With a combination of data profiles, protocols and the LHWebPlatform, Liebherr provides an infrastructure for the acquisition, transmission, storage, processing, provision and display of machine, operating and production data. In the basic app LHMachineInfo, users can see the live status of their machine tools at a glance and observe changes in real time. The LHSignalInfo app visualizes the recorded signals, taking into account all measuring points and their exact time stamp. Liebherr has expanded the range of functions of LHWebPlatform to include a further tool: The LHReportInfo app visualizes and analyzes the performance of the machine and generates reports and evaluations from the machine data – a decisive step toward more productivity.
WGT 280 and WGT 400 gear inspection devices
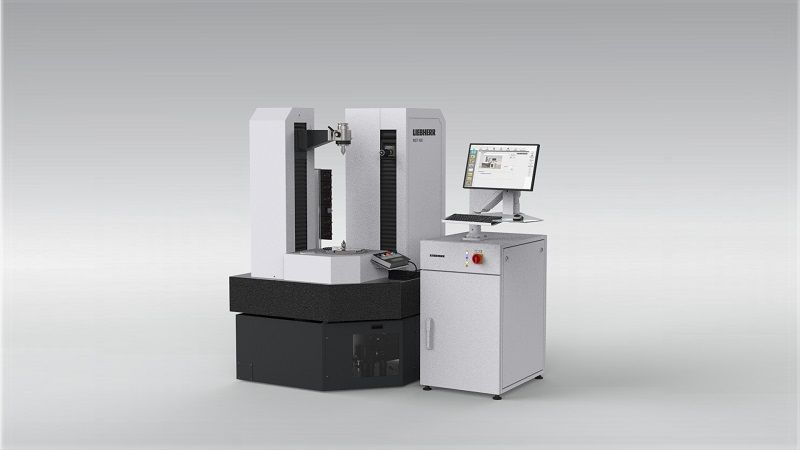
The four-axis measuring instruments of the WGT series have high-precision mechanics and electronics, which are controlled by smart and user-friendly software. They meet all accuracy requirements regarding gear measurement and comply with VDI guideline VDI/VDE 2613, group 1. In addition to the gear inspection machine options available as standard, customer-specific solutions are also available, such as adjusting the travel range on the Z-axis, longer tailstocks to accommodate long shafts, and rotary tables adapted to the payload. An automatic sensor changing system ensures uninterrupted measurement of the workpieces and also offers the highest levels of convenience for the user. The extensive software features make the machines suitable for measuring all types of gears, such as spur gears, bevel gears, worms, worm gears, shafts, gear cutting tools, and other rotation-ally symmetrical parts.
Training for gear hobbing and generating grinding
Are you looking for high-quality, individual training courses and workshops on the topics of gear hobbing and generating grinding? Would you like to specifically improve or refresh your gearing knowledge in an effective way? Liebherr Academy offers a new and modern Machine Training Center (MTC) including a gear hobbing and generating gear grinding machine for practice purposes. Sign up here:
go.liebherr.com/axd8mh
Pallet handling systems as a productivity booster
Liebherr pallet handling systems open the door to increased productivity, even for small batches.
Pallet handling systems handle workpieces on uniform transport pallets. This makes them the ideal automation system for one-off and small batch manufacturing, facilitating unmanned shifts through to “lights-out manufacturing” and enabling unit costs to be reduced by up to 40 percent and machine running times increased to up to 90 percent. The application and combination possibilities are diverse