cincinnatigearingsystems.com
Dontyne Systems
Booth #237227
The Gear Production Suite software for Dontyne Systems has a range of options to assist in the design and manufacture of gear components. The concept of the software is to provide a common platform for designers and manufacturers to improve production efficiency. The software can design gear systems and analyze them under operating conditions, then automatically calculate tool forms and confirm the accurate generation of workpieces by simulation of the intended production method. Potential problems can be detected at this stage and any changes that need to be implemented before machining. Machine processes such as hobbing, profile grinding, shaping, shaving, skiving, and honing as well as forming techniques such as sintering, forging and injection molding can be considered. Measurement data can be imported into the system to assess the accuracy of the surface and define any corrective action. Increasingly this is possible using devices on the shop floor for in-process control. The software has been in use for 20 years worldwide with major markets in the USA, Europe and Japan. Dontyne will be demonstrating integrated solutions of the design software machine tools and digital gauges for workbench and on-machine devices at IMTS 2024.
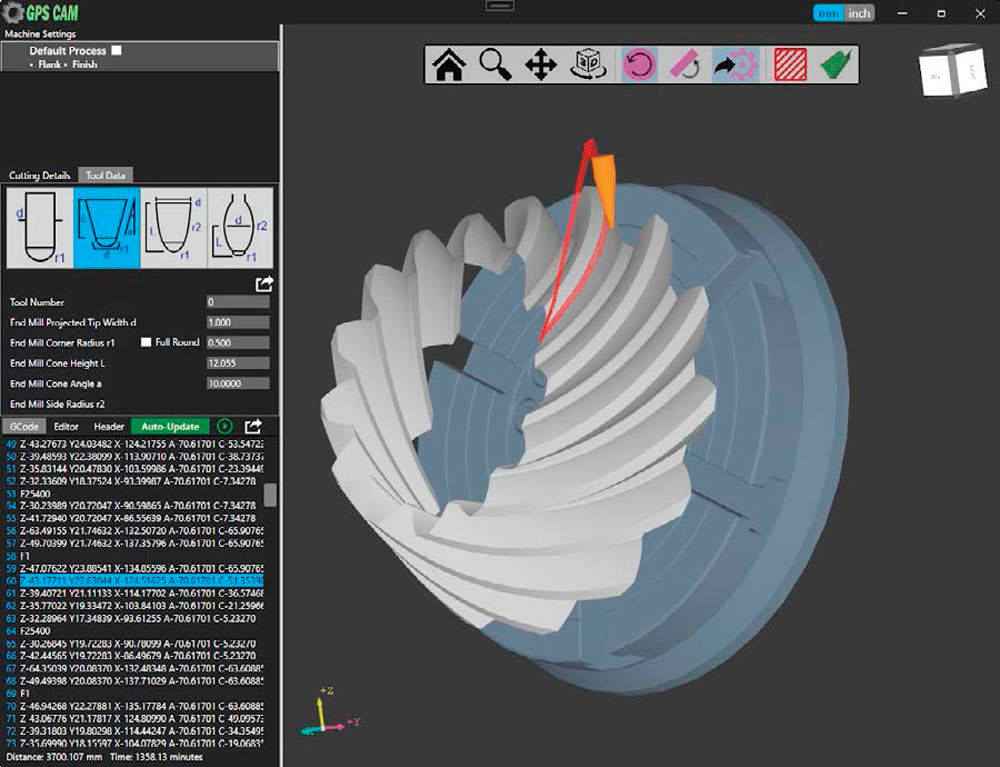

Recently Dontyne has added GPS CAM module to simulate production on 5-axis machines. The simulation can be for End Mill tools for small batches enabling versatile, economic manufacture for fast turnaround and fixed tools for larger batch sizes or faster machining times. The calculated surface points are converted to G-Code by the software based on tool selection. The process can be enhanced by using GPS inspection files which can be exported directly to gear checking machines or CMMs. Dontyne Gears was formed to support R&D projects and offer design and prototyping services to our clients. The workshop facilities can be used to validate GPS system by producing customer parts from project files on the machine tools both roughed and finished, and inspection on a range of devices depending on intended production levels. Once proven the approach is brought in-house by the client, facilitated by the GPS software. Aerospace, motorsport and luxury car sectors have been quick to take up this capability for complex bevel and hypoid forms, but the software has been applied to cylindrical gears too for the rapid development of new gearbox arrangements. Project work has seen the design and machining of gear pairs days rather than weeks to ISO Grade 5 or better, and surface finish well within aerospace tolerance levels. See the brochure on our website for details or visit the Dontyne booth at IMTS.
dontynesystems.com
DTR
Booth #237017
DTR manufactures a full line of gear-cutting tools—such as hobs and milling cutters—and provides new tool design solutions for a global market, serving customers in over 20 countries.
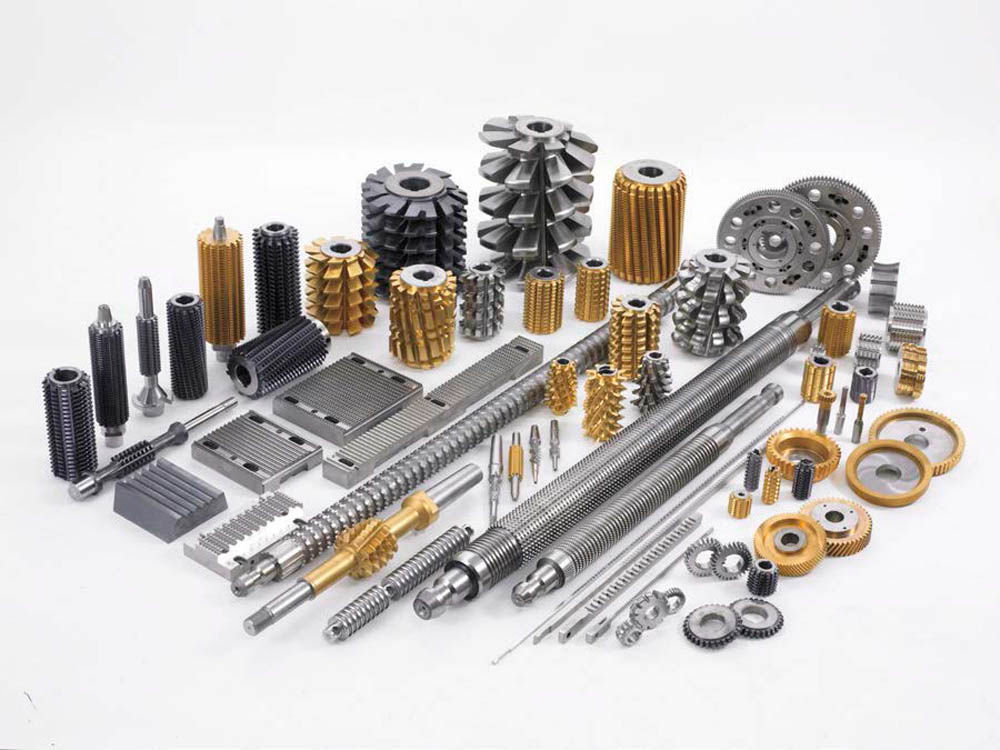

DTR adds value for customers with high-quality/performance tools, competitive pricing, fast/on-time delivery and technical support from expert technicians.
dtrtool.com
DVS Technology Group
Booth #236920
DVS and its subsidiaries will have experts on-site to present their latest, advanced solutions for metalworking and automation. Gear-specific competencies include skiving, chamfering/deburring, internal/external gear-cutting tools, grinding, honing, and more.
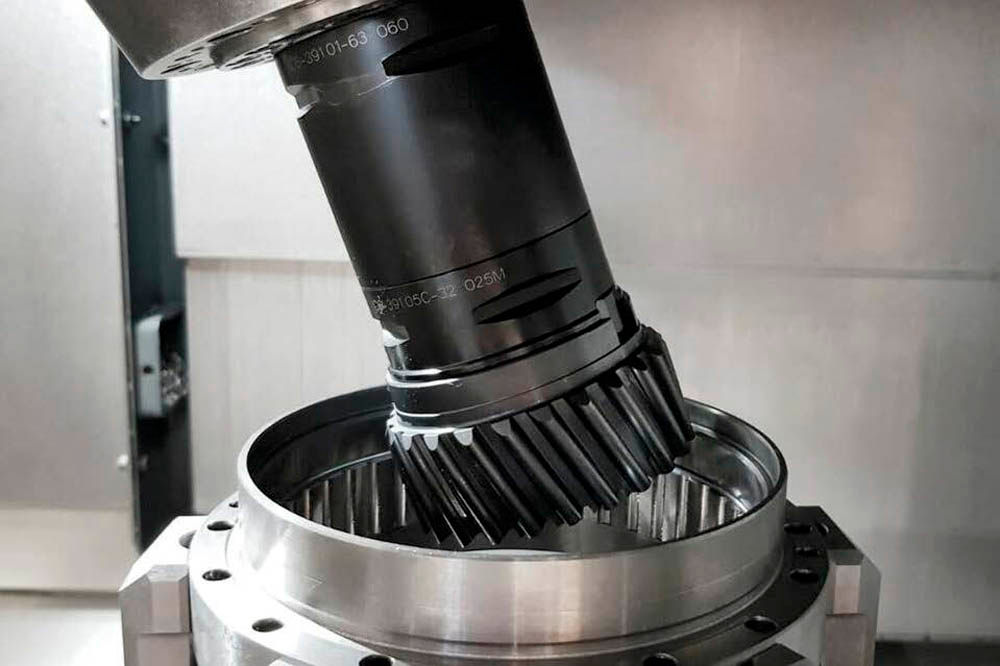

