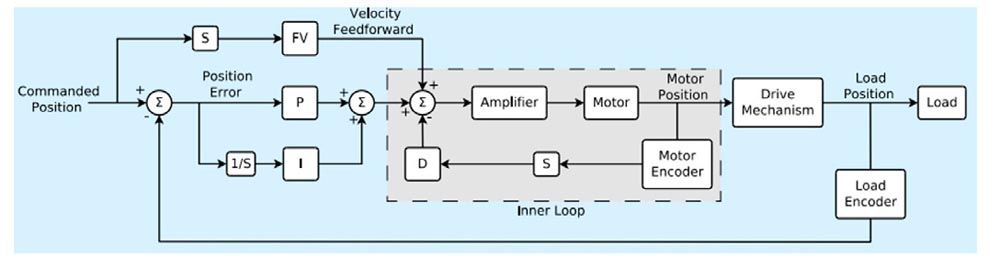
Figure 4—Standard dual Loop PID control block diagram (courtesy of Galil Motion Control).
Position errors can also be reduced with a higher gear ratio by increasing resolution and therefore minimizing the effect of gear backlash. The increased resolution is due to finer control of the system’s output for a given input. With more teeth on the gears, the system can make smaller and more precise movements, resulting in improved resolution. This finer control helps minimize position errors. Lastly in a PID control system, higher gear ratios can enhance the overall rigidity of the mechanical system and improve the stability during position control, minimizing the impact of vibrations or external disturbances that could introduce errors.
Backdrivability for Safety and Human Interaction
Safety is a primary concern in robotics. Accurate position control ensures that the robot operates within its defined workspace and avoids collisions or accidents. Robots that work alongside humans require agile position control to ensure that they do not pose a safety risk to human operators. As such, backdrivability (i.e. low impedance system) is essential for mechanical compliance to be driven from the load side, managing contact with humans and undefined objects (Figure 5, ref 4). The backdrivability is characterized by its mechanical impedance consisting of the gearbox inertia, stiffness, and losses due to backlash and friction.
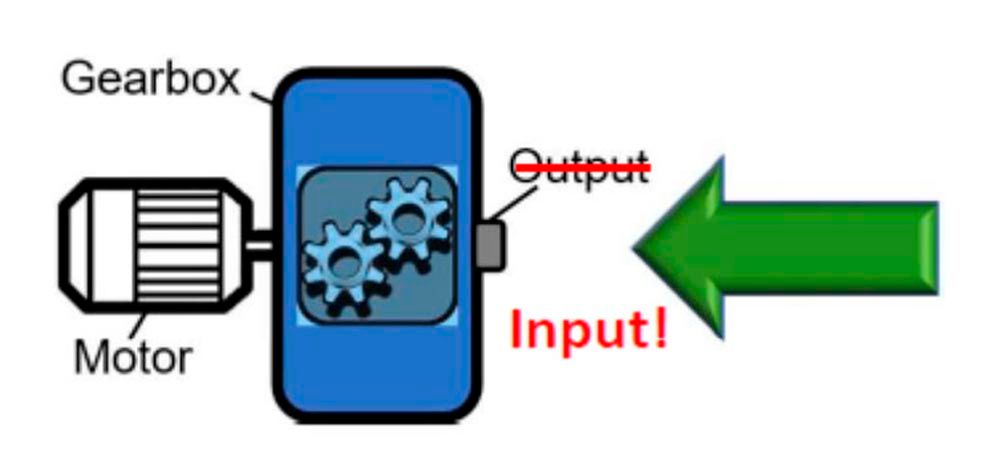
Figure 5—Backdrivability: Mechanical compliance from the input side.
Discussion
For most industrial robot applications, gearing backlash is an issue robot manufacturers have been able to work around by using strain wave gearing (also known as harmonic gearing), introduced in 1957, and later, cycloidal drive or cycloidal. Strain wave gearing uses a flexible spline with external teeth, which is deformed by a rotating elliptical plug to engage with the internal gear teeth of an outer spline, as shown in Figure 6. These drive systems provide compactness, relative light weight, high gear ratios, and high torque capacity.
