As anticipated, this is performed starting from the minimum project thickness: following incremental steps this thickness will be gradually increased until reaching the minimum safety factors required by the designer.
The verification performed in such places is referred to as bending SF and pitting SH; there is nothing to prevent extending expectations based on the application. It is noteworthy that as the face width increases, the face load factor KHβ factor worsens because it worsens the contact footprint: this phenomenon is considered according to ISO 6336-1 (Ref. 9), changing the load-increasing coefficients.
The code finds the gear’s face width that allows the minimum requirements for safety.
At this point begins the performance check: the boundary conditions have been modified where it is wanted to verify the friction losses.
The contact analysis is launched, according to Ref. 10 and 11. It is also possible to launch different boundary conditions to have an efficiency curve. In this study, the friction coefficients are used according to Niemann (Ref. 12); finished the calculation loop the results are stored moving to the next configuration.
The calculation time is minimal: just a few seconds for each configuration; for this reason, it is possible to explore a very high number of technical solutions, not precluding the analysis of any solution.
Discussion
Below is a case of practical analysis, where the procedure previously exposed is tested.
First, the definition of the combinations is given:
z ring
|
z planet
|
module |
num. planets
|
z sun
|
min |
max |
min |
max |
min |
step |
max |
min |
max |
min |
40 |
150 |
18 |
51 |
1 |
0.5 |
6 |
2 |
3 |
17 |
Table 1—Combination input values.
According to the choice shown, there are 71,807 possible combinations, following the above-mentioned procedure.
Recall that no other parameters have been changed in this context, which could strictly be modified by the user depending on the objectives: simply could be modified the combined calculation of the possible variations of input data to generate other case studies. Note that no changes in pressure angle were analyzed in this paper, variations in coefficient of teeth (addendum, dedendum, and root range), lubricant oil, and geometric tolerances: however, also these new variables can be added to the calculation loop without any kind of problem.
Below are the geometric and/or design parameters that have been imposed by choice, and not cycled within the code:
pressure angle |
quality ISO | ref. profile | micro geometry |
tip diameter allowed |
root diameter allowed |
x lim sun |
step for center distance |
face width |
SF min |
SH min |
[°] |
[-] |
[-] |
[-] |
[mm] |
[mm] |
[-] |
[mm] |
[mm] |
[-] |
[-] |
20 |
8 |
A |
NO |
0/-0.2 |
0/-0.5 |
0.2 |
0.05 |
10/30 |
1.50 |
1.20 |
Table 2—Frozen values by user choice.
Concerning operating conditions, where to perform the calculations is below:
power | speed @resistance | speed @performance | required life | amplification factors |
[kW] | [rpm] | [rpm] | [h] | [-] |
10 | 2000 | 5000 | 1000 | 1 |
Table 3—Operational conditions for checks.
Generated the file with all possible combinations, and the study was carried out.
The outputs that are saved for each combination are different, such as geometry—strength (SH and SF) and performance—losses—info.
Formulas to calculate SH and SF are according to ISO 6336-2, published in 2019. It used method B (analytical approach) for calculation factors.
Formulas for gear geometry are according to ISO 21771 groups.
Gear power losses load dependent PVZP are calculated according to ISO/TR 14179-2, i.e., following the Niemann (Ref. 12):
(1)
where:
Fn is the tooth normal force
μ is the friction coefficient
vg is the sliding speed
Each studied solution must respect geometric constraints; some of them—which if not respected do not allow defining a close geometry—are given below; the user can change them accordingly with his knowledge:
- minimum distance between 2 planets = 0.2 mm
- factor for minimum tooth thickness at tip = 0.2
- coefficient for minimum root gap = 0.2
- coefficient for minimum tip clearance = 0.15
- required transverse contact ratio = 2.0
- maximum permissible value for specific sliding = 3.0
- coefficient for tip clearance = 0.2
Paying attention to the 71,807 solutions proposed, only 2,088 have found a design solution (2.9 percent) and will be stored in the database results.
