The Evolution of a Pencil Sketch
Hetec GmbH Utilizes Liebherr PHS 1500 Allround for flexible part manufacturing
Edited by Matthew Jaster, Senior Editor
Hetec GmbH, the Hessian machining technology specialist and supplier for tool, mold, and machine construction, has automated its production using the pallet handling system PHS 1500 Allround. The company almost exclusively manufactures individual parts and small series with long spindle running times and does not seem like a typical automation customer at first glance. Nonetheless, a flexible automation system was the right solution. In this case, the secret to the system’s success is its integration with three identical Grob G751 5-axis machining centers and the Procam master computer. This combination enables the company to achieve optimal machining flexibility.
Everything started with a piece of paper, a pencil sketch of four rectangles. The general managers of Hetec GmbH – Friedhelm, Günter, and Tom Herhaus – had given intensive thought to the requirements and layout of such a system and were prepared to create the necessary peripheral conditions for it. The aim was maximum flexibility in order processing for just-in-time production.
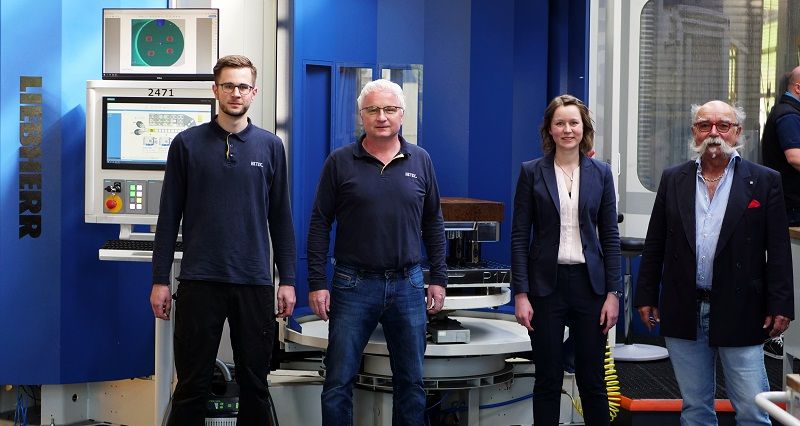
Modern company with digital processes
Founded in 1998, Hetec specializes in the sophisticated five-axis milling of components, in particular complex components for tool and mold construction, as well as general machine construction. Hetec almost exclusively machines individual parts and adherence to tight delivery deadlines is key. A modern machine park consisting of 5-axis machining centers guarantees the utmost precision right down to the smallest tolerances in micrometers.
Every detail has been considered in the production workflow. Each tool is electronically monitored and can be used in every machine, which ensures minimal retooling times. Order management for the individual workpieces is digitalized. The components receive a material routing slip with a bar code containing all the stored information, which can be updated in real-time if changes are made. An app produced by the machine supplier reduces standstill times by allowing users to check the current status of the system at any time, even outside the factory, and to respond immediately to warnings.
Desire for more flexibility
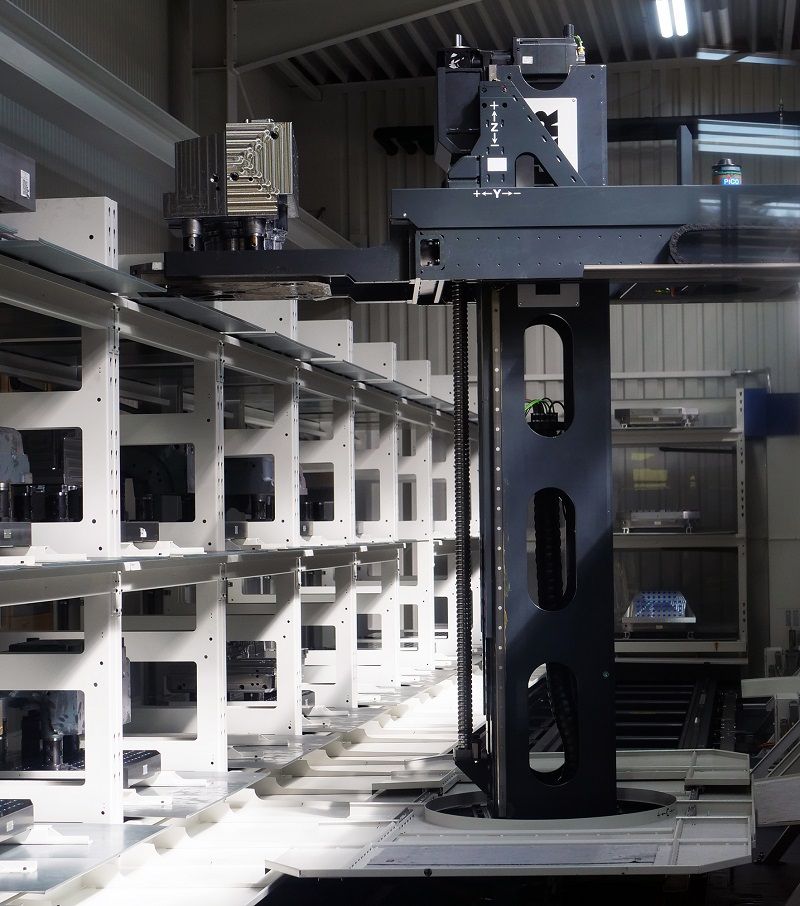
Given the great diversity of parts, absolutely precise just-in-time manufacturing of complex components is a basic prerequisite for sustainable success and customer satisfaction. The path to automation as a solution to this challenge was developed step by step. First, the company invested in a zero-point clamping system which was later supplemented with a Grob G551 with a pallet changing system to be able to manufacture continually on weekends as well as weekdays.