The future of gear manufacturing will rely on new engineering talent to navigate areas like smart manufacturing, system integration, automation, and robotics.
“Mechatronics is the key,” Cinquemani said. “Commercially, consolidation is going to limit customer’s choices resulting in opportunities with potentially lowered barriers through new technology.”
Young added, “From our perspective, the tolerances required from customers are trending higher. This places more pressure on supply chain and machine manufacturers themselves.”
Describe the most important trends affecting your business and the gear industry in 2023. What should our readers know about these trends?
“Electrical mobility.”
“Russian War COVID´s effects in the production chain.”
“Automation growth.”
“Cost efficiency, supply chain, the Build America Buy America Act, supplying solutions instead of products, factory automation.”
“Reduced income by European inflation on the global market.”
“e-mobility.”
“Stock-outs for spare parts for machinery repair.”
“The overall gear manufacturing industry is still maintaining extremely long lead times. This helps us since we are able to offer expedited production services.”
“Government mandated electric automobiles.”
“New products.”
“Continued cost increases for alloy steel.”
“We serve a wide range of industries with low volume/high mix products, subcontract manufacturing and repair. With inflation and the weaking economy, production volumes drop and repair becomes more cost effective. Having specialized in this type of work, we have developed equipment and methods that allow us to continue to expand our market reach at a very low cost.”
“Recession.”
“Staffing—especially industry specific positions—is very difficult. Bi-partisan emphasis on return to U.S.-based manufacturing is great. Increases in aerospace, outer space, industrial, defense and medical/instrumentation.”
“Supply chains, if recovered at all, are hanging on by a thread. Inflation and cost increases are rampant. Business is good, costs are high. Bookings are up but shipped units are lower.”
“Continued funding for government contracts. Continued stability in oil prices. Further development of EV gearing for automotive.”
“Increasing supplies and availability of permanent magnet motors that may not require gear reducers.”
“Car sales have changed. Lower production drives higher demand and higher profits. Make less cars but make more money. It’s a good model for the OEMs but not the suppliers.”
“Vehicle electrification and how it affects the gear demand.”
“Stability of supply chain including gear materials.”
“Advent of EV industry. Optimization of gearbox with the given package.”
“Aging aerospace platforms becoming more competitive. Materials and labor are becoming more expensive.”
“Lack of orders for light-weight, high power density new starts.”
“Employment trends: It will continue to be hard finding good people.”
“Demand for large gears for mining and bulk material handling projects remains solid. Smaller gear drives for unit material handling slowing down.”
“Gearless drives on large conveyor belts. Lithium production South America geopolitical situation(s).”
“Raw materials lead-time is easing. Customer orders are less optimistic starting in the 3rd quarter of 2023.”
“Increased material costs, energy costs, heat treatment costs and tooling costs. Worldwide competition.”
“Uncertainty regarding worldwide business given geopolitical tensions.”
“5-Axis machining, 3D Printing—new ways to make old products. Fewer people, quicker turnaround.”
“Overseas and Mexican sourcing by competitors.”
“Lack of raw material availability and shortage of skilled manpower.”
“Tighter tolerances on every aspect of the gear while trying to maintain efficiency.”
“Costs of living/inflation; recession; staffing shortages.”
“Oil, off-highway and big truck business.”
“Standardizing calculation methods for involute splines with straight or highly crowned teeth. Incorporating bearing manufacturers' proprietary data on internal geometry into computational models for gearboxes and shafts. Improving surface finishing methods for splines designed for low friction and high misalignments.”
“Heat treatment issues.”
“Service.”
“Shortage of employees. Automation needs serious consideration by all.”
“Worker availability and skill levels.”
“Maintaining quality and speed in production, especially being a jobbing gear manufacturer and meeting customer expectations.”
“Inflation.”
“Green energy.”
“Skilled trade. I think it is important to lead in training the next generation of skilled machinists. We are starting to see a turn in this country that it is OK not to go to college and that the skilled trades are a pathway for a lot of our younger generation to have a high paying, highly skilled job without a degree. We are finally seeing support from the local and state government as well. I think the companies that stay ahead on this front will be well set going forward.”
“Raw material pricing, labor needs and inflation.”
“Delivery capability.”
“EV requirements. Safety.”
“The invention of EVs has shifted the focus for us and many other companies involved with gear manufacturing. We are a gear cutting tool supplier, so we are now concentrating more on carbide hobs and skiving cutter development, as these products will be in high demand if EVs flourish in the future. With so many alternate technologies being experimented (hydrogen, etc.) eventually one thing is for sure that automobiles are not going anywhere and they will definitely need a powertrain in some form another. Maybe the products will become expensive in the beginning due to economies of scale not being present, but there will definitely be demand.”
“EV powertrain.”
“Getting the younger generation more excited about manufacturing. We have a few, but could use more.”
“Low demand.”
“Automation and e-mobility.”
“Moving back productions from Asia to Europe.”
“Supply chain issues and trying to replace retiring, skilled employees. A university degree (support staff) will not replace highly skilled tradespeople that are in such short supply as to be nonexistent (the ones that contribute to GDP).”
“Inflation impacts in the USA as compared to other world areas is a concern relative to competitiveness. U.S. wage growth and the strength of the dollar are concerns.”
“Pandemic caused inflation. Labor pool for technical help. Long lead times for mold components. Program timing delays due to supply chain delays.”
“Innovation and research.”
“Lack of skilled help available.”
“We are almost out of work. Everyone is going to electric cars.”
“Improve efficiency (smaller losses) for all transmissions, especially for transmissions in mechatronic systems. That means transmission for high ratios with low number of elements. Transmission with very low weight for a referred ratio are in the focus of research and development. Low weight are the key for low cost (when you accept the same production quality and the same tolerances for all parts and elements for transmission).”
“Skiving.”
“Grinding of ring and pinion gears for rear axles.”
“Desire for increased revenue reduces personnel and drives higher usage of early optimization tools.”
“Miniaturization of gears and gear train components seems to be the direction our customers are going in.”
“Electric vehicles powertrain using less gearing.”
“Electrification, not only on automotive.”
“Powertrain electrification is currently a high priority among most automotive companies. The number of gears in electric drives is much lower. PHEV vehicles will have more gears in the drivetrain than current ICE vehicles. My belief is that the U.S. will most likely have 60% PHEV vehicles and only 20% BEVs.”
“Continuity of supply of high quality steel.”
“Demand for automation in all industries. Growth of distribution center supply model. Both have been positive for gearmotor business.”
“Skiving tool application. Impact of future mobility (e-mobility) on the gear manufacturer industry. Business inquiries are good.”
“e-drive technology, Ukraine crisis.”
“Cost of capital equipment, manpower.”
“With the economy slowing, low-volume manufacturing will become the driving force. Low volume is very difficult to automate and typically requires higher skill people to make one or two of a part number.”
“EV madness. China recession. Global recession.”
“New energy sources. How will these affect the transmissions and axles. New materials and heat treatments.”
“New drive systems already under development.”
“Reduced staff may cause delivery shortfalls.”
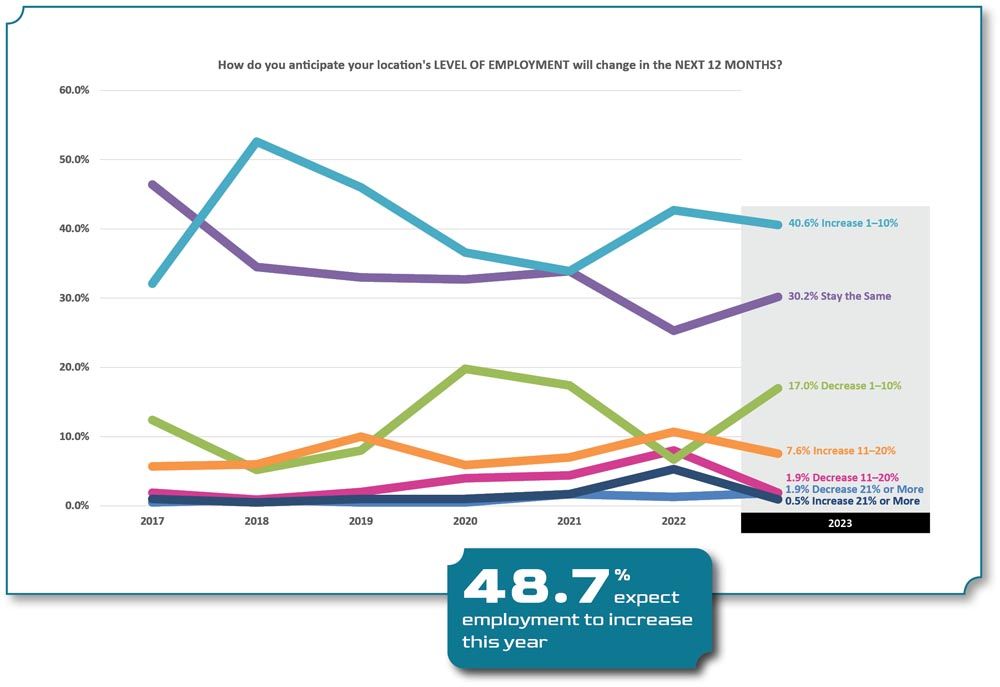
Meeting Today’s Gear Industry Challenges
On the supplier side, machine tool companies are looking closely at e-mobility, energy, sustainability, electrification, Industry 4.0/IIoT to provide new technologies and solutions as gear manufacturing starts hitting pre-pandemic production figures.
