Today’s demands also include clamping very thin parts for the robotic gearboxes (flex spline gearbox). Mytec Hydraclamp clamping tools are designed to clamp components the entire length of the clamping area. If the component is irregularly shaped, we clamp around it to achieve the highest accuracy. The company designed a hydraulic chuck in combination with a changeable back stop and slotted collet. This gives the customer options to clamp different diameters and components with one hydraulic chuck. This hydraulic chuck is used to machine the spline in the “gear shaping” process on a Liebherr machine.
Easier Internal and External Spline Inspection
Frenco GmbH has introduced a new horizontal slide option for the inspection of internal and external splines with AVM and IVM gaging systems. Advantages of this new development are the easier handling of long workpiece shafts through adjustable V-blocks with longitudinal travel; and repeatability for MdK averages of ≤ 1.3 μm.
eurotechcorp.com
GF Machining Solutions—#338376 (South Building)
GF Machining Solutions will highlight advances in EDM technology, service, support, automation, and tooling designed to help shops power through their unique manufacturing challenges with complete solutions and holistic support. Plus, System 3R will highlight tooling solutions to reduce setup time and automation solutions to maximize machining hours.
For customer growth and success, these integrated problem-solving solutions include the new CUT X 500 and CUT P 350 Pro wire cutting EDM machines for precision part generation. To maximize machine-tool value and competitive readiness, the company’s new Success Packs feature comprehensive customer support as well as digital services that add connectivity for remote machine monitoring and troubleshooting from GF Machining Solutions experts. Rounding out the lineup of live demonstrations will be an automated cell featuring a MILL 400 U and FORM P 350 with a FANUC Robot. There will also be a System 3R WorkPartner 1+ modular pallet system connected to a GF Machining Solutions LASER P 400 U laser texturing machine.
With Intelligent Power Generator (IPG) technology, the CUT P 350 Pro delivers surface finishes as smooth as Ra 0.08 µm and heightens accuracy with integrated thermal regulation that maintains temperature at ± 0.2°C. To accommodate heavy workpieces, the machine’s QUADRAX mechanical system keeps the table, work tank and dielectric liquid stable.
Capitalizing on more than a century of EDM technology, the CUT P 350 Pro and CUT X 500’s new Uniqua human/machine interface (HMI) delivers optimal functionality and ergonomics in a 19" vertical touchscreen, full keyboard, and mouse. Abundant automation options add to the machine’s scalable flexibility, with optimized production for electronics, automotive, medical and mold and die manufacturers through more than 600 pre-programmed cutting processes.
The AgieCharmilles CUT X series holds extreme accuracies in machining positioning and pitch. Developed to provide high precision and thermal stability in large runs of complex components, including stamping tools, multi-cavity molds and micro components, the CUT X 500 and all other CUT X machines feature adapted mechanical structures, dedicated machine calibration and testing to deliver pitch accuracy as low as 1.0 µm. High-precision axes, short measurement loops, dual measurement on all axes, consistent isolation of the EDM area from heat sources and submerged working areas optimize conditions for micro applications. Two-spool Automatic Wire Changer technology and an onboard Job Management System help further reduce processing time and simplify job prioritization.
gfms.com
Haimer—#431510 (West Building)
Today, Haimer, is doing a lot of research in milling, turning, and grinding tools, and their optimal use. Among other things, this is demonstrated by a complete range of grinding wheel adapters for tool grinding machines of for Vollmer, Walter, UWS Reinecker and Rollomatic.
Haimer also offers a wide range of suitable grinding wheel adapters for the innovative high-precision multi-task machines, which unite milling and turning, as well as grinding technology. These holders are available in HSK-63 spindle coupling as a monoblock version or in multi-part with one or four clamping screws. A corresponding offer is also available for the HSK-A100 and PSC 63 spindle interfaces.
In addition, Haimer supplies special customized grinding wheel adapters for clamping diameters from 56 mm to 280 mm which can be equipped with various efficient cooling options for the grinding wheels.
