Machine and Tool Concepts for Contract Manufacturing
Liebherr solutions enhance flexibility, accuracy, and efficiency at SPN Schwaben Präzision
The Swabian transmission and drive solutions manufacturer SPN Schwaben Präzision Fritz Hopf GmbH manufactures gearboxes, gears, and drive systems according to individual customer requirements. (Swabia is a region in southwestern Germany known for its engineering and manufacturing excellence.) SPN relies on various machine and tool technology from Liebherr-Verzahntechnik GmbH.
SPN was founded over 100 years ago in Glashütte, Saxony as a workshop for contract gear manufacturing. After the war, the company moved its headquarters to the Swabian town of Nördlingen and initially manufactured precision gears for watches. Today, around 300 employees there develop and manufacture gearboxes, gearing components, drive systems and components for drive technology and mechatronics. “We manufacture customer-specific drive components and gearboxes with the highest precision,” says Stefan Ohmüller, head of production technology at SPN. The company is continuously investing in the expansion of its production capacities and over time has developed into a true one-stop shop for gears. The wide variety of parts is now being manufactured, among other things, on seven machines from Liebherr-Verzahntechnik GmbH. The company also purchases tools and clamping devices from Kempten.
Advancing Gear Shaping Technology for Increased Efficiency
For many years, SPN has been using Liebherr gear shaping machines for workpieces with diameters of up to 300 mm. To absorb production peaks and increase capacities, in 2018 the two existing machines for gear shaping were supplemented by an LS 180 E, which offers a range of benefits: its shaping head is equipped with an electronic helical guide that facilitates frequent workpiece changes. The helix angle can be easily and continuously adjusted via the clear user interface of the LHGearTec. This allows it to machine a wider range of parts and also reduces setup times. Automatic loading allows several machines to be operated at the same time. “Due to our different quantities, we still need machines that can be operated manually, but at the same time place great value on multi-machine operation. Automation helps us here,” explains Ohmüller.
Gear Grinding Machines for High Profile Accuracy
