Tyrolit Announces Management Changes
Dr. Christoph Swarovski already declared a year ago that he would be stepping down from the executive board in the first quarter of 2022 after 20 years in the company’s management. However, he will continue to support the company as a member of the advisory board: “I would like to thank all employees and partners for the successful years in which Tyrolit has developed into one of the world’s most successful market providers. I look forward to remaining associated with Tyrolit as an active member of the advisory board.”
Left to right: Thomas Friess and Christoph Swarovski.
Thomas Friess will take over the position of Chairman of the Executive Board on January 1, 2022. The international orientation, continuity at all locations and the development of future industries will remain the focus of the family-owned company.
Friess comes from Germany and has lived in Austria for 18 years. The married family man holds a degree in business administration and has held numerous management positions at internationally active companies in Germany, the USA and Austria over the past 23 years. Mathias Margreiter, Chairman of the Tyrolit Advisory Board: “Tyrolit has a stable foundation for consistent and sustainable growth. In Thomas Friess we have found a highly experienced and qualified person to continue the path successfully taken under Christoph Swarovski.”
Since 2019, Friess has been a mainstay in the corporate development of the international abrasives manufacturer and is very familiar with the strategic orientation of the group of companies, the organization and the values it lives by. “I am looking forward to this responsible task. Innovative spirit, vision and partnership in practice remain central virtues at Tyrolit,” confirms Friess. The new CEO’s particular focus is on advancing digitalization and the development of future industries such as medical technology, electrical engineering and environmental technology. “With the help of innovative Tyrolit technologies, we will ensure the necessary precision within these future industries in the future and also make a valuable contribution to reducing the CO2 footprint,” adds Friess, aware of the company’s successful orientation.
In addition to Christoph Swarovski, Andreas Buchbauer is also retiring from the Tyrolit management board. A new executive board has been appointed for the group of companies around Friess: Peter Dollinger will in hold the position of CFO, Arno Pichler (Metal Industries) and Andreas Sauerwein (Construction) will represent their respective divisions on the board. All three people have already been active in the company for years in the executive board or in management positions.
“Thomas Friess and his team will find a profitable, very healthy Tyrolit Group with an excellent international position. The owner families and the new operational management are clearly committed to the group’s locations and employees. The main plant in Schwaz will remain the heart and brain of Tyrolit,” Margreiter said.
www.tyrolit.com
Jorgensen Partners with Chip Processing Supplier S.F.H.
To strengthen its breadth of product offerings and provide manufacturers a one-stop-shop for all metal chip processing needs, Jorgensen Conveyor and Filtration Solutions has solidified a strategic alliance with chip processing equipment manufacturer S.F.H. based in Saint-Étienne, France. The new business partnership will benefit both companies and provide Jorgensen the exclusive rights to sell S.F.H. products in North America.
Jorgensen will initially focus on offering a wide variety of S.F.H. chip processing products including chip shredders, briquetters and centrifuges. In addition, Jorgensen will offer complete, integrated chip processing solutions. In the future, the two companies plan to introduce several additional products to the North American market.
According to Karl Kleppek, Director of Sales and Marketing at Jorgensen Conveyor and Filtration Solutions, “S.F.H. produces extremely robust chip processing products and systems, and Jorgensen is confident they will be a great partner and perfect fit for our customers in the machine tool industry. This new partnership will enable us to sell individual chip processing equipment and complete turnkey systems alike.” Kleppek adds, “our new relationship with S.F.H. coupled with our wide range of conveyor and filtration solutions position Jorgensen as a complete coolant circuit and chip processing solutions provider.”
With over 40 years of experience, S.F.H. specializes in three key areas of chip management: hydraulic fluid pump systems, equipment for separation of solids and liquids and waste recycling. “As S.F.H. enters the North American market, we welcome Jorgensen’s leadership as our strategic partner in this step toward long-term growth,” said Bruno Fillardet, President of S.F.H. “We’re eager to build on our professional relationship.”
www.jorgensenconveyors.com
Sandvik Coromant To Acquire ICAM
Sandvik has signed an agreement to acquire Canada-based ICAM Technologies Corporation, a provider of innovative solutions that translate CAM data into optimized coding for guiding CNC machining operations. With a global reach, ICAM sells to some of the world’s most renowned companies in the aerospace and defense, general engineering and automotive industries. The company will be reported in Sandvik Coromant, a division within Sandvik Manufacturing and Machining Solutions.