“In the near term, we don´t envision significant major shifts in gear manufacturing technology,” said Udo Stolz, vice president of sales and marketing at Gleason. “We are focused today on driving the continuous improvement of precision and productivity in existing processes. These efforts include meeting stringent quality and advanced surface roughness requirements and increased productivity today required by gear manufacturers (particularly EV) to minimize noise, vibration, and harshness (NVH). Hard fine finishing technologies like grinding and honing and, increasingly, skiving, will play an important role in achieving these goals.”
There has been an increasing demand for automation products, in conjunction with gear machine offerings, according to Peter Wiedemann, managing director, Liebherr-Verzahntechnik GmbH. “For sure, even job-shop customers – as well as customers in low-cost labor countries – who did not in the past consider automation, are more-interested than ever. This is most-likely due to the overall global skilled labor shortage in manufacturing. For this reason, a close collaboration with our customers not only includes an automated system, but also the proper training and smart-factory solutions like Industry 4.0, to get started with these turn-key solutions from the onset of a new installation,” he said.
“The greatest challenge is to fulfill the increasing demand for our machines and services. Klingelnberg is perfectly positioned to serve the growing markets for e-mobility and wind power and our production capacities are fully booked,” said Christof Gorgels, vice president innovation and technology at Klingelnberg. “The trends we are paying close attention to are digitization and data driven optimization approaches as well as gear noise becoming a major quality criterion. Besides improved surface finish brings advantages in terms of efficiency which is interesting to improve renewable energy generation and especially wind power.”
“We are going to be quite busy in 2023 with several new projects which is a good thing, but at the same time this brings on challenges that we have been facing the previous year that appear to not be going away,” said Shane Hollingsworth, vice president of sales, Kapp Technologies.
“Supply chains are still stretched out and at times unpredictable which makes scheduling difficult, it’s no secret the industry is looking to solve a skilled labor shortage—mix in unreliable schedules adds to the complexity. We are not seeing one area that is affected, it’s everything from bearings, electronics, controllers, and vessel delays to name a few.”
—Shane Hollingsworth,
Kapp Technologies
An area grabbing significant attention continues to be the EV market.
“We have seen in Europe along with China that this market is further along being accepted and introduced in the market. North America has touched its toe in the water. We see more and more projects being introduced, but still at a much lower production scale. Future energy prices, infrastructure, and legislation will be major influencers for how this market continues to develop,” Hollingsworth said.
Scott Knoy, vice president of sales at Nidec Machine Tool America said the core business of Nidec is electric motors.
“Part of the reason they acquired Mitsubishi Heavy Industries was it gave them a partner to help produce electric motors globally. We recently sent some machine tools down to a Mexico plant for this reason. We’re moving into the market because that’s where the business is headed. There’s a big push for electrification across the board,” Knoy said. “There are basically two types of EV transmissions. You have the external helical gearsets used most famously by Tesla. These are very easy to make the gears, but it’s not as efficient as a planetary set. We’ve recently seen two-stage planetary sets where the weight and overall efficiency is much better. We think they’re going to go in this direction as things progress,” Knoy added.
Even though inflation cooled in the last two quarters of 2022, Helios Gear Products continues to pivot to address employee wages/benefits and product pricing — while keeping their ears to the ground regarding market competition.
“No one has perfect foresight, but the situation does not seem to be fully settled, so our planning (financial, sales, marketing, operations) needs to incorporate an element of flexibility for 2023,” said Adam Gimpert, president, Helios Gear Products.
“Smart manufacturing trends continue to be very interesting, and they have the chance to transform gear manufacturing. I feel this will be a ‘tipping point’ change still years in the future, but I think it’s worth following as it evolves,” Gimpert said.
How is the push toward ELECTRIFICATION affecting your business?
“Not too much at this point. EV is not our direct sector. Our customers are slowly moving towards it, though more and more customers are asking about our environmental, social and governance (ESG) policy.”
“New challanges by reduced tolerances.”
“Decreasing quantities.”
“It still doesn’t affect us.”
“Some negative effect.”
“We are seeing an increase in business from ancillary industries such as mining and mineral processing.”
“I believe electrification is a hoax, so what can it do but hurt everyone?”
“We are using the new motor technology in industrial drives.”
“Minimal.”
“Demand for repair and customization to reduce cost of purchasing electrified products will increase our sales.”
“We have seen units for EVs in quoting much more. At this point it is not yet affecting us, but we do zero automotive.”
“Little to no direct impact.”
“Opens new opportunities in both automotive and genset applications.”
“Increasing product demand in some markets.”
“Awaiting orders that have been quoted. Changes in demand. Accelerating modernization of production. Changes in teeth size range.”
“Our company began investigating opportunities to enter the EV market.”
“It gives us the impetus to prepare for new challenges and thus invest in infrastructure.”
“Zero.”
“Huge, no need for gearing.”
“It is not.”
“Some impact in newer gear designs from OEMs.”
“No effect at this time.”
“Less power installed or divided power = smaller reducer, less money.”
“No effect.”
“Not much.”
“Decrease or set to zero our business.”
“We are not affected by it.”
“No effect.”
“More prototype work from various companies.”
“No real effect at this point.”
“Not at all.”
“Higher costs are offset by less stringent safety requirements in steelmaking and rolling mill plants.”
“Not affected.”
“Too much.”
“Not much.”
“Minimal impact at this stage, but it is a journey that we have now started, and we are now working with small OEMs in development stages.”
“Increase sales.”
“Improving our downtime due to excessive load shedding.”
“None.”
“Not an urgent issue.”
“A little bit.”
“Not applicable. We serve industry markets like mining, cement, sugar, steel, power etc.”
“Outsourcing of gearbox parts.”
“We are finding and pursuing new opportunities by entering into horizontal expansion of our product line.”
“Few new designs in progress. Appears that our customers’ resources are invested in BEV technologies.”
“It has not.”
“Keep same.”
“There are fewer gears in electrified cars, trucks and devices.”
“None.”
“As a supplier of more than just gears it is actually helping us from the standpoint of more business.”
“Very important.”
“Not applicable for us.”
“We see a decrease in the gears we make for diesel engines.”
“It is reducing gear demand in automotive sectors. It is requiring higher cost processing in other areas.”
“Our business is not affected by the push towards electrification.”
“Not impacted.”
“High.”
“Unknown.”
“Negative.”
“For the automotive industry, the mass and the volume of transmissions will become smaller than for cars with an ICE engine. That means the production of transmissions (in kg) will become smaller, the precision and quality will become higher. Research and development will become higher, the quantity will decrease.”
“Massively.”
“Very little.”
“Electrification drives new business. The gears change but are still required and in some cases require additional changes to deal with electrification’s shortcomings.”
“Will cause some decrease in volume.”
“Huge investments are being made in battery plants and electric drive systems.”
“Completed strategic purchase of motor and VFD Companies to support existing gear business.”
“Only slightly.”
“Slightly negative impact.”
“Some impact.”
“Negatively in general, opportunities in specific fields.”
“We are not involved in this segment, so it won't affect our business.”
“No effect.”
“Introducing a lot of new installations to change gas to electricity.”
“New opportunities slightly beyond our capabilities.”
How are you handling and navigating supply chain issues heading into 2023?
“Situation is getting better.”
“2020 was tough. We were able to resolve our supply chain in 2021, thought with some delays in delivering.”
“Reduced staff.”
“Increased capacity in procurement and SQA.”
“Looking for other alternatives.”
“Trying to expand our vendor base.”
“For certain types of raw materials that customers specify we can only offer quotes that are good or 48 to 72 hours.”
“Very little problem.”
