Making it in Mobile
Making it in Mobile
Alabama manufacturer puts InvoMilling to the test
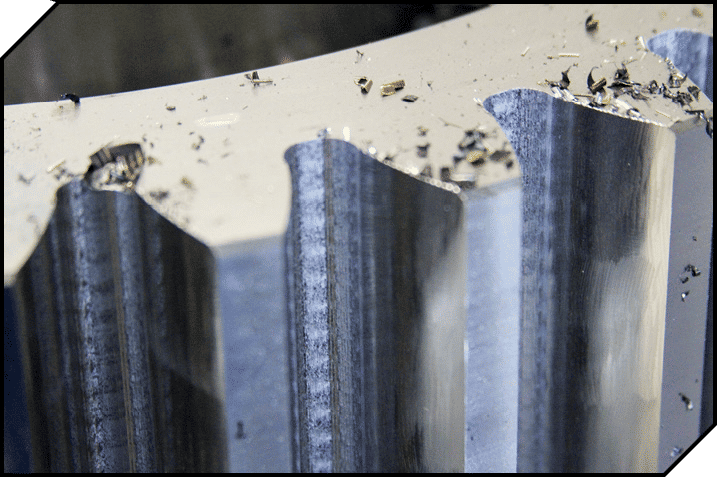
"If it's broken, bring it on in." That's the advice offered by Roy Parker, president and owner of Jones Welding Company Inc. Since 1911 (see sidebar) the Mobile, Alabama machine shop has enjoyed a reputation for taking care of whatever parts need fixing. It’s no wonder. With 11 Mazak CNC lathes and machining centers — several with 5-axis or multitasking capability — along with a full complement of gear hobbers and shapers, and a handful of skilled machinists to run them, Jones Welding (JWC) can deal with most anything that comes through its doors.
JWC sits not far from the Port of Mobile, the only deep-water port in the state. David Dearing, power transmission specialist at Jones, explained how the company benefits by its close proximity to the water. “We service much of the shipping industry in the area. There’s a lot of service and repair work, and quite often we have to analyze and reverse engineer one-of-a-kind parts through x-ray fluorescence analysis (XRF) to determine material types, CMM measurement in conjunction with SolidWorks to produce 3D models and assemblies, and 3D printing to build working prototypes.”
Aside from replacing the broken components found in cargo ships and container handling equipment, JWC also does custom work for the steel, chemical and paper industries. “We’re quite versatile,” Dearing said. “From close-tolerance parts you can hold in your hand to parts that weigh in excess of 10 metric tons, we've tried to position ourselves as a one-stop shop. Today we service whatever industry we can sell a product or service to.” Despite its extensive CNC capability, however, Dearing pointed out that JWC isn’t a production job shop, specializing instead on quick-turnaround, low-volume work. “An order for 50 pieces is a large quantity for us.”
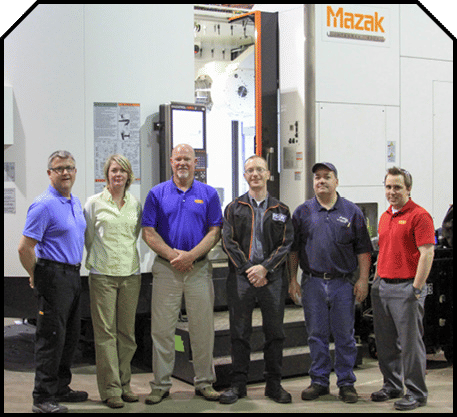
With small production runs, changeover is a big factor in any company’s profitability. To meet the need for reduced setup time, JWC invested in quick-change chucks and workholding, and outfitted its machines with Coromant Capto toolholders, a modular tooling concept from Sandvik Coromant Corp., Fair Lawn, NJ. The Capto system, Dearing explains, allows JWC’s machinists to change cutting tools in seconds, making this job shop very effective at producing parts in small batches.
Many of those parts are gears. JWC’s equipment allows the company to cut gears between ½" to 88" in diameter. The problem, said Dearing, is tooling up for all those different gears. “Each gear profile requires a specific hob. At a few hundred bucks a pop, it can really add up.”
This means JWC invests in hobs that will quite possibly never be used again, a cost that is difficult to pass on to the customer. Adding insult to injury, many of JWC’s jobs are emergencies — when a plant is shut down because of a broken gear, the pressure is on to provide quick turnarounds as well as an ever-increasing level of precision. If the hob needed to cut that gear isn’t sitting in JWC’s tool crib, it frequently becomes necessary to overnight one in, further increasing costs and downtime.