The latest innovation in the Haimer program is the high-precision clamping system for round shanks “High Precision Clamp Master” which can be used on many well-known cutting tool grinding machines with drawbar clamping. The flexible system is perfectly suitable for automated blank changing. It pays off quickly, especially for small batch sizes with automatic loading, as the machine is ready to grind again in a very short time.
The Haimer High Precision Clamp Master is characterized by the highest level of accuracy. The runout and wobble can be adjusted in the machine and the highest runout repeatability of
A core product in the Haimer portfolio since 1996 have been the Tool Dynamic balancing machines that compensate the unbalance from milling and turning tools, but also from grinding wheels. Even if balancing seems complicated at first glance, with Tool Dynamic machines it is easy to handle and affordable to everyone.
haimer-usa.com
Hainbuch—#431636 (West Building)
Hainbuch offers a mandrel with a hexagonal pyramid shape instead of a round taper, designed with stringent manufacturing requirements and process reliability called Maxxos.
Thanks to the hexagonal pyramid clamp, maximum torque transmission can be achieved. Up to 155 percent more transmissible torque and up to 57 percent higher bending stiffness compared to the classic Mando T211 mandrel. This makes it possible to achieve higher process parameters and consequently improve the yield of finished parts. Greater process reliability is facilitated by the spacious layout between the clamping bushing and the clamping pyramid. Even during the clamping process, this design prevents virtually any dirt getting onto the surfaces. This significantly cuts down the frequency of maintenance times for cleaning and lubrication. Overall, the mandrel has a clamping diameter range of 18 to 100 mm. The clamping areas of each size are designed to overlap. This has the advantage that users can choose from up to three mandrel sizes depending on the clamping diameter. The larger the mandrel is, the greater its stability and rigidity. Smaller mandrels may be able to handle more of the customers smaller workpieces. The aligned, segmented clamping bushings have a minimum concentricity of 0.01 mm and can even be supplied in a high precision version.
hainbuchamerica.com
Heidenhain Corporation—#135716 (East Building)
Heidenhain will feature the new TNC7 in North America. This standard-setting CNC control supports users from initial design to final machining, from one-off jobs to serial production, and from simple slots to complex contours. Its control platform lets machine manufacturers adapt the user interface to their machines and offers dynamic development potential for even greater functionality.
Along with easy and intuitive operation, users enjoy support from a virtual simulation of the machined part and work envelope. It will be the basis of future control generations from Heidenhain. The control features high-quality hardware components including a 24-inch full HD touchscreen monitor and an advanced, individually adaptable user interface. Its entire operating concept was redesigned from the ground up.
The interface of the TNC7 was designed to help users achieve the best possible result with maximum speed and convenience. Different machining tasks call for individualized work environments, which is why users can adapt their screen content through personal favorites, their own home menu for a faster start. And thanks to its fast-operating speed, the control reacts immediately to data input.
The TNC7 enhances familiar Klartext programming with smart functions and newly developed graphical programming. Users can draw contours directly on the touchscreen and convert them into dialog guided TNC Klartext programming code. Cycles and older contour programs can still be used, including already existing NC programs. A diverse package of functions, intelligent probing cycles, and graphical guidance for determining the position of clamping devices completes the next level of smart programming.
Not only will the TNC7 be on display at the IMTS Heidenhain Booth #135716 (East Hall), but also at the IMTS Student Summit Booth #215600 and Hermle USA Booth #339119 (South Hall) in action on its Hermle C250 High Performance line five-axis milling machine tool.
heidenhain.us
Jergens—#432154 (West Building)
Jergens announces its first preview of several new workholding products that will be on display and demonstrated at this year’s IMTS.
First among them will be additions to the company’s tooling columns made in the United States and constructed of single piece cast iron for maximum rigidity. These columns open horizontal machining potential and are a solid basis for custom workholding to suit specific customer needs. Several new styles include square, cross, and rectangular. Additionally, three mounting options are available—center pin, edge and ZPS—and the new columns are fully customizable.