“We are developing new local suppliers. to avoid dependence of imports.”
“Working very closely with suppliers and customers.”
“Acceptably.”
“Living with them. Placing larger orders and stocking.”
“We pay our suppliers and vendors in 30 days or less. This typically gives us preferential treatment.”
“Brute force. Larger purchases, higher inventories, more vendors.”
“Diversifying supply base for items which typically didn't need it prior to COVID. Trying to source all components domestically.”
“Supply chain is vastly improved.”
“It’s tough, lead times are hurting our competitiveness.”
“Looking for new suppliers.”
“Our company is developing new business partners.”
“Invest in supply chain to mitigate the drawbacks in delivery as well as quality.”
“Pushing costs back to our customers.”
“Looking at alt sources and automotive supply.”
“Involving key customers more quickly and relying on their strength more often.”
“Adding resources and attempting to utilize sources in same hemisphere as plants if possible.”
“Beefing up inventory and keeping ahead of the curve.”
“New vendor sources brought online in 2022 will significantly decrease supply chain issues.”
“Difficulties to find reliable partners.”
“Adding new suppliers as needed.”
Broadening supply base, sourcing more product from reliable overseas vendors.”
“Lack of components.”
“We are developing alternative suppliers.”
“With support from our customers.”
“Specifically looking into forgings rather than bar stock.”
“Carefully...not sure how to answer this question. The best way is to say adding inventory and ordering earlier to address the longer lead times.”
“Not been a factor.”
“Much longer lead times especially for larger size bearings. Trying to make structural designs more modular and flexible, not constrained to one kind of bearing.”
“By strong SCM strategies.”
“Planning.”
“Supply chain issues are settling down but can’t be ignored.”
“Diversification.”
“We are ordering more and carrying more stock to avoid delays.”
“We are working on it.”
“Finding additional sources.”
“Raw material is the biggest issue.”
“Having more than one partner.”
“Do not see any supply chain issue.”
“Don’t have much issue there.”
“We are not seeing issues.”
“Better now than during COVID, but still a few supply issues.”
“We have been minimally affected. We are a job shop with some room to be flexible.”
“There is no rhyme or reason to some of these issues. Handling it is like an oxymoron.”
“Good.”
“More automation.”
“Trying to move to reshoring supply chains. Offshore has way too many pitfalls.”
“We are making changes internally to better serve our industry and our clients moving forward. We will be vertically integrating more and building up internally held stock so we can control more of our supply base. We are here to support those companies that also wish to become American made and lessen their dependency on foreign products.”
“At the moment we don’t have problems in our supply chain.”
“Supply chain issues are improving.”
“Supply chain management remains a critical component in our ability to not just survive but to thrive in 2023. Multiple sourcing, logistics and attentive inventory control will be the key to insuring material stocks are in house at the right time and quantity to meet our customers’ requirements.
“Purchasing ahead at first sign of issues.”
“No change.”
“Not really a problem.”
“Not well.”
“Increase the in-house capacity!!”
“Find the way to expand existing supply chain network.”
“Buffer management. Nearshoring.”
“Has generally not been an issue.”
“Not well.”
“Difficult.”
“Unknown.”
“Over capacity.”
“Expanding in Mexico to supply North America and Latin America markets.”
“Buying extra inventory.”
“We don’t have any influence on it. We need to deal with it and find alternatives.”
“Proactive progression.”
“Continuous review and monitoring of supply chain situation.”
“Increasing the price of finished products.”
“Higher inventory levels and quoting longer lead times.”
“Finding new sources worldwide.”
“Hope for better subcontracting deliveries.”
“We’re not.”
An Increase in Automation/Robotics
While automation cannot solve ALL manufacturing floor challenges, the opportunity to setup a machine and have it run all day/night unattended is appealing.
“We collaborated with a company at IMTS called AWR (Automation Within Reach) and they make CNC machine tending units. The baskets are a source of anxiety and high cost in many of these applications so they’re moving away from baskets. The AWR unit at IMTS featured a reloadable shelf, two sides, and a robot would work on Side A while the operator is loading or unloading on Side B. This machine would run continuously and only need about five minutes of operator attention per hour. This is what AWR specializes in,” said Knoy.
While automation is not going to help you with a shop’s skilled operations, Knoy said it can take the grunt work out of the equation for activities such as loading, unloading, measuring, part washing, etc. anything that can be integrated into these machining cells. Now management can free up skilled technicians to handle the important challenges on the shop floor.
He believes automation is going to increase significantly in gear manufacturing especially in the Tier 2 suppliers and the job shops. “They’re really starting to see the benefits of these smaller tending machines because they’re very flexible, you can set them up quickly and they provide longer runs.”
Hollingsworth said automation has a significance in Kapp Technologies current and future machine tools due to the diversity of the markets the organization serves. “Clearly, the automotive sector is the leader in automation/robotics utilization and for such we offer machines capable to interface with varying platforms and sizes,” he said.
Liebherr has supplied its own automation—including robotics and other automated systems—for its gear machines since the early 1980s.
“Part of our division of Liebherr has been automating complete factories, and building our own gantry systems, palletizers, and providing robotic integration since the 1970s in fact, said Scott Yoders, vice president sales, Liebherr Gear Technology, Inc. “We see these automated solutions moving from their traditional gear-cutting markets like automotive and truck, into other areas like aerospace, construction, agriculture, and even larger gear cutting applications like wind-power, oil and gas, as well as mining products. We even have interest from some small job-shop customers for automation of even small batch sizes.”
Helios Gear Products has always focused heavily on automated gear manufacturing processes. “Over the past four years, we have dramatically reduced the cost of these systems while keeping them simple and without a third-party integrator, which lowers the bar for manufacturers to benefit from them.
“Robots, cobots, new automation systems, and programming will also continue to evolve, meaning decreased costs and easier implementation. This will allow complete flexibility for manufacturers to easily re-tool cells and workflows to address changing market demands.”
—Adam Gimpert,
Helios Gear Products
The shortage of skilled workforce in combination with more attractive robotics pricing on one hand, and increased capabilities on the other hand, offer some interesting opportunities, according to Stolz.
“By having our own automation division, Gleason can meet the automation needs of our internal manufacturing and offer integrated automation solutions for gear manufacturing machines as well as general machine tools for non-gear applications. In the future, the ease of integration, increased capabilities and improved collaboration will certainly increase the trend for agile production and the use of automation to perform even more complex tasks.”
Gorgels at Klingelnberg is also seeing more automation in combination with the company’s machine tools.
“Whereas this was a focus mainly for mass production such as automotive in the past, today we even see a growing need also for large gears e. g. in the wind industry. So, there is an increasing need for flexible automation systems and systems capable of handling big and heavy parts.”