Visit DVS and discover their integrated and synergistic solutions for hard-finish machining, their solutions in the field of future technologies, and their tool and CNC machine program.
dvs-technology.com
EMAG
Booth #237047
Visit EMAG to learn more about its portfolio of automated machining solutions that make entire production processes quicker, less prone to error and more cost-effective. Whether needing to simply speed up production or add a “lights out” shift, EMAG has a tailor-made system to fit your unique components.
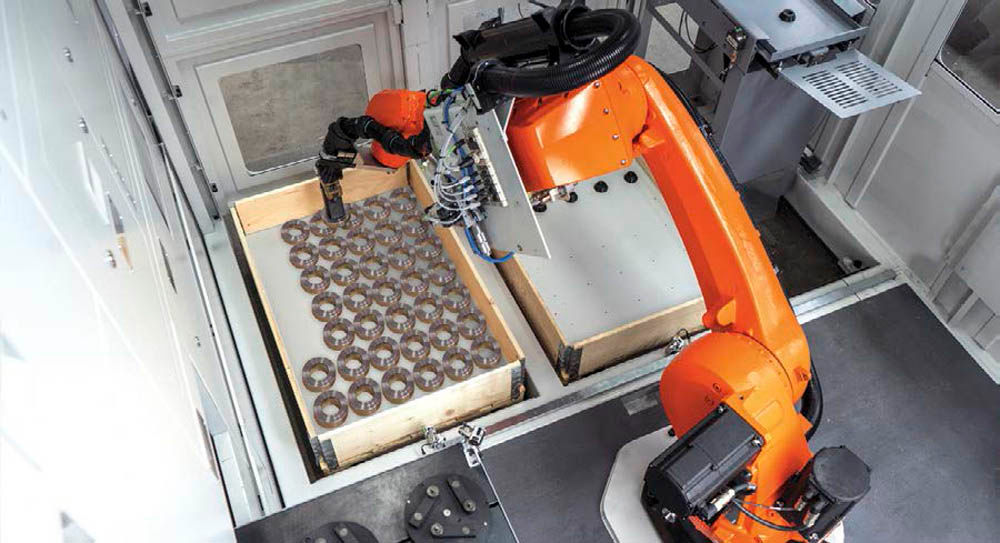

Featured technologies include VL 3 DUO Turning Machine with bin picking automation, WPG 7 Universal Cylindrical Grinding Machine for workpieces up to 250 mm, and the VT 4-4 Turning Centers for demanding shaft production.
emag.com
Federal Broach & Machine
Booth #237238
Federal Broach & Machine, a division of Nidec Machine Tool Corporation of Japan, will exhibit their Vertical Rising Table Broach Machine (VRT). The machine is capable of fully automatic broaching of internal spur splines. In addition, the companion Federal Broach tools will be available for show attendees to review.
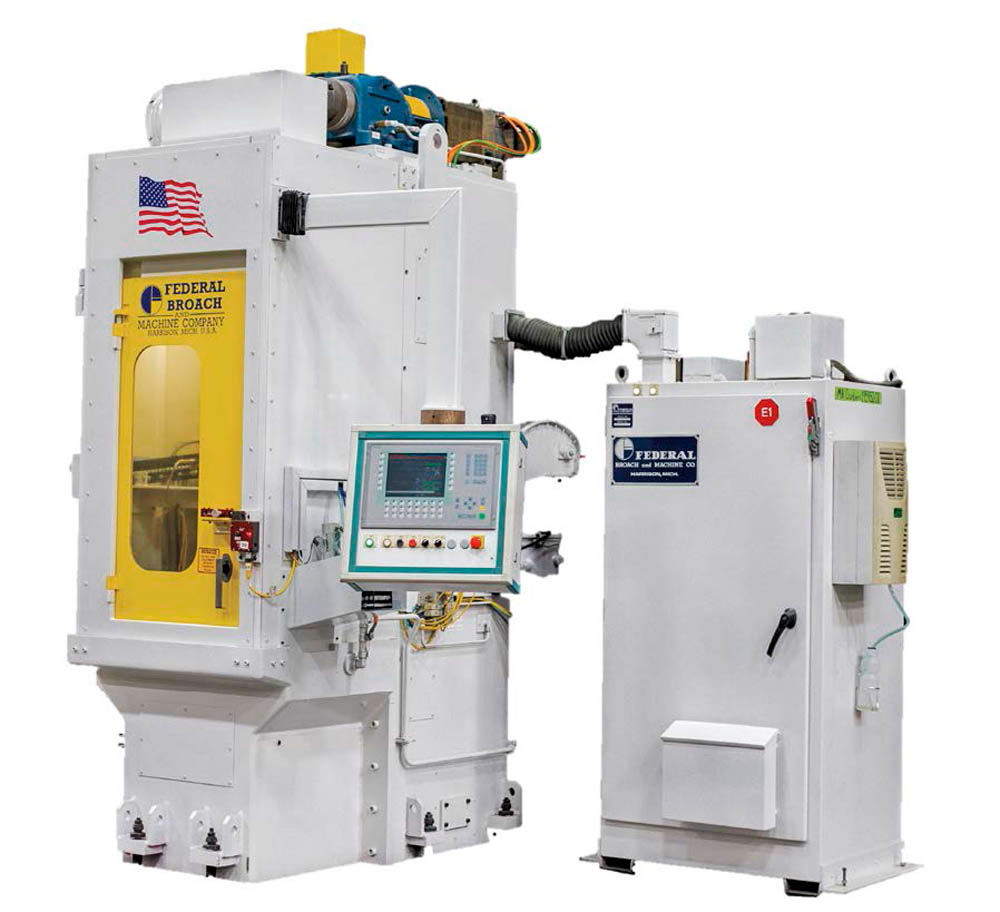

The machine can be built with five to 20 tons of force for a wide range of applications. Capable of hard broaching, the VRT has a small footprint and is suitable for mass production as well as job shop installations. According to Ken Kernen, President of Federal Broach, “The new Vertical Rising Table Broaching Machine is our newest and most flexible machine, and we are proud to be exhibiting if for the first time at IMTS 2024.” Kernen added, “The modular design allows the force, stroke, tool length, coolant type and CNC control type to be tailored to the exact needs of the customer.”
nidec-machinetoolsamerica.com
Gleason Corporation
Booth #236909
Gleason is a global leader in gear technology. Gleason’s “Total Gear Solutions” range from gear and transmission design software to the development and production of gear manufacturing machines and related accessories, gear metrology equipment and automation systems. Gleason products are used by customers in the automotive, commercial vehicle, aerospace, agricultural, mining, energy, construction, power tool, marine and many other industrial equipment markets.
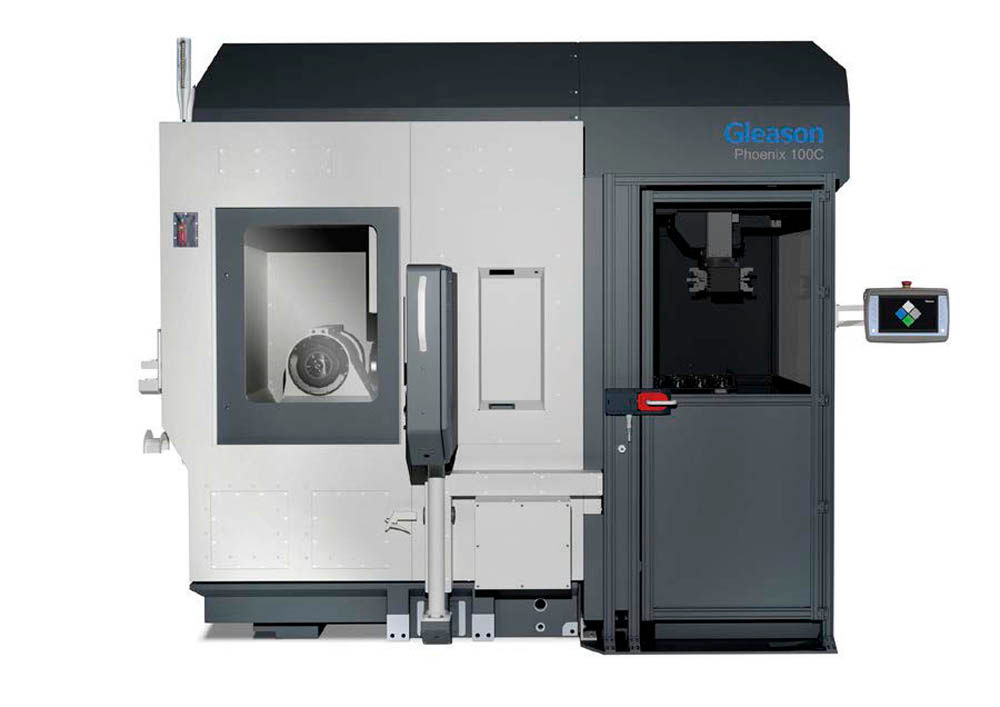

