Grand Prize Awards
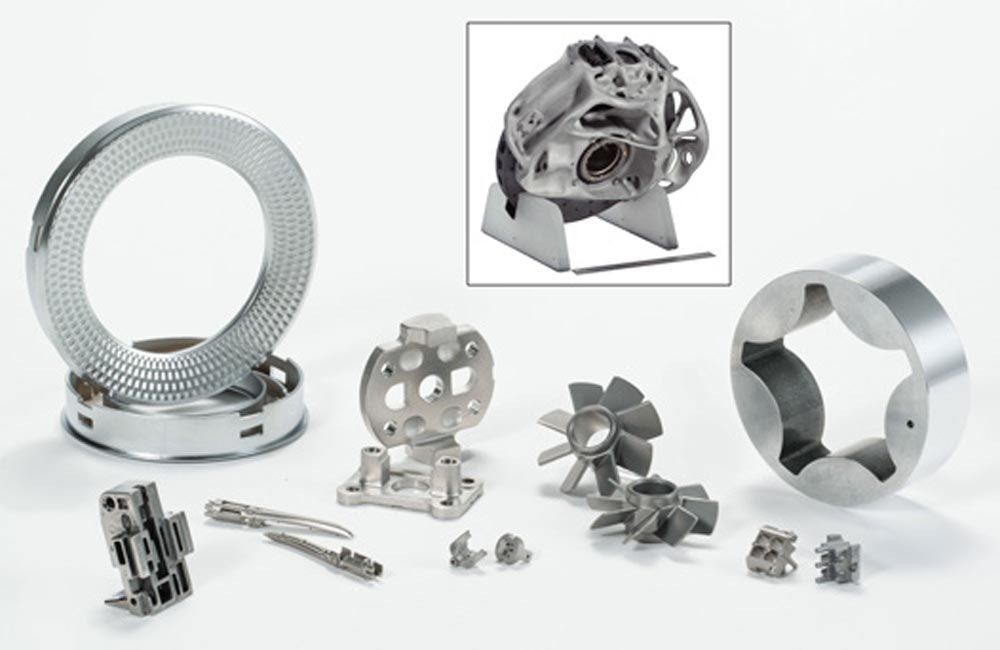
Group photo of Grand Prize Winners.
A Grand Prize in the Automotive—Engine Category for Conventional PM components has been awarded to GKN Sinter Metals and their customer Pierburg, for an aluminum metal-matrix composite outer gerotor for an Italian luxury sports car dry sump pump. It is the first aluminum gerotor used in a dual-material aluminum-steel pump gear for a production vehicle application. The inner profile of the gerotor for this high-performance application was critical for it to function in conjunction with a steel inner rotor with a different thermal expansion coefficient. The part provides a 50 percent reduction in rotating mass, which becomes even more significant with six gerotors per gang pump assembly.
A Grand Prize in the Automotive—Chassis Category for metal injection molded (MIM) components has been awarded to Kyerim Metal Co., Ltd, and customer Hyundai Motor Company, for a MIM-316L stainless steel rotary wheel used for selecting various internal functions in Hyundai-Kia Motors automobiles. The MIM part replaced an electroplated plastic rotary wheel and exhibits more than four-times the durability of the plastic part.
A Grand Prize in the Automotive—Chassis Category for Metal Additive Manufactured (AM) components has been awarded to Divergent Technologies, Inc. and their customer Czinger Vehicles, for a brake assembly chassis structure used in the Czinger 21C hypercar. The ultralightweight chassis structure is made by laser-beam powder-bed-fusion using a proprietary high performance aluminum alloy. Full vehicle validation was completed, and the component passed accelerated durability and proving ground abuse, dynamic stiffness, noise-vibration-hardness, as well as various Federal Motor Vehicle Safety Standards.
In the Aerospace/Military/Firearms Category for MIM components, a Grand Prize has been awarded to ARC Group Worldwide and their customer Palmetto State Armory, for a fire control housing that holds the trigger mechanism in a consumer pistol firearm. The fire control housing mounts into the frame of a pistol and supports various fire control mechanism components. The part facilitates the assembly of the firearm and supports the sear and blocker that are safety components.
In the Lawn & Garden/Off-Highway Category for MIM components, a Grand Prize has been awarded to INDO-MIM Pvt Ltd., for a rotor flow meter used in an agricultural sprayer made from MIM-17-4 PH stainless steel. The rotor is used to measure the flow rate of pesticide or fertilizer that passes through an extended boom on either side of a carrier while spraying a field. The rotors were previously machined. MIM processing was more cost-effective.