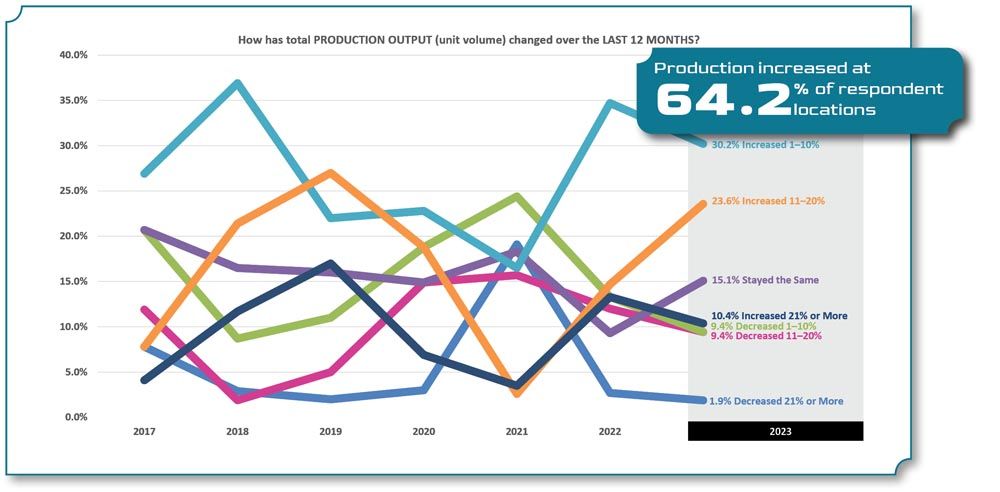
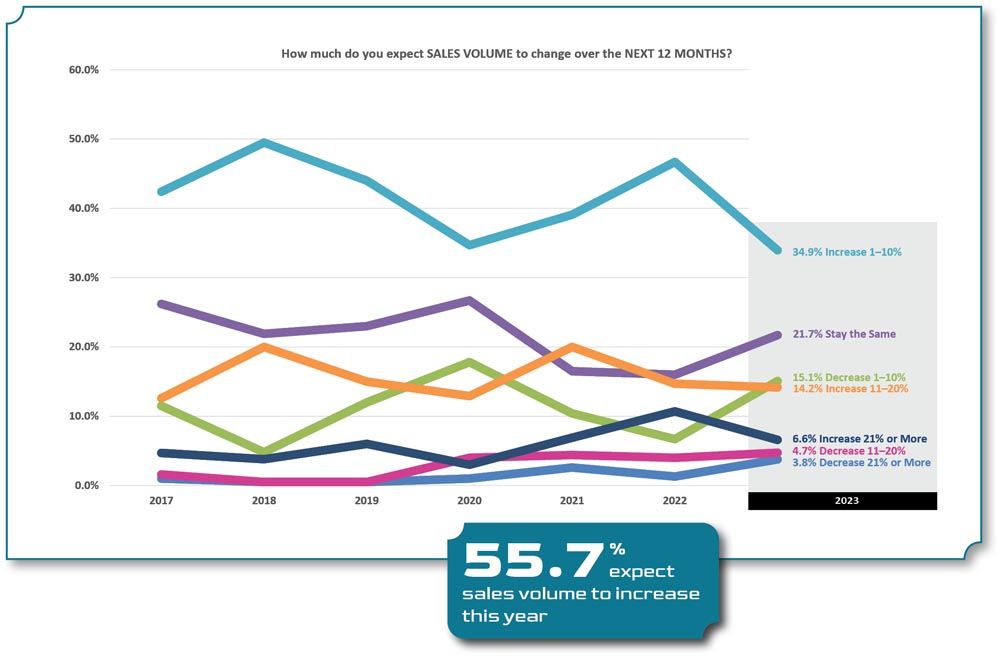
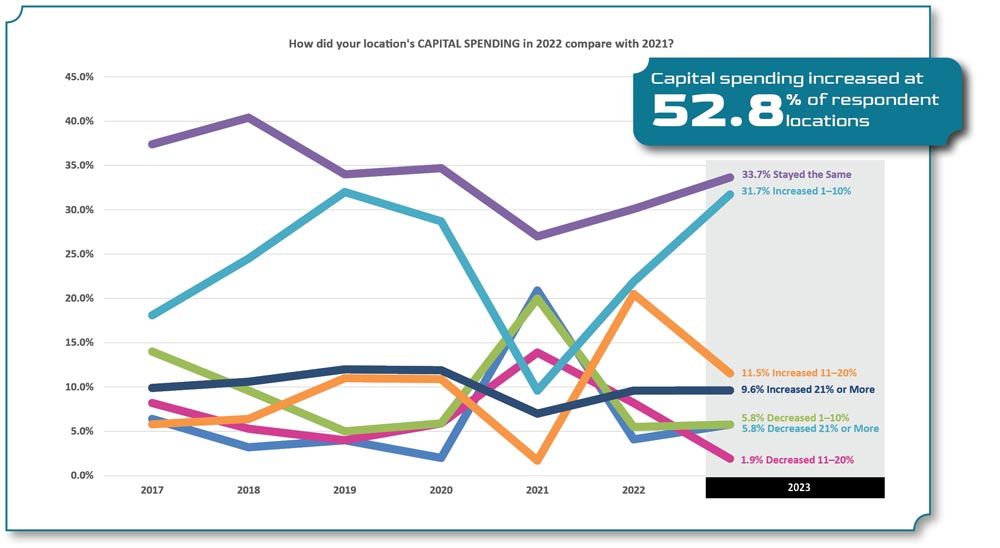
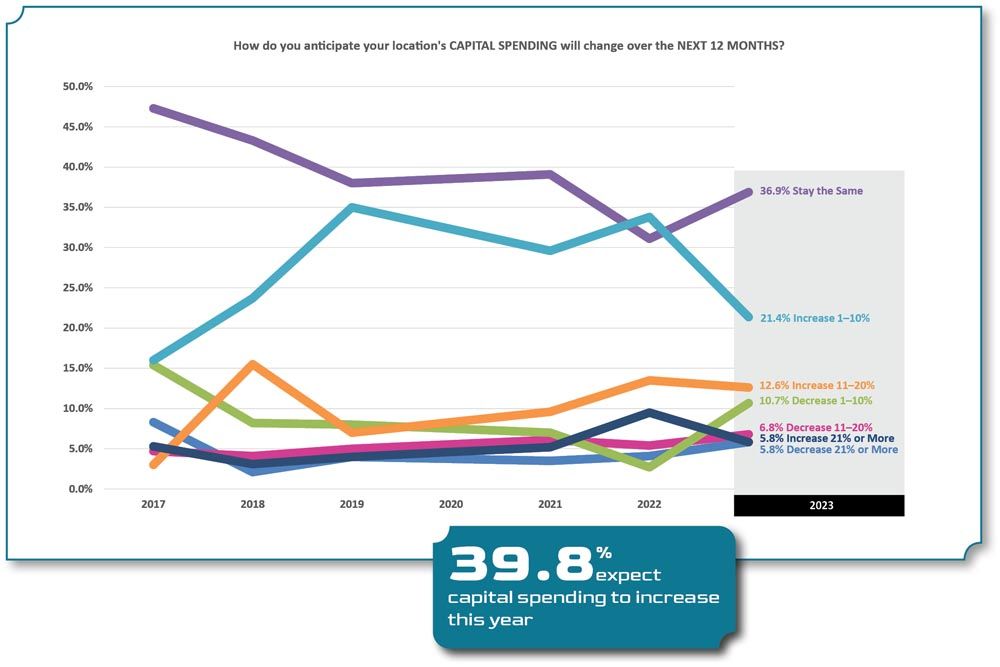
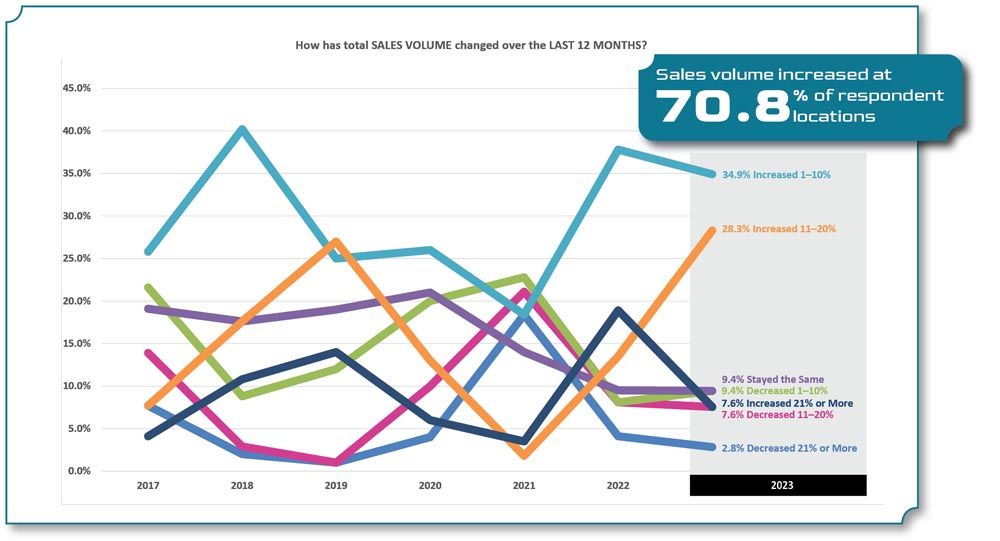
What role will emerging technologies (including, but not limited to IIoT,additive manufacturing, robotics and automation) play in your organizationin the coming years?
“More automation in production.”
“It’s slowly move towards it, but is definitively here, especially robotics and automation. It helps to get more efficient and productive, particularly when it is hard to hire qualified people for a particular task.
“Increased smart manufacturing technologies (process control). work simulation by digital twins.”
“Big role.”
“We are about to start in automation.”
“Not much as we use conventional machine tools and don't have many CNC machines.”
“We are presently doing extensive research and development using additive manufacturing for tooling and inspection.”
“I will be surprised if we are changed from any of these things but we have purchased machines that can be automated.”
“Will be phased in as customer demand requires.”
“IIoT, robotics and automation have limitations when making 10 or less of a part number. 3D printing has a way to go in reducing costs for producing parts for logging, construction and farming equipment manufacturing, modification and repair.”
“Not much.”
