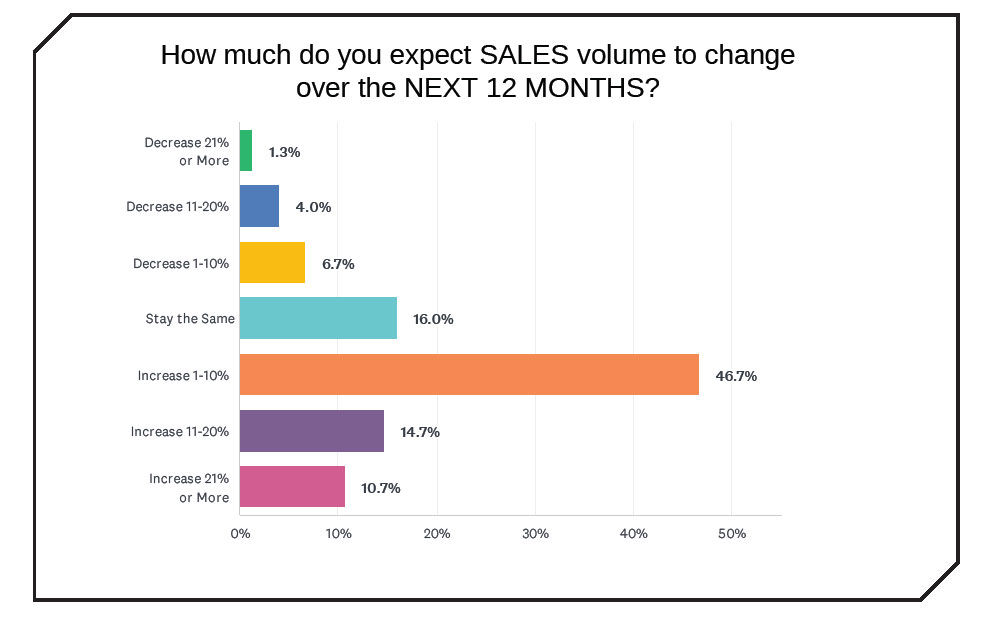
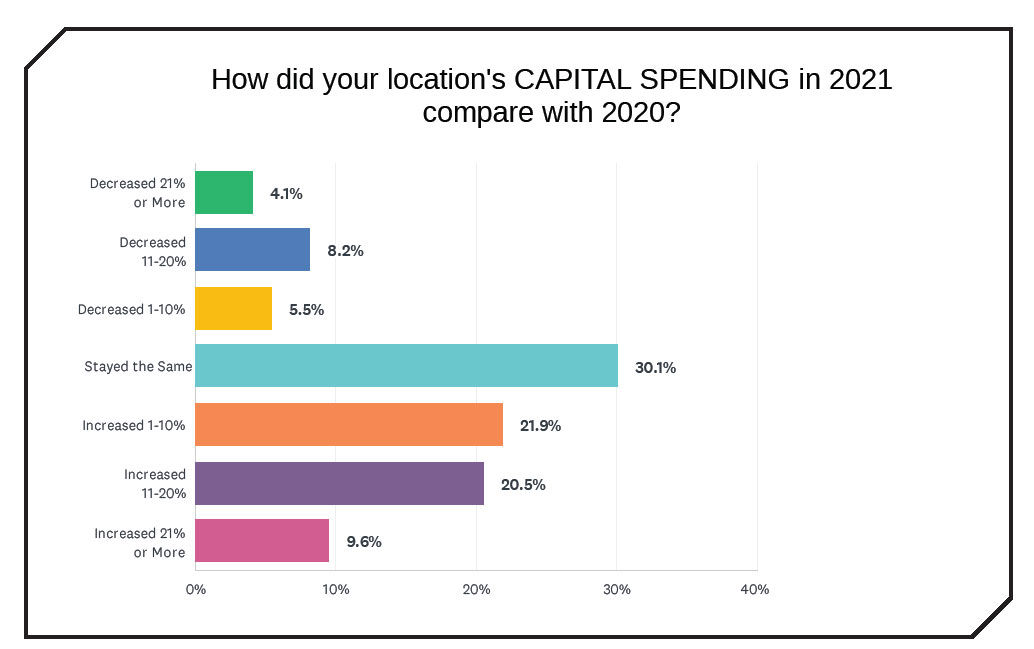
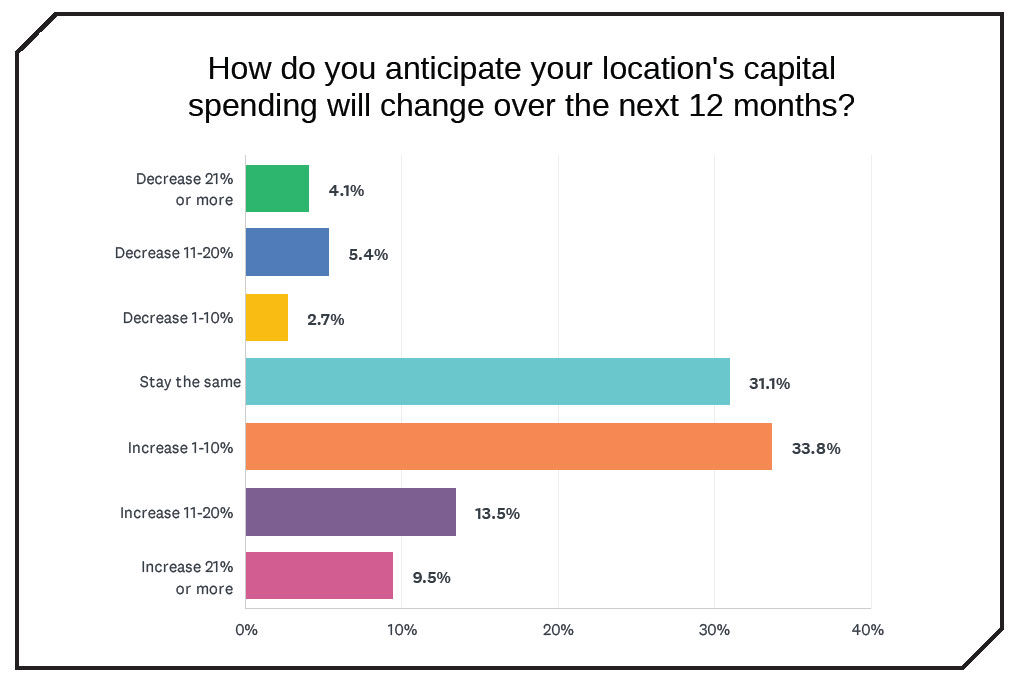
How has the COVID Pandemic affected your business?
“Dramatically. Huge reduction in demand for civil aircraft parts.”
“Extremelly hard. Several projects were stopped.”
“Caused many delays and now is just the excuse for anything that costs more or is delayed.”
“Absences. It is difficult to recover from absences in today’s environment.”
“The first year was very tough due to automotive pause. 2021 ended up being a record year for us once automotive came back to life.”
“Restricted access to end users did require different sales approach to maintain and grow order intake.”
“Impacts on workforce availability due to illness and supply chain has made it difficult to provide reliable lead times.”
“Being an essential business we have been able to stay open the entire length of the pandemic and business has actually increased due to the product line.”
“Meetings with customers and supplier are more difficult.”
“Presence of associates at work has become hardly predictable; Suppliers share same problem, so, deliveries of raw material/half finished blanks have been delayed throughout the year.”
“Slump late 2020, early 2021. Steep rise later in 2021.”
“2020 dipped from previous but 2021 bounced well back.”
“Delay in shipment from supply chain; difficult to hire workers to increase our production to respond to the increased orders.”
“Decreased production capacity.”
“Difficult in travels, no raw material availability.”
“20% revenue loss.”
“Growth is positive. But getting raw material at competitive price became hurdle.”
“Fed and State dysfunctionality on safety and protocols are simply astounding. Some level of uncertainty is expected. The lack of clear direction and significant uncertainty, constant state of turmoil was massively disruptive to efficiency.”
“Difficult to man all machines with laborers not able to show up. Little interest in new people taking open jobs.”
“Very little impact.”
“Not very seriously.”
“Hasn’t.”