A Grand Prize has been awarded to INDO-MIM Pvt Ltd., in the Hand Tools/Recreation Category for MIM components for a quick-change core retaining anti-drill part used in a security door lock assembly. The complex part requires high strength and good wear resistance and is made from M2 tool steel. The cube-like structure has four, square through holes and across its center has three cylindrical projections—one at each edge and one in the center.
In the Medical/Dental Category for MIM components, a Grand Prize has been awarded to INDOMIM Pvt Ltd., for a stainless-steel curved jaw, part of an advanced bipolar device designed for use in open or laparoscopic tissue sealing surgical procedures.
In the Medical/Dental Category for AM components, a Grand Prize has been awarded to 3DEO Inc., for a MIM-17-4 PH stainless steel clevis, the primary component in a wristed end-effector assembly used in robotic minimal invasive surgery. The clevis interfaces with multiple components to enable controlled articulation of remote surgical tools inside the body. A hybrid AM approach is used to make the parts that offers the robustness and accuracy of CNC machining and the scalability of MIM.
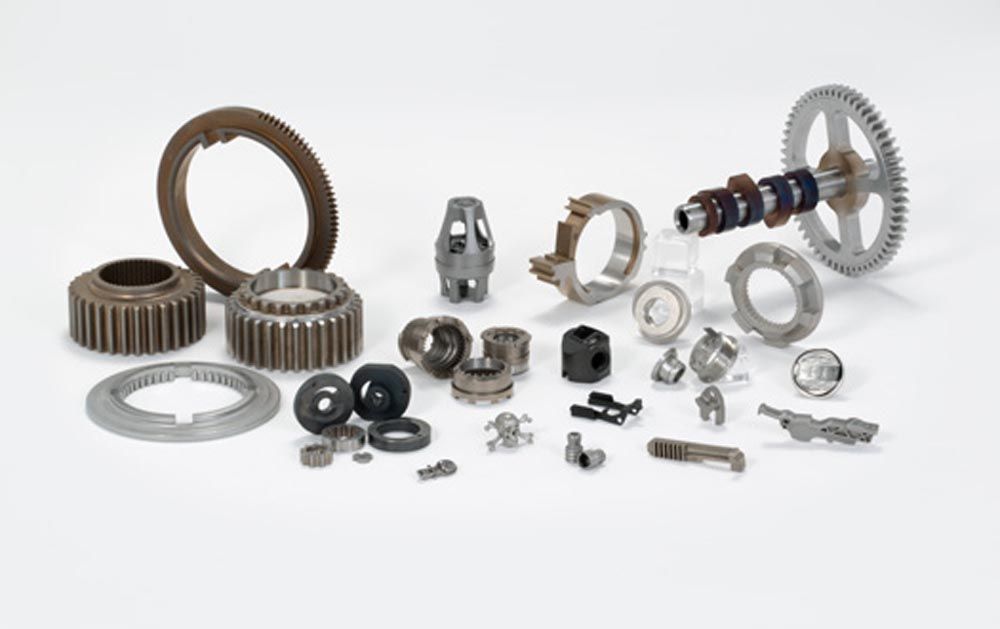
Group photo of Awards of Distinction.
In the Electronic/Electrical Components Category for MIM components, a Grand Prize has been awarded to ARC Group Worldwide, for a stator assembly, plate and frame used in small aerospace servo valves. Both parts are produced using two-cavity, three-plate injection molds. The stator assembly is part of a flux-carrying device that delivers magnet and coil flux to an armature. The assembly is used in servo valves for flight control actuation. MIM technology offered an opportunity to produce this assembly at a significantly reduced cost.
Awards of Distinction
In the Automotive—Engine Category for Conventional PM components, an Award of Distinction has been given to Nichols Portland LLC., a division of Nichols Portland Inc., for an eccentric ring used in a variable displacement oil pump. The sinter-hardened parts provide enhanced performance compared with prior generation designs that used steam-treated as-sintered parts.
In the Automotive—Engine Category for Conventional PM components, an Award of Distinction has also been given to DSB Technologies, LLC., formerly SSI Sintered Specialties LLC., and customer Purem by Eberspaecher, for a 309L stainless steel sensor boss that is welded to an automotive exhaust system and holds a sensor for monitoring engine performance.
In the Automotive—Engine Category for MIM components, an Award of Distinction has been given to INDO-MIM Pvt Ltd., for a vane lever that is used as a gas flow controller in the turbocharger of an internal combustion engine. The MIM part is made using HK30 austenitic stainless steel that has good oxidation resistance and strength at operating temperatures of 800–850ºC. The part was previously made by machining wrought bar stock.
In the Automotive—Transmission Category for Conventional PM components, an Award of Distinction has been given to Burgess-Norton Mfg. Co., for drive and driven sprockets, a pressure plate, and a sector gear, made for BorgWarner, and used in an automotive transfer case. The sprockets are warm-die compacted from FL-4405 with admixed nickel.
