Figure 2—Jens Haag, Managing Director Zahnradfertigung OTT GmbH & Co. KG (left), and Patrick Henes, Head of Quality Assurance, in front of the loaded P 152 precision measuring center.
Modern Challenges
After coronavirus, the energy crisis, inflation, and now the threat of recession, Haag stated that the company is primarily hoping for calmer waters again.
“We are simply living in very turbulent times. As a supplier to gearbox manufacturers, we have also been facing competitors from Asia and India for a few years now, most of whom have completely different production options than we do in terms of price. This makes it all the more important for us to manufacture high-quality products, achieve fast and reliable delivery times and also offer projects and components that not everyone can produce. Standing out from the crowd in certain areas is important—by delivering on traditional German virtues such as inventiveness and innovation,” Haag said.
“With the successor model to the P 150, we wanted to apply the principle of smaller measuring instruments to medium and large precision measuring centers: an inherently rigid construction that no longer requires a foundation. The challenge was to achieve the same accuracy. We did this by developing new correction procedures. The P 152 is a 100 percent in-house development that incorporates all our Klingelnberg know-how. And we are proud of the fact that we have succeeded in achieving all the technical goals we set for ourselves,” said Kai Bartel, head of product line precision measuring centers at Klingelnberg.”
Bartel further discussed the performance features that characterize the P 152.
“Full software compatibility and high accuracy, and the various z-axes of 1,200 mm/1,500 mm and chucking lengths of up to 2 m. We have also improved operability and ergonomics. Thanks to its high efficiency, the precision measuring center is characterized by low power consumption during operation and a small footprint. With the P 152, we were able to create a modern measuring center with an efficient layout and a very harmonious appearance.”
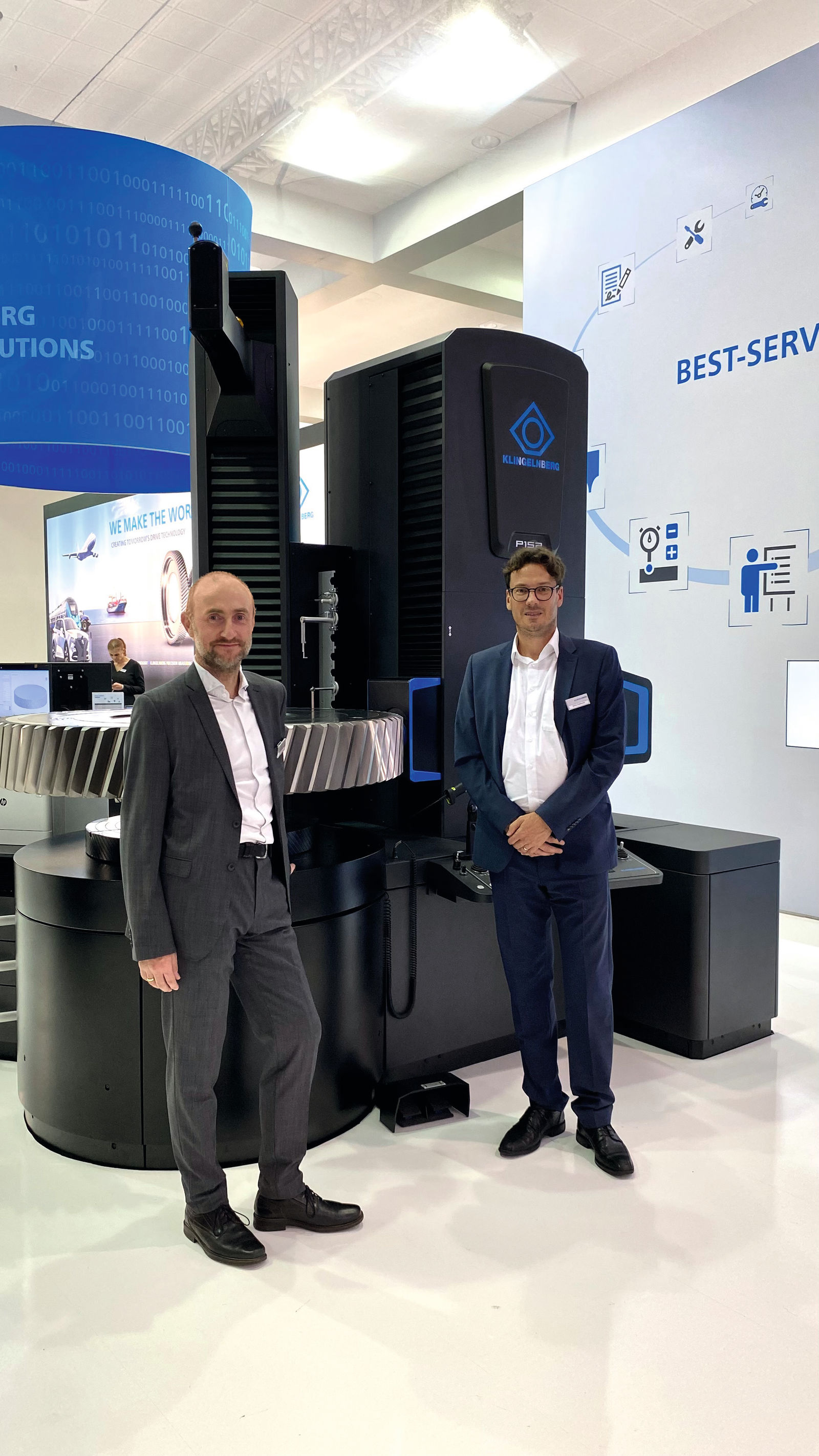
Figure 3—Kai Bartel, Head of Product Line Precision Measuring Centers Klingelnberg (left), and Stefan Finkbeiner, Sales Director Klingelnberg, were delighted to present the P 152, the latest member of the Klingelnberg Precision Measuring Centers family (P-Series), at EMO.
