The second-generation gear skiving machine is characterized by high rigidity (machine bed, flat guides, spindle rigidity), which means that longer tool holders can also be used. This enables collision-critical internal gears to be produced reliably and in high quality. The tailstock also makes the machine ideal for shaft machining. Chamfering is optimally integrated into the machine with the revised ChamferCut and FlexChamfer units.
Liebherr helps you individually select the gear-cutting tools. Intensive technology development and extensive tests at customers underpin the know-how of our experts. The specific tool development and production are carried out by Liebherr internally. Conical and cylindrical tools can be used.
Highlights
– Fast machining times
– High-performance spindle with internal cooling lubricant feed
– Integrated automation system
– Tool changer integrated in the machine
– Roughing and finishing tools
– Machining cluster gears in one workpiece clamping operation
– Simultaneous gear skiving and chamfering in one machine
– Process-optimized tool design and production
Digitalization Solutions
Customized digitalization solutions for your requirements
With a combination of data profiles, protocols, and the
LHWeb-Platform, Liebherr provides an infrastructure for the
acquisition, transmission, storage, processing, provision, and
display of machine, operating, and production data. In the basic
app LHMachine-Info, users can see the live status of their
machine tools at a glance and observe changes in real-time.
The LHSignalInfo app visualizes the recorded signals, taking into
account all measuring points and their exact time stamp.
The LHReportInfo app visualizes and analyzes the performance
of the machine and generates reports and evaluations from the
machine data—a decisive step toward more productivity.
Gear Cutting Tools
Holistic technological competence with Skiving3
The success of gear skiving lies in the significantly higher efficiency and productivity of this process compared with shaping
and the considerably higher flexibility and lower investment
compared with broaching.
Liebherr knows the entire process of gear skiving profoundly.
We have combined all of our expertise concerning tool design,
machines, and technology of gear skiving in the Skiving3 technology package. Very high accuracy in tool production, coupled with
optimal tool design, guarantees excellent gear quality and long
tool life. Liebherr guarantees the reliability of its manufacturing
process at the highest quality level.
The gear skiving tools are available in tapered and cylindrical form
and can be optionally manufactured from powder-metallurgical
high-speed steel (PM-HSS) or full carbide.
The combination of axial crossing angle, cutting speed, feeding,
and other kinematic parameters make the method very flexible:
Particularly for internal gears in medium batch sizes and external
gears with an interfering contour, gear skiving is an additional
“ace up your sleeve” in the gear cutting range.
Highlights
– Optimal tool design
– Best quality: High level of accuracy and long tool life
– Short delivery times and process support
Tools and Clamping Device Catalog
Immerse yourself in the world of efficient manufacturing with our
tool and clamping device catalog! In just a few clicks, our online
catalog gives you solutions that will optimize and accelerate
your production processes. From the SECLA clamping fixture or
our stock tools and hob arbors to the innovative CUTHOL tool
holder, we provide you with all you need in one convenient
location.
– Fast delivery times: We know how valuable your time is. This is
why we make sure that all products in our catalog are delivered
quickly, sparing you unnecessary delays in your production.
– Flexibility: Every manufacturing process is unique. Our catalog
offers you a wide variety of solutions that can be individually
adapted to your specific requirements, thus increasing your
productivity. If you don’t find what you’re looking for, we offer
customized product solutions.
– One-stop shopping: With our comprehensive catalog, you can
equip your entire operation and find any tool you require in one
convenient location. This not only means huge time savings but
also guarantees seamless integration in your production
processes.
Measuring Machine WGT 400
Are you looking for a solution to ensure quality and increase
productivity in gear manufacturing?
The four-axis measuring instruments of the WGT series have
high-precision mechanics and electronics, which are controlled by
smart and user-friendly software. They meet all accuracy requirements regarding gear measurement and comply with VDI guideline
VDI/VDE 2613, group 1.
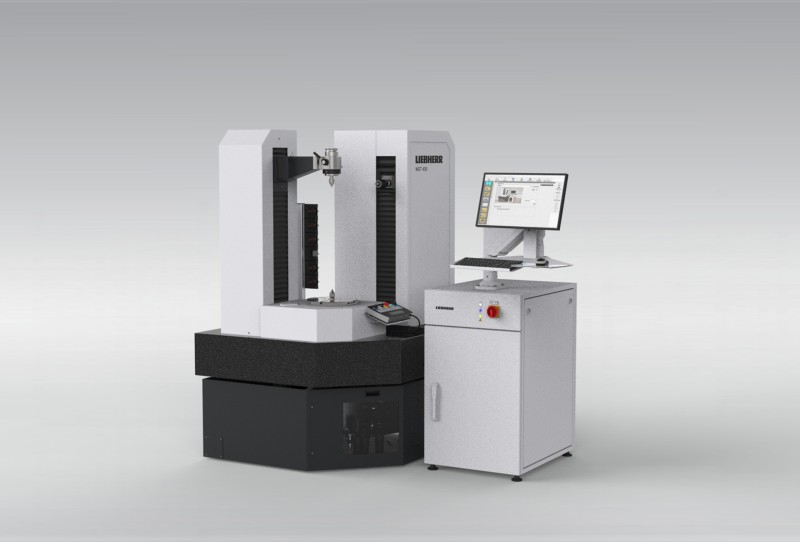
In addition to the gear inspection machine options available as
standard, customer-specific solutions are also available, such as adjusting the travel range on the Z-axis, longer tailstocks to accommodate long shafts, and rotary tables adapted to the payload. An automatic sensor changing system ensures uninterrupted measurement
of the workpieces and also offers the highest levels of convenience
for the user.