A second new product introduction is Jergens new five-inch heavy duty machine vise. Made of stress relieved ductile iron and flame hardened, the new vise provides very long usable life and predictable performance. They are also more easily moved and relocated by the operator due to the relatively small size and weight, but also ensure secure part holding and tight tolerances from general machining to high production. Additions include hardened jaw plates and a Ball Lock fixture plate quick-change kit. The vise is also made in the United States.
A third development is with the company’s Quick-Loc pallet system (QL2). This will replace the existing product line and features an improved design that engages pull studs inside the receiver. QL2 has a hardened coating for long life and durability. The range is compatible with all existing top tooling. Quick Loc pallet systems are used for fixturing on horizontal, vertical, and rotary operations. These low-profile adapters and pallets ensure repeatability of 0.0003" and provide clamping forces of nearly 14,000 lbs.
Also included in these several expansions are two new ZPS installation choices for compact, light duty applications. SP140, the smallest clamping module on the market, and K02 pull studs utilize pneumatics and a mechanical spring in a small package. The combination offers quick-change solutions for vise or gripper jaws, electronic component manufacturing, packaging machines, medical technology, and automation.
Jergens also offers a washdown tool. This simple device provides 360 degrees of spray using coolant flow to reduce machine cleanup time after a cycle. The ball cleaner washes chips off exposed surfaces, cleaning the machine at scheduled intervals which helps support long machining cycles and lights out machining periods when no operator is present. The washdown tool goes into the tool changer just like any other tool.
The full range of Jergens core products—including Ball-Lock, ZPS, Quick-Loc, Fixture Pro, and OK-Vise—will be on display throughout the exhibit.
jergensinc.com
Jorgensen Conveyor and Filtration Solutions—#338164 (South Building)
Jorgensen Conveyor and Filtration Solutions will spotlight its new FlexFiltration line, including the company’s new Flex G Series of modular filtration systems. The cost-effective systems feature pre-engineered modules that ensure fast, easy, flexible filtration configurations and add value for virtually any application.
FlexFiltration systems efficiently remove fine chips and grinding sludge to achieve coolant clarity down to 10 microns or less. They are especially well suited for challenging applications with materials that range from cast iron, steel and aluminum to composites and plastics.
Pre-engineered base configurations and numerous options enable quick construction of FlexFiltration systems to meet specific coolant-flow requirements. Standard, low-profile and stainless-steel tanks make these systems ideal for machine tool OEMs and regular end users. Other modular options that complete a system include high-pressure pumps, auxiliary pumps, tramp oil skimmers, coolant chillers, heat exchangers, liquid level sensors, temperature sensors and the ability to control/interface with existing pumps and other equipment.
Jorgensen’s Flex G Series systems feature gravity media filters. The gravity media filtration option is the first one available in the FlexFiltration product line. Gravity filters are offered in 30, 60 and 90 gpm options and come standard with low media roll detection, no media alarm sensor and automatic roll advance. A variety of different disposable cloth medias are also available based on specific applications. Additional primary filtration options including bag filtration, cyclonic, and permanent media types will soon be offered.
jorgensenconveyors.com
LK Metrology—#135230 (East Building)
LK Metrology, Inc. will offer four different CMMs including: the LK ALTERA M SCANTEK 5 equipped with a Renishaw REVO-2 5-axis scanning system; the LK Multi-Sensor ALTERAC equipped with LK’s new blue line laser scanner and a new surface roughness probe; the new ALTO 6x5 Bench Top CMM; and finally, a new COORD 3 UNIVERSAL CMM with a TP200 touch probe. CMMs with PH20 and PH10 probes will also be on display.
LK will be launching an advanced version of their TouchDMIS software as well as demonstrating the newest version of their well-known CAMIO programming and measuring software. In addition, the new Industry 4 Metrology Gate, LK’s portal for remote inspection monitoring, will also be shown and demonstrated. Other CMM software like Renishaw Modus, Polyworks, and CMM Manager that are frequently used with LK Metrology CMMs will also be available for demonstration.