“I am really happy to welcome ICAM to Sandvik Coromant and I look forward to us working together and strengthening our offer to our customers. ICAM’s ability to deliver code reliability across all major CAD/CAM systems is well-aligned with our goal to serve all our customers in the best way possible, with a CAD/CAM-neutral portfolio” says Helen Blomqvist, President Sandvik Coromant.
ICAM’s software combines post-processing, machine simulation, and tool-path optimization into solutions that save programming and part machining time, streamlining customer workflows as the user can go from their CAM system to verified and optimized coding (G-code) in just one step. ICAM’s offering is complimentary with the verification and optimization technology of CGTech, a global leader in software for numerical control (NC/CNC) simulation, verification and optimization, also owned by Sandvik and reporting into Sandvik Coromant.
“For more than 30 years, CGTech has been a leader in simulating CNC machining, while ICAM has been a leading processing provider. ICAM and CGTech synergies will give customers a competitive advantage by reducing machining time and dependency on programming experience. Like CGTech, ICAM is a technology leader with entrepreneurial spirit, and we have known and respected each other for years. We look forward to working with everyone on the ICAM team.” says Margaret Schmitt, president of CGTech.
“I and the rest of the ICAM team are really excited about the future. For many decades ICAM and CGTech have seen the world of CAM systems, computers, operating systems, machine tools and their controls evolve exponentially. And only through hard work, focus and dedication, both companies not only kept pace with all this change but have distinguished ourselves in our respective disciplines. ICAM and CGTech continue to share the same prestigious customer base who use our products as part of the most dependable and accurate Virtual Part Manufacturing Process in all metal removal industries worldwide. On top of all this, we come from the same business culture, we have similar roots and equally have a rare tremendous depth-of-knowledge in a very complex world guaranteeing that this new relationship holds huge potential and promise for developing even greater innovations for our customers for years to come” says John Nassr, owner of ICAM.
ICAM was founded in 1971 in Montreal, Canada, and currently has 27 employees. In 2020, the company had revenues of approximately SEK 30 million and an EBITA margin of approximately 25%. The transaction is expected to close during the fourth quarter of 2021 and is subject to customary closing conditions.
www.sandvik.coromant.com
GearOffice Consulting Announces Product and Service Expansion
GearOffice Consulting Services announces an expansion of its products & services and the launch of a new GearOffice website. In addition to the GearOffice computer program for gear hobbing analysis, the new services include gear design, gear processing, gear inspection and process debugging, SPC for gear manufacturing, and training.
Yefim KotlyarThe GearOffice principal engineer, Yefim Kotlyar, has over 40 years of experience in the art of gearing. His expertise includes developments of various gear cutting & grinding technologies, development of gear inspection and evaluation technologies, development and implementation of SPC for gear manufacturing processes and design and validation of gears and gearing systems. He is the author and one of the owners of GearOffice computer program. Yefim Kotlyar has served on a number of AGMA technical committees and he has authored many articles on gearing subjects.
The GearOffice computer program was designed to performs various hobbing and gear geometry calculations and maintain Gear/Hob/Machine/Hobbing Project records. The program keeps gears, machines, and hobs as independent objects. It can combine a gear, a machine, and a hob into a hobbing project, to determine (or select) cutting parameters, and calculate the results: cycle time, chip thickness, approach and overrun distances, hob setting angle, feed scallop depth, depth of enveloping cuts, force, torque, as well as tooth thickness/DOP/span. It also determines tolerances based on AGMA/DIN/ISO class and vice versa. Finally, it calculates many important gear geometry characteristics i.e. roll and polar angles, roll length, pressure angle, tooth/space thickness and more for normal, transverse, and axial planes at any gear diameter.
www.gearoffice.com
Walter Surface Technologies Acquires Allegro Industries
In its quest to become a global leader for safety and productivity, Walter Surface Technologies is pleased to announce the acquisition of Allegro Industries, a USA-based leading manufacturer of high-quality safety equipment, respirators, air sources and ventilation equipment.
Through this acquisition, Walter is expanding its safety and PPE product offering to industrial users complementing its high-end metalworking products.
