Hobbing and Chamfer Cutting
Efficient, Flexible Gear Manufacturing on a Single Machine
It wasn’t long ago that cylindrical gear chamfering and deburring was almost an afterthought. Now the process ranks as high in importance as hobbing, shaping and grinding. Seemingly every gear manufacturer, particularly those developing transmission gears for e-drive applications, recognizes that anything less than a flawless tooth flank can result in premature transmission failure, less-than-optimal efficiency, and unacceptable noise. Thus, generating a chamfer to precise customer specifications is critical to minimize the potential for sharp, brittle edges after heat treat; avoid edge load situations in the gearbox; and eliminate excessive stock and hardened burrs in the tooth flank prior to the hard finishing operations (conditions which can greatly diminish tool life).
280HCD — the Single-Machine Solution
For producers of spur and helical gears in sizes up to module 5 mm with 280 mm workpiece outside diameter and 380 mm shaft lengths, two chamfering processes now exist: chamfer hobbing, for high volume automotive and light truck applications, including final drive ring gears and shafts; and fly cutter chamfering, delivering flexibility for lower volume, small lot jobber applications. Chamfer hobbing first became available on Gleason machines with the Genesis 160HCD vertical Hobbing and Chamfering Machine, then the range was expanded to include even truck-size gears with introduction of the Genesis 280HCD. Fly cutter chamfering, which had long been employed on bevel gear cutting machines, was adapted for the first time as a viable chamfering process for cylindrical gears on Gleason’s Genesis 400HCD Hobbing Machine, designed for workpieces up to 450 mm outside diameter and module 8 mm. Yet, for many gear manufacturers, it’s not an either-or proposition. Most can benefit from a single platform that can perform both processes interchangeably, and thus open the door for many new opportunities, whether with an increase in productivity, or through the production of smaller lots requiring tremendous flexibility.
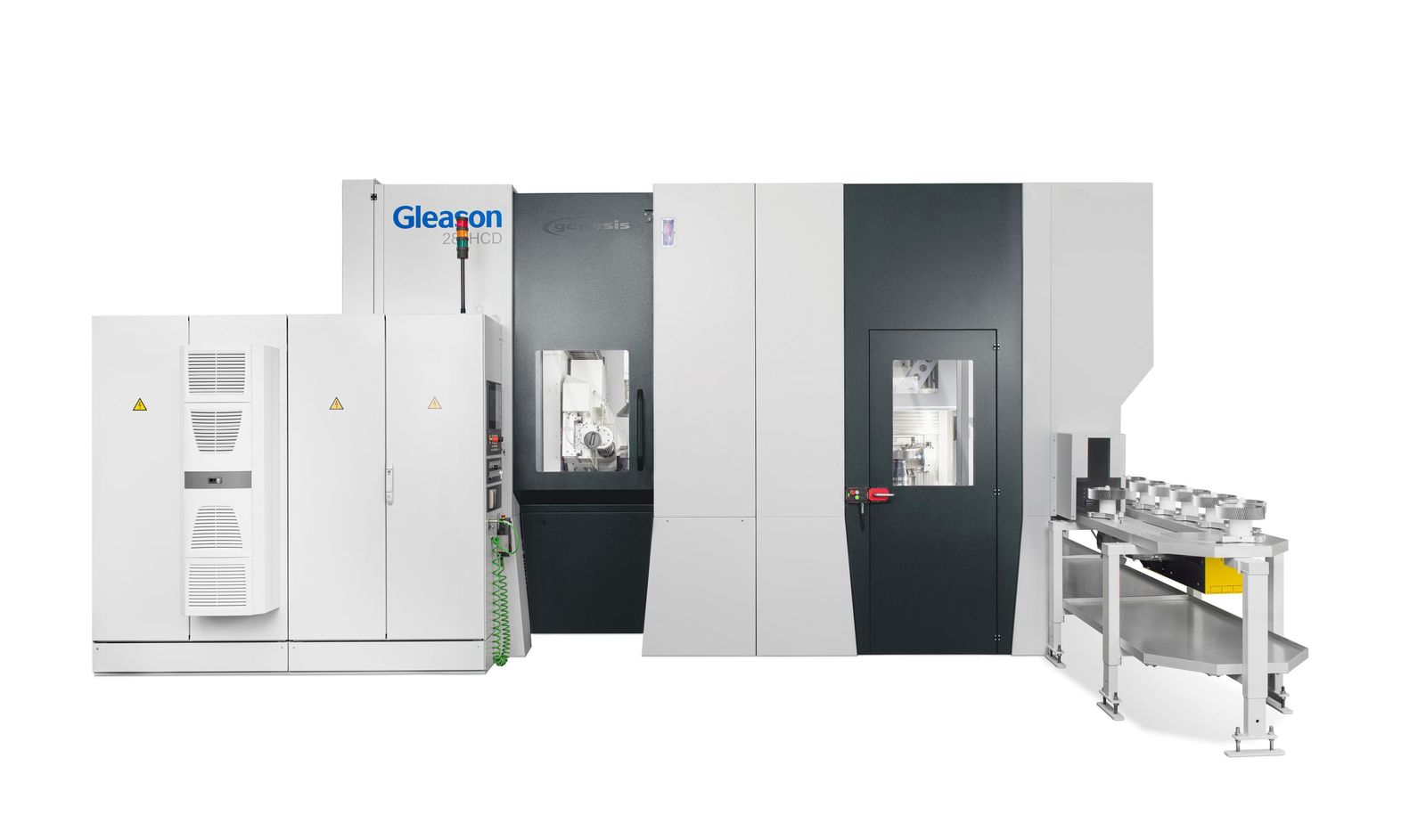
280HCD Hobbing and Chamfering machine with chamfer station for chamfer hobbing and fly cutter chamfering.
The 280HCD combines hobbing with a chamfering/deburring station attached to perform either chamfer hobbing or fly cutter chamfering in parallel to the hobbing operation. The 280HCD features a gantry loader to link gear hobbing with the chamfer cutting station and external automation/storage. Most importantly, users can benefit from having both chamfering processes on the same machine and at their disposal with just a simple tool change.