Related accessory products to be seen will include LK’s new SLK20 blue light line laser scanner; a new LK surface roughness probe; and a new LK FREEDOM V2 measuring arm with rotary indexing table.
lkmetrology.com
L. S. Starrett—#135044 (East Building)
The L.S. Starrett Company has enhanced its AVR300 Multi-Sensor Vision System with a large 2.36" (60 mm) FOV-dedicated 0.14x telecentric lens for micron-level resolution and accurate field-of-view (FOV) measurements. For greater efficiency and accuracy, more of the part can be viewed in every image on the new AVR-FOV 0.14X system. Due to “superimage” technology, which allows multiple images to be stitched together to form one larger image, together with the system’s touch probe technology, the AVR-FOV 0.14X can accurately inspect a wide range of features on large or complex parts, as well as on multiple small parts.
The AVR-FOV 0.14X automated part programs deliver accurate results to the micron level in a matter of seconds with “Go/ No-Go” tolerance zones, and data are provided in one easy-to-interpret report. These features allow metrology users in manufacturing facilities or QC labs to produce accurate, fast, and repeatable results.
“Building on the success of the AVR300 multi-sensor system, now customers can measure and inspect a wider range of parts, including those that are complex with intricate features,” said Mark Arenal, general manager, Starrett Metrology Division, “The interface on the AVR-FOV 0.14X is user friendly and intuitive so all users, including operators right on the shop floor, can complete the inspection process.”
Equipped with the M3 software package from MetLogix, a traditional mouse as well as a touchscreen monitor make user interaction easy and intuitive. Auto part recognition enables creating a part measurement program that comprises the desired features of a part for inspection, which can automatically be saved in the system or to a network. Programmable light output options can be built into the program as defined steps, including being called up as the part recognition program initiates. Once the program is created, placing that part within the camera’s field-of-view allows for the saved program to initiate and run the inspection. A Renishaw Touch Probe may also be utilized for quick acquisition of discreet points along a part’s profile as well as Z-axis measurements.
The AVR-FOV 0.14X has an X-Y-Z travel of 12" x 8" x 8" (300 mm x 200 mm x 200 mm). The Starrett AVR-FOV 0.14X Multi-Sensor Vision System is made in the United States.
starrett.com
Mazak Corporation—#338300 (South Building)
Among the 19 machines in the Mazak booth will be models from the company’s Ez, INTEGREX Multi-Tasking, new SYNCREX Swiss-Style and NEO Series in live real-world production demonstrations. Mazak also will feature automation systems, its MPower complete customer care program and Mazak Capital Equipment Financing (MCEF) for one-stop factory-direct financing.
Mazak’s Ez Series of machines puts Mazak reliability, accuracy, and performance into shops of every size. The Kentucky-built Ez Series includes turning centers and vertical machining centers with compact footprints and numerous options.
At IMTS, Mazak will feature the QT-Ez 8MY Multi-Tasking CNC Turning Center with an 8" chuck and integral-motor spindle that handles a wide range of materials, along with milling capability and Y-axis functionality for single-setup processing of diverse parts. In live demonstrations, the automation-ready QT-Ez 8MY will pair up with a cobot to spotlight flexibility and productivity in unattended machining.
Mazak INTEGREX Multi-Tasking machines transform complex part production with single-setup convenience and performance for advanced machining. They unify the processing power of multiple machine tools for Done in One efficiency that easily accommodates automation and unattended versatility. At IMTS, Mazak’s INTEGREX i-450H ST Multi-Tasking Center will show attendees how it delivers the combined processing power of a turning center and full-function machining center, with a second turning spindle and a lower turret with optional rotary tool capabilities to minimize fixtures, tools, handling and non-cut time.
