GT: Is your Automatic Electron Beam Correction technology a feature unique to JEOL’s EBM solution?
RP: Our Automatic Electron Beam Correction technology was ported over from our JBX E-Beam lithography systems. JEOL released the first computer-operated EBL system in 1967, so there is deep IP even within the subsystems of our EBM solution. Our Automatic Electron Beam Correction technology provides confidence to our users the system will operate as intended for long periods of time without user intervention. Last year during the winter break, one of our EBL users at a National Lab wrote a pattern meeting tool spec for 360 hrs (15 days) nonstop. This Automatic Electron Beam Correction technology is at the core of our reliability and day-to-day repeatability.
GT: Please describe the “scattering phenomenon” and how your e-shield and helium-free environment serve as a solution?
RP: The “scattering phenomenon” occurs when a powder particle does not have adequate adhesion to the build platform. The e-shield prevents energized particles to pass to a powder particle outside the designed build area. Without e-shield, unintended artifacts are created and damage to the system could occur if the “scattering phenomenon” is not controlled. The patented e-shield and our unique scan strategy helps eliminate the “scattering phenomenon” or “smoke events”. This strategy removes the need for helium, an expensive and limited natural resource, and any other gases.
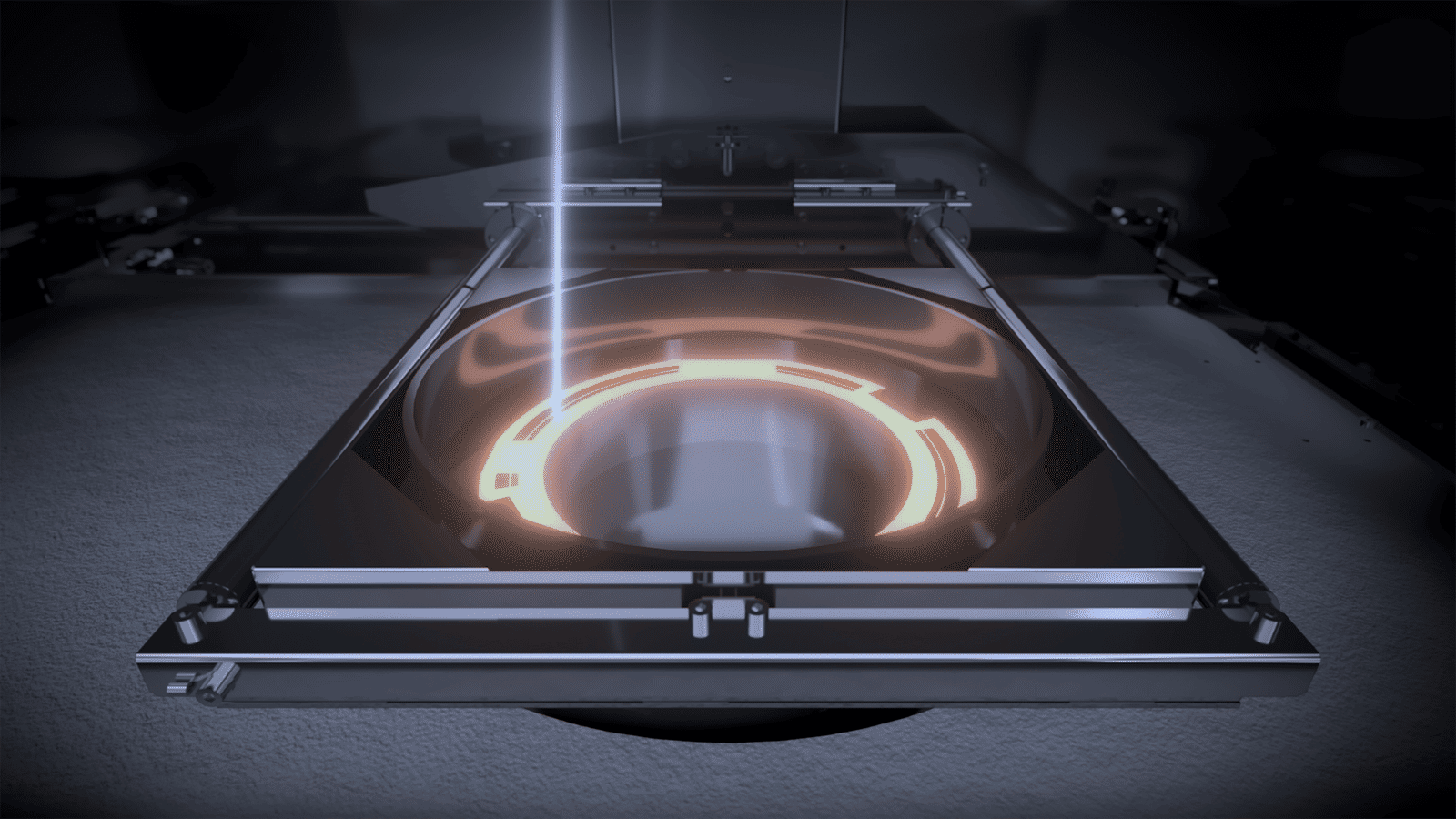
JEOL’s unique helium-free, powder-dispersal prevention system avoids the scattering phenomenon. That not only allows parts to be manufactured in a clean space at a low-cost, the surface of the cathode is also less susceptible to damage, allowing the electron beam to remain stable.