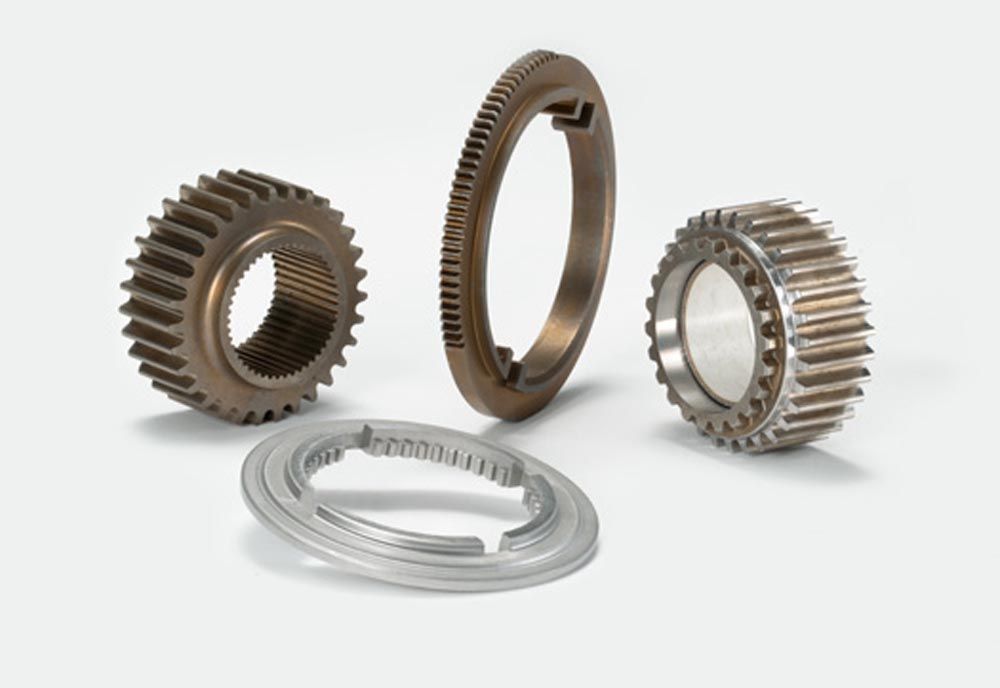
Drive and driven sprocket award winners.
In the Automotive—Chassis Category for Conventional PM components, an Award of Distinction has been given to Metalpó Indústria e Comércio Ltda. and their customer Haldex do Brasil Indústria e Comércio Ltda., for a rack used in a braking system for trucks. The rack is made from diffusion-alloyed FD-0405, warm-die compacted and case hardened to achieve good wear properties.
In the Automotive—Chassis Category for MIM components, an Award of Distinction has been given to INDO-MIM Pvt Ltd., for an upper cap, lower cap, split center, and split center bleed for a high-end automotive suspension system sub-assembly. The parts are made from MIM-4605 and heat treated.
In the Automotive—Chassis Category for Metal AM components, an Award of Distinction has been given to Azoth, for a shift knob emblem for General Motors Cadillac, Blackwing V-series cars. The part is made by binder jetting using a proprietary 316L stainless steel powder and binder. The part was designed with AM in mind. Other than surface polishing, there are no additional post-sintering operations performed.
In the Aerospace/Military/Firearms Category for MIM components, an Award of Distinction has been given to OptiMIM, a Form Technologies Company, and their customer Savage Arms Inc., for a MIM-4605 bolt end-cap for an SPR Impulse rifle. The bolt end-cap has a large, open structure shape with four side holes. It has comparatively thin walls in relation to its size.
In the Aerospace/Military/Firearms Category for MIM components, an Award of Distinction has also been given to Advanced Powder Products Inc., for a one-piece slide release for a firearm. The part is made from an air quenched and tempered S7 tool steel. The part was originally designed for stamping, but the complex geometry was too much of a challenge.
In the Lawn & Garden/Off-Highway Conventional PM components Category, an Award of Distinction has been given to Alpha Precision Group, a division of Nichols Portland Inc., for a camshaft assembly used in a family of engines ranging from 19–27 hp for consumer lawn & garden machines. The assembly comprises six PM components (a cam gear, four cam lobes, and a thrust washer). All five parts are assembled to the precision ground shaft by means of highly automated, specialized assembly cells.
In the Lawn & Garden/Off-Highway Conventional PM components Category, an Award of Distinction has also been given to FMS Corporation and their customer TEAM Industries, for a spider dampener insert, part of a torque spider sub-assembly for ATV transmissions. The part was originally designed as a metal casting that required secondary machining, but was redesigned for PM, eliminating the need for extensive machining operations.