“We’re optimistic it will help us from a staffing perspective in particular.”
“Large capital expenditure ideas are still difficult to get approved.”
“Automation will play a role in increased high-volume gearing production. Additive manufacturing already being used for certain non-critical parts and may eventually be used for structural but non-rotating parts.”
“More emphasis and investment.”
“Part of our strategy rests on our inspection products replacing personnel. This should be seen as a positive in the market.”
“They greatly influence and contribute to manufacturing process improvement and target customer change.”
“Not thought much in this line yet.”
“Increased productivity.”
“None.”
“A more significant role.”
“Could be significant with more cost-effective predictive maintenance tools available.”
“Virtual production skills.”
“Increase of competitiveness.”
“Limited effect for now.”
“It will be significant especially as it becomes more cost competitive.”
“Useful for flexibility and energy saving.”
“Not sure at this time.”
“None in the immediate future.”
“Significant.”
“Robotics only chance to compete.”
“Simplify online wear monitoring of difficult to access components and gearboxes. Measurement of torques and loads in scenarios that are difficult to estimate or simulate beforehand to improve existing designs by reducing unnecessary safety margins.”
“Should go for automation.”
“Increasing levels of Industry 4.0/IoT refining databases and statistical analysis. Opportunities to increase automation, add robotic handling is now high on the wish list.”
“We are looking at all options to deal with worker shortages.”
“We are a small jobbing gear manufacturer and cannot possibly afford the new innovative trends but will implement what becomes more useful to our needs.”
“More automation in our product.”
“Zero.”
“Very little to our industry.”
“A small role.”
“Will Support shift of business model from supply chain to demand chain.”
“Extensive digitalization.”
“Not sure, but should be for the better.”
“None.”
“COVID and post COVID have distracted us from innovating.”
“None! Advanced technologies cannot put a machine together.”
“It is my main focus this year to keep adding these types of tech.”
“Important.”
“Additive manufacturing will be a possibility if costs can be decreased and speed improved.”
“We will continue to advance our technology.”
“Important role, especially robotics and automation.”
“Automation needs to increase dramatically to fill the void from a lack of U.S. workers and the need to manage costs.”
“Emerging technologies play a critical role in our ability to thrive in the coming years. Additive manufacturing has made huge strides over the last decade and promises to hit the tight tolerances needed for precision gears in the coming years. We are increasing our utilization of both robotics and automation to remain competitive on a global scale.”
“We are a critical supplier to the robotics industry.”
“Automation may be our only way forward.”
“Robots will become more important.”
“Quite important.”
“Key role. Automation and machine learning will change the way we work and control our processes.”
“Hopefully a significant help to reduce labor shortages.”
“Some, but not a lot. Low per part volumes limit the ability to increase automation.”
“Will require more automation.”
“I believe that lloT will play a greater role on how we manage our production on the shop floor.”
“Additive manufacturing.”
“Already adding IIoT capability to existing products. Much more to do. Automation of our factories already started and to increase in the years to come.”
“Adding more automation.”
“Only slightly playing into our facility.”
“Focus is on digitalization.”
“Minor.”
“All emerging technologies are already installed, with important effects on the product offering and ROI.”
“Not Much.”
“With low volume manufacturing and repair for base industries, IIoT will not help much without an ISO language for sharing information. We already have robotic welding and find it does not help much in lots smaller than four of a part number. We have done different forms of additive for years and it probably will never be a significant portion of our sales. We use CNC machines for lots of 1 to 10 for most of our production. Further automation does not seem cost effective at this time because of setups. We add several new part numbers per week in lots of one to 10. We are working on building machine tools for low volume part machining.”
“Mainly robotics and automation. IIoT in a lower degree.”
“Tooling increased outputs are sought after.”
“Not sure.”
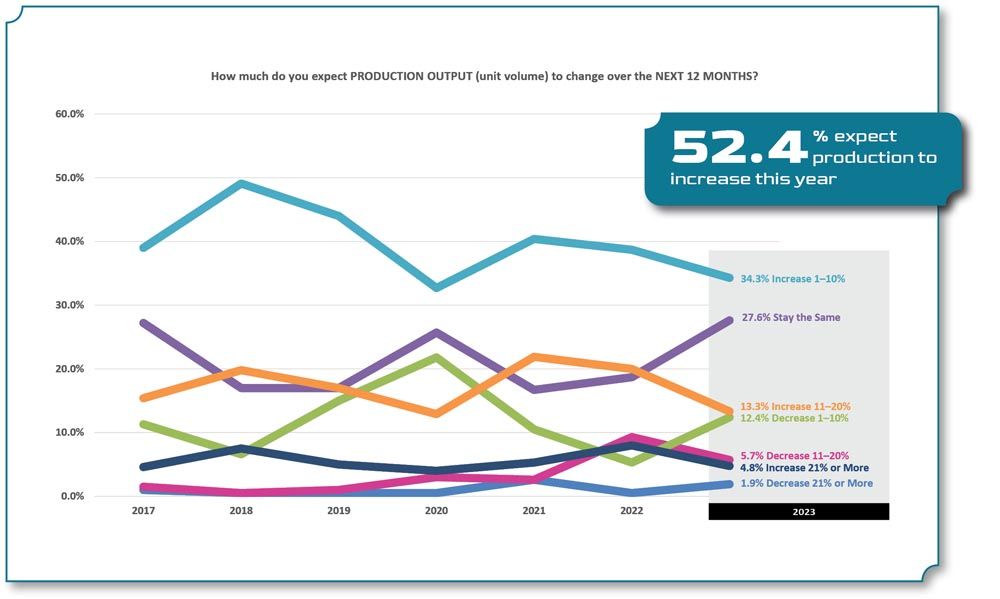
How is your organization addressing the skilled worker shortage?
“Training program. Partnership with schools.”
“Reaching out to universities and offering internships.”
“Employing skilled workers takes longer, but we are able to hire people that we are looking for.”
“In-house training.”
“Incentives for applicants.”
“Ongoing training of current staff.”
“It is a challenge. The new generation of workers do not prefer shop floor jobs.”
“We do not have a problem within our organization. However we hear about worker shortages from our suppliers.”
“We have a few good people.”
“We are buying more than producing.”
“In-house training.”
“Hiring young, inexperienced people. Looking for a diamond in the rough.”
“Internal training.”
“Participating heavily and sponsoring many different internships through local high schools and apprenticeships through local community colleges.”
“Focus tasks requiring skilled work and allow low-value-added work to be performed by unskilled labor.”
“Collaboration with local vocational programs, increased scope of co-op program, second chance employment in certain cases.”
“Reaching out to community colleges and four-year universities.”
“Suffering.”
“We kept our workforce.”
“Our company strives to hire new young people and at the same time spends time passing on skills.”
“Tapping into industrial training institute.”
“Hire in advance.”
“Grow talent inside our business.”
“Importing workers from other regions.”
“Job fairs, tapping into trade schools, hiring more in-house HR support.”
“Shower them with amazing benefits as we have done in the past. Best way to keep skilled/good workers is to invest in them.”
“More modern machine to counter lack of know-how or intelligence.”
“In-house training of new machinists.”
“Using recruiters, more classroom training, apprenticeship program.”
“Not addressing due to reduction of production.”
“We are not affected by the skilled worker shortage.”
“Hiring offshore.”
“Increased starting pay, going to job fairs.”
“Hiring unskilled and training, partnerships.”
“By retaining skilled laborers.”
“Hope.”
“Always shortage.”
“Constantly on a recruiting campaign for young technicians and skilled workers.”
“Automation.”
“We are doing on-the-job in-house training.”
“We are fortunate to have a good labor pool.”
“Hiring and training in house.”
“Working as best as possible to get new employees into the mix. So often, they do not like working in a volatile manufacturing environment.”
“We train and educate.”
“Automation.”
“We have permanent employees and have a very strong training team to bring unskilled workers to skilled level in no time.”
“Longer lead times.”
“Not Well!”
“Always looking and willing to hire young talent, we work with the local college.”
“We are letting the dust settle on this one.”
“I have a rotating internship and apprenticeship program I have year round with local high schools with manufacturing programs.”
“Training young people.”
“Going to have to try in-house training before all the skilled workers are retired.”
“Our systems are easy to operate and able to be entirely automated, which allows companies to increase productivity despite labor shortages or lower experience labor.”
“We make internal training.”
“Continued hiring, cross training and employee development.”
“The skilled labor shortage remains in the forefront of our efforts to grow in 2023. First, addressing our current workforce to minimize poaching from a competitor and second, increasing our efforts to train from within. By improving pathways to advance within ourorganization we provide an environment that retains our skilled labor force and attracts talentfrom outside.”