GT: What role do you see AM playing in the gear industry as the technology achieves more mainstream adoption?
RP: We think AM can make the gear industry more efficient and bring new solutions to its customers at a faster rate due to the inherent advantages of AM. There are cases where traditional manufacturing and additive manufacturing are complementary, giving gear manufacturers the possibility to mix and match these technologies for their optimum solution.
The long-life cathode, which lasts over 1,500 hours, can greatly reduce downtime for cathode replacement. The secret is JEOL’s original vacuum technology, developed in the manufacturing of electron beam related equipment.
We believe our long history of development and production of advanced, field-proven electron microscopy and electron beam technology, combined with JEOL’s extensive service and support network, is an opportunity to integrate quality and reliability into the employment of this novel technology.
jeolusa.com
Nidec Machine Tool—#237036 (North Building), #338252 (South Building)
DED, or directed energy deposition, as implemented in the Nidec LAMDA 3D printing systems, utilizes a powerful focused laser beam to melt powdered metal that is supplied to the build area by a nozzle. As the laser heats the powder, it melts and sinters to the baseplate or layer below.
There are three powerful technologies integrated into the LAMDA’s state-of-the-art control. First, by monitoring and controlling the laser power in real-time, the size and temperature of the melt pool is constantly controlled to permit accurate deposition and full integration of metal onto the part being printed. This monitoring system also provides a fully verified quality control record of the build.
State-of-the-art local shield nozzles with enhanced shield performance. The optimized shield gas jet expands the shield region area up to 45 times the conventional size. The local shield function eliminates oxygen in the environment around the molding process to prevent the oxidation of molten metal.
Secondly, when printing materials that are reactive with oxygen, inert argon gas is used by the LAMDA Local Shield. This excludes oxygen from the melt pool and allows large components to be 3D printed without the need for an expensive atmospheric chamber. This also greatly reduces the cost of operation by not needing to purge large quantities of this inert gas.
The third important technology brought to additive manufacturing detects potential problems before the process fails. To build large items defect-free, LAMDA has deep learning AI for anomaly detection. The machine knows and can detect many anomalous patterns at installation, and the machine will “learn” additional new anomalies as they occur. This image processing occurs at 300 images per second, which is faster than the speed of the CNC control unit.
Nidec Machine Tool’s LAMDA2000 3D metal printer is a direct energy deposition additive manufacturing system.
Applications for DED include uses beyond full 3D printing builds. The ability to apply material to an existing part is a valuable repair option for expensive, hard-to-make, and long-lead-time components. The ability to use two different materials, for example, titanium and Inconel, on the same part opens even more possibilities for repair and solving problems.
The range of materials that can be used with DED is quite amazing. Stainless steel, maraging steel, Inconel, titanium, and even aluminum can be used without an atmospheric chamber.
For gear manufacturing and gearbox repair, having the ability to add material back to a large (expensive) gear or shaft can be a game-changer. Printing workholding components, robot grippers and a vast array of tooling is another example of DED providing value to the gear-making community.
nidec.com/en/nidec-machinetool
Fortify—#433114 (West Building)
Fortify developed Digital Composite Manufacturing (DCM) to unlock new material properties that cannot be achieved with today’s 3D-printed photopolymers. They achieve these properties by suspending and aligning Functional Additives (particles and reinforcing fibers) in a resin matrix during printing. Fortify’s open materials platform allows for a wide range of material properties that can be architected to meet the most stringent application needs.
A 3D-printed gear made with Fortify's HTS resin. In DCM, functional additives must be uniformly distributed to achieve consistent material properties. Fortify’s Continuous Kinetic Mixing (CKM) addresses this issue by blending, recirculating, and heating the resin-additive matrix as required throughout the printing process.
Fortify partners with the world’s leading chemical companies to architect specific material properties based on the need of a particular application and solve printability challenges that are barriers to commercialization on other photopolymer platforms:
Example parts made with HTS resin.
High Deflection Temperature (HDT) and high strength and stiffness ceramic-fiber reinforced photopolymer tuned for use in tooling applications.
Low-loss dielectric materials for use in high-bandwidth, high-frequency communications systems.
Technical ceramics with low shrink for high-temperature and radio-frequency applications.
High-temp electrostatic discharge (ESD) material for tools, jigs, and fixtures that can be placed directly into a solder reflow oven.
Resins with 10x the thermal conductivity of any other photopolymer with electrical insulation for sensitive heat transfer applications.
Fortify's FLUX Series printer lineup.
Fluxprint is Fortify’s fiber alignment module. In DCM, during the printing of each layer, a magnetic field is applied across the build area. This aligns all fibers throughout the layer in the target orientation. Individual regions of this layer are then cured with UV light. This locks the orientation of fibers only in those regions. This process of orienting and locking fiber is repeated as needed within each layer and for the subsequent layers. This unique ability to control fiber orientation throughout a part allows for precise tuning of material properties and is unprecedented in any manufacturing technology.
Ben MacDonald, Senior Applications Engineer, said the following about Fortify’s high-temperature and strength (HTS) resin, a particularly strong material candidate for gear applications: “HTS is a resin that is uniquely suited for printing gears due to its strong wear resistance properties which enable gears printed in HTS to significantly outlast alternate materials. This wear resistance is paired with a high HDT allowing for these gears to operate in harsh conditions while maintaining structural integrity.”
fortify.com