At this point to view the results it was necessary to develop a tool for analyzing the results that allows to view the relationship between the different variables: it can then be possible to identify the trend and focus on the parameters most important in the definition of the gear geometry specifications based on the target project.
A matrix plot visualization has been developed so that cross-correlations between variables can be displayed: it is easily possible to view the sizes of interest and in this way the results, through x-y canonical graphs. In addition, a series of filters and choices have been introduced, that allows both to underline the variables of interest and to analyze the findings of interest for a given range of variability of one or more variables. It is possible to create databases of design proposals in which to find the most suitable solution for a specific case. Most variables are chosen at the beginning of the study, the greater the database extension.
Before showing the results matrix plot developed in the paper, it is shown that the classic results display interface is used today in KISSsoft.
In Figure 1, there are two variables according to the two axes x-y (in the specific minimum root and flank safety factors), reporting a third parametric variable through color (transverse contact ratio in case). Each solution is recalled by a number.
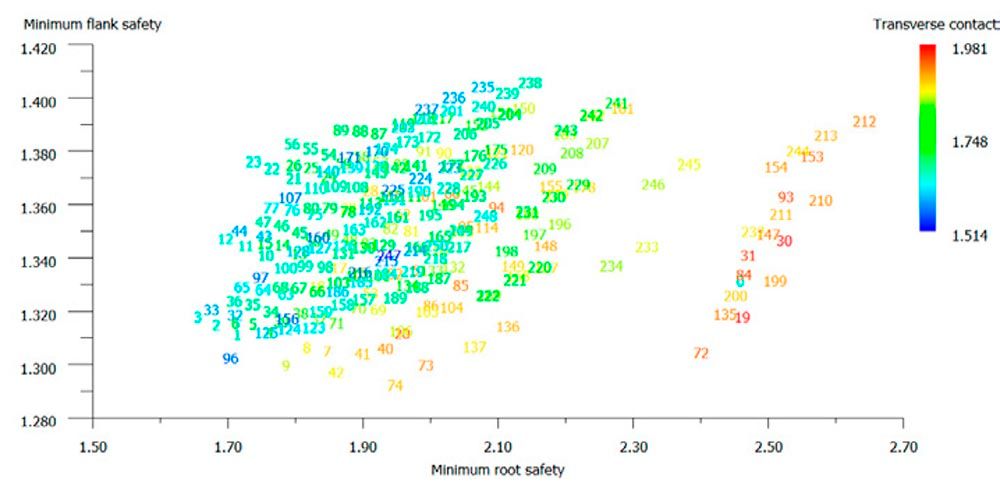
Figure 1—Typical output in commercial software (Ref. 11).
Although this display allows choosing the outputs of interest, focuses the maximum attention on three parameters at a time. Sometimes it is necessary to have more than three variables under control at the same time; with the display as shown in this example, it becomes necessary to change one of the three variables and plot the graph again, losing the previous info. Alternatively, you must save each image separately.
The proposal developed in this paper instead allows for displaying results at the same time. It is possible to choose the number of appropriate variables and get cross-related in between all parameters simultaneously. It is possible to identify possible design trends with project objectives.
The results obtained are not understood as a process of direct optimization, but as a tool to help the designer identify the solution that best meets the design needs.
To better clarify the reading, the results are reported with gradually increased variables.
In Figure 2, the correlations between SH and SF are reported, adopting the module as a parametric. The use of the fictitious variable of the case study “case” allows having under control the number of the simulation to which reference is made.