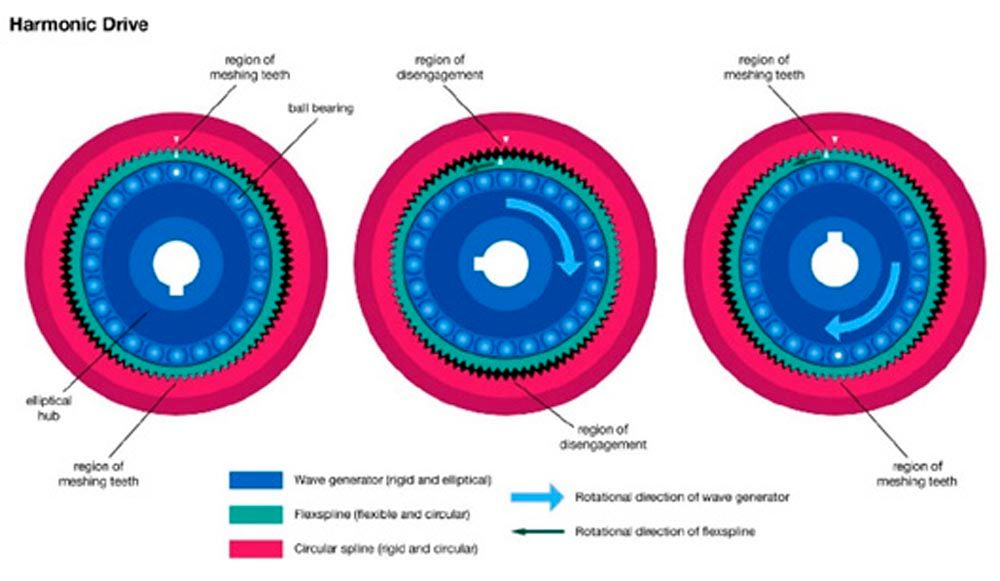
Figure 6—Strain wave gearing (harmonic drive).
John Tuohy (manager, business development at FANUC America) mentioned that FANUC, with their gear partner Nabtesco, has been able to produce robots with less than half of an arc-minute backlash under load and positioning precision of 0.02 mm at high velocity using large gear ratios ranging from 100:1 to 300:1. The challenge for gear manufacturers in the industrial robot market remains the predictability, limitation of material to minimize weight, size, inertia, and longevity of gear components.
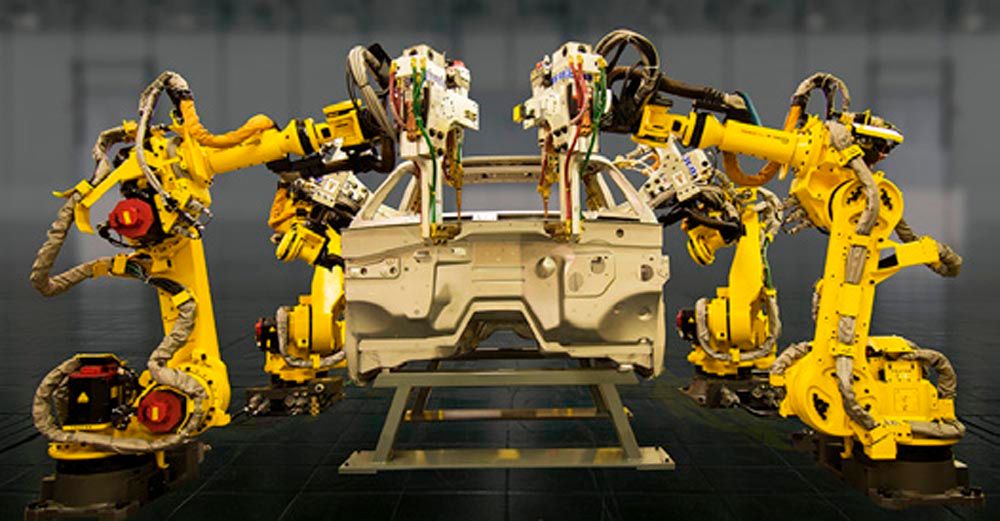
Figure 7—FANUC industrial robots.