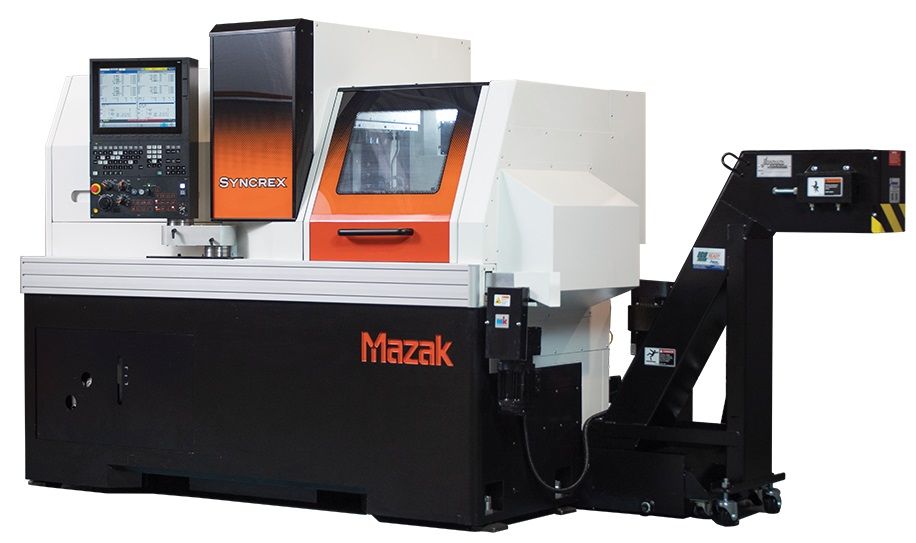
Mazak's new SYNCREX Series of Swiss-style machines come in four bar capacities ranging from 20-38 mm. The machines are available in seven, eight and nine-axis configurations. A nine-axis model with full B-axis contouring is also available. SYNCREX machines feature Mazak’s new MAZATROL SmoothSt CNC control that provides fast, easy job setups. Mazak Swiss Set-up Assist (MSSA) along with the Mazak Dynamic Chip Control (MDCC) features help reduce set-up times and part production.
mazakusa.com
Norton|Saint-Gobain Abrasives—#237042 (North Building)
Norton|Saint-Gobain Abrasives will offer a portfolio of gear grinding products specifically designed by category to provide higher profile accuracy, supreme form holding and burn-free grinding in worm, profile, and bevel applications. Highlighting the range is an innovative dual-worm wheel design that enables two operations in one grinding wheel, substantially saving time and cost.
“In today’s increasingly stringent industry requirements for higher accuracy and improved surface finishes, our high performance Xtrimium grinding wheels are engineered to deliver the highest quality gear grinding solutions” said Josh Fairley, product engineer, Norton | Saint-Gobain Abrasives.
Norton Xtrimium Dual-Worm Grinding Wheels feature a unique design with a high-performance vitrified bond section for grinding and a fine-grit resin section for polishing the gear teeth, enabling one wheel to perform what traditionally required two wheels. Substantial savings in wheel costs and productivity via the elimination of wheel swapping, can be achieved with the Norton design. In addition, improved surface finishes of Rz = 1.0 mm and Rpk = 0.05 mm, and reduced harmonics (noise) are realized. The Norton Xtrimium Dual-Worm Grinding wheels can also be adapted to existing machines.
The Norton Xtrimium Gear Grinding Platform also covers the whole range of gear grinding processes and leverages the whole spectrum of Norton grains and bond technologies to match each customer's requirements, whether with:
Worm Grinding Wheels featuring micro-structured ceramic grain and providing free cutting action and wheel homogeneity, allowing constant performance throughout the wheel thickness for the life of the wheel. Superior grinding rates and increased form holding without burn are achieved with these worm grinding wheels.
Profile Grinding Wheels which are ideal for deep profile gear grinding. The wheels feature high porosity and permeability, create exceptionally high material removal rates, and friction-free grinding.
Bevel Grinding Wheels featuring a highly porous bevel formation for extremely fast, burn-free cutting.
nortonabrasives.com
Rego-Fix—#431822 (West Building)
Rego-Fix will showcase innovations that extend the company's Swiss precision beyond toolholding. Featured technologies include the 3D-EdgeMaster measuring device and MasterBar test arbors—two new product entries for setup and test measurement. Other spotlighted innovations are expansions to the company's existing lines of internal coolant retrofit systems with additional flexibility for high-speed spindles and for turning centers along with the company’s new powRgrip CoolBore collets that offer peripheral cooling in a form-fitting tool grip, and powRgrip Sealed Cap Collets to protect tools from contaminants and dust.