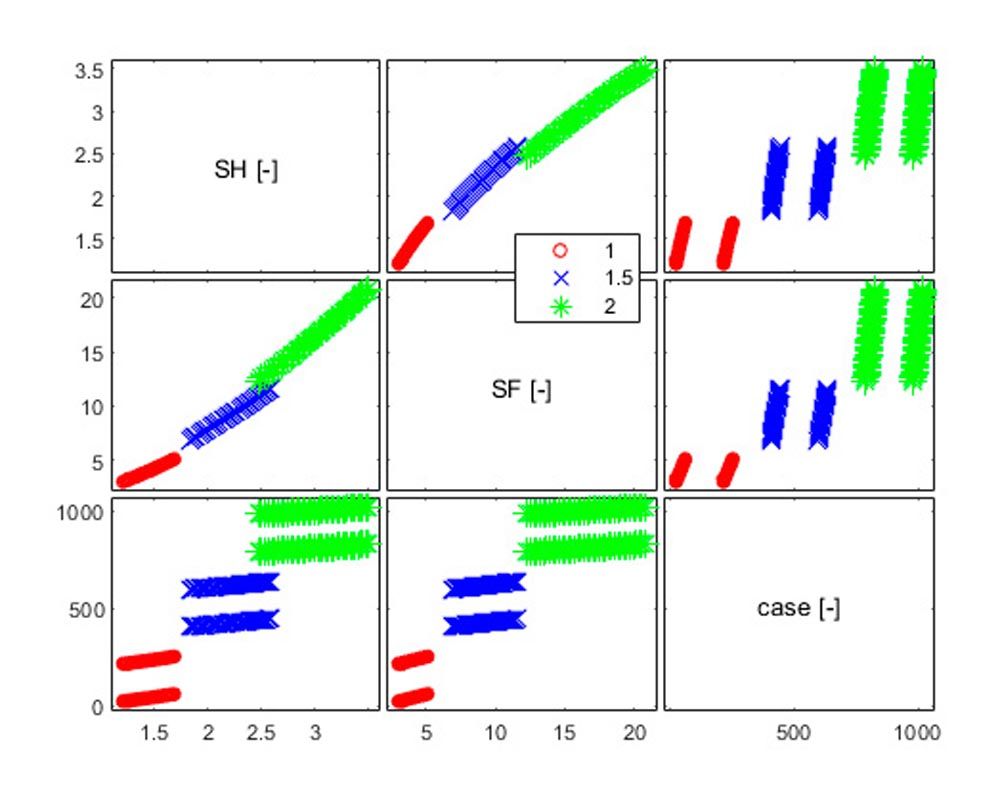
Figure 2—Matrix plot parametrized by module.
It is then possible to increase variables in output, as well as the output ranges to consider.
Figure 3 shows 5 output results for each solution—not taking into account the fictitious variable “case”—and higher number of module parametrized (1.0:0.5:3.5) than Figure 2 (1.0:0.5:2.0) with only 2 output results, SH and SF. The results in the figure below are about transmission ratio, external diameter of the sun and type of dynamic response expected in the system.
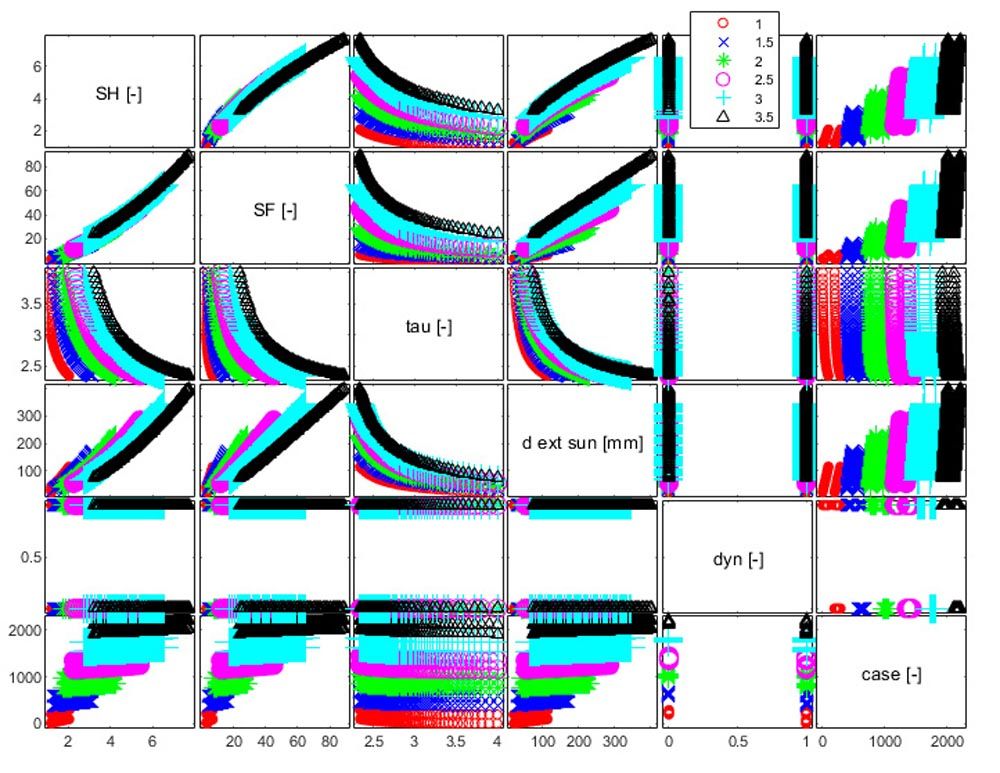
Figure 3—Matrix plot with six parameters.
It is evident how the user can manipulate it: the visualization here proposed allows finding any correlation trend between variables.