“More training internally.”
“We can’t find any.”
“Engage more old people (with high know-how!) to work longer than normal.”
“Reinforced benefits for retainment and new employees.”
“Not very well. Trying to find trainable workers, which is difficult.”
“Additional training of our unskilled workers through the local community college.”
“A big problem.”
“Apprentice programs for skilled trades have been re-started in the last four years due to the shortage of skilled tradespeople in the area.”
“Continually hiring due to turnover. Recruiting for and providing apprentice program for skilled trades with local community college.”
Automation.”
“Being more flexible on working hours and in-house training.”
“Struggle at this time.”
“More efforts in job opportunity promotion.”
“Training and selecting manpower interested in the gear industry.”
“We are increasing on-the-job training.”
"Training internally.”
“Haven't seen any changes. Still hoping for better results.”
“We’re not.”
A Focus on Training and Workforce Development
Workforce development and training continues to make headlines—not just in gear manufacturing but the entire industrial sector.
Gimpert plans to focus even more time and energy on internal training in 2023.
“Maintaining existing strong personnel is key to successfully weathering any future industry disruptions, and I feel training must be part of the solution. Interestingly, online training resources continue to expand, so connecting the dots between these resources and employees who could benefit is the work to be done,” he said.
Klingelnberg’s main goal is to ensure skills to support customers with local personnel in the different time zones and without experts travelling.
“We have increased our online training and support efforts for customers and our own colleagues,” Gorgels said. “We keep a wide network with universities, innovation hubs and local organizations. In combination with our apprenticeship program, we can attract talent even in a challenging environment.
The key in the future will be the increasing need for data collection not only for measuring machines but more and more with our machine tools also. “This goes very much in line with an increasing focus on software development for digitization to support our customers moving forward. This increases the need for data handling and evaluation so the need for new skills in the workforce on the shop floor comes naturally,” he added.
Workforce development is a win-win situation, according to Stolz at Gleason.