To add Rego-Fix precision to setup measurements, ergonomic 3D-EdgeMaster centering devices shorten setup time and ensure part accuracy in an IP 67–compliant shockproof and splashproof design for demanding applications. Designed to set zero points, probe reference edges and workpieces, calibrate measuring paths, center machine axes and determine bore centers, these new devices feature repeating accuracy of ≤0.01 mm. 3D-EdgeMaster is available in metric and inch sizes and with short or long probes, all individually serial numbered, with fully traceable inspection and performance certification for demanding industries.
Shops can minimize spindle-damage risks and maximize process reliability with MasterBar test arbors, available with HSK, steep-taper ST, BT and CAT interfaces for correct machine tool setup and spindle precision with every use. Ground to the same exacting specifications as Rego-Fix toolholding products and supplied with full technical certification, these devices check spindle runout, spindle and arbor alignment, and arbor length to boost part quality, reduce scrap and recheck for changes in runout and parallelism after a crash.
Hi-Speed reCool (RCR-Hi) quickly and easily retrofits high-speed and high-frequency spindles up to 40,000 rpm for precise internal coolant delivery at 100 bar maximum pressure with emulsion and oil-based coolants. This patented solution makes full use of high-performance equipment, with a ceramic coating for reduced friction and support for ER(M) 11 and 16 sizes in 3–10 mm tool shank diameters.
Now turning centers can benefit from the increased productivity, longer tool life and greater chip-evacuation efficiency with the quick-installing internal coolant conversion of externally threaded reCool (RCR-AX) for internally threaded live tools. Designed for lathes up to 12,000 rpm, this solution supports 100 bar maximum pressure with emulsion or oil-based coolants and 3–20 mm tool shank diameters. A copper-like coating reduces friction for higher performance.
For the highest gripping force of any Rego-Fix coolant collets, form-fit powRgrip CoolBore Collets (PG-CB) deliver high-pressure peripheral coolant for optimized chip removal in medium to high-performance applications. These collets change out quickly with other powRgrip coolant collets and provide maximum coolant output pressure for PG 25 (including short collets) and PG 32.
Shops that machine ceramics, sintered carbide, graphite, glass and other complex materials can protect their tools from contaminating chips and dust particles with powRgrip Sealed Cap Collets (PG-SC). These quick-change collets provide ultra-low total system runout of ≤3 µm at 3 x D, with equally high vibration damping for long toolholder life and consistent performance. Also available with optional cooling channels, these completely closed heads and sealed caps are a must with today's demanding materials.
regousa.com
RINGSPANN—#431968 (West Building)
RINGSPANN has recently consolidated its position as an OEM supplier for machine tool manufacturers. Now the Germany company offers high-performance diaphragm and taper sleeve clamping systems that are specially tailored to the requirements of the skiving process to produce high-precision external and internal gears.
The diaphragm and taper sleeve clamping systems are particularly predestined for the internal gear cutting of thin-walled workpieces that must not deform under any circumstances during machining—for example weight optimized toothed rings for planetary gears. In this application, they replace conventional jaw chucks.
“Both versions of RINGSPANN’s skiving clamping systems are based on fundamental functional principles that have proven themselves in gearing technology over a number of years,” says Volker Schlautmann, head of the company’s Clamping Fixtures/Shaft-Hub-Connections customer team. Typical of their design is a relatively open construction, which enables rapid chip removal.