SPN relies on the LCS 150 generating and profile grinding machine from Liebherr-Verzahntechnik GmbH for the high-quality requirements associated with flank grinding. Among other things, this offers numerous advantages for job shops: both CBN and corundum tools can be used, an integrated device quick-change system and automatic clamping fixtures reduce setup times considerably, and automatic loading by a ringloader with two stations supports the multi-machine concept. The LCS 150 can machine even the smallest drive pinion with a module of 0.4 with the highest profile accuracy. SPN was so satisfied with the performance that they purchased another gear-grinding machine, the LGG 280, in 2022.
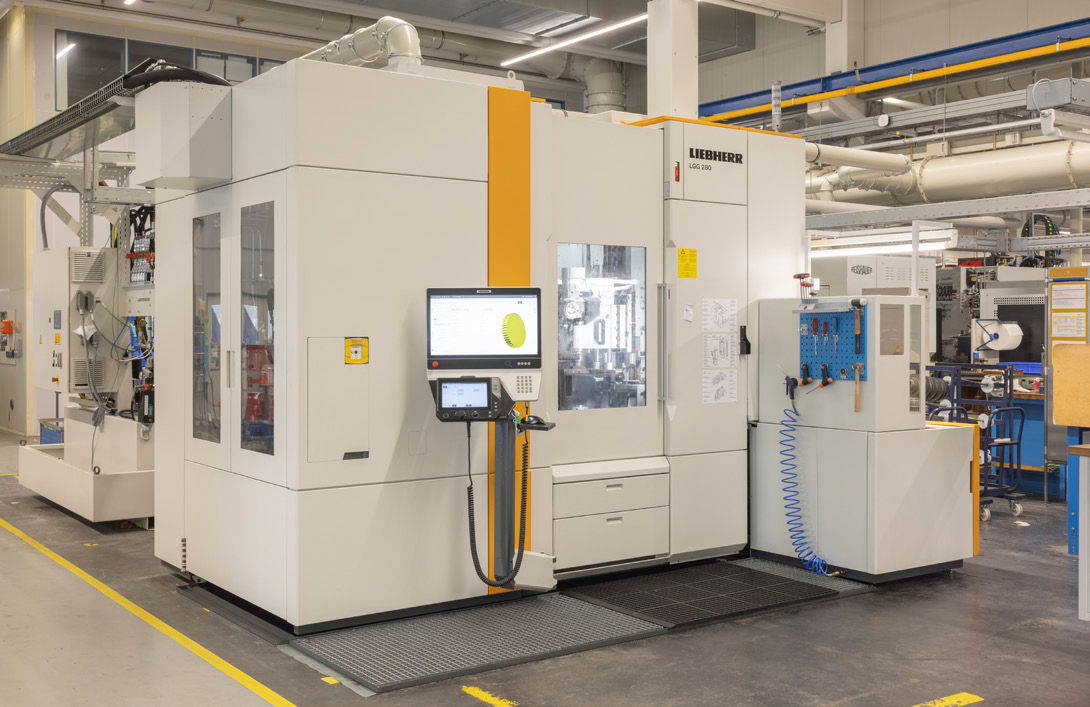
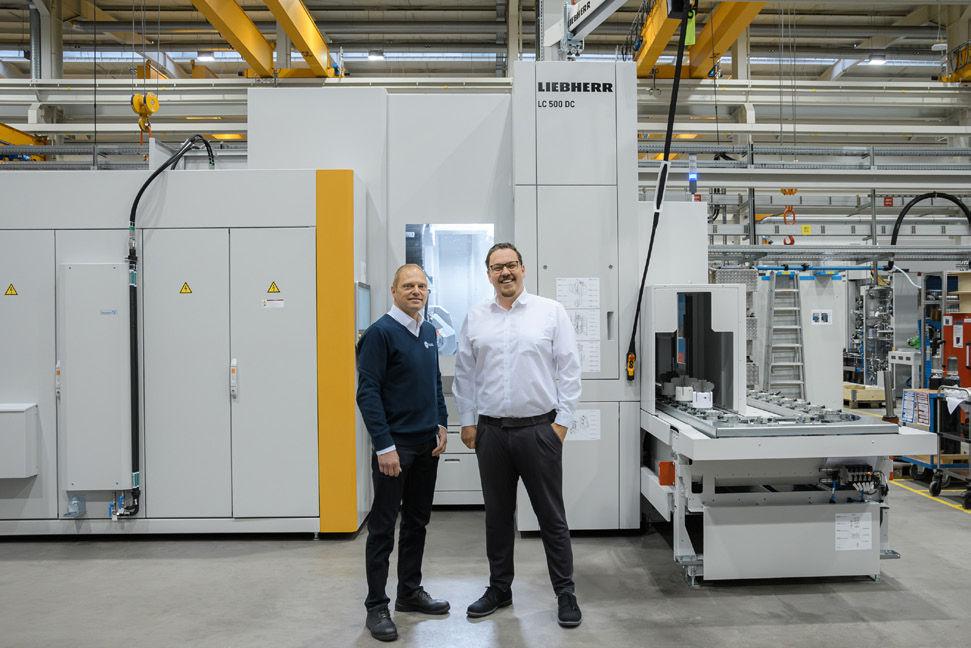
Gear Hobbing Machine with Integrated Chamfering Device
Due to increased order volume for a large agricultural machinery manufacturer, an LC 500 DC was added to SPN’s machinery in April 2024. The decisive factor in their decision to purchase it was the integrated machining unit, which combines two chamfering technologies in one machine—a special feature of the new generation of machines. In addition to the fast, economical ChamferCut process, FlexChamfering—chamfering with common end mills—is particularly attractive for SPN, as it is suitable for small batch sizes. “As a specialist in customer-specific solutions, we often have smaller batch sizes and a large variety of parts, as we have to react very flexibly to customer requirements. Now we can produce defined chamfers with low tool costs, especially in small quantities,” says Ohmüller. The flexible LC 500 DC enables a wide range of gears up to a diameter of 500 mm to be manufactured with cleanly reproducible results.
Everything from a Single Source for Smooth Processes
SPN uses Liebherr tools on all three shaping machines and takes advantage of Liebherr-Verzahntechnik’s convenient pick-up service to have them sharpened regularly. SPN can keep an eye on the wear behavior of the shaper cutters thanks to the supplied simulation. “This means that we always know which root diameter the tool is currently making and can adjust the corresponding machine settings,” explains Ohmüller. On the gear grinding machine, the flexible SECLA segment clamping arbor ensures short setup times. “Machines, tools and clamping devices from a single source provide us with a high level of production reliability,” enthuses Ohmüller.