“We are very excited to welcome Allegro to the Walter family. Walter is always looking to provide solutions that answer the needs and challenges facing industrial end-users. Now, with this acquisition, Allegro brings the product and manufacturing expertise that will allow us to continue our mission to help our customers work better all while keeping them safe,” said Marc-André Aubé, CEO of Walter. “This transaction is an unequalled opportunity to build up our activities in the North American market as we continue to evaluate other growth strategies, namely through accretive acquisitions,” he added.
Tom Johnston, president and founder of Allegro Industries welcomes the new relationship: “We are proud to see Allegro adding its solutions to Walter’s renowned offering. The fit is right, and we look forward to Allegro’s potential within the Walter group of companies.” He adds, “We are very excited to be a part of the Walter team.”
Following this transaction, Allegro will continue to operate under its own brand. The transaction is effective immediately, and activities for both customers and suppliers remain unchanged.
www.walter.com
Forest City Gear’s Wendy Young named business catalyst of the year
Wendy YoungForest City Gear is proud to congratulate Wendy Young, President and CEO, for being named the 2021 Individual Business Catalyst of the Year by the Rockford Chamber of Commerce.
Young began her career at Forest City Gear in 1983 as a delivery driver, machine operator and expediter. Young has been part of Forest City Gear’s leadership team for over 20 years, during which time she has helped drive significant growth and expansion. Young currently serves as president (since 2002) and CEO (since 2015).
According to the Rockford Chamber of Commerce, Young’s nominator had this to say, “Wendy’s energy and dedication to her family, business, and community are second to none. Wendy is in constant pursuit to help those in need and less fortunate. Over the years I have personally observed Wendy’s business acumen at work as she has led a world class, precision Gear Manufacturing Company through many difficult periods. Wendy often is found mentoring and assisting associates through hardships they were experiencing that was totally unrelated to work and business. Wendy’s spirit, drive and compassion for excellence has been instilled in her family and is felt and noticed by those who know her.”
www.forestcitygear.com
KISSsoft Announces Training Schedule Through Summer 2022
The KISSsoft training program 2022 in English offers introductory training courses, advanced training courses and special training courses on selected topics. This year, KISSsoft will again be offering live streams, which will allow attendees flexibility and planning security, as well as the opportunity to interactively ask questions and participate in discussions in a virtual setting.
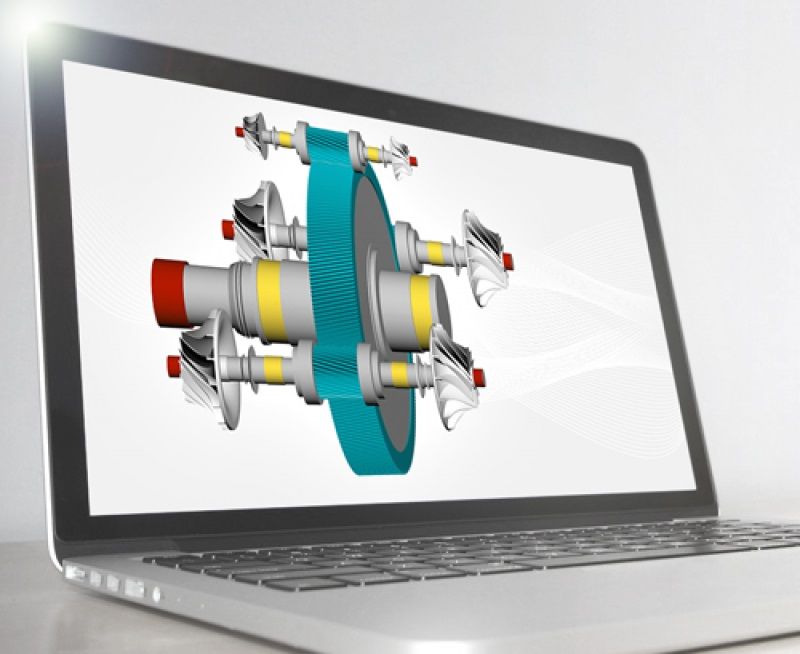
March 1–2
Shaft and Bearing Calculation (Basis)
March 22–24
KISSsys - Modeling Gearboxes (Basis)
March 29–30
KISSsys - System Calculations (Advanced)
March 31
KISSsys - Model Customization (Special)
May 9–12
Fine Pitch Gears in Plastic and Sintered Material (Special)
June 21–23 / June 28–30
Cylindrical Gear Design, Analysis and Optimization (Advanced)
www.kisssoft.com/en/products/training/upcoming-seminars