Characteristic of the diaphragm clamping systems are a short overall length and a very uniform application of the clamping forces on the workpiece. They also offer the possibility of clamping on the shortest clamping surfaces. The key features of the taper sleeve clamping systems, on the other hand, are the large clamping depth and an impressive degree of rigidity. In both cases, the frictional connection is made via workpiece encompassing clamping elements, which can be quickly and easily exchanged during changeover. RINGSPANN supplies both versions ready for use, balanced and, if required, with air system control.
ringspanncorp.com
Siemens—#133346 (East Building) and 433028 (West Building)
Siemens will present its hardware automation and software technology portfolio, highlighted by the first-ever, digital-native CNC platform, Sinumerik One, for machine tool applications. In addition, Siemens will present its solutions and services for the industrialization of additive manufacturing. In booths 133346 and 433028, the company will highlight how machine users can quickly and easily embark on their digitalization journeys—from part concept to design, digital twin to simulation, part and machine production, as well as total integration of these processes into the digital enterprise for job shops and production departments alike.
In the Controls and CAD-CAM pavilion, Siemens will demonstrate the end-to-end production and installation of a transmission housing and bracket for the eRod, an autonomous electric vehicle that will be in the booth for visitor inspection. The parts are made by additive and subtractive machining processes. At every stage of the part’s development, including machining, display kiosks will take visitors through the digital process. From the Siemens NX CAM design software, which enables the use of 3D models, data and processes to seamlessly connect planning and shopfloor operations on a digital thread to the Sinumerik One,the digital-native CNC that permits a digital twin of the machine and its full operation in production,Siemens has streamlined machine shop operations as well as leading automotive, aerospace, off-highway and medical part production facilities worldwide.
In the Additive pavilion, Siemens will demonstrate its CNC implementation into the additive and additive/subtractive production worlds, displaying part production processes from design to the finished part. Visitors can discuss their manufacturing challenges with Siemens to determine the optimum method of part design and manufacturing, whether one-off or full production runs, all performed with digitalization methods for validation and time/cost containment.
siemens.com/us/en.html
Unisig—#339159 (South Building)
Unisig will showcase the technologies that make it an industry leader in extreme depth-to-diameter hole drilling, including the ability to create holes with outstanding precision. The company’s UNE6 Series small-diameter gundrilling machines excel at drilling deep holes in demanding materials, including high-strength titanium and surgical-grade stainless steel, and achieve superior concentricity through tool and workpiece counter rotation.
At the show, Unisig will highlight medical production on the UNE6-2i that features two independent high-speed spindles for production of 10" or 30" maximum part lengths and available integrated automation onboard. The machine’s high accuracy allows it to drill hole diameters from 0.03–0.25" (0.8–6 mm) and depth-to-diameter ratios from 20:1 to more than 100:1 in workpieces up to 11 lb. (5 kg). With 28,000 rpm total drilling speed and a 3,000 psi (207 bar) flow-based coolant system, the UNE6-2i combines exceptional process control with an intuitive smart control interface.
Customers in industries that include aerospace, automotive, energy, firearms, hydraulics, defense, and oil and gas, as well as medical and moldmaking, can consult with application engineers and technical sales staff at IMTS to discuss optimization of applications including drilling and beyond.
unisig.com
Wintriss Controls Group—#135073
Wintriss Controls Group has announced it will be demonstrating new, advanced features in its ShopFloorConnect OEE and Data Collection Software at IMTS. The latest functionality in ShopFloorConnect gives manufacturers efficient and easy-to-use software for increased efficiency and reduced downtime, including when remote monitoring is required. The software can significantly increase manufacturing capacity and profitability by identifying and quantifying excessive production losses and bottlenecks.
Advanced ShopFloorConnect OEE and Data Collection Software collects downtime and production efficiency data from every machine, ranging from CNC machines to presses, fabricating machines and more, in all areas of discrete manufacturing. Data is displayed in real-time, and indispensable manufacturing reports are produced, including detailed OEE reports in a variety of formats. At IMTS, Wintriss will showcase the new ShopFloorConnect PM Tracker which enables users to track important machine preventative maintenance (PM) items by run hours or machine cycles, issues targeted alerts when an item requires PM, and tracks the maintenance work history for all machines.
ShopFloorConnect 6.0 also features a new Universal Interactive Application Program Interface (API) that enables users to quickly set up two-way data sharing with any ERP or MES software.
shopfloorconnect.com