"I'm sure [Kantus] is right, and I'm also sure that I'm right.
Both statements are true."
Now, if you feel like you just fell down a flight of steps built
by M.C. Escher, it's just because what Kinney said is pure paradox.
It's simply not possible for forging to be progressing while
at the same time not changing.
Kinney says it is. Kantus says it's not. Who should you
believe?
Both.
A Heated Debate
To even begin to dissect this paradoxical problem, it would be
of great use to first understand the basics.
Here's a quick crash course:
production. The [forged] form is made as close as possible
to the finish contour of the part to reduce machining time and
to keep the amount of wasted material low. Forging tolerances
are [commonly] held within ±0.030" (0.8 mm) and machining
stock allowance is in the range of 0.080 to 0.120 per side. The
surface finish of forged surfaces [for steel parts] is around 500
micro-inches.
"The advantages of forgings include: [shortened] machining
times, as the raw material is shaped close to the final contour of
the part and excess material can usually be removed in a single
[operation], thus less machining and nonfunctional surfaces do
not require machining."
That's per gear blanking expert Robert Endoy — it's accurate,
informative and completely up-to-date.
And it was published in an issue of Gear Technology in 1992.
Seems impossible that almost 25 years have gone by and key
data remains totally untouched, but here we are. Of course,
none of this is to say staying the course is a bad thing. Some
great things remain steadfast and constant through the years,
stubbornly defiant in the face of Father Time himself.
There can be elegance in simplicity, after all. And, by most
accounts, creating forgings is just that.
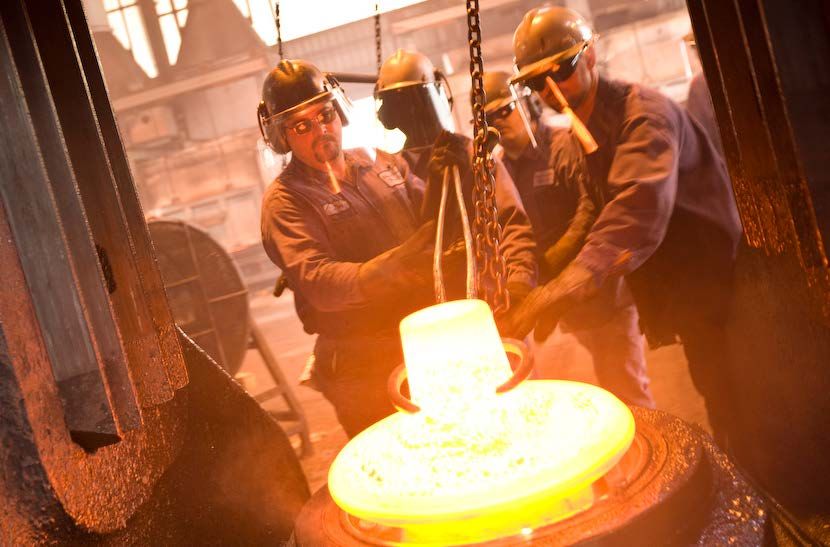
Photo courtesy of Clifford-Jacobs Forging
"The process looks very simple," Kantus said of Ajax's method
of making rolled rings. "We start out with bar material and
we cut it to a weight, and then we forge it into a pre-form so it
looks like a donut. That then goes on a rolling mill where you
can roll it out to the required dimensions. Then most of them
go to heat treat and then machining.
Shawn O'Brien, vice president of sales and marketing at
McInnes Rolled Rings (Erie, PA) also peppered the word "simple"
into his explanation of McInnes' forging process.
"We keep our process simple by focusing exclusively on
seamless rolled ring forgings with rectangular cross sections,"
O'Brien says. "We have three distinct ring manufacturing areas.
Each area has dedicated furnaces, blanking presses and material
handling equipment located and optimally sized to provide the
mills with hot metal in the most efficient manner possible."
Rolled rings, which both Ajax and McInnes specialize in, are
a unique type of forging that offer a distinct set of pros and cons
when compared to products made from die forging, the process
that Clifford-Jacobs uses.
forging method is best," O'Brien says. "Open die forging covers
the broadest size range but typically requires most gross input
weight and processing time. Impression die methods are best
suited for high volume, near net shape orders that will likely
repeat. However, the initial time and expense of creating dies
make this a cost prohibitive method for low volume, short lived
programs."
Clifford-Jacobs Forging (Champaign, IL), a company owned
by IMT that produces steel forgings for the mining, gear, aerospace,
energy, and defense industries, normally makes its forgings
from special bar-quality steel. As steel bars are rolled, the
grain structure within the steel is forced to flow along the centerline
of the bar. When a standard or custom forging is produced
from the bar, this inherent grain flow bends to follow the
contour of the forged shape.
"In some cases, we actually use pre-forms," Kinney says. "We
produce more near net products than, in most cases, a rolled
ring could produce. We actually could use a rolled ring as a preform
for what we do. That's really what, in a sense, differentiates
us. [IMT] has a lot of companies, but Clifford-Jacobs is probably
our premier company on the gear side."
O'Brien adds:
"For gears or bearings with a basic OD × ID × height geometry,
seamless rolled rings provide the best of all forging options,"
he says. "There are a wide variety of ring mills in terms of size
and control technology. The latest in ring rolling technology
enables quick set-up times, minimal stock allowances and size
consistency from ring to ring."