The advent and the significant growth in the next 8–10 years of human-centered robots (humanoid and collaborative robots) has a significant impact on how the mechanical drive should be integrated. In conventional industrial robots, robustness and performance are linked to the robot’s ability to maintain its position trajectory under an external disturbance force. In contrast, in human-centered robotics, the close interaction between robots and humans requires low forces when there is a deviation from the position trajectory. Therefore, they require low mechanical impedance or backdrivability for safety reasons, as discussed in the background section “Backdrivability for Safety and Human Interaction” above. In addition, human-centered robots are required to operate in an unpredictable environment with an undefined sequence of operations/tasks. The table below summarizes the differences in gear drive requirements and challenges for gear manufacturers for industrial and human-centered robots.
| Industrial robots | Human-centered robots |
Gear General Requirements | - High torque density
- High gear ratio
- Controlled industrial environment
- High speed and accuracy
- High volume production
- Deterministic system
- Predictability, reliability, and maintainability
- Position controlled
- Minimal interaction with humans
| - Low torque density and gear ratio
- Backdrivability / low mechanical impedance
- Position and force control
- Flexibility in task performed in less deterministic AI controlled space
- Interaction with human and multiple decision point
- Unpredictable environment
- Low noise and vibration
- Multiple configuration and fragmented market
- Position and force controller in proximity of humans
|
Gear Challenges | - Lower manufacturing cost
- Material development for longevity and maintainability
- Predictive reliability
- Production capacity
| - Lower weight and size
- Backdrivability
- Predictable backlash and hysteresis over product life and variable environment
- Availability of data to accommodate environmental errors
|
We can see that gear backlash is one of the most important elements in robotics systems, but near-zero backlash may not be sufficient to meet the future need in human-centered robotics.

Figure 9—Compound planetary traction system inside the Archimedes drive.
New technologies, such as the Archimedes Drive from Innovative Mechatronics Systems with a Wolfrom drive and traction rollers (see Figure 9), are at the forefront of zero-backlash innovation. Thibaud Verschoor, founder at IM Systems, recognizes that true zero backlash is difficult. Engineers working on servo applications generally consider “zero backlash” to be between 0.5–5 arc min. (Ref. 6). Verschoor offers the following classification for backlash accuracy:
- Micro accuracy:
- Increased accuracy:
- Standard accuracy:
The unpredictability of human-centered robots will require sophisticated integration of electromechanical hardware with artificial general intelligence to achieve the connection between a human’s physical and cognitive behavior. Within the human environment AI database, the human-centered robot will evolve and learn from the information collected from the environment. These parameters, such as backlash, are needed to modify the motion control models from the initial build throughout its life, as components wear out and patterns and rules of operations change. As Robert James, vice president, product technology at Motus Labs mentioned, “The software will be driving the gear drive robotics joint. With AI, we will have to be able to predict drive degradation, feedback errors, and maintenance issues. The essence of the gear drive will be to understand the DNA of the gear profiles, its backlash, and its performance over time. We are the widget of the software industry.” The drive backlash can no longer be considered an error in the system that will be compensated for, but instead, it should be integrated into the future human-centered robot blueprint.
As human-centered robots become a motion-control computing problem, calculating errors from backlash range becomes the Achilles heel of drive systems. With computing power increasing drastically and the ability to collect large databases of data during gear manufacturing, the next generation of gears will have to go beyond backlash range to cognitive gear modeling. In this approach, the gear manufacturer and robot designer recognize that each gear is part of a more complex AI control system model, and each can be characterized with its own DNA, from the embryonic material science to the final manufacturing process and assembly. The proposed future cognitive gear model recognizes the backlash and mechanical impedance in the design and fabrication but also serves as an evolving function within the human-robot software model.
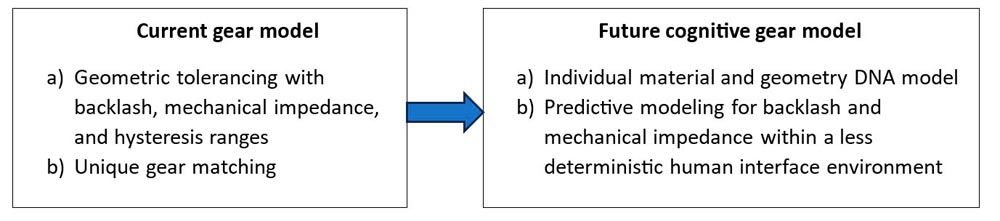
Figure 10—Proposed future cognitive gear model.