As gear industries advance, so does the need for unparalleled precision. Gleason’s Phoenix 100C Bevel Gear Cutting Machine has been designed to bring speed, flexibility and ease of use to the high-volume production of precision bevel gears for robotic, power tool and other applications of similar size. The 175GMS nano Gear Metrology System heralds the advent of a new era, where nano-level inspection is no longer the exception, but the rule. The 175GMS nano and Phoenix 100C Bevel Gear Cutting Machine can be experienced live at IMTS.
gleason.com
GMTA
Booth #237126
GMTA will present its comprehensive range of solutions for producing gears and powertrain components. Whether you need a standalone machine or a complete system cell, GMTA offers tailored solutions designed to deliver a high ROI and optimize your production processes.
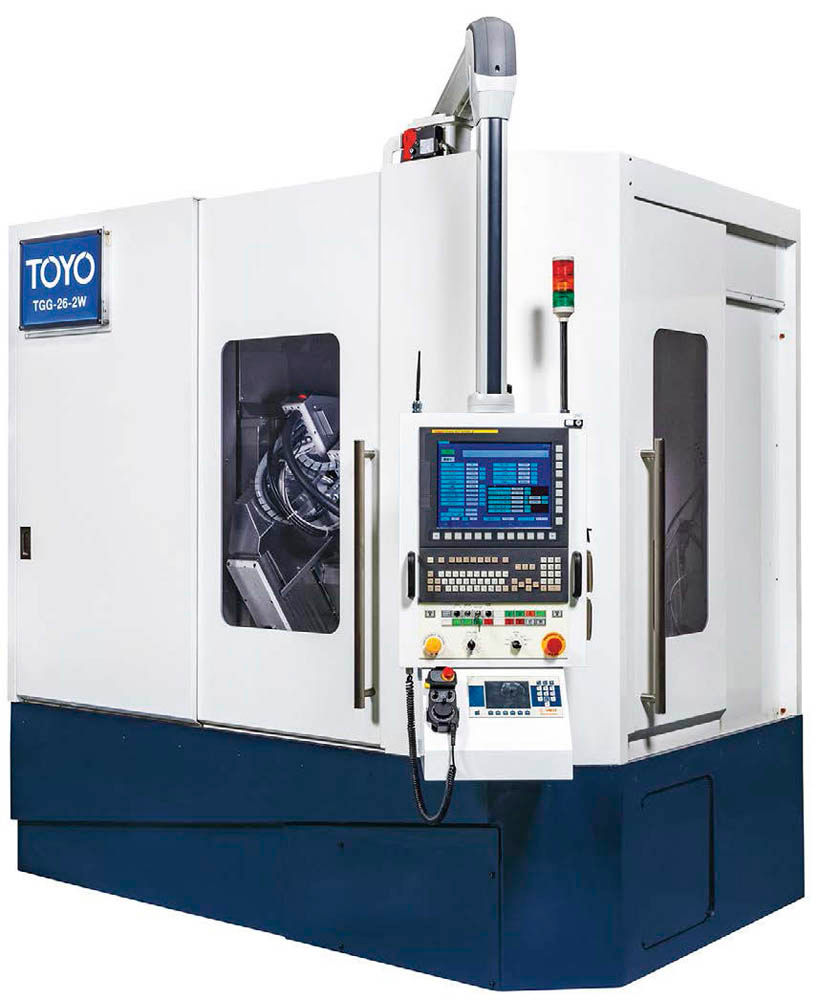

Featured in the GMTA booth is the TOYO TGG-26-2W Gear Grinding Machine that offers versatile gear grinding (accommodating workpieces with an outer diameter of up to 10 in.). This machine includes two work heads for efficient workpiece installation, removal, cleaning, and gear adjustment during machining, significantly reducing non-grinding (idle) time. It is also equipped with an auto-balancer and AE sensor for automatic balance and position adjustment, minimizing alignment time. Our proprietary teeth surface correction application ensures ideal gear grinding with a user-friendly interface.
gmtamerica.com
Hainbuch America
Booth #431636
Hainbuch America will unveil its latest machining innovation, the AC (Automated Change) Line. This solution is a fully automated system for workholding device changeover for manufacturing efficiency and precision.
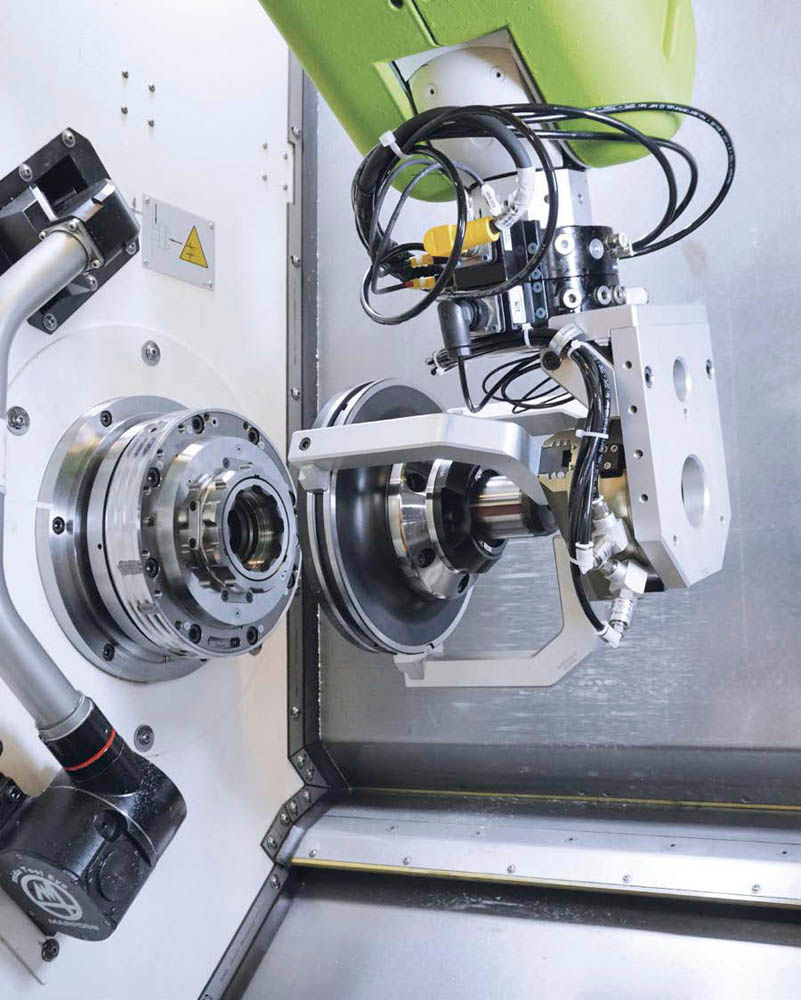