“It has made it more difficult to predict employee engagement. Having whole departments out due to COVID.”
“Lost one employee completely. Have had to shut down departments within the organization due to Covid related illnesses.”
“Sales are stagnant. We are still comparing ourselves to 2019.”
“Decrease in demand from commercial airline customers, attendance challenges.”
“Lots of volatility in the business.”
"Decreased sales compared to 2019; 2020’s sales of gearboxes were 80% compared to 2019.”
“Hard to find employees, everything costs more.”
“Not at all.”
“2020 was worst period. However 2021 we surpassed previous best.”
“Minimally.”
“Laid off night shift.”
“Bad shutdowns.”
“Increased our customers’ demand for our product.”
“Continues to limit face to face interaction.”
“Projects have been delayed.”
“Somewhat positively from the revenue standpoint. It kept us very busy from keeping employees healthy and safe to making our customers happy. Many unprecedented situations and questions had to be resolved and addressed, as well as going thru a long period of adaptation.”
“Hard to find people and many want to work from home.”
“Having employees quarantine for a positive test even though no symptoms are present has significantly affected our production efficiency.”
“Significant reduction in revenue.”
“High absentee rates, lateness in receiving product due to shipping delays.”
“Covid tossed in the proverbial Monkey Wrench. Between remote employees and absences, it takes a lot longer to do some simple things.”
“The flow of people and goods got worse.”
“Very minor effect.”
“Increased challenges in managing an already thin workforce.”
“Had a staffing issue when 5 of 10 employees had covid at the same time.”
“The pandemic has completely transformed how we approach sales: meetings are nearly all remote and live, and travel expenses have plummeted.”
“Initially took a hit, has since recovered.”
How are you handling and navigating supply chain issues heading into 2022?
“Minimal issues with supply chain.”
“Not handling.”
“Fortunately, in our company the impact of lack of supplies has not been significant.”
“Looking for other vendors to fill the gap.”
“Adding more suppliers..”
“Day to day…”
“These issues are handled by our Corporate division. For components without contracts, cost increases are passed through.”
“So far, we have not had supply chain issues. We are purchasing ahead of orders on some longer lead time parts.”
“Pre-order and more planning.”
“Steel substitutes and finding new suppliers.”
“Probably the biggest issue ahead along with hiring skilled labor. Looking for alternatives to the current vendor base. Increasing stocking orders to allow for the extended lead times and to minimize the constant price increases.”
“Anticipating the order of new material.”
“Providing longer and more stable planning; periodical meetings to assess suppliers are providing us adequate capacity.”
“Taking early action. Seeking alternative suppliers. Higher Stock levels.”
“Freight costs and delivery times are channeled directly to customers and quotes.”
“Try to find other suppliers who have available capacity for the new business.”
“Trying to find alternative suppliers and work with higher stocks.”
“Monitoring closely, developing alternate sources, but the prices of raw material are not stable.”
“With difficulties. Need to extended supply network.”
“We continue to significantly adjust schedules and take down weeks because of lack of material and supplies.”
“Doing the best we can, planning where we can.”
“Badly.”
“It is our No. 1 concern.”
“Quoting longer lead times. Increasing prices to cover additional costs.”
“Increasing inventory while seeking alternative sourcing.”
“Apprehensively.”
“Lead time extensions.”
“You have to work more closely with customers as to deliveries.”
“Purchasing excess inventory to hedge for shortages.”
“Paying considerably more if materials are even available.”
“Looking ahead for materials required. Allowing more time for outside services.”
“Suffering with the inflation of prices but no lack of supplies. Our customers are being more impacted than we are.”
“The beginning of 2022, material availability has been slow in stock and delivery. Steel suppliers have consolidated their inventory to specific key cities. Large steel orders and small are slow to fill.”
“Pessimistic .”
“Management cannot formulate a plan as our suppliers are affected randomly and are struggling to keep up.”
“Order early.”
“Preparing the stock for the critical pieces (bearings, some raw materials) and increasing the future contracts.”
“Long-term call orders.”
“We try to keep at least two suppliers.”
“Larger stock built.”
“Some parts shortage affected the total output.”
“Buy early and more than usual.”