Conclusion
Despite recent progress in the range and accuracy of robot sensors and more powerful computing controllers, drive backlash remains one of the most significant problems in robotics. This is especially true for human-centered robots where gear ratios are generally lower than the industrial robots and backdrivability is required for safety. Gear backlash causes errors in the position and force control loop that affect the robot’s mechanical impedance, generate noise, lose efficiency, and induce vibrations. From micro to standard accuracy gearboxes, the backlash value is sold with a zero to max range where the lower and upper limit might provide a significant difference in the motor/gear PID model. To further compound the issue, the backlash range changes over time due to wear in materials, lubricants, and environmental conditions. The environmental conditions and usage of human-centered robots are much more highly unpredictable than industrial robots. Backlash remains an unknown factor that the present robotics software can’t insert into its motion-control model.
Today, robotics is a computer problem but “transmissions are where the problem starts” (Ref. 9) as Sangbae Kim, director of the Biomimetic Robotics Laboratory and a professor of mechanical engineering at MIT said. To play a major part in the next 10 years of human-centered robotics, the mechanical drive industry needs to develop a means to leverage next-generation computing power with a large AI database and capture gear digital mechanical DNA to allow computer modeling to account for errors in backlash and cognitive AI gears. These new gear drive digital models should be augmented by the research and development of new lighter anisotropic materials, a smaller drive envelope, and performance modeling in unpredictable environments.
The global robot market is expected to grow 50-fold in the near future. Increasing production capacity with the integration of intelligent digital technologies into manufacturing and industrial processes, such as IoT networks, AI, robotics, and automation will maximize operational returns and lower the cost of industrial robot’s drives.
agma.org/event/backlash-and-the-future-of-robotic-applications/
Lemire.PBDConsulting@gmail.com

Contributors
Special thanks to the following contributors to this article (in alphabetical order):
Mary Ellen Doran, AGMA Director Emerging Technology
Pablo López Garcia, Robotics & Multibody Mechanics Group, Vrije Universiteit Brussel
Kel Guerin, Co-Founder, READY Robotics
David Harroun, Vice President, Helios Gear Products
Robert James, Vice President Product Technology, Motus Labs
Robert Kufner, President and CEO, Designatronics Inc.
Jason Lazar, Nabtesco
Tim Pirie, Chief Technology Officer, CGI Inc.
Denis Rancourt, Professor in Bio-Mechanical Engineering, Université de Sherbrooke
John Tuohy, Business Development Manager, FANUC America
Thibaud Verschoor, Co-founder and Head of Product, Innovative Mechatronics Systems B.V.
References
- International Federation of Robotics World Robotics 2023 Report: Asia ahead of Europe and the Americas, September 26, 2023.
- Eliana Giovannitti, Sayyidshahab Nabavi, Giovanni Squillero, Alberto Tonda, Journal of Intelligent Manufacturing 2022, 33:1921–1937.
- Galil Motion Control: Advanced Control Techniques for Real World Drivetrains June 2017.
- “High-ratio planetary gearboxes for the next robot generation,” AGMA—2022 Fall Technical Meeting (FTM) Dr. Ir. Pablo López García.
- “Factors influencing actuator’s backdrivability in human-centered robotics,” MATEC Web of Conferences 366, 01002 (2022) Pablo López Garcia.
- IMSystems White Paper – Drive Precision in Robotics: Tackling the Issues of Backlash and Lost Motion, September 6, 2023.
- “On the Potential of High-Ratio Planetary Gearboxes for Next-Generation Robotics,” Pablo López Garcia, Power Transmission Engineering, April 2023.
- RoboBusiness Conference October 18-19, 2023 Santa Clara Convention Center
- RI Seminar: Sangbae Kim: Actuation, structure and control of the MIT cheetah robot, October 2013.