The AC Line streamlines transitions between workholding devices with speed and accuracy. This workholding solution reduces downtime and enhances overall productivity, allowing manufacturers to maximize their machining capabilities.
hainbuchamerica.com
Helios Gear Products
Booth #236906
Helios Gear Products of South Elgin, IL, will feature gear manufacturing solutions including the Hera 90 CNC gear hobbing machine, the M673 CNC gear shaping machine, and the MSR rotary magazine with automatic loading. Helios will feature the high-speed shaping capabilities of the M673. With shaping speeds of up to 2,000 strokes per minute, the capability to accommodate versatile shaper cutter types (disc, bell, and shank) and flexible automation system options, manufacturers can achieve their precision shaping goals.
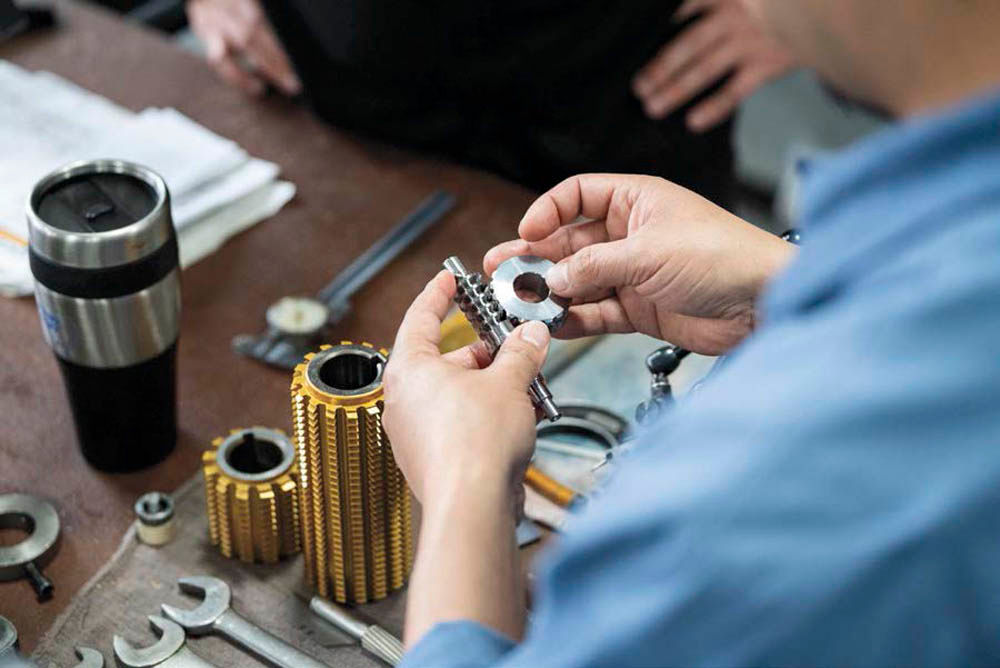

Advancing gear manufacturing productivity even further is the new MSR. This rotary magazine with automatic loading offers comprehensive, versatile automation by integrating manufacturing cells with operations such as gear generation, washing, deburring, and laser marking. The MSR features stackable workpiece towers that offer more capacity than rotary conveyors and is offered with a variety of robotic loading options to feed up to 4 machine tools at a time for fully optimized gear manufacturing operations.
heliosgearproducts.com
HWR Workholding USA
Booth #431579
The North American subsidiary of one of Germany’s premier workholding providers, HWR Workholding USA provides manufacturers with innovative workholding systems that achieve high levels of flexibility and security. The company is best known for its zero-point workholding system for milling applications and patented self-centering compensating chucks for turning applications. HWR partners closely with machine tool builders and automation providers to develop solutions that are easily integrated into advanced manufacturing operations.
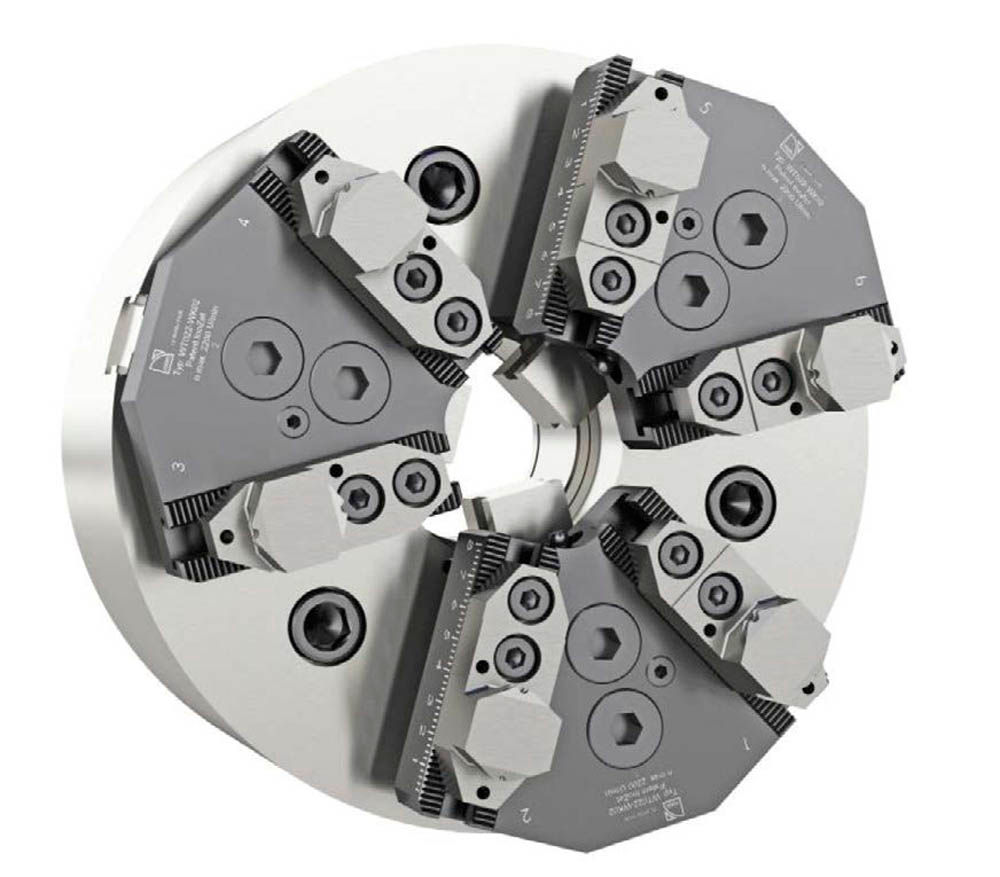

HWR Workholding USA has announced that it will be bringing its full line of innovative workholding products to IMTS 2024. Exhibiting at IMTS for the first time, HWR will be highlighting new and existing solutions for both turning and milling applications. Additionally, the booth will feature a RoboJob automation cell demonstrating the ease with which HWR products facilitate process automation.
hwr-usa.com
Index
Booth #339119
Index will be demonstrating its full range of high-precision machining solutions, which will include the North American debut of its C200 Fanuc, a cost-effective new variant of its production machining center. The company will also showcase the Index iXperience, its comprehensive portfolio of value-added services that provide manufacturers with an optimized solution, from the acquisition and installation of a single machine to the development and delivery of a turnkey production system.
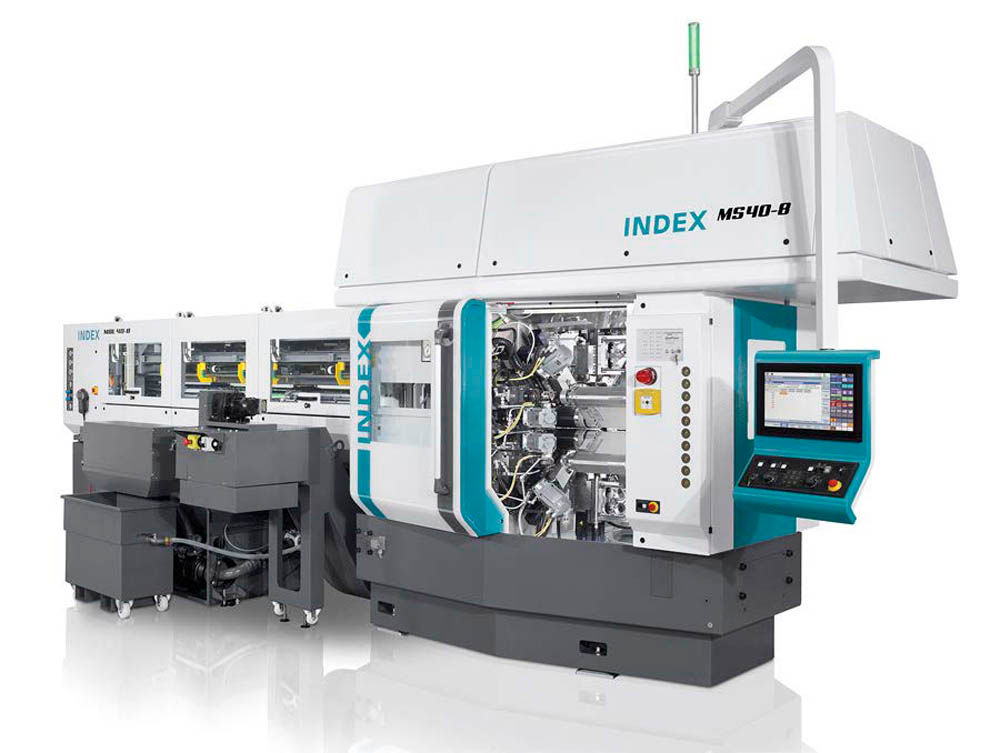