“Lost production due to shortage.”
“Using multiple suppliers.”
“Work with what I have in hand, telling our clients our situation before accepting the job.”
“Long-term agreements, larger stock.”
“Delivery time increased.”
“Poorer selection.”
“Buying ahead, more shopping for price.”
“Our customer schedules are getting affected due to this.”
“Buying in advance on projected requirements.”
“Buying extra and ahead of normal.”
“Minimal negative impact.”
“Just dealing with upset customers for the long shipping delays!”
“Poorly.”
“We’re not.”
“Ordering parts as early as we can and sometimes we search ebay and Amazon for short order supplies.”
“Very well.”
“Dual sourcing as much as possible as well as bringing on new suppliers. Carrying more inventory.”
“Additional pre-planning, anticipating requirements.”
“Not a big problem.”
“No real supply chain issues.”
“With some delays that affect production, but were able to find intermittent solutions.”
“So far not so bad except for price increases.”
“By forcing our forwarders to look outside the box for savings/lead time improvements. Also adjusting budgets for the increase in costs.”
“Careful prediction of needs for forward ordering to adjust for logistics issues.”
“Preordering raw materials where deliveries may be critical.”
“Like everyone else, trying to be patient while leveraging any and all connections.”
“Doing what we can to stay ahead of any issues. Finding backup suppliers.”
“Increase inventory.”
“Increase the frequency of contact with suppliers.”
“Stocking heavily on items where we are confident there will be turnover.”