At the same time, it is possible to narrow the ranges as happened in Figure 4, restricting the transmission ratios to be displayed by x
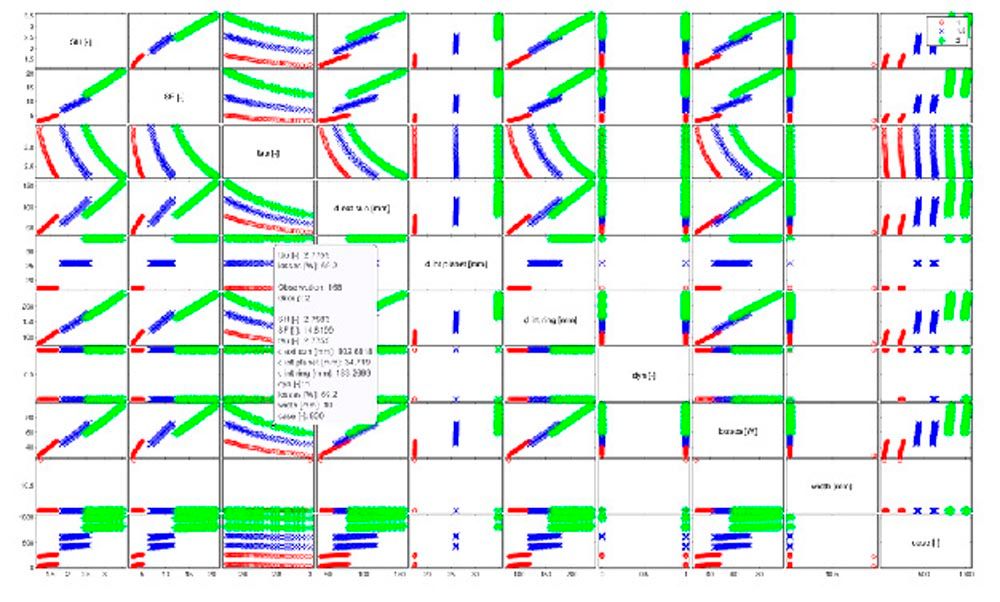
Figure 4—Matrix plot parametrized by module with constrained ranges.
With the procedure indicated, it is possible to store a large number of technical solutions, with an equal level of design accuracy from which to choose the most suitable for this application.
Thanks to this visualization it is easy to evaluate the losses synthetically and identify if there is some parameter driving the loss minimization logic, all while having under control all the design data of every single epicyclic gear train.