With eight motorized spindles, the MS40-8 CNC multi-spindle allows for extremely short cycle times on both complex and simple parts. The machine is available with dual synchronized spindles and can be operated in a double four-spindle mode to produce two complete parts with every full rotation of the spindle drum. The machine can be configured with up to 18 CNC slides, as well as additional Y axes, to perform a diverse range of processes. All the machine’s motorized spindles are fluid-cooled and can operate independently of the other seven, allowing each to apply cutting data optimized to the process being performed.
index-group.com/en_us
Jorgensen Conveyor and Filtration Systems
Booth #338009
With over 70 years of experience in designing and manufacturing advanced conveyor, coolant filtration and chip processing solutions for machine tool, metalworking, and material handling, Jorgensen Conveyor and Filtration Solutions offers a wide range of standard and customized systems to companies across North America and globally. Jorgensen will feature its PermaClean coolant filtration system that’s combined with the new EcoFilter 80 self-cleaning conveyor and automated coolant solution.
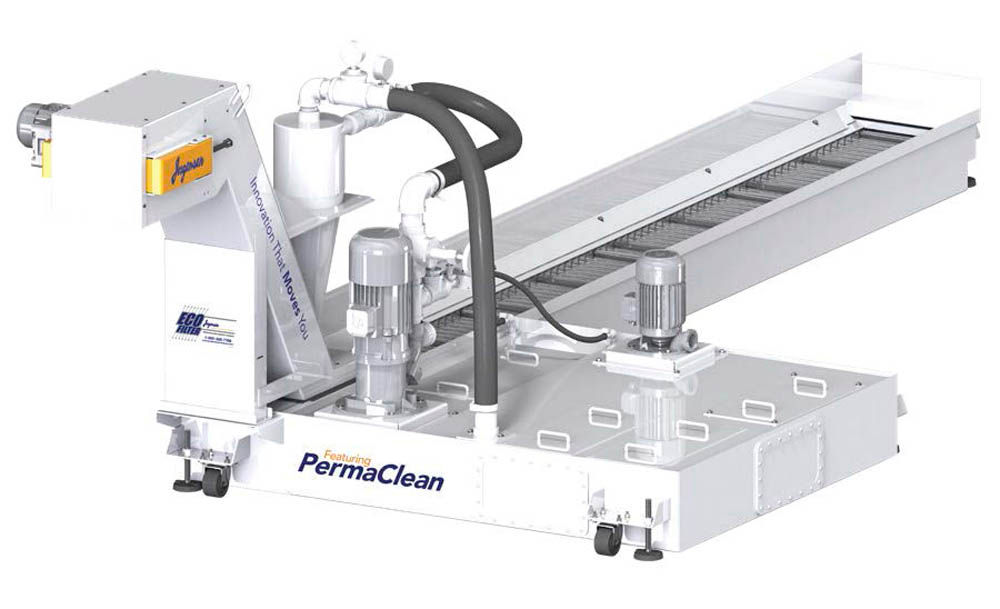

The EcoFilter 80 enables efficient filtration of fine chips to 80-microns nominal and is the first economical non-drum style conveyor below 100-micron filtration. EcoFilter conveyors use a two-stage chip removal and filtration process that carries out large chips on a hinged or scraper belt. Fine chips flow with used coolant between the belt runs to a flow-through EcoFilter cell where they are separated from the coolant.
jorgensenconveyors.com
JTEKT Machinery Americas Corp.
Booth #338700
JTEKT Machinery Americas Corporation will feature 7 new metal-cutting machines and automation solutions at IMTS booth 338700, plus IoT solutions and technology presentations. Showcasing a complete range of production solutions powered by JTEKT, the company’s new offerings include horizontal machining centers, a WELE 5-axis VMC as well as a vertical turning center, Takisawa Taiwan CNC turning centers and two new production cylindrical grinding machines.
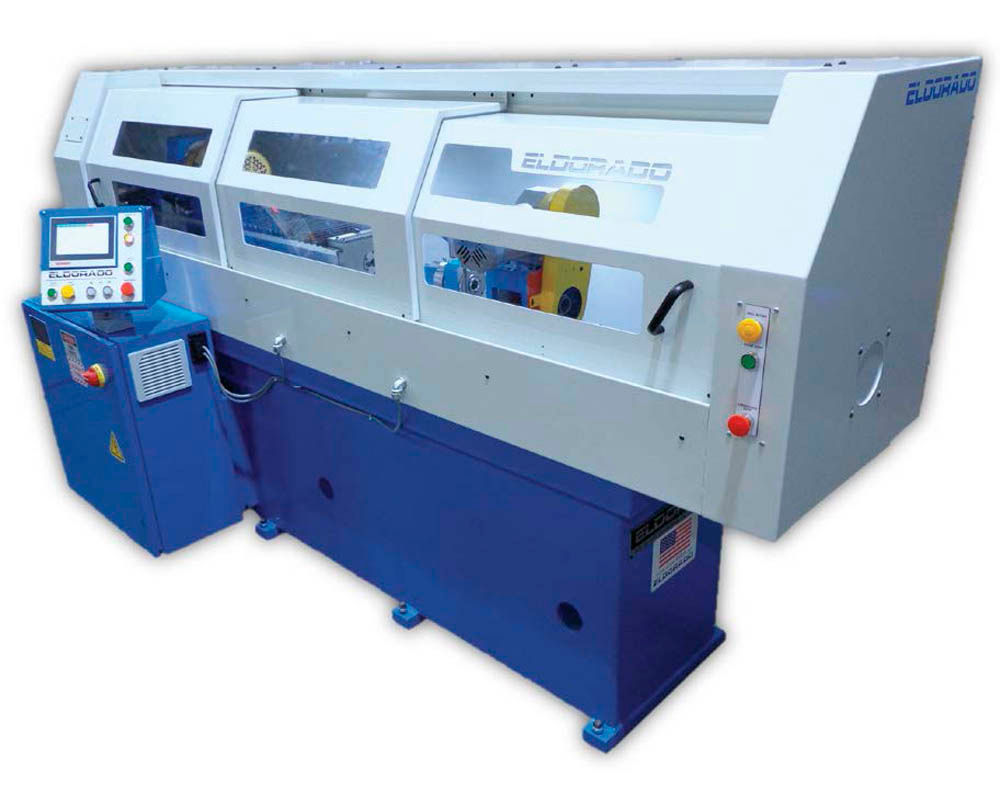

JTEKT will use IMTS to demonstrate its FH5000 Series high-speed horizontal machining centers (HMC) with advanced pallet automation, specifically, a pallet pool for efficient flexible machining system operation. The competitive advantage of FH5000 machines is that they offer 25 percent more machining capacity than other machines in their size range.
jtektmachinery.com
Kapp Niles
Booth #237024
Kapp Niles offers precise and cost-effective technology for grinding and inspection of parallel axis involute gears and other sophisticated components. With Kapp Niles’ purpose-built machine series, it meets the needs of every gear application and noninvolute precision profiles.
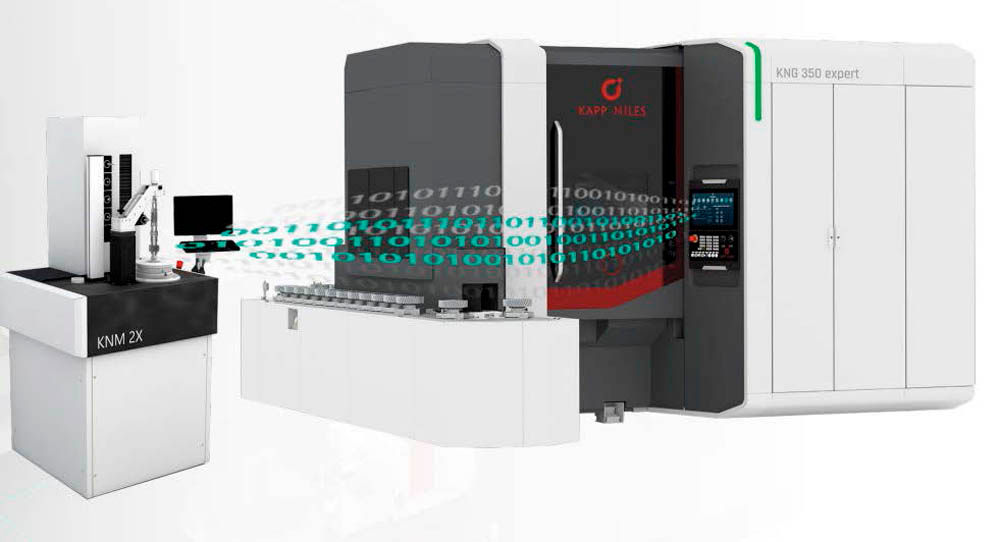