The extensive software features make the machines suitable for
measuring all types of gears, such as spur gears, bevel gears,
worms, worm gears, shafts, gear-cutting tools, and other rotationally
symmetrical parts.
Highlights
– Highest precision provided by granite guides and air cushioning
– Low operating costs due to contactless guides and reliable
probes as well as inexpensive spare parts
– Flexible for all types of gears
– User-friendly interface and ergonomic design
– Manufacturer-neutral GDE interface for data transmission
to production machines
– Highest precision provided by the new roughness sensor
PHS Allround Pallet Handling System
Automation system for machine tools from batch size 1
The Liebherr PHS Allround pallet handling system typically interlinks up to four machines and increases productivity—just like all
Liebherr pallet handling systems.
The modular system can be individually configured and expanded
at any time if required. The possibility of the frontal arrangement
of machines, additional units, and shelves offers maximum flexibility in the system design.
Innovative options such as the double loader and front access set
new standards in this product segment. The front access allows
individual machines to be decoupled from the system, while the
remaining machines continue to produce without restriction in
Automatic Mode.
The double loader reduces the time needed for a workpiece
change and thus maximizes its productivity—or it increases its
flexibility by using different pick-up forks for different pallet sizes.
Highlights
– Double loaders as a more cost-effective alternative to machine
trains with pallet changers
– Integration of different machine sizes in one system
– Three sizes for transport loads from 800 to 3,000 kg
– Very narrow telescopic unit combined with large stroke allows
any machine to be loaded
– Can be combined with additional technologies such as
automated setup and tool handling systems for even more
productivity
Bin Picking Solutions with LHRobotics.Vision
From the technology package to the turnkey robot cell
Liebherr supplies automation systems for automated raw parts
input and finished parts removal in production facilities and possesses extensive system and software competence for position
and object recognition with 2D and 3D camera systems.
With the LHRobotics.Vision technology package, Liebherr is making
this industrial application expertise available to a broad range of
users of robot integrations, to withdraw unsorted components from
deep bins with process reliability. As a manufacturer of bin-picking robot cells, Liebherr knows the challenges of the application and,
with the aid of artificial intelligence has simplified the software so
much that it can be intuitively used by anyone.
The technology packages consist of a 3D image recognition system
and the LHRobotics.Vision software for object identification and
selection, collision-free withdrawal of parts, and robot path planning up to the depositing point.
A special feature is the optional simulation tool LHRobotics.Vision
Sim. This enables the user to test and optimize the processes in a
completely virtual manner, without expensive hardware investment.
Highlights
– LHRobotics.Vision
– Software for object identification and
collision-free withdrawal of parts
– Open sensor and robot interface: a single bin-picking software
for all applications
– LHRobotics.Vision Sim
– Virtually simulate bin picking
– Available as a software package or turnkey robot cell
– Version with artificial intelligence for optimum part detection
E-Mobility—Battery Pack Assembly
Turnkey systems for automated assembly
of battery packs for electric vehicles.
With many years of experience in automated large-scale
production in the automotive sector, Liebherr can draw on proven
expertise.
As a specialist in heavy-duty automation, Liebherr offers a modular product system that is ideally suited for battery pack assembly. Conveyor systems, linear gantries, industrial robots, storage
solutions, intralogistics concepts, and process stations can be
individually combined to form a complete system. The degree
of automation, cycle times, and productivity are adapted to the
specific customer requirements.
The holistic approach encompasses standardization of interfaces
and integration of sub-suppliers, consideration of parallel processes, implementation of emergency and failure strategies, as
well as guaranteeing parts availability and traceability. Liebherr
offers comprehensive and flexible project management as a
general contractor.
Our services range from flexible small batch to fully automated
large-scale production.
—Transport: first-class machine and plant-linking solutions
—Assembly: reliable dispensing, screwing, and assembly
processes
—Inspection: leak testing, electrical testing, process
monitoring
liebherr.com