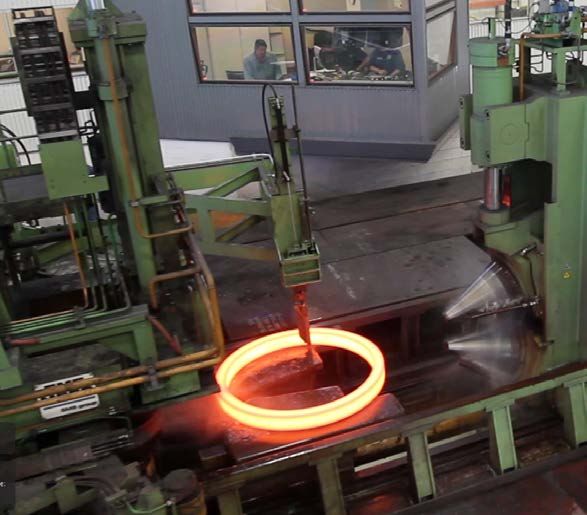
Photo courtesy of McInnes Rolled Rings.
So, as O'Brien clearly states, the process for making forgings
hasn't changed in — wait what?
The latest in ring rolling technology.
Somewhere at Château d'Amboise da Vinci is rolling over in
his grave.
Forging Ahead
To truly understand the forgings paradox you must first realize
that preservation and change aren't always mutually exclusive.
It is possible, for instance, to make alterations to a car without
completely transforming the car into an entirely new entity
(though detractors of the "Ship of Theseus" thought experiment
would argue differently, but that's a paradox for a different day).
Such is the case with creating forgings — the process is fundamentally
the same, there have just been a few recent upgrades.
"While forging as a process remains quite similar to what was
done generations ago, the application of engineered innovations
such as direct-from-forge-heat-treating makes it considerably
more efficient and effective today," Kinney says.
Forgers and ring rollers aren't trying to reinvent the wheel, so
to speak. They're simply trying to make the wheel easier to produce
and easier to use.
"There have been a lot of innovations in the press and forging
market to use modeling and simulation to give you better
results," Kinney says. "We're really immersed in that process
— giving you a better idea of the grain flow and what the
final near net part is going to look like.
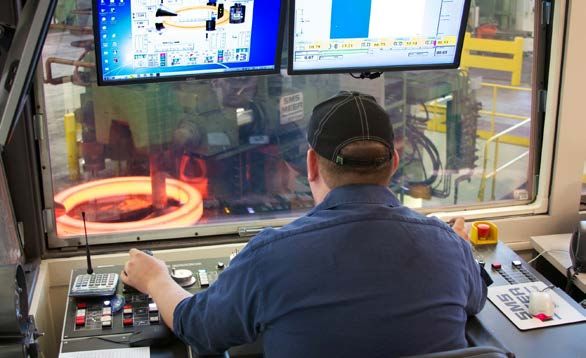
Photo courtesy of McInnes Rolled Rings.
"Specific to Clifford-Jacobs, we are also involved in development
work with SCRA (South Carolina Research Authority) to
produce what we call direct forge intensively quenched parts
that we believe will be a game-changing approach to the forging
and heat treating process. It's a development project that's
underway, but our goal is to better integrate forging and heat
treating to produce superior parts. We're really excited about
that."
For companies that specialize in rolled rings, like McInnes
and Ajax, innovation has come in the form of newer machinery
and more advanced, intuitive software.
"It's like comparing a car being manufactured a decade ago
to now," O'Brien says. "You didn't have XM Radio but you had
radio — is it really different if the music is still coming out?
"A lot of the difference is user interface and how much more
you're able to rely on technology. That's not to say the operator's
experience isn't valuable, but if you combine an experienced operator with the newest technology, then the horsepower
behind it is that much greater.
"The hydraulics, the frame upon which they sit, the method
of forging, that all remains the same. It's kind of the ‘sheet
music' that's different — the software, the computerized rolling
methods, et cetera. The newer the machine the latest you have
in terms of that.
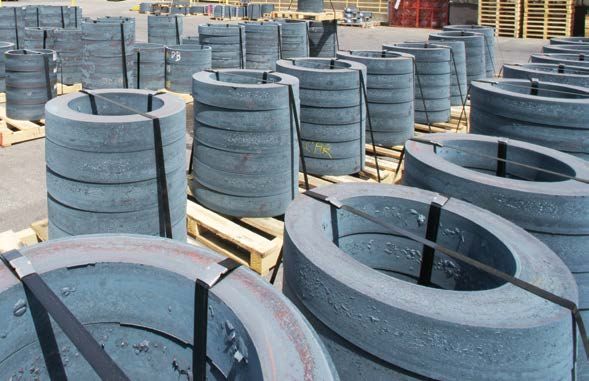
Photo courtesy of McInnes Rolled Rings.
"Newer is better in terms of control, user interface and maintenance
diagnostics."
For gear manufacturers, the main cause for concern isn't
necessarily how easy it is to make the forgings — nor should it
be — but in the quality of the forgings once they're made.
And the good news for buyers of forgings and rolled rings is
that besides being more quickly and efficiently made than ever
before from a supplier's perspective, they're also produced at a
higher quality, and more consistently so.
"The percentage of rings that are within your nominal size
range are going to be better over time," O'Brien says. "If it's a
manual controlled mill, you're going to have inconsistencies
from piece to piece. Within a single job, a computer controlled
mill is going to be putting out the same piece consistently.
"I think [the difference is] repeatability, consistency, and
you're going have tighter tolerances and less allowance."
And with that, the paradox that began tangentially with da
Vinci hundreds of years ago becomes less of a riddle and more
of minor problem solved by good old fashioned persistence and
ingenuity.
Now if we can just get da Vinci to tell us where that darn
Holy Grail is.
For more information:
Ajax Rolled Rings
Phone: (803) 684-3133
www.ajaxring.com
McInnes Rolled Rings
Phone: (814) 459-4495
www.mcinnesrolledrings.com
Clifford-Jacobs Forging
Phone: (217) 352-5172
www.clifford-jacobs.com