Kapp Niles provides a wide spectrum of machine models suited to the processes of discontinuous profile grinding and continuous generating grinding. As a manufacturer of gear and profile grinding machines, Kapp Niles also offers custom grinding and dressing tool technologies that can be utilized on any brand of machine.
kapp-niles.com
Liebherr Gear and Automation Technologies
Booth #236914
In the gear skiving machines, the process, tools, machine and automation system, come from a single source, since Skiving³ is primarily about delivering a complete solution for the customer. The process provides high-quality assurance and productivity when machining internal and external gears. Skiving³ is especially suited for internal gears of medium size and quantity, as it is much faster than shaping and more economical than broaching.
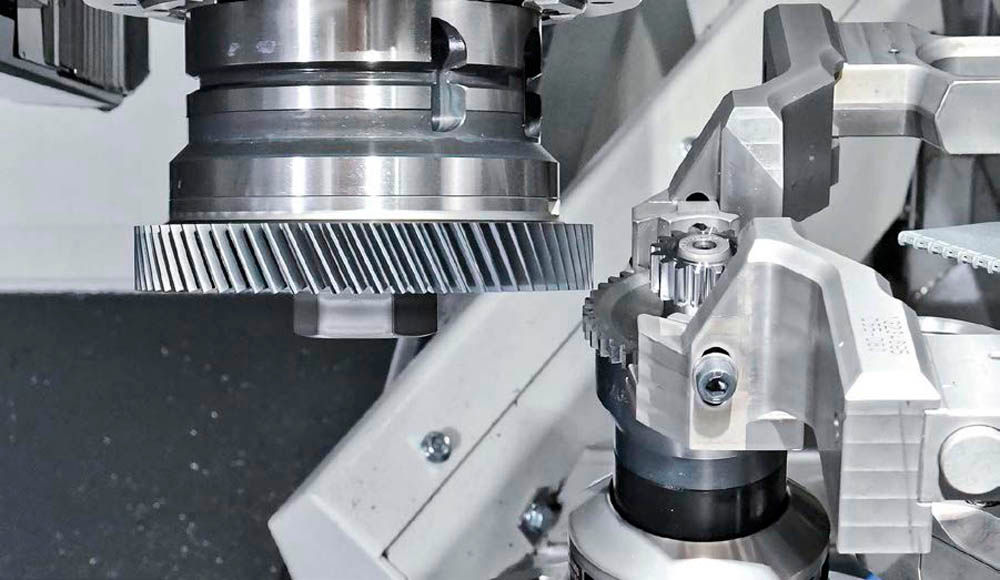

Liebherr will showcase the LK 280 DC gear skiving machine for shafts and rings. The LK 280 DC offers rigid design, a ringloader for fast automatic loading, tailstock for shaft machining and optimum workpiece clamping and optional chamfering during the machining process. Liebherr offers tool design and manufacturing of conical and cylindrical skiving cutters, process-optimized tool design and tools in PM-HSS & carbide versions. Additionally, Liebherr’s process includes analysis and simulation for optimal cutting conditions, availability of application engineers for optimal customer support and 3D collision analysis of part, tool, holder, automation, and machine.
liebherr.com
The L. S. Starrett Co.
Booth #134130
The L.S. Starrett Co., a global manufacturer of precision measuring tools and gages, metrology systems and more, will be demonstrating the latest in quality control inspection technology. “Supporting smart manufacturing and connectivity, we are excited to demonstrate at IMTS the very latest solutions in wireless measurement data collection and transmission, in addition to our wide breadth of leading metrology solutions,” said David Allen, Vice President, The L.S. Starrett Co.
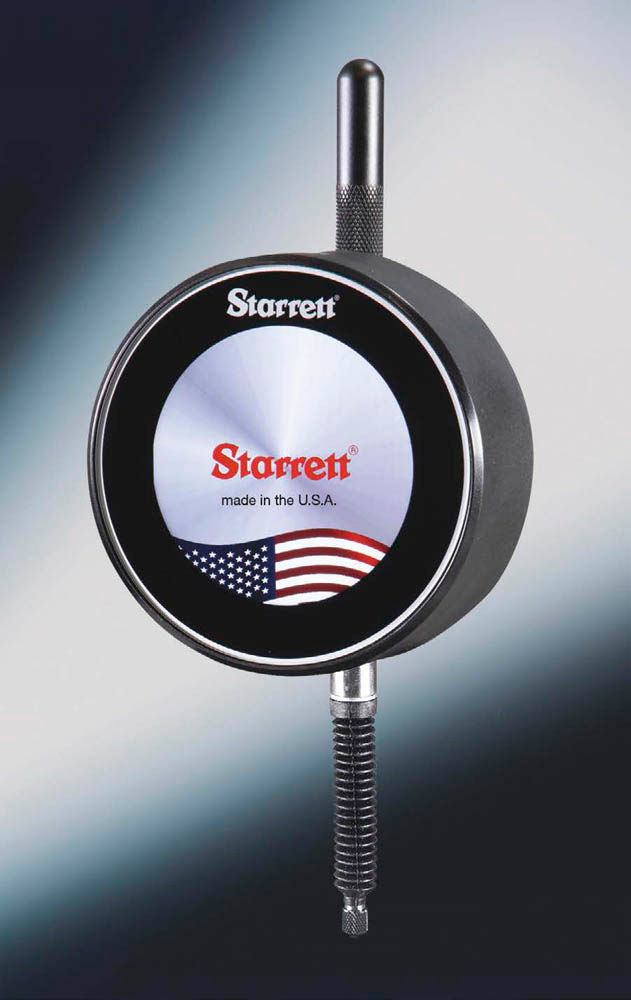

Starrett will be displaying a broad range of wireless, electronic, and mechanical precision measuring tools, and will be debuting its innovative, all-new, W4900 Wireless Digital Indicator utilizing touchscreen technology, that redefines comparative indicating measurement. It is an intuitive, fast, easy-to-use gage. The latest electronic and wireless micrometers, bore gages, calipers and height gages will also be demonstrated, supporting Industry 4.0 initiatives via DataSure wireless data acquisition.
starrett.com
Nagel Precision, Inc.
Booth #236945
Nagel Precision Inc., established in 1982, is an affiliate of the Nagel Group (Established in 1948) and located in a ISO 9001 & ISO 14001 certified manufacturing facility in Ann Arbor, MI. Nagel Precision specializes in honing and superfinishing and will feature Variogear specifically engineered for honing gears.
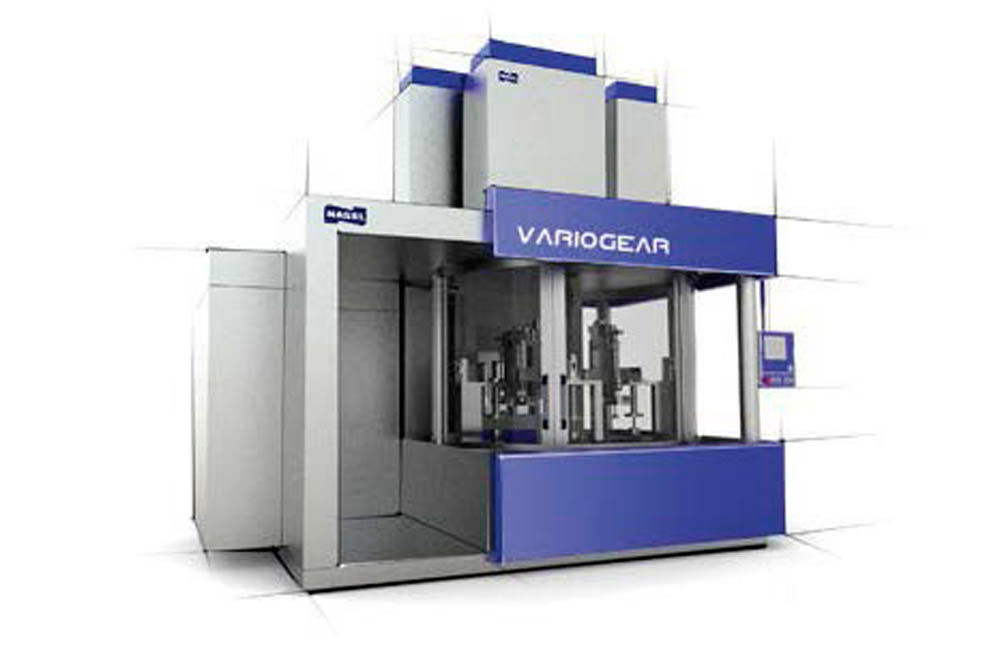