To understand the details that can be reached, the inner diameter of the planet and ring have been stored. They may be design limitations in the design phase when choosing such numerical values, to be written to the problems of:
- system dimensions, in the case of the ring diameter;
- support geometry of the planet carrier, in the case of the planet diameter.
In these, are directly available, the analysis of dynamic setting to define that the system is dynamically driven by a kind of forcing instead of another, symmetric or sequential mesh sequence. It is so easy to change the boundary conditions to jump out from the matrix plot, to visualize better the results based on the target. In Figures 3 and 4 the same results shown before are divided by the kinematic forces, in the case 1 instead of 0 for sequential and symmetric solutions respectively.
Moreover, the designer once again chooses the number of constraints. For example, a specific range of transmission ratio can be simply isolated simultaneously also building the type of dynamic response (1 instead of 0), and the root diameter of the ring teeth (
It is possible to parametrize the results based on what the designer wants to see.
The intention is to show how results can be easily shown, focusing on the designer’s interest.
Such charts are to be understood as project maps to help the designer allow the wisest choice of the transmission system to have under control the greatest number of variables.
Future Work
There are therefore many developments that it would be possible to think about.
Firstly, the automation of the entire process analyzed in this paper could allow the development of a user-friendly black-box package, easy to use for the designer.
Secondly the parametrization of system stiffness, on a geometric basis, allows for calculating the dynamic response of the system; it is in this way to identify which of the forcing dynamics of the system satisfy the designer’s choice (Ref. 5).
The same calculation has already been implemented for the calculations of external gears: joining the two works would allow to extend the analyses also for complex transmission systems. Complex systems could also be considered for a multistage epicyclic gear system.
Conclusion
This paper shows a methodology to extensively evaluate different designs of epicyclic gear systems.
As outlined, no choice is required on the part of the designer who is free to probe all design variables.
The study was divided into different steps well defined:
- Selection of variables to be included in the study and the automatic generation of all mathematically possible combinations;
- Automatic design of each epicyclic system according to geometric constraints and minimum security requirements guaranteed;
- Results in visualizations according to filtering logic and results sampling.
Acknowledgments
The authors would like to thank KISSsoft and Gleason Corporation for the software used to develop the script described in this paper, Ing. Ivan Saltini for his constant support, and the University of Bologna for the access to bibliographic references.
References
- Turci, M. and Solimine, V. “Closed Loop for Gears: Some Case Studies.” Paper No. 22FTM11, AGMA Fall Technical Meeting, 2022.
- Matlab, Software User Manual.
- Pinnekamp, B. and Hider, M. and Beinstingel, A. “Specific Dynamic Behavior of Planetary Gears.” Paper No. 19FTM26, AGMA Fall Technical Meeting, 2019.
- Kahraman, A. “Gear Dynamics and Gear Noise Short Course,” March 21-24 2022. The Ohio State University.
- ANSI/AGMA 6123-C16, Design Manual for Enclosed Epicyclic Gear Drives.
- ISO 53:1998(E), Cylindrical gears for general and heavy engineering—Standard basic rack tooth profile.
- Kissling, U. “Use of duty cycles or measured torque-time data with AGMA ratings.” Paper No. 21FTM07, AGMA Fall Technical Meeting, 2021.
- Turci, M. “Design and Optimization of a Hybrid Vehicle Transmission.” Paper No. 18FTM06, AGMA Fall Technical Meeting, 2018.
- ISO 6336-1:2019, Calculation of load capacity of spur and helical gears — Part 1: Basic principles, introduction, and general influence factors.
- Weber C., Banaschek K.; FVA-Bericht 129 und 134, Elastische Formänderung der Zähne und der anschliessenden Teile der Radkörper von Zahnradgetrieben, FVA 1955.
- KISSsoft, Software User Manual, 2023.
- Niemann, G.,Winter, H. Maschinenelemente, Band 2, Berlin: Springer 1983.