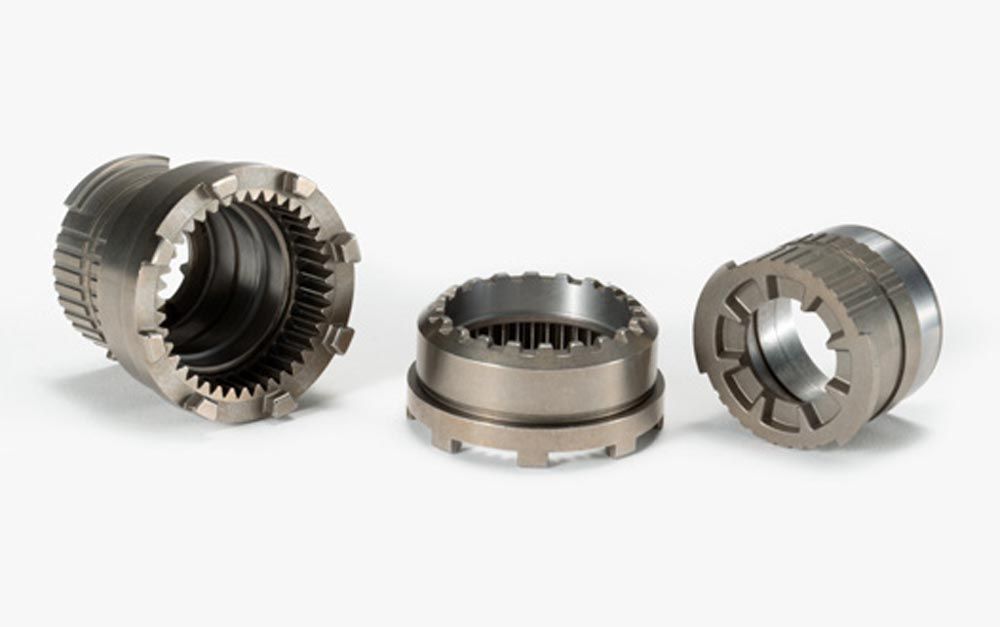
In the Hand Tools/Recreation Category for Conventional PM components, an Award of Distinction has been given to Porite Taiwan Co., Ltd., for a ring gear, used in the gearbox of a cordless drill. It is divided into two parts due to the multisection appearance. The two PM parts are machined, pressed for alignment, followed by a plastic injection overmold operation.
In the Hand Tools/Recreation Category for MIM components, an Award of Distinction has been given to ARC Group Worldwide, for a lock-arm button used in a pocketknife. When depressed, the button fires the blade open or allows the operator to close the cutting tool safely. The part is molded using MIM-420 stainless steel and is hot isostatically pressed after sintering.
In the Hand Tools/Recreation Category for Metal AM components, an Award of Distinction has been given to Amaero and their customer Sankuer Composite Technology, for a “skull” guitar tuner. The parts are made from Inconel 718 using laser-beam powder-bed-fusion processing. The ID of the inner keyway is sized to mate with the tuning machine peg without modification.
In the Industrial Motors/Controls & Hydraulics Category for Conventional PM components, an Award of Distinction has been given to Nichols Portland LLC., a division of Nichols Portland Inc., for a pump head sub-assembly for fluid delivery. The assembly comprises six PM parts, an inlet plate, eccentric ring, inner and outer gerotors, a spline coupling, and an outlet plate.
An Award of Distinction has been given to Indo-MIM Pvt. Ltd. in the Industrial Motors/Controls & Hydraulics Category for MIM components, for a control cone used as a fluid controller in a fuel pump. This is a highly complex part with a cylindrical stepped outer diameter that varies like a dovetail towards one end. The part was previously machined and producing the angular hole through difficult high-volume machining. MIM is far more suitable for high-volume production.
An Award of Distinction in the Industrial Motors/Controls & Hydraulics Category for MIM components has also been given to PTI (Polymer Technologies Inc.) and their customer Elevator Products Corporation (a division of Schindler Elevator Corp.), for an elevator button assembly that is impervious to solvents and disinfectants. These parts solved a problem encountered during the COVID-19 pandemic—elevator button assemblies machined from stainless steel and over-molded with polycarbonate threaded inserts were being degraded by various solvents and disinfectants used excessively to sterilize highly touched areas in elevators.
In the Medical/Dental Category for MIM components, an Award of Distinction has been given to ARC Group Worldwide, for a MIM 14-4PH impaction handle lever, a single-use instrument used in knee-replacement surgery. Tight profiles are maintained in relation to the distal end of the instrument to ensure proper engagement with mating parts. This impaction handle lever represents one of the first single-use instruments converted from plastic to metal injection molding.
mpif.org