Equipped with electromechanical honing spindles and the latest generation of the Nagel control system, Variogear offers flexibility for high output levels enabling extremely short setup times. Variogear allows post-process measurement after each of the three possible honing operations giving an effective feedback control for each separate process stage. The machine can be loaded automatically or manually. The rotary table transportation serves to reduce nonproductive time for efficient productivity.
nagelusa.com
Nidec Machine Tool America
Booth #237238
Nidec Machine Tool America manufactures gear cutting and finishing machinery, broaching machinery, gantry and boring mills, OD grinders, 5-axis machining centers, 3D printing machinery, wafer bonding technology, gear-cutting tools and broach tools and tooling.
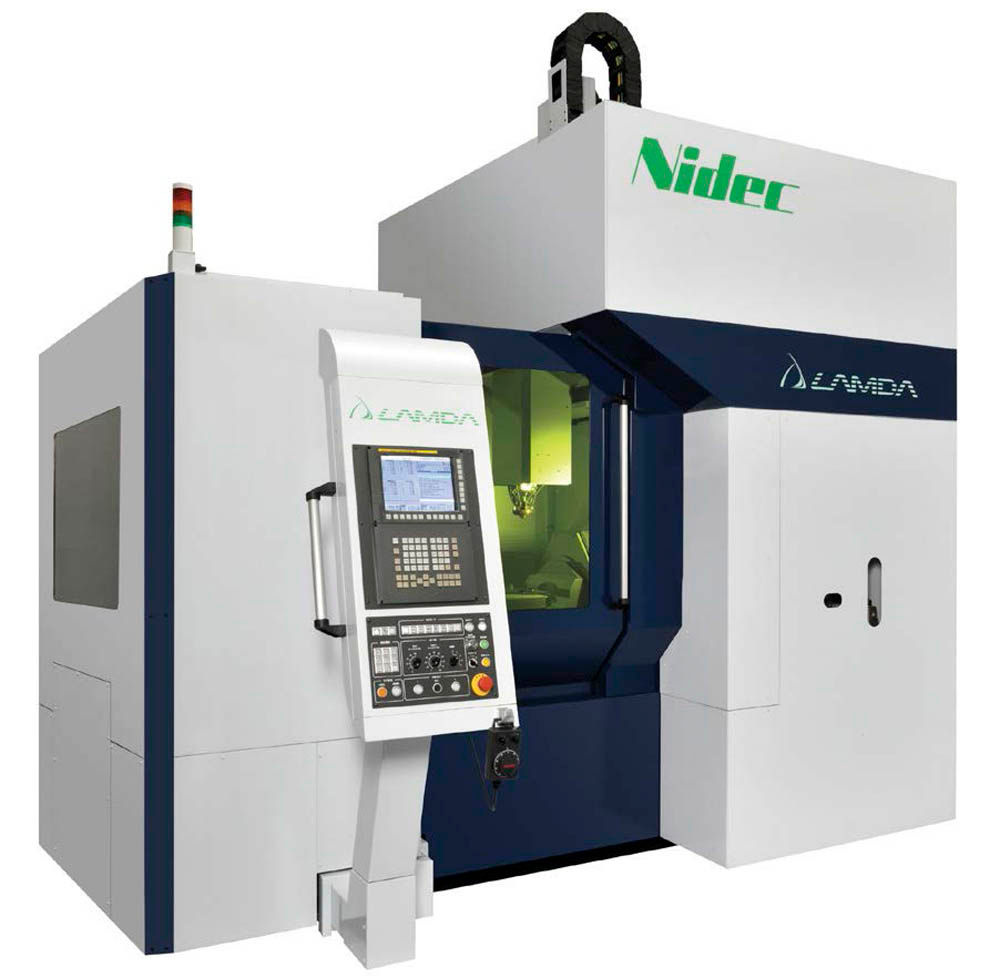
Nidec will showcase the LAMDA500, a mid-sized powder Directed Energy Deposition (DED) metal 3D printer. Designed for diverse metal additive manufacturing needs, the LAMDA500 boasts a generous build volume of 500mm x 500mm x 500mm and five-axis functionality, ideal for producing complex industrial metal parts.

Also featured is the CF26A, a cutting chamfering machine that is used to machine the chamfered portions of gears. The machine is designed to achieve high-precision and high-efficiency machining, and it is particularly well-suited for the machining of gears for electric vehicles.
nidec-machinetoolamerica.com
Norton | Saint Gobain Abrasives
Booth #237042
Norton | Saint-Gobain Abrasives, will be highlighting a range of high-performance abrasive grinding products and technology. Gear grinding solutions that feature a new high-performance bond designed for gear grinding in extreme, tight tolerance environments will be highlighted. The portfolio of gear grinding products is specifically designed by category to provide higher profile accuracy, supreme form holding and burn-free grinding in worm, profile, and bevel applications.
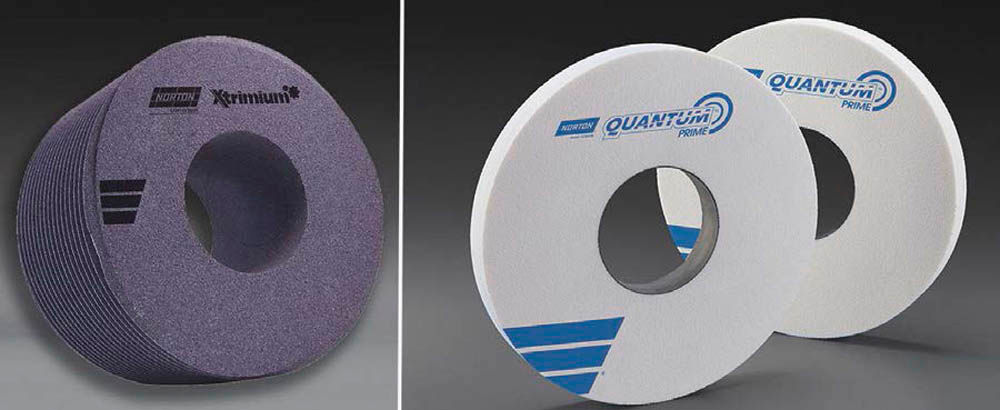

Norton Quantum Prime grinding wheels which feature proprietary nano-crystalline ceramic grain offer high productivity gains across a wide range of applications will also be highlighted. The Quantum Prime grain delivers high grinding efficiency and part quality, as well as significantly longer wheel life than traditional ceramic grains. Wheels are available in a range of types including OD, ID, gear grinding, toolroom, disc grinding, mounted wheels, surface grinding, creepfeed and flute grinding.
nortonabrasives.com
Sandvik Coromant
Booth #338348
Sandvik Coromant, a global supplier of cutting tools, machining solutions and advanced manufacturing knowledge, will showcase an extensive array of holistic engineering products and services to help shops with data-driven solutions and machining technology. Booth visitors can expect an immersive experience that brings together the company’s products, expertise and digital machining technology for a wide range of industries, with solutions that drive greater productivity and manufacturing wellness in advanced machining applications.
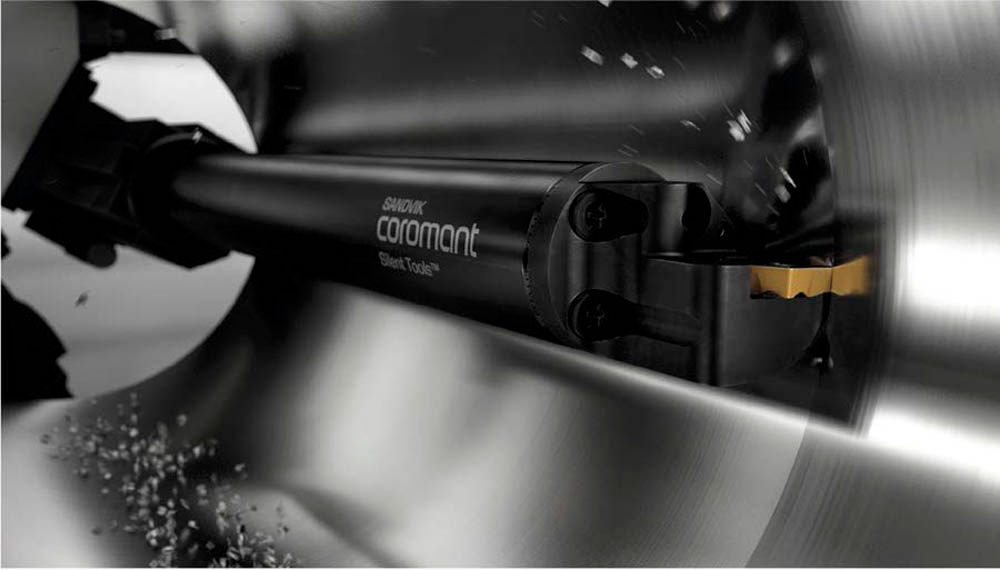

“Our presence in the Machine Tool Hall underscores our commitment to providing a streamlined and comprehensive experience for attendees as a one-stop destination for all their machining needs,” said Veronica Messersmith, Americas President for Sandvik Coromant. “With all of our offerings under one roof, visitors can easily explore the full breadth of our advanced technologies and services and discover new ways to drive efficiencies and productivity gains across the entire value chain.”
sandvik.coromant.com
Speedgrip Chuck Co.
Booth #432268
Speedgrip Chuck Company’s QCR (Quick-Change Receiver) is a manually actuated cam-lock receiving plate that attaches to CNC lathe spindles and reduces the time needed to change workholding clamping devices. Like tool retention in the spindle, the QCR features automatic release of draw connections.