“It helps Gleason to continue its many years of industry leadership, while at the same time ensuring career development opportunities, productive new skills and, ultimately, a successful career path for all our employees. The challenge is finding people with the right skills and qualification. Our internal qualification programs, including apprenticeships, training on the job, digital and on-site learning and/or leadership development programs, all contribute to a better and more qualified workforce.”
The Gleason Gear Trainer concept (started as Home Trainer during the pandemic) is providing high-level education for thousands of participants every year free of charge.
“With Gleason`s unique expertise in ‘design-manufacturing-inspection’ we have the bandwidth to provide in-depth know-how during seminars, on-site courses or through the highly regarded Gear School. Our employees greatly benefit as well from these programs,” Stolz said.
Liebherr has invested heavily in its Training Center in Kempten, Germany, to formally train operators, technicians, as well as mechanical and electrical maintenance personnel, with both in-person and online formats.
“We believe it’s necessary to help the introduction of these new skillsets in the gear machining workforce,” Wiedemann said. “For that very reason, Liebherr has invested heavily in our Training Center to formally train operators, technicians, as well mechanical and electrical maintenance personnel, with both in-person and online formats.”
Field service is an area where Nidec is focusing its development efforts.
“Right now, we have 16 field service engineers so we’re well staffed for what we do, but we’d like to get a couple younger people on staff and train them up. We’re partnering with some of the local colleges here in Michigan to find new talent but it’s still a huge challenge.”
—Scott Knoy,
Nidec
"Mechatronics is the area of study that is most appealing, however, we’re not seeing the interest in our line of work. They typically want to work at GM or Ford. The travel is another issue. Many of these field service engineers are road warriors and they travel more than the sales team, it takes a certain breed to be on the road across North America this much,” Knoy said.
Hollingsworth believes there’s no short-term solution for the skilled workers crisis.
“States and local municipalities are making more and more investments which is a good start, but these need to grow on a larger scale to address the larger problem. The machines being built today are being tasked more to help alleviate this pressure, time will tell how far this evolves the controller’s and software’s of the future,” Hollingsworth said.
Kapp headquarters offers a nice apprenticeship program and the company has started offering summer internships where future employees are brought to the United States for eight weeks.
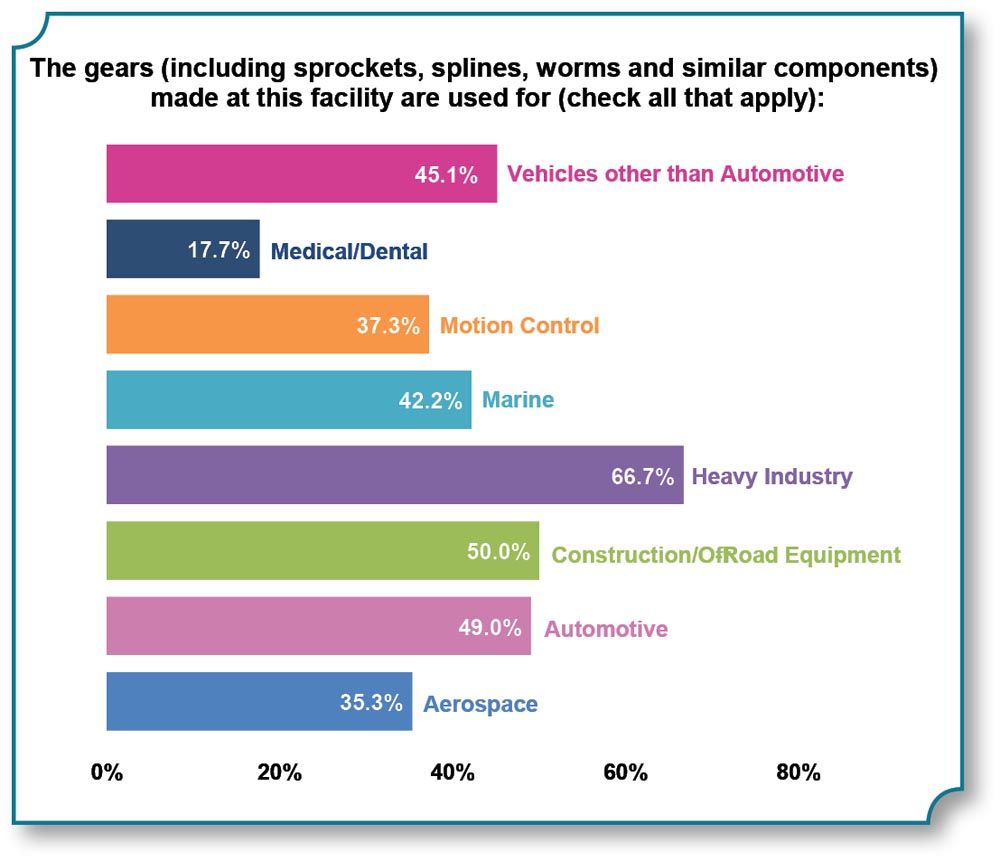
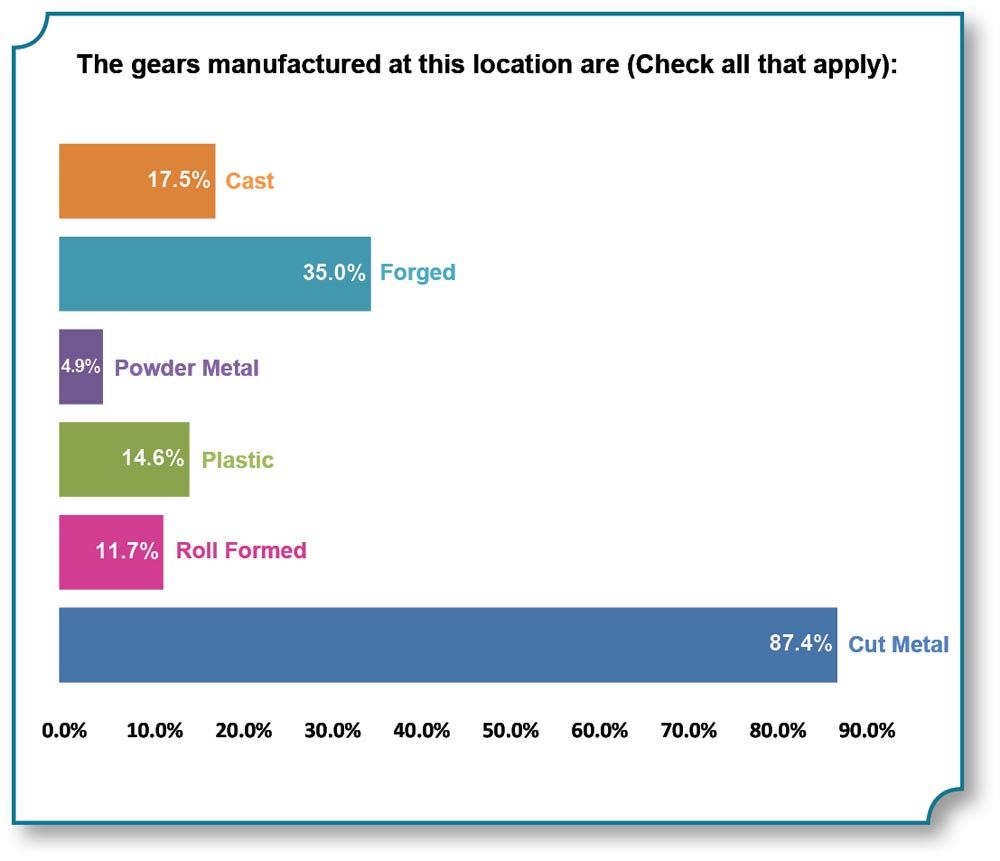
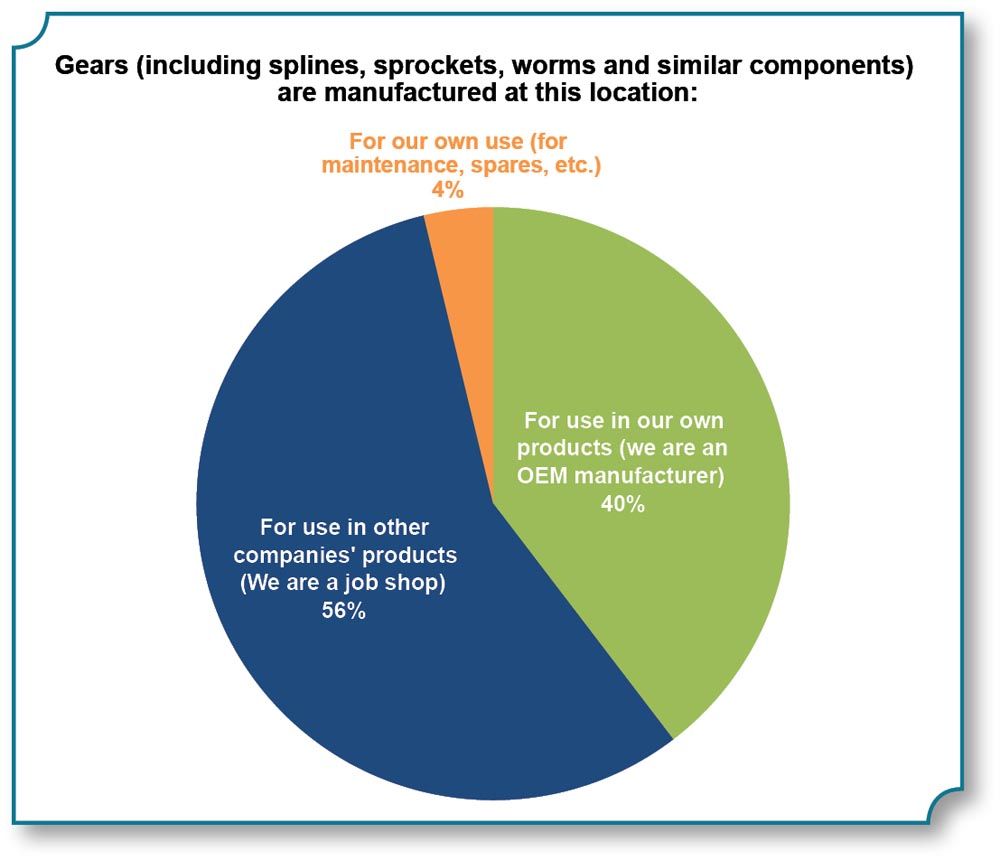