“Spending more and waiting longer.”
“Supply chain is slow in delivery.”
“All quotes have been updated with extended deliveries. New vendors have been found for competitive shipping solutions.”
“Stretching commitment times.”
Demographics
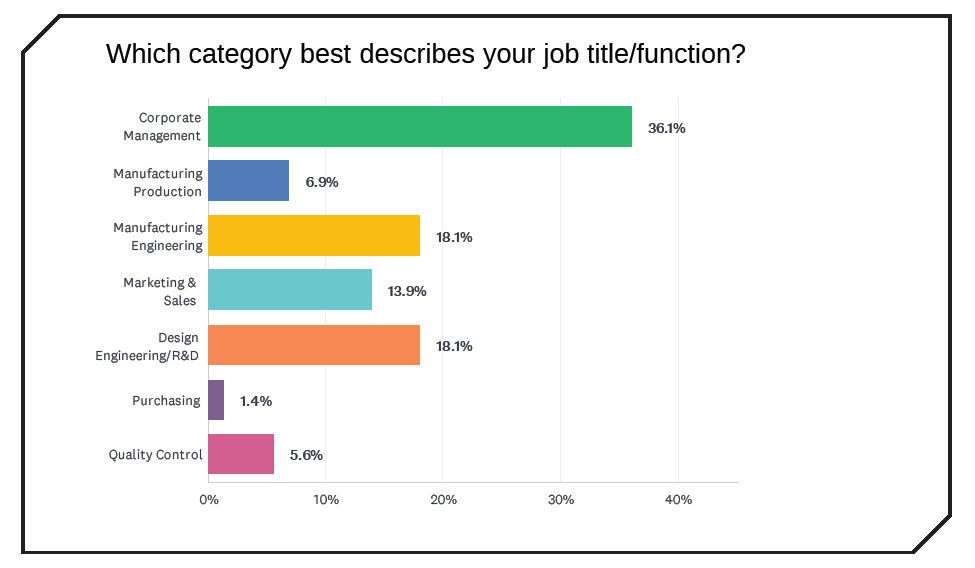
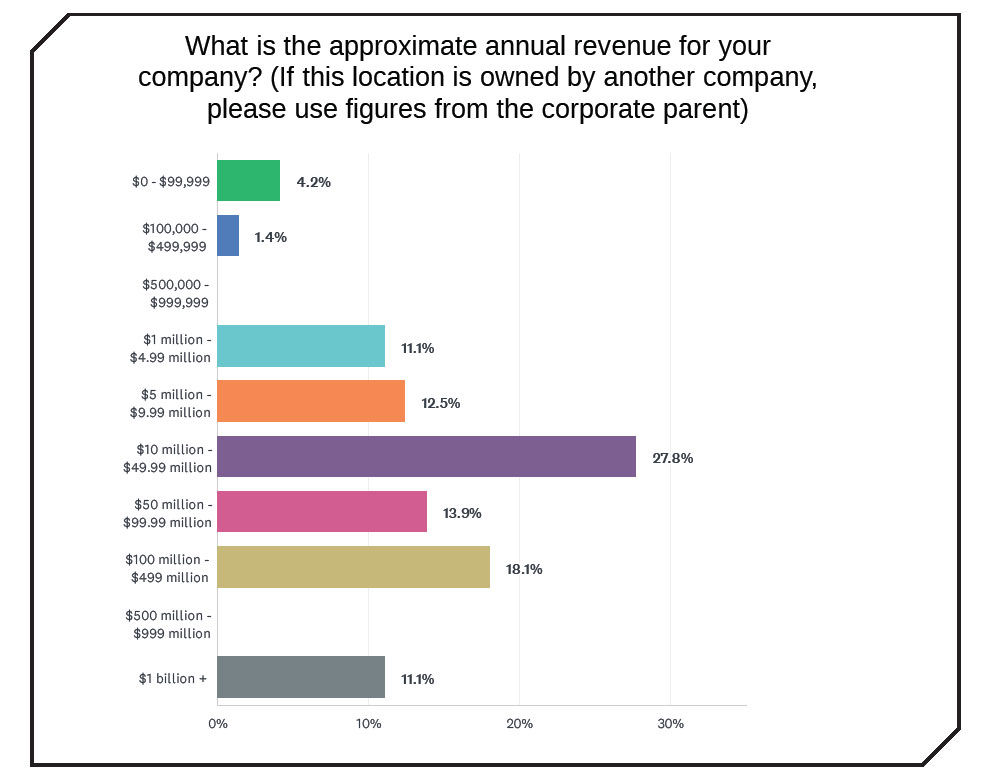
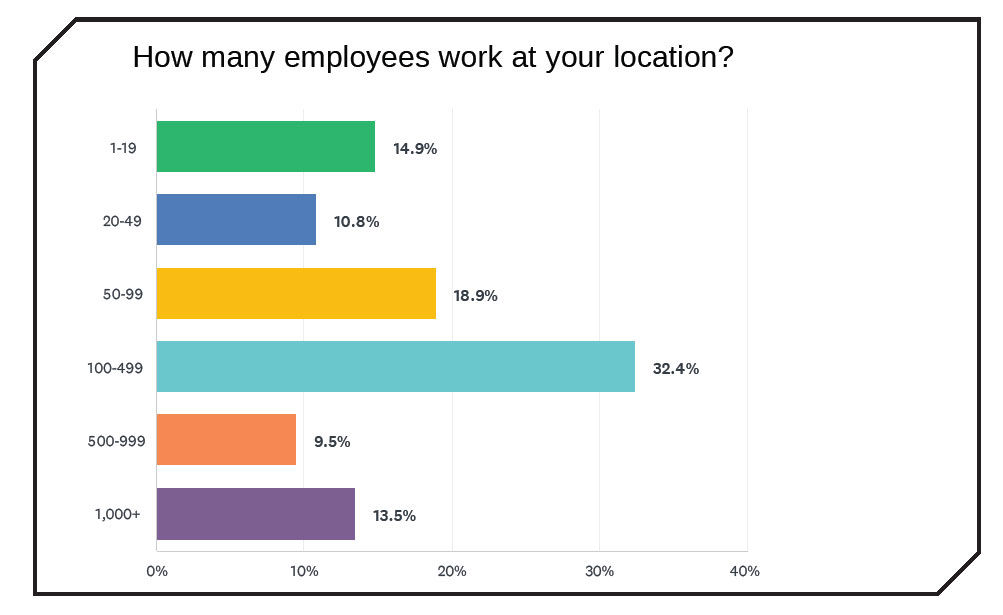
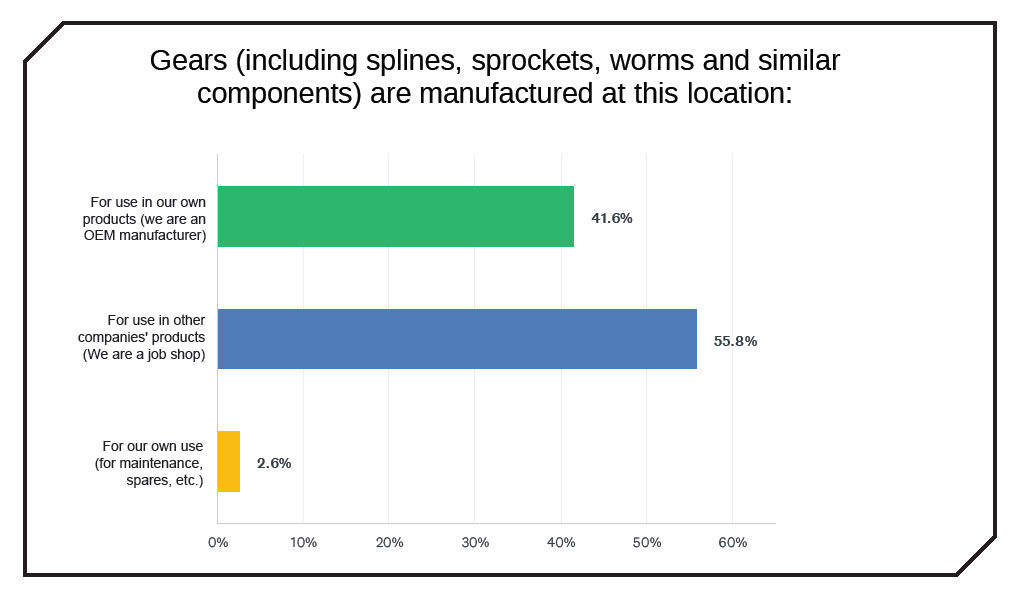
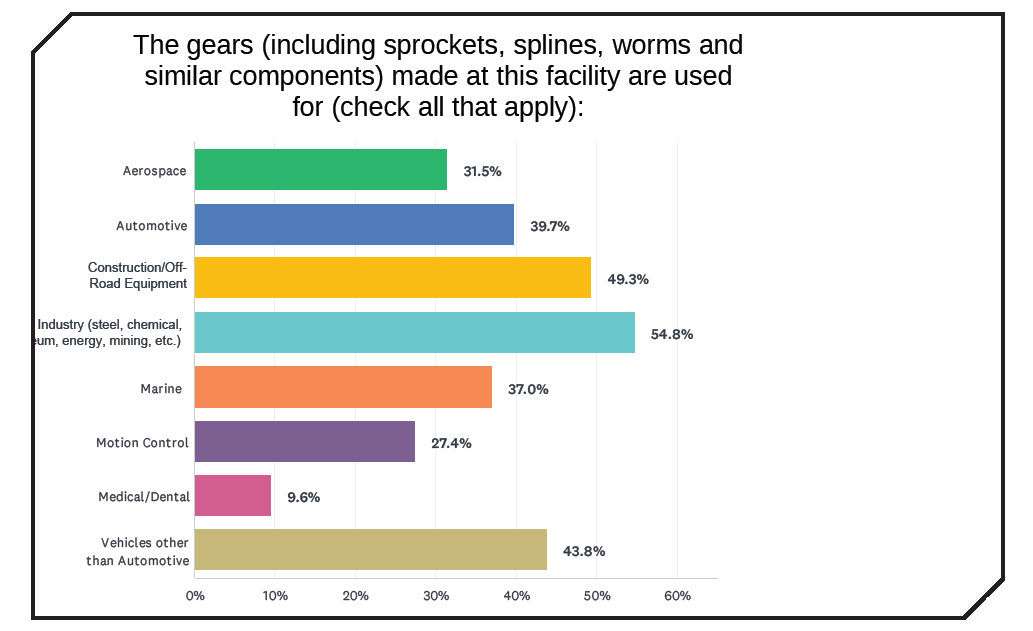
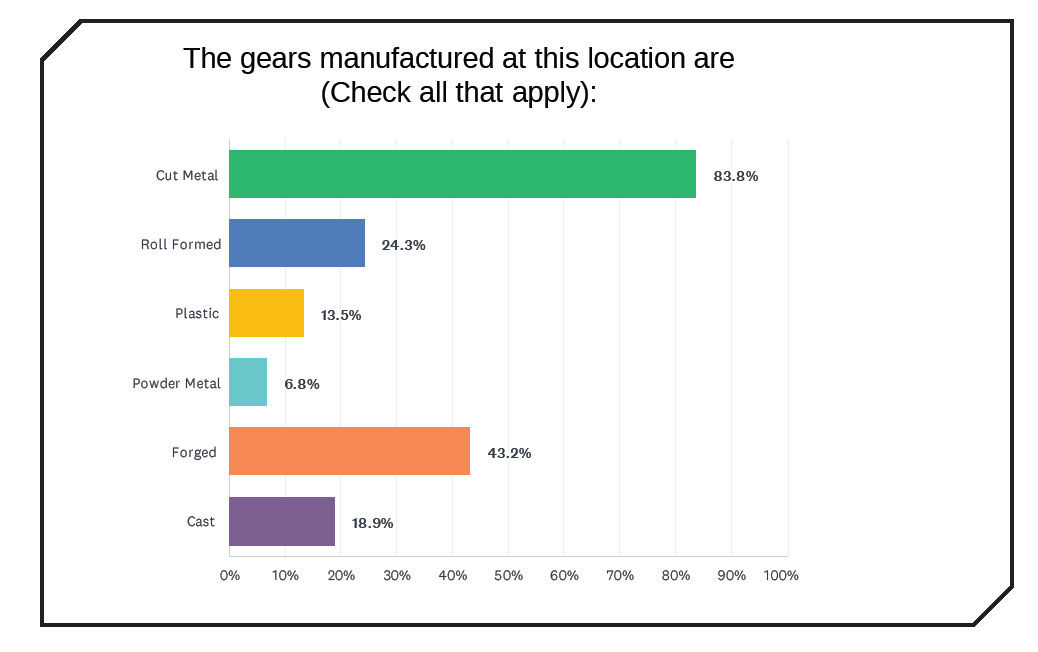
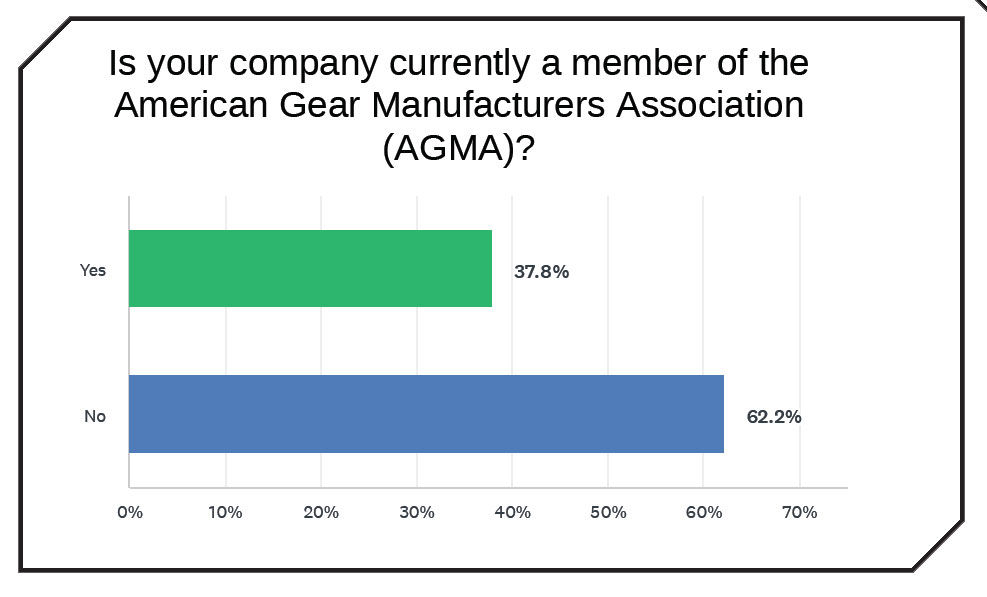