Application Benefits
Internally, the new P 152 is thought to close the gap in the Klingelnberg measuring center portfolio.
“The fact the P 152 no longer requires a foundation significantly reduces the workload for our customers. In addition to lower costs, this also offers very flexible installation options,” said Stefan Finkbeiner, sales director at Klingelnberg.
The measuring center will be of particular interest to all gear manufacturers who need to cover a wide range of components—from small to 1,520 mm component diameters and weighing up to 8 tons—as well as a wide variety of measuring tasks.
“The P 152 enables measurements to be performed regarding dimensions, geometry, position, tools, roughness, worms, worm wheels, and much more. The P 152 is the ideal addition, especially for customers who have a machine park in the range of, for example, the Höfler Rapid 800/1250/1600 cylindrical gear grinding machine. This is because the maximum workpiece weight of eight tons is suitable for the parts that are manufactured on these machines,” said Finkbeiner.
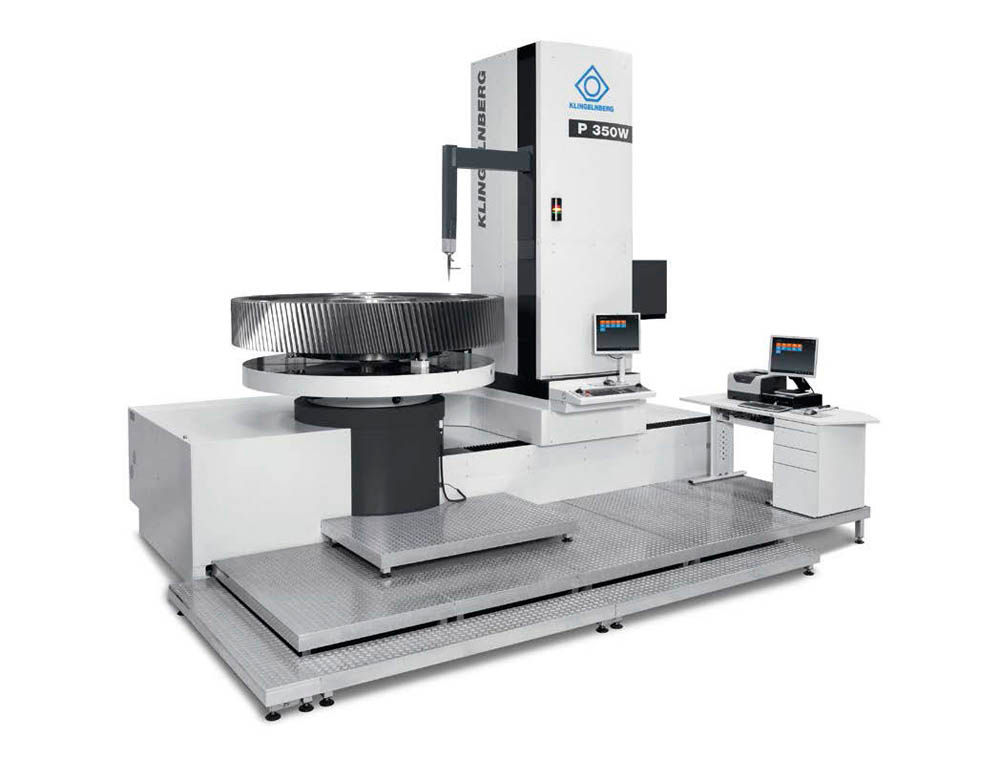
Figure 4—Klingelnberg Precision Measuring Centers (P-Series) handle most measuring tasks in a wide range of industries. For example, the P 350 W is designed for workpieces up to 3,800 mm in diameter and 20,000 kg in weight, making it ideal for components for wind power plants.
High Demand
Finkbeiner believes Klingelnberg has launched exactly the right product at the right time. The launch went extremely well and demand is currently very high.
“The P 152 precisely meets the requirements of our customers, such as Zahnradfertigung OTT, with whom we have a long-standing, trusting, and open working relationship. Zahnradfertigung OTT has a very wide range of components to deliver.”
“Our initial experiences with our new precision measuring center have been very positive. We have been able to significantly reduce measuring times compared to our Höfler EMZ 2602 gear measuring machine, which has now been decommissioned. Various measurements can now be carried out in a single clamping operation, including of course the gear geometry, shape, and position as well as the surface roughness of the tooth flanks,” said Patrick Henes, head of quality assurance at Zahnradfertigung OTT.
Since Zahnradfertigung OTT received the first delivered P 152, there were small suggestions for improvement here and there, which were quickly implemented by Klingelnberg.
“Our wide range of parts in particular means that we have many individual requirements in terms of how gears must be tested and evaluated. Klingelnberg always provided us with reliable and highly professional support to make various adjustments to the software,” Henes said.
“It was an important pilot project for us too,” added Bartel. “So, we were very pleased with the positive feedback from Zahnradfertigung OTT—both during the acceptance process and afterward.”
klingelnberg.com