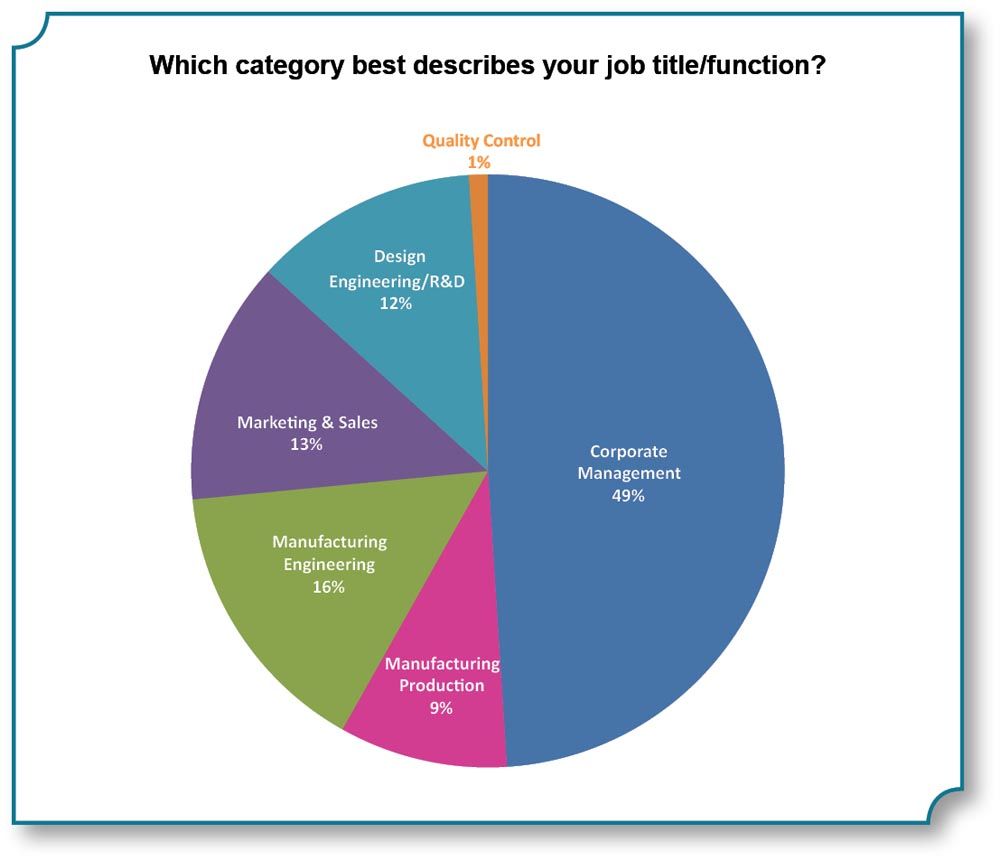
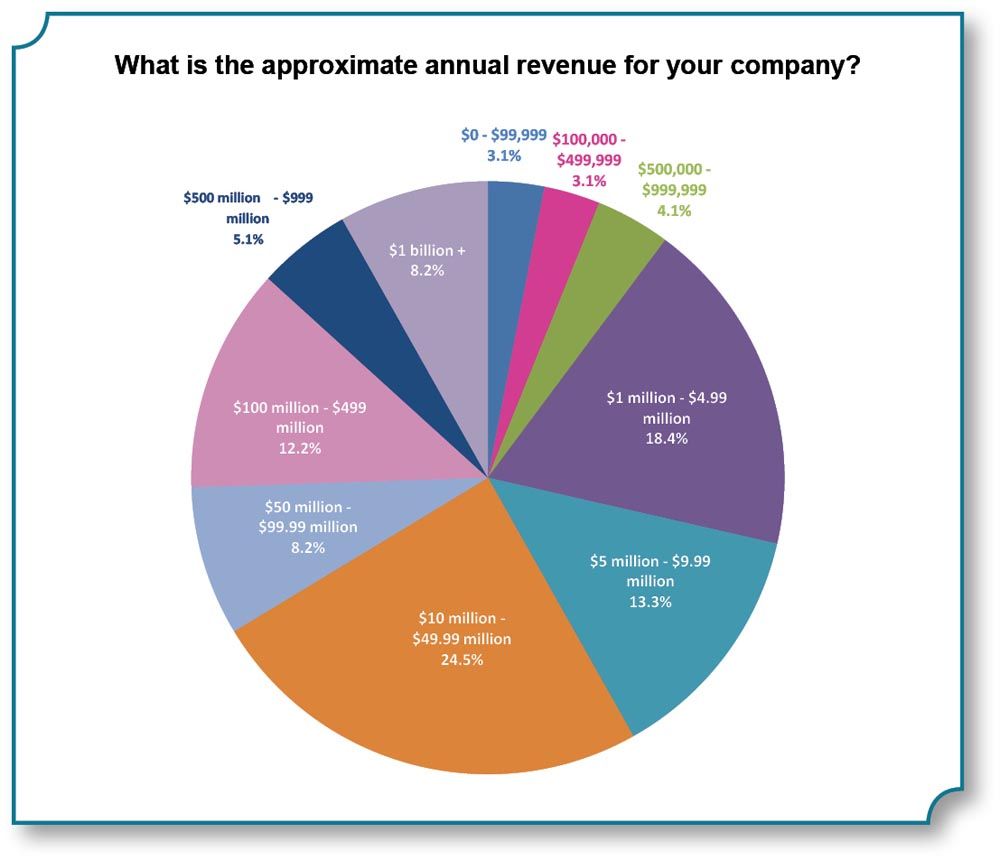
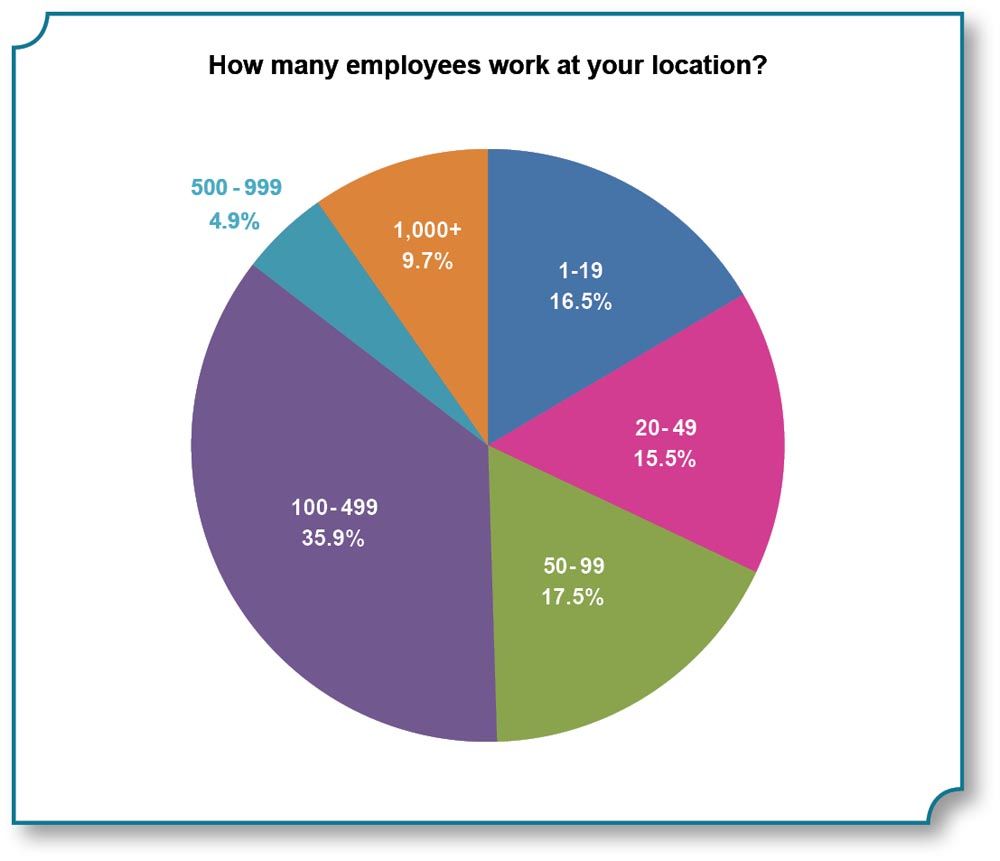
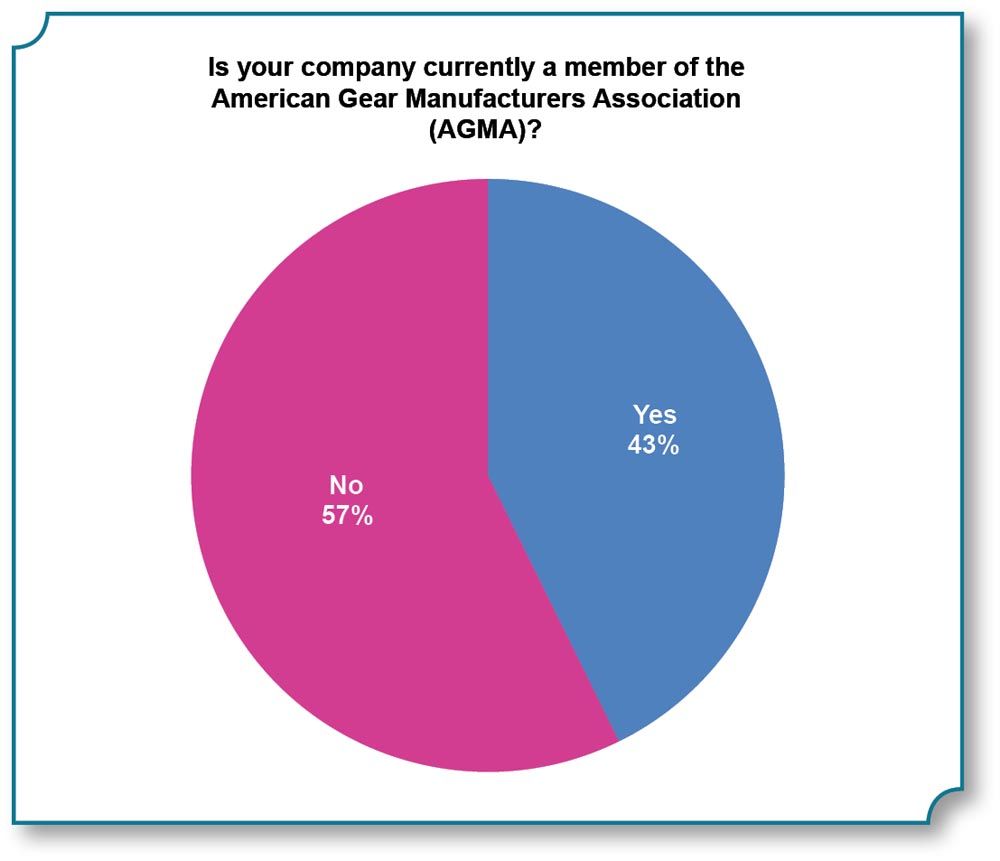
How Will Things Change Moving Forward?
The gear industry will clearly have an increased level of automation moving forward, and data-driven Industry 4.0 will have a profound impact on machine tool digitization.
“We will also see a trend toward larger gear cutting demand, owing to a worldwide energy crisis developing since the past 1.5 years (wind, oil, gas),” said Wiedemann.
“Furthermore, the electrification trend will see increased demand in our high-end gear machining solutions like Hobbing with ChamferCut and DFT Gear Grinding. We see this automotive segment continuing to increase the demand for sophisticated solutions... Not just tooling, clamping, and automation, but also the software, mathematics, and know-how for the topological modifications required for noise reduction in gearboxes,” Yoders said.
Quality requirements and cost per piece are still going to drive future gear design and manufacturing strategies, according to Stolz, adding that the tailored solution which fits best to achieve the task will succeed.
“Due to the electrification strategies in automotive, the overall number of gears will be lower, but more sophisticated and complex. Since manufacturing solutions alone will not be able to guarantee success, integrated design, manufacturing, and inspection solutions in a Closed Loop system will be important keys for future success.”
—Udo Stolz,
Gleason Corporation
"As the design parameters and the cost per piece for specific manufacturing processes are already set during the design phase, it will be mandatory to provide gear and transmission designers with some substantial manufacturing know-how,” Stolz said.
“With the increasing need for electric vehicles, gear noise becomes a big focus. This increases not only the quality requirements for gears but also the need to understand gear noise as a new quality criterion. We will see an increasing number of roll testing systems in the industry within the next years,” Gorgels said.
The smart factory floor, according to all the participants interviewed, is coming and will offer wholesale changes in terms of technology and utilization.
“Smart manufacturing will continue to trickle into the industry while automation remains a leading solution, albeit with more “intelligence” (IIoT) than in the past,” said Gimpert. “20th century manufacturers will slowly die away, and 21st century manufacturers (clean, digital, human-centric) will lead new business, acquisitions, and hiring.”
Editor's note: Read more in-depth analysis on the State-of-the-Gear-Industry at geartechnology.com