Flexible Machining with Liebherr
Liebherr offers a comprehensive solution for complete machining by integrating a tool changing system and a chamfering device. Additionally, the company offers turning, drilling and gear cutting functions of the latest generation of Siemens controls.
The ability to completely machine a workpiece with a gear cutting machine requires the following:
- Flexible programming which enables a combination of gear cutting processes with turning, drilling or hobbing operations.
- A tool changing system which accelerates the workflow over various sub-processes.
- Automated tool check and workflow correction.
- An intelligent distribution of primary and secondary processes.
Flexible Programming
With the programming system LHGearTec and the new control panel LHStation, Liebherr offers a comprehensive operating concept which enables users to define gears with optimum efficiency and precision. When combined with the Siemens programming system programGUIDE, further contours can be programmed. Bores, slots, levelings, engravings and threads become a standard.
Tool-Changing System
The Liebherr tool changing system can be used in various ways. Firstly, it makes the process more flexible and efficient. It can incorporate different gear cutting tools, even those specifically intended for roughing and finishing processes. This means that more expensive tools are only used where they are necessary, thus saving money and extending tool life.
Secondly, sister tools can also be accommodated to increase productivity. The remaining magazine stations utilize up to twelve tools, enabling you to perform additional operations such as drilling, hobbing or turning in the same clamping fixture used for gear cutting processes.
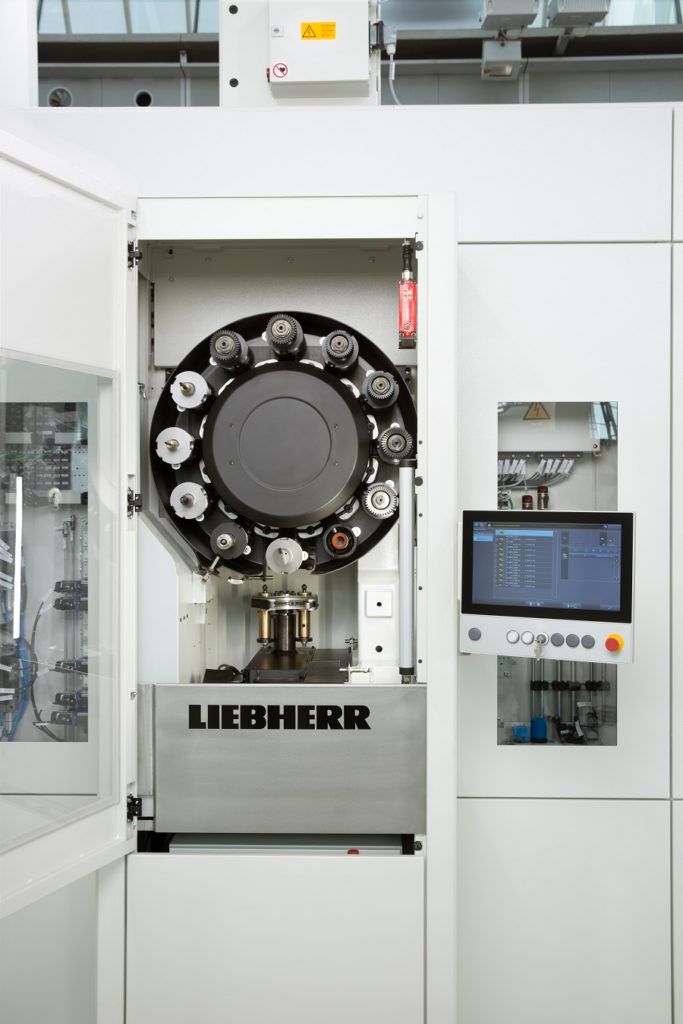
“This enables us to achieve maximum flexibility at the same time as maximum precision, because the reference surfaces remain the same through all the machining steps,” said Dr. Peter Pruschek, head of electrical design and machine control development. “For specific application cases, this removes the need for an upstream turning machine or a downstream machining center.”