Advantages of Chamfering
State-of-the-Art Chamfer Cutting Technologies for Cylindrical Gears
Chamfering of cylindrical gear profiles has, traditionally, taken a back seat to the primary cutting and finishing processes. The common wisdom was that the process added to cost but had little impact on part quality. All of that is now changing. There is a fast-growing appreciation for chamfering, as manufacturers recognize the significant handling and processing advantages it offers downstream when chamfers and gear flanks remain burr-free and can be produced according to required specifications. What excites manufacturers most are the new chamfering technologies now available. While chamfer rolling technologies are still most common, manufacturers of automotive- and truck-sized gears are exploring new technologies that meet their most ambitious chamfering requirements, while greatly reducing the cost of the operation.
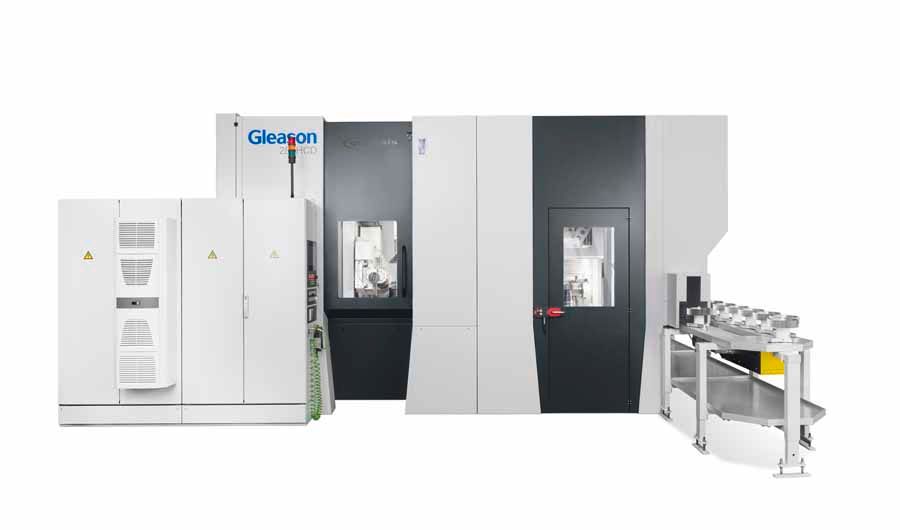
Here are two examples of new chamfer cutting technologies that can provide great results for a wide range of applications:
The Economic Approach: Chamfer Hobbing
For medium- and high volume production of workpieces up to 280 mm in outside diameter and module 5, Chamfer Hobbing fulfills most of the known chamfer tolerances and those expected in the future. Chamfers are defined in the gear design process and chamfer hobs can be designed accordingly, whether comma or parallel chamfer forms are requested or designs are with or without root chamfer. Chamfer sizes and angles are typically requested in a similar range known from other chamfering technologies, like chamfer rolling.
Chamfers on the left and right flank are cut in a generative mode with separate, dedicated chamfer hobs made of High Speed Steel (HSS) featuring AlCroNite Pro Coating. Chamfer Hobs are dedicated to the specific workpiece they are intended for (like regular hobs) and profiles are specifically designed for the particular chamfer form to be realized. The benefits of this process are burr-free face sides of the gear with no measurable burr on the edge between chamfer and gear flank. Consequently, gears are perfectly prepared for consecutive operations and burrs will not cut into the tool life of expensive tools during subsequent hard finishing operations. This is critical, since, for example, the tool life of ceramic honing rings and, specifically, their dressing tools is significant to determining the hard finishing cost of workpieces. Without chamfering, rough burrs left on tool flanks can dramatically increase tool cost and consequently workpiece cost.
Since Chamfer Hobs are essentially just typical hobs with an asymmetric profile, tool shifting can be applied, which reduces the chamfer tool cost-per-part during dry cutting to a benchmark range of one cent per workpiece. While Chamfer Hobbing with its dedicated chamfer tools fits medium and high volume production environments very well, manufacturers of small to medium lot sizes require more flexibility to address the variety of their workpieces while minimizing tool investment.
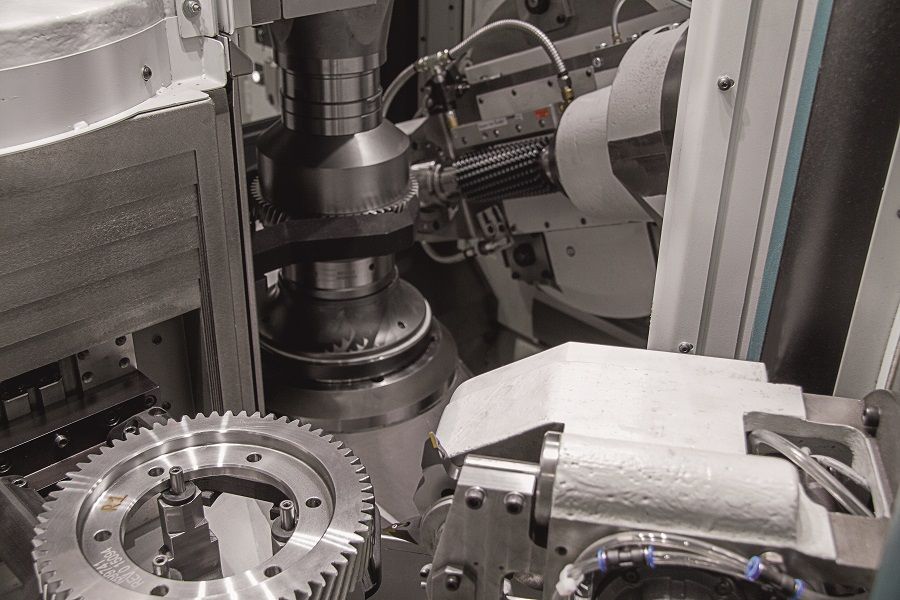