With the QCR, the time needed for operators to switch ID/OD collets, jaw chucks or face driver workholding devices on their machines is cut from an hour to five minutes, making them well-suited for just-in-time production. Visitors to IMTS 2024 can see the QCR along with the company’s other premier engineered workholding solutions firsthand
speedgrip.com
Star Cutter Company
Booth #237013
Star Cutter Company will unveil its newest generation tool grinder—the FLX. This 5-axis grinder offers high-efficiency carbide tool manufacturing within a compact footprint. It has been designed with a focus on flexibility, enabling users to modify features to exactly match their grinding needs. For unattended machining, FLX features a broad range of automation capabilities, producing large numbers of parts continuously.
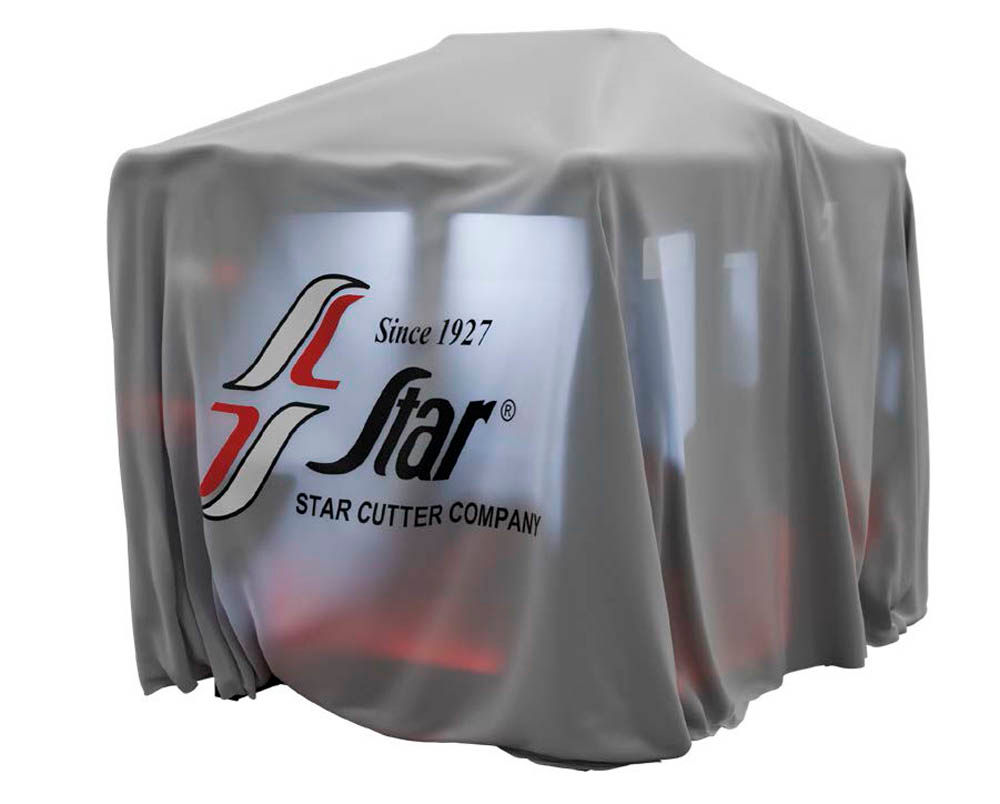

In addition to the new FLX grinder, other Star Cutter products to be featured include: TRU TECH T93X Centerless Grinder; Louis Belet Swiss Cutting Tools; solid carbide drills and reamers, deep hole drilling solutions, PCD and 3D printed tooling; hobs, shapers, Scudding and skiving cutters; carbide blanks and preforms; and more.
starcutter.com
Star SU
Booth #237013
Star SU—part of the Star Cutter family of companies—offers a wide variety of gear-cutting machinery, tools and services including vertical hobbing and chamfering and deburring machines; hob sharpening machines; hobs, milling cutters, Scudding and skiving tools, shaper cutters and shaving tools; chamfer and deburring tools; gundrills and reamers; form tools; and tool life cycle management services.

Star SU brand and technology partners include Star Cutter Company, Modul MT, Louis Belet Swiss Cutting Tools, and GMTA, Inc. / Profilator.
star-su.com
Wenzel America
Booth #134718
Wenzel America brings a broad portfolio to IMTS, offering scalable solutions for modern manufacturing. Built around a unified software platform in WM |Quartis, Wenzel offers systems that can solve any measurement challenge. The exaCT line of CT systems offers metrology-grade inspection to keep pace with the evolving needs of additive manufacturing. The GT450 brings solutions out of the gear lab and into production, with the integration of automated loading.
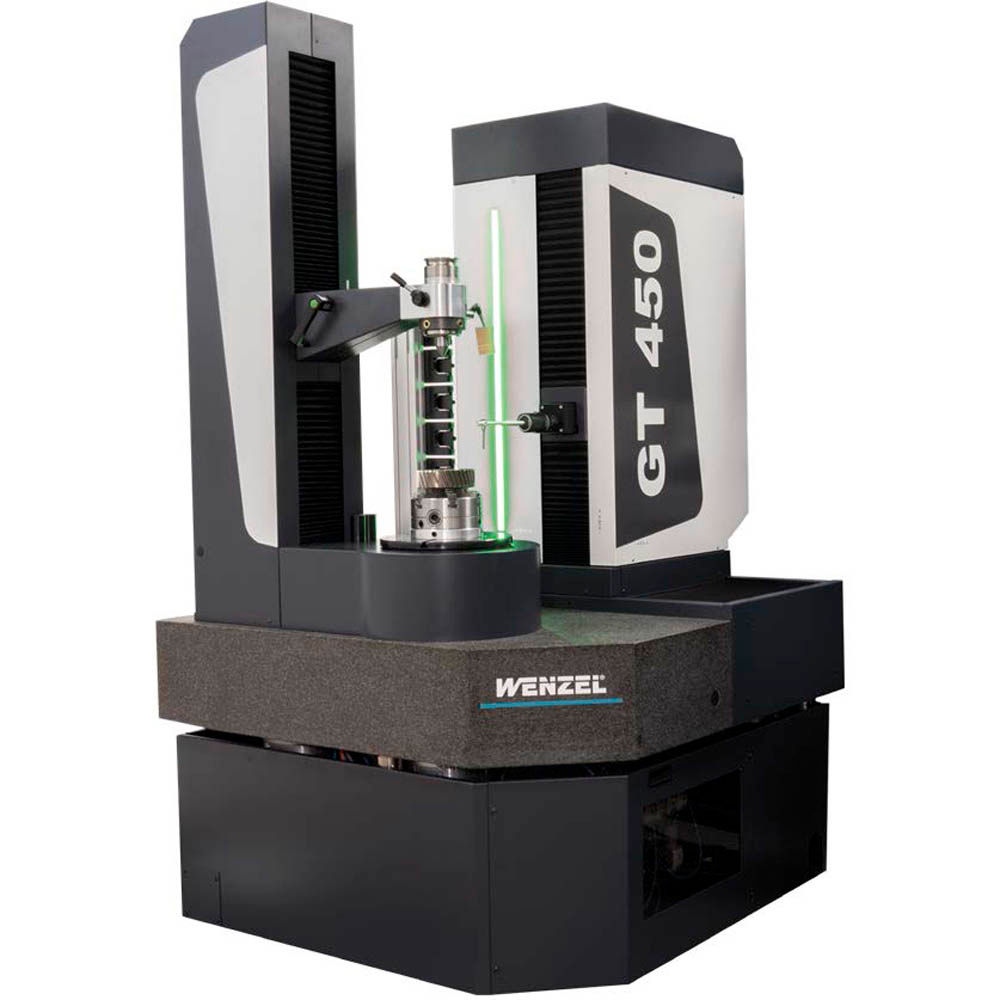

Wenzel invites you to see for yourself how we are bringing metrology forward with an innovative combination of modern, efficient software solutions, coupled with traditional robust mechanical design, to offer the most comprehensive metrology solutions available.
wenzelamerica.com
Zoller
Booth #432018
Zoller will premiere its latest automation system and showcase its complete system of manufacturing efficiency solutions. In addition to presenting the new coraMeasure LG, Zoller will display its range of tool presetting, measuring, inspection, heat-shrinking, balancing, tooling, tool management and automation technology.

“For nearly 80 years, Zoller has been a pioneer in developing technology to optimize processes around cutting tools,” said Zoller Inc. President Alexander Zoller. “Today, we’re proud to provide a complete roadmap to efficient manufacturing from CAM to finished part that can benefit manufacturers in every market segment.”
zoller-usa.com
